3D Printing Boosts Efficiency Aboard RRS Sir David Attenborough Amid Its First Antarctic Voyage
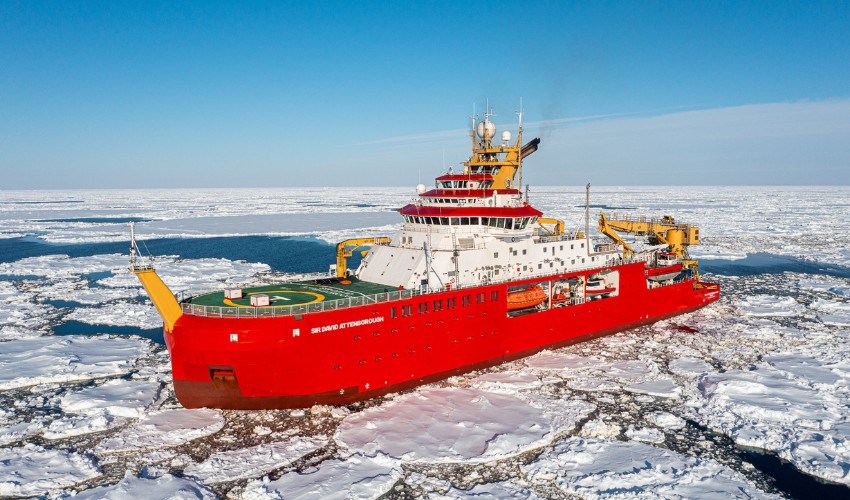
Having embarked on its first mission to Antarctica last October, the RRS Sir David Attenborough, heralded as Britain’s most sophisticated polar research vessel, is experiencing a groundbreaking utilization of 3D printing technology. In an effort to enhance onboard operations, the ship is increasingly turning to 3D printing to revolutionize its repair and modification processes. Leveraging DEFEND3D software, the RRS Sir David Attenborough can more easily access the benefits of additive manufacturing while simultaneously overcoming issues such as low bandwidth, which is of course a major concern in the Antarctic.
In the challenging conditions of remote and harsh environments, traditional repairs on vessels like the RRS Sir David Attenborough have conventionally relied on simpler materials like wood and glue. Indeed, damaged plastic components often remain broken until replacements can be sourced – a process known for its inherent costs and time-consuming nature. Additionally, while essential, the vessel’s reliance on carpenters and machinists for specific repairs has, at times, fallen short. Despite the expertise in these specialized trades, the swift creation of these precise and customized components has not always been guaranteed, highlighting the need for a more viable solution.
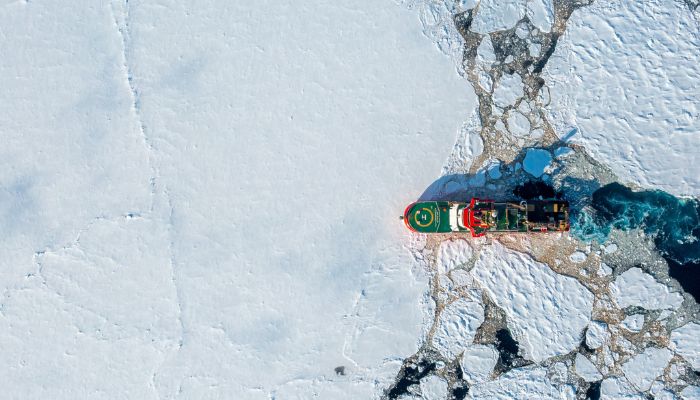
RRS Sir David Attenborough concludes its Ice Trials (photo credits: Jamie Anderson, British Antarctic Survey)
However, the introduction of 3D printing aboard the vessel has revolutionized this approach, allowing parts to be custom-made, replicated, or invented with minimal cost and significantly reduced turnaround time. The adoption of 3D printing technologies aboard ships has surged in popularity, mirroring the trend set by the US Navy, which embraced 3D printed components on their nuclear submarines last September. Though, obviously, challenges still need to be addressed, especially in areas where things like the internet are not accessible.
How DEFEND3D Enables Seamless 3D Printing Aboard the RRS Sir David Attenborough
As you would expect, implementing 3D printing onboard a polar vessel comes with its own challenges. Notably, the obstacle of limited bandwidth complicates template sourcing for designs not yet downloaded. Thankfully, in the case of the RRS Sir David Attenborough, they were able to turn to DEFEND3D, a manufacturing solution specializing in secure transmissions for remote 3D printing, which addresses this challenge through its Virtual Inventory Communications Interface software.
Distinguishing itself, this software allows vessels to overcome bandwidth constraints during template sourcing, ensuring a seamless 3D printing process by tapping into a central repository of engineer-grade parts. This capability holds especially true even in the most remote locations, where limited bandwidth might otherwise interrupt operations. The end result is enhanced operational efficiency, enabling vessels to create essential parts on demand and minimize downtime in challenging environments. Achieving this requires only 3kbps.
A recent testament to the success of DEFEND3D’s software involves the creation of a bespoke part – a bracket attachment of a peristaltic pump intended to test the salinity of water samples. Crew members aboard the vessel reported the software operated without any issues, ensuring the prompt use of the part without delays while still aligning precisely to the design specifications.
Installation of this 3D printing technology aboard the RRS Sir David Attenborough marks a significant stride of maritime innovation. DEFEND3D’s software, adept at overcoming bandwidth challenges, not only ensures immediate benefits for on-demand repairs and component creation, but also establishes a foundation for sustained, uninterrupted research missions in the harshest environments. This moment solidifies a commitment to advancing scientific endeavors in the extreme conditions of polar exploration. You can find out more on the British Antarctic Survey website HERE.
What are your thoughts on this use of 3D printing technology aboard the RRS Sir David Attenborough? Let us know in a comment below or on our LinkedIn, Facebook, and Twitter pages! Don’t forget to sign up for our free weekly Newsletter here, the latest 3D printing news straight to your inbox! You can also find all our videos on our YouTube channel.
*Cover Photo Credits: British Antarctic Survey