Additive Assurance Talks Ensuring Part Quality in Metal 3D Printing
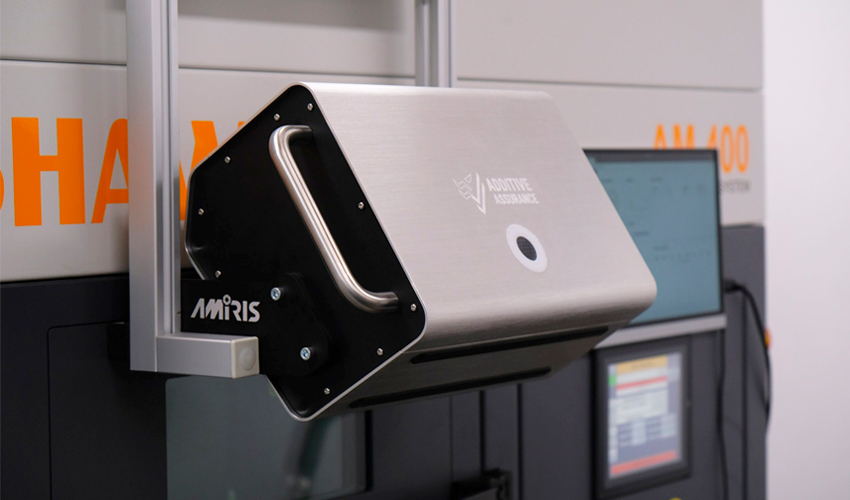
Metal additive manufacturing is being used by many advanced industries thanks to the ability to create complex and customized parts. However, to ensure feasibility and quality, it is essential to validate the parts obtained. This is an essential step to avoid defects and ensure optimal performance. In turn, certifications ensure that specifications and mechanical properties are consistent in each production batch, providing confidence to end users. Thanks to these processes, users are assured of the quality, durability and reliability of components, facilitating their integration into diverse applications, from medical and aerospace to automotive and industrial sectors. This contributes to the consolidation of metal additive manufacturing as a viable option in Industry 4.0. One of the companies at the forefront of this technology is Additive Assurance, with its AMiRIS solution. We spoke with its founders to learn more about their activity.
3DN: Could you introduce yourself and tell us your connection to 3D printing?
I’m Marten Jurg, an additive manufacturing engineer and CEO of Additive Assurance. With my co-founder Andrey Molotnikov, we started Additive Assurance to solve what we saw as the most important limitation in 3D printing: part repeatability and consistency. We’ve been pushing the boundaries of metal additive manufacturing for more than a decade. I started working in additive manufacturing (AM) through research R&D projects for aerospace systems integrators, and later took on projects in other sectors, such as energy and medical devices. From this experience, qualification and certification have always been very much in the forefront. While it’s great to be able to manufacture complex geometries, if you can’t certify them for use, they’re useless.
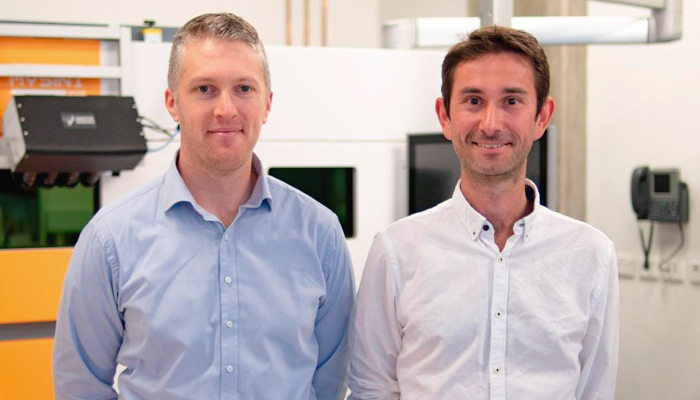
Additive Assurance co-founders Marten Jurg (left) and Andrey Molotnikov (right).
When we started, we were investigating the fatigue properties of L-PBF parts for aerospace applications, where the impact of stochastic defects can create a significant reduction in part design life, and the potential of AM designs. We saw that the stochastic nature of AM drove up costs and posed a barrier to adoption. We realized that if we could ensure part consistency through inspection, we could help reduce costs and unlock large-scale production.
3DN: What is Additive Assurance? How did it come about?
Additive Assurance is a provider of quality assurance solutions for metal laser powder bed fusion (L-PBF) systems. The genesis of Additive Assurance dates back to my PhD with Andrey at Monash University. At the time, we were working on the fatigue of AM parts made with L-PBF, and were confronted first hand with the inconsistency issues that arise in this process. Like many others, we were using CT scanning to detect defects in fabricated parts. CT scanning is slow, expensive and was a major bottleneck.
The problems we were observing in the process piqued our curiosity for on-site monitoring in 2016. We saw the wealth of information available through observation of melt emissions, however, existing systems really suffered from two main drawbacks: the volume of data generated and the lack of analysis. Through experimentation with various detection modalities, we developed what would become AMiRIS, a high-resolution, long-exposure near-infrared monitoring technique that could be easily adapted to any L-PBF machine. The high-resolution meltpool images were rich in detail, and their format allowed us to develop a machine learning approach to locate defects where they occurred.
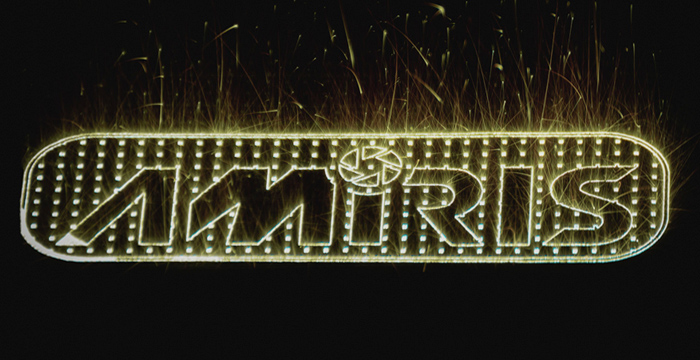
Photo Credits: Additive Assurance
We also saw problems in the complexity of the other solutions available and the difficulty of installing them on machines, requiring significant downtime for installation and voiding the manufacturer’s warranty. End users also don’t know what to do with the mountains of information they produce, resulting in other issues such as data storage and finding time to translate what it all means. We worked with our development partners and customers to solve these problems.
3DN: What is AMiRIS and what is its role in the additive manufacturing process?
AMiRIS is a quality control sensor suite for all L-PBF systems, independent of machine supplier. It uses near infrared sensors combined with machine learning techniques to identify defects and anomalies with micron accuracy. ML models allow users to locate and identify faults automatically. Thus, they can stop faulty constructions, saving time and money. But most importantly, they provide proof of construction conformance, the basis for part certification.
The AMiRIS platform is available as a scalable cloud-based solution or as a local installation. Sensing units are installed on fleets of different machines and transmit the captured data to a central server, where GPU compute instances locate defects and inconsistencies. Centralizing all this information allows users to form a complete picture of their AM operations, from part defect to machine productivity and preventive maintenance.
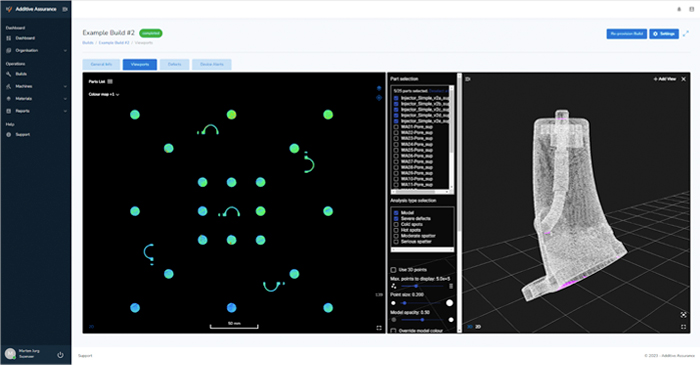
The AMiRIS cloud-based platform (photo credits: Additive Assurance)
We use machine learning analytics that combine the data stream into simple pass/fail criteria based on user-defined limits. Machine failures, laser scanning errors, geometric variations, coater interference, process variations, underfusion and overfusion are just a few of them. AMiRIS is easy to install, non-intrusive and can be applied on existing platforms without interrupting work.
3DN: What advantages does the technology offer and what markets are you targeting?
When it comes to AM, increasing production and productivity is critical to expanding our industry, and doing so while ensuring quality is essential. We have worked quietly with groups in the aerospace, energy and orthopedic device sectors. Our technology increases productivity in these industries, with the added benefit of traceable quality documentation.
Most of the industry has had to rely on post-process inspections, such as CT scanning, which is very time-consuming and expensive for parts produced by L-PBF. As a result, sometimes the production process stops for months, only to find out that the parts do not pass inspection. The user then goes back to the beginning to reprint the same components, doubling the cost and lengthening the lead time. AMiRIS allows the user to see defects on parts in production, to save time, money and headaches in the post-processing phase. With our technology, end users can expect to increase productivity and scale production while reducing wasted material.
We primarily target regulated manufacturers in the aviation, commercial space, defense, medical and transportation markets, but have also found valuable applications in other industrial sectors. We are always on the lookout for forward-thinking experts willing to embark on the journey with us to drive AM into mass production globally.
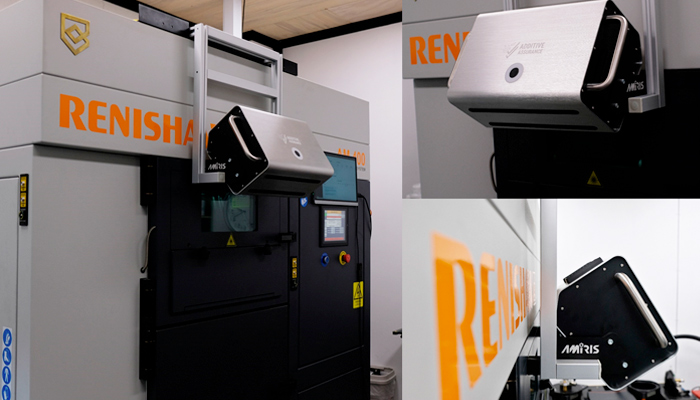
The AMiRIS sensor unit mounted on a Renishaw machine (photo credits: Additive Assurance).
3DN: What can we expect from Additive Assurance in the future?
Like other industries and advanced manufacturers, we are looking for increased production capacity. With larger scale printers producing more parts, we will see more potential for critical defects and the need for industry-focused regulated solutions. That’s why we collaborate with manufacturers and software providers to integrate our technology into these fast-growing machines and service more platforms in more locations. Global expansion is an important priority. As we continue to grow and expand into other markets, we are building our strategic alliances. We are looking for bright new talent to help us lead in this critical field and help raise global standards.
3DN: Any last words for the readers?
In the last few years, the industry has been willing to assert itself. Lack of quality was an obstacle, but no longer. Advanced on-site control, analysis for certification, qualified assurance and reporting have arrived. We would love to have forward-thinking companies, experts and personalities join us on this journey or join our advisory board. We now have a viable solution for certifying the quality of parts in production – that’s confidence you can rely on. You can find out more about the company HERE.
What do you think of the solution developed by Additive Assurance? Let us know in a comment below or on our LinkedIn, Facebook, and Twitter pages! Don’t forget to sign up for our free weekly newsletter here, the latest 3D printing news straight to your inbox! You can also find all our videos on our YouTube channel.
*Cover Photo Credits: Additive Assurance