Unilever setzt auf 3D-Druck zur besseren Herstellung von Plastikflaschen
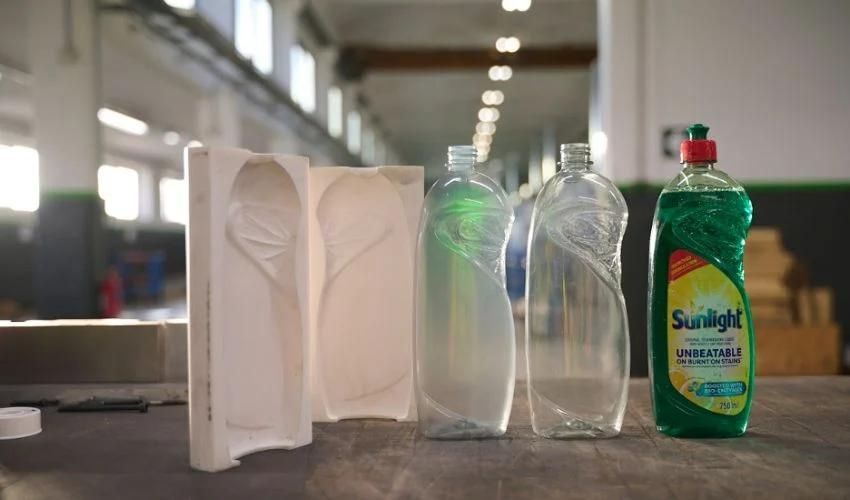
Ein weniger diskutierter Bereich, in dem wir in den letzten Jahren das Wachstum des 3D-Drucks beobachten konnten, ist die Verpackungsindustrie. Mit einem Marktwert von 1,21 Mrd. US-Dollar im Jahr 2023 und einem erwarteten Anstieg auf 2,56 Mrd. US-Dollar bis 2023, laut Future Market Insights, haben wir in den letzten Jahren gesehen, dass sich immer mehr große Namen wie L’Oréal und Pepsi der additiven Fertigung zuwenden. Jetzt kommt mit Unilever ein weiteres Unternehmen hinzu, das für die Herstellung von Formen für Kunststoffflaschen auf den Harz-3D-Druck von Formlabs setzt.
Vielleicht haben Sie noch nie von Unilever gehört. Einige Produkte und Marken des britischen Unternehmens wie Axe, Ben & Jerry’s, Dove und Knorr haben Sie aber bestimmt schon einmal gehört. Das „fast-moving consumer goods (FMCG) conglomerate“ ist der größte Seifenhersteller der Welt, dessen Produkte in über 190 Ländern erhältlich sind. Der FMCG-Sektor ist jedoch hart umkämpft, und so sucht Unilever ständig nach neuen Wegen, um innovativ zu sein. Dazu gehört auch der jüngste Schritt, 3D-Druck für Flaschen zu verwenden.
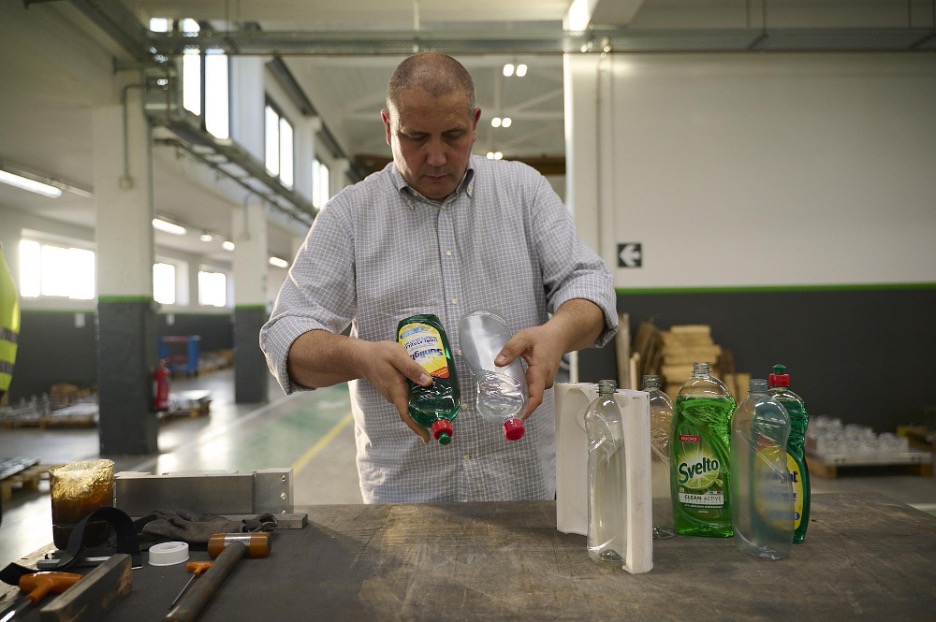
Comparing bottle prototypes made using the 3D printed mold
Stefano Cademartiri, CAD & Prototyping Owner, Unilever, fügt hinzu: „Ein Konsumgüterunternehmen wie Unilever muss so schnell wie möglich oder vor der Konkurrenz auf dem Markt sein. Man muss den Verbrauchern das beste Produkt zum besten Preis in der kürzest möglichen Zeit anbieten. Der 3D-Druck hilft uns, diesen Prozess zu beschleunigen.“
Wie nutzt Unilever den 3D-Druck zur Herstellung von Flaschen?
Traditionell dauert die Herstellung einer einfachen Kunststoffflasche viel länger, als Sie vielleicht erwarten. Vom Entwurf bis zum fertigen Produkt, einschließlich der Herstellung der Formen vor dem Blasformen, vergehen oft Monate. Außerdem gibt es kaum Möglichkeiten, verschiedene Prototypen und Designs auszuprobieren, da die Herstellung einer einzigen Form etwa sechs bis acht Wochen dauert.
Durch die Integration des 3D-Drucks in den Prozess wird diese Zeitspanne drastisch verkürzt, da eine 3D-gedruckte Form in nur zwei Tagen fertiggestellt werden kann, wodurch sich die Pilotphase auf nur zwei Wochen verkürzt – und das bei deutlich geringeren Kosten. Flavio Migliarelli, R&D Design Manager, Serioplast Global Services, erklärt weiter: „Mit der 3D-gedruckten Form können wir im Vergleich zur Standardform bis zu 70 % Zeit und 90 % Kosten sparen. In der Vergangenheit mussten [Kunden] bis zu 12 Wochen auf ein einziges Design warten, jetzt können wir fünf Designs herstellen.“
Es sollte klar sein, dass der 3D-Druck in diesem Fall in Verbindung mit traditionelleren Methoden eingesetzt wird. Genauer gesagt werden die Formen mit einem Form 3L 3D-Drucker von Formlabs und dem Rigid 10K-Harz hergestellt, das präzise Formen mit glatter Oberfläche ermöglicht und gleichzeitig dem Innendruck und der Temperatur standhält. Der Einsatz von SLA half Unilever auch dabei, mehr Details in die Flaschen zu integrieren, wobei Logos und andere feine Details gut zur Geltung kamen.
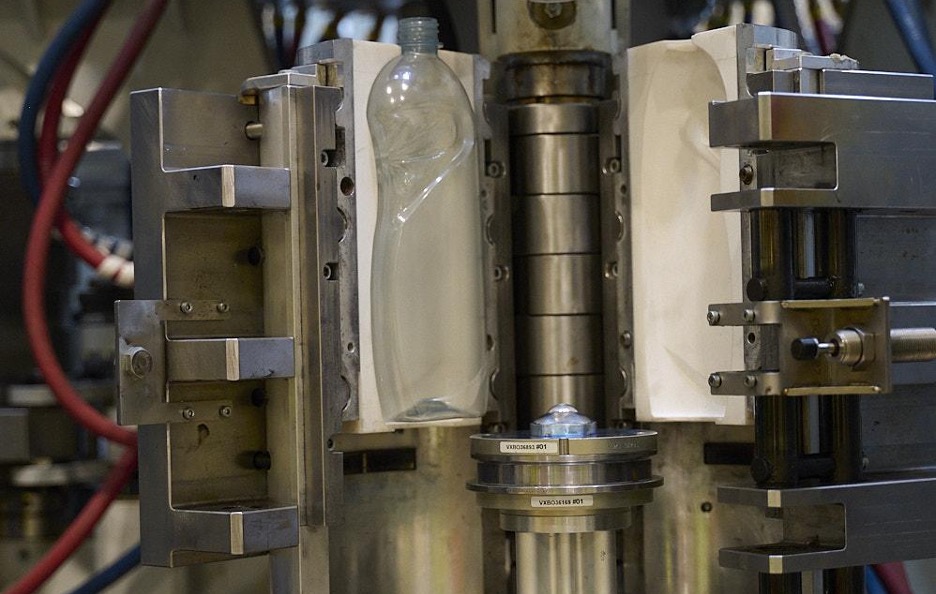
Die 3D-gedruckte Form wird an einer Metallvorrichtung befestigt und kann dann in Verbindung mit dem Blasformverfahren zur Herstellung von Kunststoffflaschen verwendet werden
Nach der Herstellung der Form könnten die Flaschen dann im Blasformverfahren hergestellt werden, in diesem Fall im Streckblasverfahren (SBM), das üblicherweise zur Herstellung hochwertiger, glasklarer PET-Behälter verwendet wird. Zu den Anwendungen für die Kombination dieser Technologien gehören das frühzeitige Testen von Aspekten der Produktionslinie dank der Ähnlichkeit der Flaschen mit dem Endprodukt, die Validierung des SBM-Verfahrens und des PET-Vorformlings sowie die Beschleunigung des Prototyping. Weitere Informationen finden Sie im White Paper HIER.
Was halten Sie von der Entscheidung von Unilever, für die Herstellung von Formen für Plastikflaschen den 3D-Druck einzusetzen? Lassen Sie uns dazu einen Kommentar da, oder teilen Sie es uns auf Facebook oder LinkedIN mit. Möchten Sie außerdem eine Zusammenfassung der wichtigsten Neuigkeiten im 3D-Druck und der additiven Fertigung direkt und bequem in Ihr Postfach erhalten? Dann registrieren Sie sich jetzt für unseren wöchentlichen Newsletter.
*Bildnachweise: Formlabs