Lithoz and ORNL Are Working Together to Develop High-Performance 3D Printing Ceramics
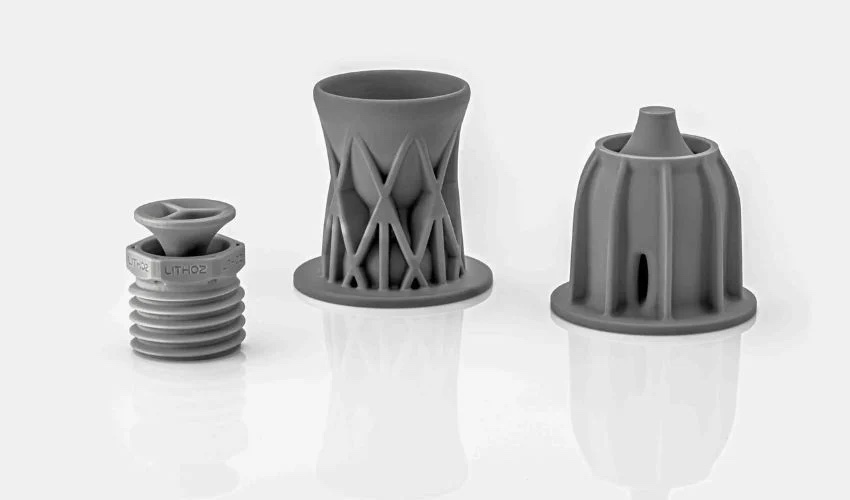
It is no secret that ceramics are often used to make parts in various sectors. Indeed, they are often used in industries like aerospace, defense and industry thanks to their incredible properties and strength. Notably, ceramics are well-known for their ability to withstand very high temperatures. In the latest news, in order to further drive forward development in the field of high-temperature ceramics, the Austrian company Lithoz GmbH and the Oak Ridge National Laboratory (ORNL) of the US Department of Energy have concluded a Cooperative Research and Development Agreement (CRADA), as announced by Lithoz on December 5.
The focus of this cooperation agreement for research and development is to use Lithoz’s 3D printing technology to conduct further research in the field of processing non-oxide ceramics in additive manufacturing. The partners are therefore working together to produce 3D-printed non-oxide ceramic parts that can withstand extremely high temperatures. In this way, the participants hope to make the additive manufacturing of these ceramics scalable for industry.
“This project will build on ORNL’s years of research in developing and testing high-temperature materials and ceramics. By combining our expertise with Lithoz 3D printing capabilities, we have the potential to change the concept of high-temperature ceramics processing for heat exchange, aerospace and defense applications,” explained Corson Cramer, Extreme Environment Materials Processing Group staff scientist at ORNL.
Paving the Way to Ceramic Success with Lithoz and the ORNL
Lithoz’s new 3D printing technology, Laser-Induced Slipcasting (LIS), is to be used. LIS relies on laser slurry drying, or net shaping, technology, which makes it possible to guide computer-controlled light amplification by stimulated radiation emission. This dries out liquid-embedded layers of solids. The aim of this technology is to produce complex geometric parts, especially on a larger scale than previous molding processes allow. By incorporating intricate internal channels into the 3D printable design, the parts can ultimately be lighter and produced more efficiently. The technology also enables an expanded range of materials, as it is also suitable for processing dark ceramics such as silicon carbide and silicon nitride.
Building on this basis, the focus of the ORNL-Lithoz agreement is to further develop the technology and test it to its full potential. On the one hand, the performance of the technology will be tested by testing it with a common oxide ceramic material. Further steps will involve 3D printing from a primary material – such as silicon nitride and silicon carbide – which will be removed from the molded component in a subsequent step.
This stage is crucial for the aim of the cooperation agreement, namely to create high-performance ceramics for extreme temperatures, as silicon nitride and silicon carbide are particularly in demand in the aerospace industry. Once the debinding step is complete, the substance is transformed back into a solid by sintering, after which it is then tested for its performance and properties. Additively manufacturing ceramic parts for extremely high temperatures at an industrial level opens up further areas of application in aviation, aerospace, the defense industry and in various high-performance applications in various industries.
What do you think of the new agreement between Lithoz and the ORNL? Let us know in a comment below or on our LinkedIn, Facebook, and Twitter pages! Don’t forget to sign up for our free weekly Newsletter here, the latest 3D printing news straight to your inbox! You can also find all our videos on our YouTube channel.
*All Photo Credits: Lithoz