USACE 3D Prints Largest-Ever Civil Works Component for Soo Locks
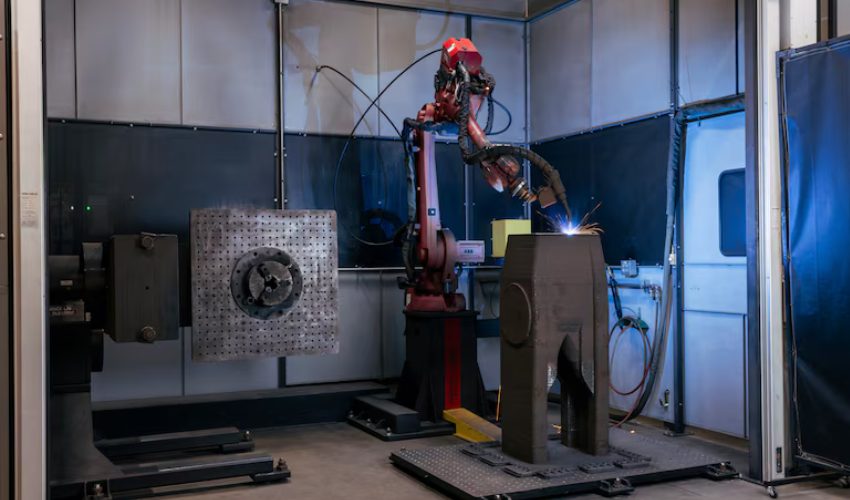
As winter traditionally forces a pause on shipping through the Soo Locks, a critical passageway for maritime commerce through the Great Lakes, the U.S. Army Corps of Engineers (USACE) is leading the way in innovative maintenance solutions. This year, USACE has taken a giant leap forward in civil engineering by 3D printing the largest U.S. civil works component ever created, successfully leveraging AM to manufacture a crucial part for the Poe Lock’s ship arrestor system.
At the center of this project was the replacement of aging components, notably the lever arm for the Poe Lock’s ship arresting system, which protects the lock’s gates from runaway ships and ship collisions. Responsible for the system’s overall function, these lever arms, which had been in service for more than 60 years, had developed cracks, requiring a swift and effective solution to ensure the uninterrupted flow of maritime traffic.
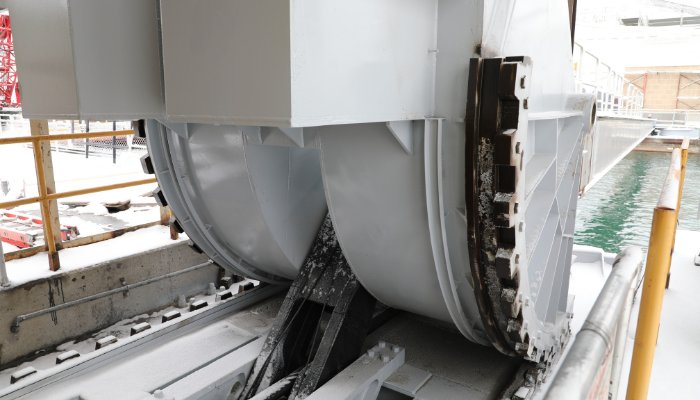
The 12 foot-long 3D printed metal part installed within the arresting system of the Poe Lock. (Photo Credits: USACE)
Faced with a tight deadline and recognizing the complexity of the project, the USACE Detroit District teamed up with field experts to explore creative solutions. Years of research by the U.S. Army Engineer Research and Development Center were consulted as the decision was made to leverage 3D printing technology to speed up production while meeting the project’s strict quality requirements. In close partnership with industry leaders like Eaton Corporation and academic institutions such as the University of Toledo, USACE tapped into Lincoln Electric, a leading provider of welding solutions technology, to quickly fabricate a new lever arm using wire arc additive manufacturing (also called WAAM).
How 3D Printing Streamlines Repairs at Soo Locks
To combat lengthy lead times and ensure top-quality replacements for the Soo Locks, the decision to turn to 3D printing was made. While traditional manufacturing methods would have required an estimated 18 months for production, posing significant challenges to maintaining efficiency at the Soo Locks, 3D printing offered obvious, immense advantages. By utilizing AM technology, the production timeline was slashed to just 12 weeks, greatly speeding up repair time while reducing disruptions to maritime traffic. Furthermore, the new lever arm exhibited superior strength characteristics, surpassing previous components by roughly 20-30%, guaranteeing improved performance and longevity.
Speaking on the integration of 3D printing into the Poe Lock project, Lt. Col. Brett Boyle, commander of the USACE Detroit District, stated, “We secure our nation and energize our economy by operating, maintaining, and preserving strategic water resources and infrastructure. That is a challenge as our infrastructure continues to age. These challenges are opportunities to deliver our program in new, innovative ways that make us more efficient. The Poe Lock ship arrestor project has been one such opportunity for our team to work with ERDC researchers to harness existing 3D printing technology in a way that safely delivers superior quality, while cutting through the extended lead times of today’s environment.”
As USACE continues its search to expand operations while cutting costs through innovative manufacturing methods, the potential of 3D printing becomes increasingly clear within the industry. With ongoing advancements in additive manufacturing techniques and materials, 3D printing presents significant benefits in enhancing resilience, reducing expenses, and accelerating project completion timelines within the sector. To learn more about this project, click here.
What do you think of the USACE’s utilization of 3D printing at the Soo Locks? Let us know in a comment below or on our LinkedIn, Facebook, and Twitter pages! Don’t forget to sign up for our free weekly newsletter here, for the latest 3D printing news straight to your inbox! You can also find all our videos on our YouTube channel.
*Cover Photo Credits: US Army Corps of Engineers