3D Printing vs CNC Machining: Which is best for prototyping?
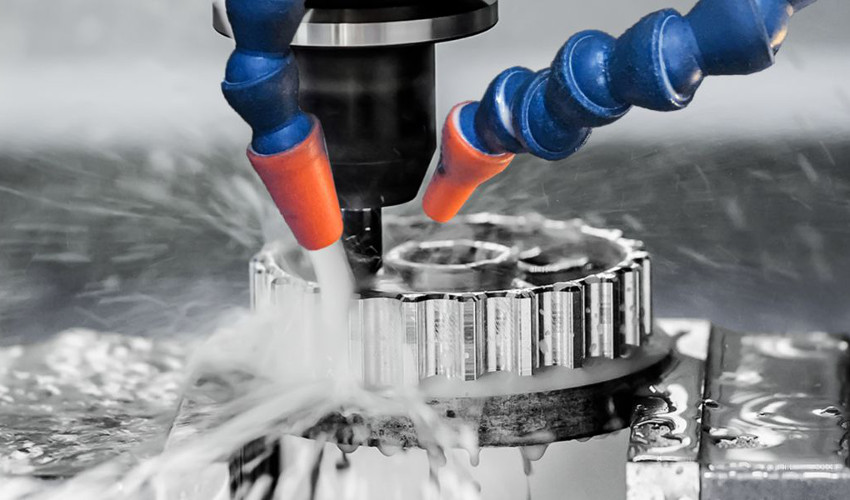
3D printing is a rapidly growing technology with many advantages over traditional manufacturing methods. It however has its problems, including that 3D printing cannot be effectively used for mass production, and is limited in speed and accessibility. Another manufacturing technique for low-to-mid production is CNC machining (computer numerical control), a fairly common subtractive technique for part creation. We decided to compare the advantages and disadvantages for each method to establish where these technologies are most appropriate.
Subtractive vs Additive Manufacturing
They key difference between 3D printing and CNC machining is that 3D printing is a form of additive manufacturing, whilst CNC machining is subtractive. This means CNC machining starts with a block of material (called a blank), and cuts away material to create the finished part. To do this, cutters and spinning tools are used to shape the piece. Some advantages of CNC machining include great dimensional accuracy as well as many compatible materials, including wood, metals and, plastics.
3D printing, or additive manufacturing, involves parts being created layer-by-layer using materials such as plastic filaments (FDM), resins (SLA/DLP), plastic or metal powders (SLS/DMLS/SLM). Using a source of energy such as a laser or heated extruder, layers of these materials are solidified to form the finished part. Advantages of 3D printing include its freedom of shape, applications in many sectors, accuracy, speed, and ability to cut costs and weight in parts.
There are however several machines that have sought to combine these two forms of manufacturing in one. Most notably of these, the ZMorph 2.0 SX, is marketed as a CNC mill which also functions as a 3D printer. This includes a CNC mill with 3 axes as well as a print head due to its interchangeable heads. Moreover, several companies have recently closed successful Kickstarter campaigns with these combined machines, such as Mooz’s 3-in-1 3D printer.
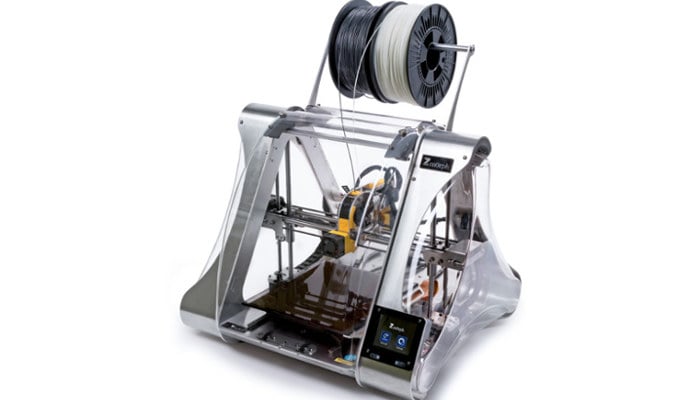
The ZMorph SX 2.0 includes interchangeable CNC and 3D printing heads.
3D Printing vs CNC Machining: Materials
Both 3D printing and CNC machining are compatible with a wide variety of materials, including both plastics and metals. 3D printing however is more focused on plastics overall, though this is changing rapidly as better and more affordable ways of 3D printing metal are being developed by manufacturers such as 3D Systems, Arcam, Desktop Metal and Markforged.
The most commonly used plastics used in CNC include ABS, Nylon (PA66), Polycarbonate (PC), Acrylic (PMMA), Polypropylene (PP), POM and PEEK. A very commonly used metal in CNC machining is aluminium, used by prototyping companies to create high-quality prototypes in a variety of industries. Aluminium is recyclable, has good protective qualities, and can create effective prototypes for machining. Other commonly used metals include stainless steel, magnesium alloy, zinc alloy titanium, and brass.
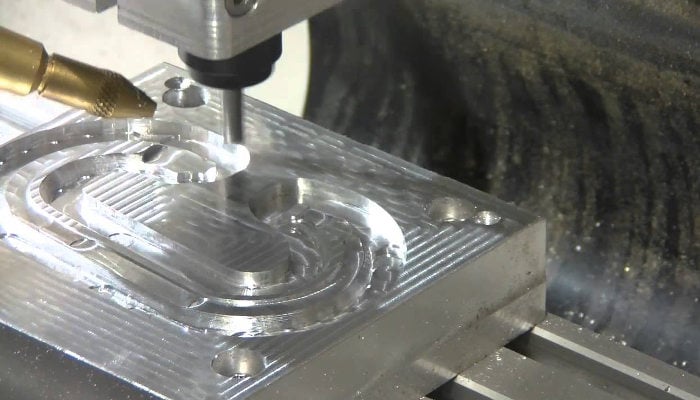
Aluminium is a commonly used metal with CNC due to its good mechanical properties.
In 3D printing, commonly used thermoplastics include ABS, PLA, Nylon, ULTEM, but also photo-polymers such as wax, calcinable or biocompatible resins. Some niche 3D printers also allow for the printing of parts in sand, ceramics, and even living materials. The most common metals used in 3D printing include aluminium, stainless steel, titanium, and inconel. It is also worth noting that to 3D print metal, expensive ($100,000+) industrial machines are required. Some materials such as superalloys or TPU (flexible material) cannot be created with CNC, so must be used with 3D printing or rapid tooling technology.
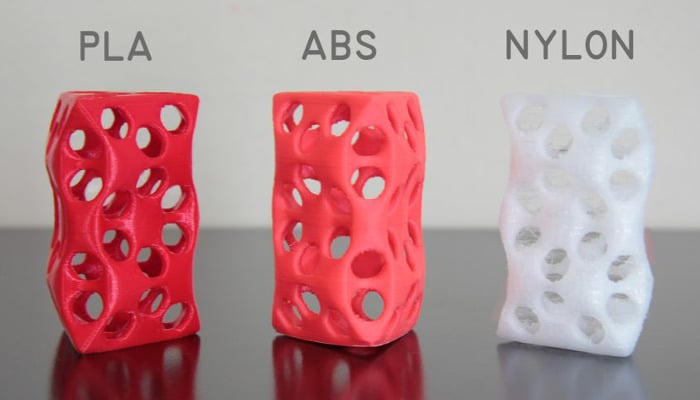
Some plastics available to be 3D printed and CNC milled.
Ease of Use
3D printing is known to be simpler to use than CNC machining. This is because once the file is prepared, you just need to chose the part orientation, fill, and supports if needed. Then once printing has commenced, no supervisor is required and the printer can be left until the part is finished. Post-processing requirements depends on the technology.
However, CNC machining is a far more labour-intensive process. A skilled operator is required to choose between different tools, rotation speeds of tools, the cutting path, and any repositioning of the material the part is being created from. There are also post-processing techniques which can require more time.
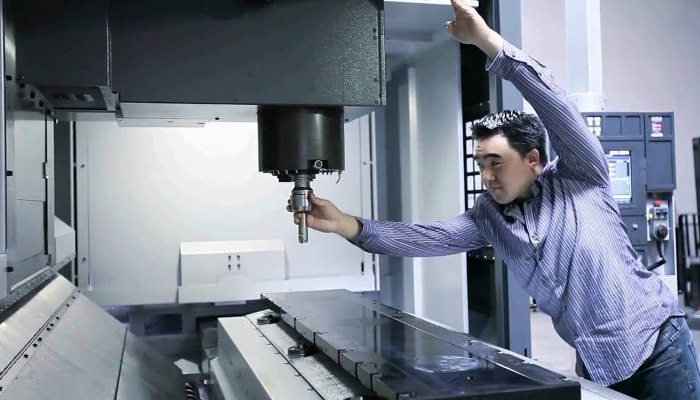
CNC requires an operator whereas 3D printing can be left alone when printing.
Accuracy, Size limitations & Geometric Complexity
Though there are a number of 3D printing technologies, we have chosen to compare CNC machining with SLS, industrial (not desktop) FDM, and DMLS metal 3D printing. In terms of tolerance, CNC machining is superior to all 3D printing processes, even DMLS. However, with minimum layer thicknesses the superiority is not so profound, and is not as precise as DMLS.
Powder bed fusion 3D printing processes such as SLS and DMLS are limited in their build volume however. Even technologies with larger build volumes such as FDM cannot compete with CNC in terms of maximum size of parts.
3D printing is well-known for its advantages in creating parts with high geometric complexity. Though supports are required for some technologies, 3D printing can create parts with geometries that no traditional manufacturing method can replicate. Technologies such as SLS and Multi Jet Fusion by HP can even do this without any support structures.
Tolerance (mm) | Min. Layer Thickness (mm) | Max. build volume (mm) | |
CNC Milling | ± 0.025 – 0.125 mm | cutting depth 0.01 mm | 2000 x 800 x 1000 mm |
SLS | ± 0.3 mm | 0.7 – 1.0 mm | 300 x 300 x 300 mm |
Industrial FDM | ± 0.5 mm | 0.8 – 1.0 mm | 900 x 600 x 900 mm |
DMLS | ± 0.1 mm | 0.4 mm | 230 x 150 x 150 mm |
Cost
Though on average 3D printing is cheaper, costs depend on how many parts are required and how quickly you need them. For larger quantities (higher double digits to 100s) CNC is likely to be more appropriate. For low volumes, 3D printing is more appropriate and lower-cost. 3D printing is also more appropriate if you need your prototypes or parts very quickly. There are additional factors however that make comparing the two technologies more difficult. These include materials varying in cost (from cheap materials like ABS to materials that can cost $500/kg like PEEK), and repairing and changing machinery (such as CNC heads).
Environmentally Friendly
Since CNC involves cutting material away from an original block, there is always going to be mess afterwards. These pieces of material need to be cleaned afterwards and disposed of, which isn’t required from 3D printing. Since additive manufacturing forms an object on the build platform from material fed into the machine, there is no mess except supports (if used). This makes 3D printing the more ethical of two methods as there is less unused waste.
Conclusion
Overall to conclude, there is no perfect, one-size-fits-all technique. Though both methods are very competent and useful technologies, the most appropriate one will depend on the material, geometric complexity, manufacturing volume, and budget. To find out which is best for your particular job, we advise you approach a local or international service, and ask for their advice. If attempting to manufacture in-house, reflect on the machinery available to you and decide whether it is appropriate for the job at hand.
What did you think is the overall better method of 3D printing vs CNC? Let us know in a comment below or on our Facebook and Twitter pages! Sign up for our free weekly Newsletter, all the latest news in 3D printing straight to your inbox!
3D printers are capable of producing parts for fit and finish, but for parts that require exceptional smoothness for mating with other precision components, CNC machining may be preferable.
what in the actual fuck is this
As someone who works for the CNC manufacturing business (https://get-it-made.co.uk/) – it is very accurate! Thank you for spreading useful information 🙂
3D printers is a great invention.
3D printers is a great invention.
Each has its own advantages, and no one can replace the other.