INTENSE M1 Mountain Bike Integrates 3D Printing for Unmatched Performance
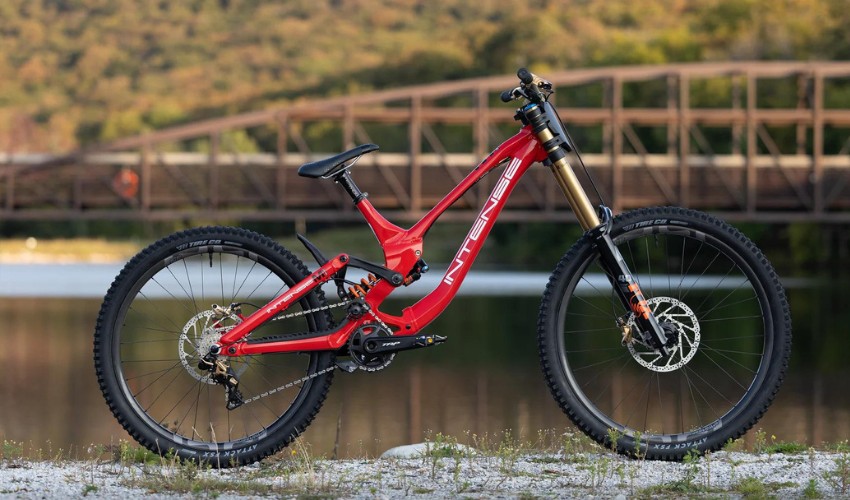
For downhill mountain bikers, conquering large drops and navigating unpredictable terrain requires lightweight, durable biking equipment. INTENSE’s M1 has long been a leader in the pack, but has recently taken a step forward to further innovate their bicycles. Through a collaboration between TRUMPF and Elementum 3D, the iconic INTENSE M1 downhill bike has received a transformative redesign after the integration of additive manufacturing. Identifying the need to improve the bike’s suspension system, INTENSE aimed to rethink the M1’s design while transcending the boundaries of traditional manufacturing methods.
Central to this redesign is the development of a new 3D printed backbone, or bottom bracket foundation. Traditionally, the original M1 brackets were manufactured using multiple parts. Recognizing the potential for improvement, the team at INTENSE identified that consolidating the design into a single piece made from 6061 Aluminum could significantly enhance the performance and durability of the suspension system. However, the part’s complexity rendered it impossible to use conventional manufacturing techniques, as the single piece incorporates internal ribbing for improved strength.
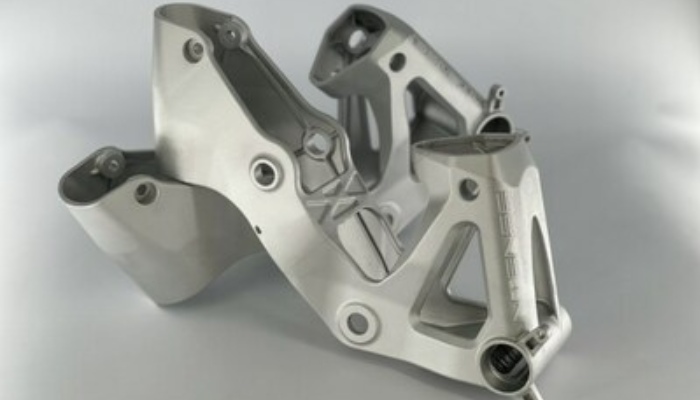
Completed 3D printed INTENSE M1 backbones, made from Elementum 3D’s A6061-RAM2 alloy.
This challenge led INTENSE to explore 3D printing as a solution, resulting in their partnership with TRUMPF to advance this project. TRUMPF’s experience in 3D printing bicycle parts proved pivotal in overcoming the design challenge, as they not only advised INTENSE to utilize 6061 Aluminum in their design, but contacted Elementum 3D for delivery of the material. As prototype testing concluded, a revolutionary 3D printed backbone bottom bracket was produced that not only met, but exceeded the expectations of INTENSE.
The backbone bracket showcased superior strength and weight reduction compared to its traditionally manufactured counterpart. Additionally, it exhibited no porosity or contamination issues, yet still held high weldability. When compared to conventionally machined parts, it is reportedly almost impossible to distinguish which bracket is 3D printed.
Speaking on this collaboration between TRUMPF and Elementum 3D, INTENSE Founder and CEO Jeff Steber added, “I’m thankful for the great work TRUMPF and Elementum 3D provided. Their guidance and expertise played a critical role in successfully producing our new M1. I am happy to report the M1 finished 2nd at the 2023 UCI Cycling World Championships.“
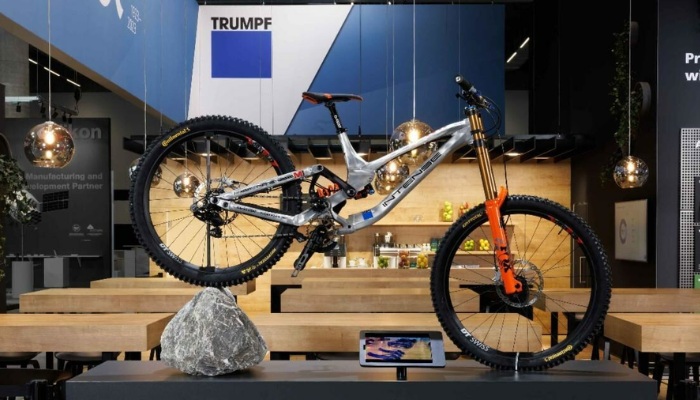
Display of the new INTENSE M1 prototype at TRUMPF’s Formnext 2023 booth.
The success of this project has paved the way for future innovations in bike frame production, an area where we have already seen much growth in recent years. INTENSE plans to incorporate additive manufacturing into its prototyping process and explore further opportunities in 3D printing for other production parts. Additionally, TRUMPF seeks to increase its usage of Elementum 3D’s aluminum alloy, citing the benefits of its advanced material properties for 3D printing. To learn more about the new M1 design, click here.
What do you think of this implementation of a 3D printed backbone in the new INTENSE M1? Let us know in a comment below or on our LinkedIn, Facebook, and Twitter pages! Don’t forget to sign up for our free weekly newsletter here, the latest 3D printing news straight to your inbox! You can also find all our videos on our YouTube channel.
*All Photo Credits: Intense Cycles