The Complete Guide to Laser Powder Bed Fusion in 3D Printing
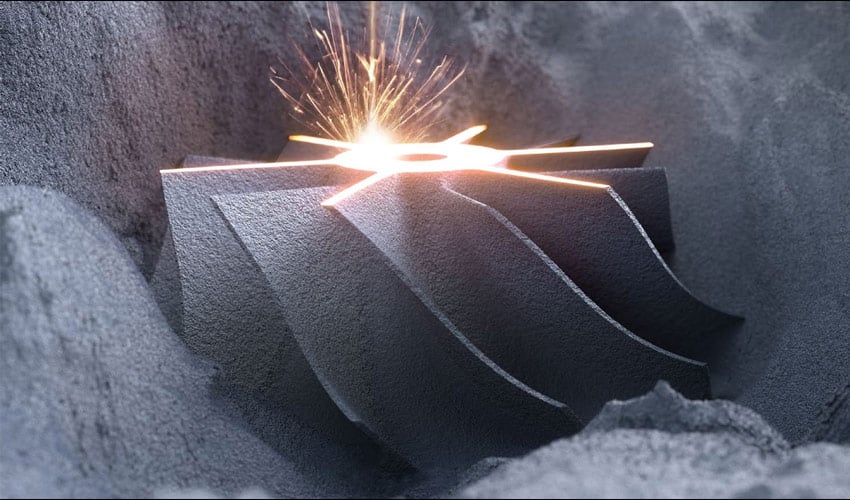
Laser powder bed fusion is a group of metal additive manufacturing methods that use, as the name suggests, a powder bed and a laser to fuse the powder together. Notably, this includes DMLS, or Direct Metal Laser Sintering, is a metal 3D printing method that is well-known for its ability to create complex metal parts. In this article, we’ll explore laser powder bed fusion, and DMLS especially, in detail, from its history and how it works, to its benefits, post-processing steps and impact on the 3D printing market.
History and Development of DMLS
The origins of DMLS date back to the 1990s, when EOS patented the process. Meanwhile, in 1995, the Fraunhofer Institute introduced the term SLM (Selective Laser Melting) to designate a similar technology. Although the terms DMLS and SLM have different origins, the processes they represent are in fact very similar. To avoid confusion, these technologies are generally referred to as laser powder bed fusion, noting that contrary to what the term “DMLS” might suggest, these processes do not involve sintering, but rather the melting of metal particles.
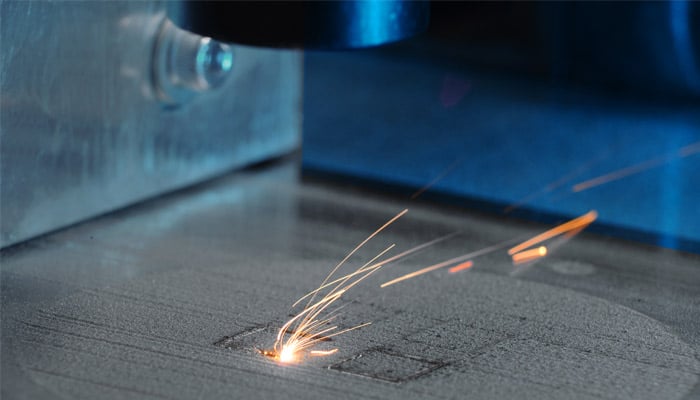
Photo Credits: Fraunhofer ILT, Aachen, Germany
The difference between sintering and melting is quite simple: melting involves the transition from a solid to a liquid state thanks to a high temperature; sintering, on the other hand, does not allow the metal to melt, as the temperature used is not high enough. As a result, the powder particles are agglomerated together, leaving a void and thus holes. To take a rather clear image, it’s like stacking apples: there will always be a gap between two pieces of fruit. 3D-printed parts will therefore have low mechanical strength, unlike in fusion, where the liquid fills these gaps.
How DMLS 3D Printing Works
To initiate printing, the 3D printer creates an inert atmosphere in its chamber and heats it to the optimum printing temperature. A thin layer of metal powder, generally between 20 and 60 microns thick, is then deposited on a platen. A fiber-optic laser then scans the cross-section of the part, melting the metal particles according to the 3D model. Once a layer is complete, the tray descends and a new layer of powder is added, repeating this process layer by layer until the final part is formed. In summary, the DMLS 3D printing process is as follows:
- Material preparation: The base material is a fine metal powder, often a specific alloy. This powder is stored in a hopper and fed into the printing machine.
- Preheating: Before printing, the powder is preheated to a temperature slightly below its melting point. This ensures that the material solidifies rapidly after the laser has passed over it.
- Roller application: For each layer of the print, a thin film of powder is applied to the printing plate using a roller.
- Laser fusion: A high-power laser is precisely aimed at the top layer of metal powder. The laser’s intensity is adjusted to reach the material’s melting temperature, causing it to melt and solidify immediately as it cools. This step is repeated layer by layer to build the object layer by layer.
Key Benefits of Laser Powder Bed Fusion
Laser powder bed fusion processes, including DMLS, offer a number of advantages:
- Geometric complexity: It enables the design of geometrically complex parts, impossible to obtain with conventional metal fabrication methods such as milling.
- Reduced weight and number of components: Thanks to topological optimization techniques, LPBF can reduce the final weight of parts and the number of components to be assembled.
- Mechanical strength: Parts produced using DMLS have a mechanical strength comparable to those manufactured using traditional subtractive manufacturing techniques.
LPBF Materials
Laser powder bed fusion allows for the 3D printing of metal parts from aluminum, titanium, inconel, steel and cobalt-chromium.
Post-Processing
After printing, the 3D printer is cooled down, and the unfused powder is removed from the tray, often by suction. Parts are attached to the plate using print supports. Unlike SLS technology, these supports are commonly recommended in DMLS to minimize warping and distortion caused by high temperatures. After the print has cooled, the supports are usually removed by cutting, machining or wire EDM.
As with SLS, printed parts are surrounded by an unfused powder called “cake”. Parts can be cleaned by compressed air or sandblasting. After cleaning and removal of supports, LPBF parts undergo a post-treatment process that may include heat treatment to reduce residual stresses, CNC machining, or polishing to improve surface quality.
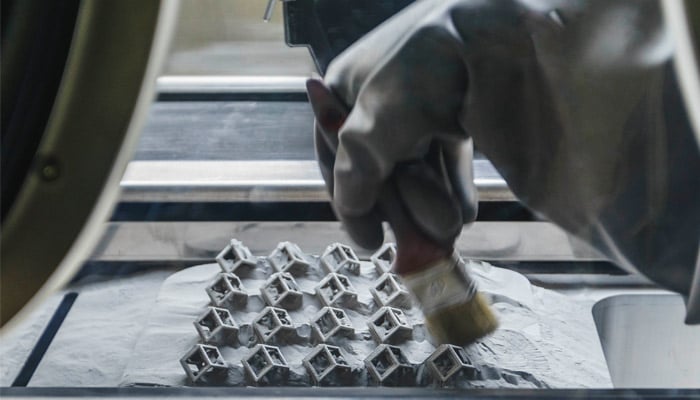
Post-processing steps vary in importance
Laser Powder Bed Fusion 3D Printing Market
Laser powder bed fusion finds applications in sectors such as aerospace for jet engines, automotive for brake calipers and pistons, medicine (especially dentistry) for implants, and other industries. Several key players, including EOS, 3D Systems, AddUp, General Electric Additive, SLM Solutions, Trumpf, Sisma, and Renishaw, offer solutions in this fast-growing market.
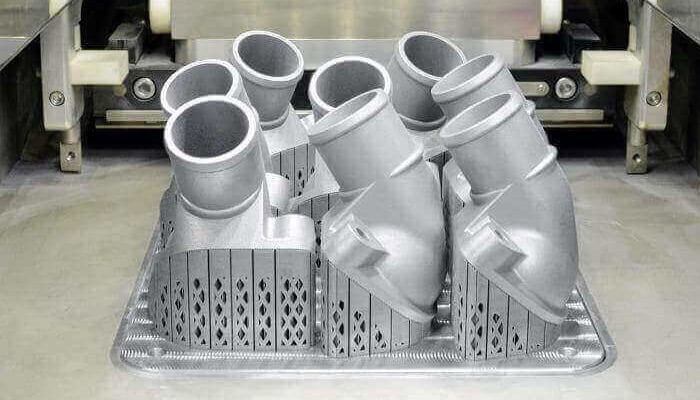
Photo Credits: Mercedes-Benz
Do you use laser powder bed fusion? Let us know in a comment below or on our LinkedIn, Facebook, and Twitter pages! Don’t forget to sign up for our free weekly newsletter here, the latest 3D printing news straight to your inbox! You can also find all our videos on our YouTube channel.
*Cover Photo Credits: DMG Mori
The following fact is wrong (see above): “… in 1995 the Fraunhofer Institute introduced the term SLM for Selective Laser Melting.”
The term SLM is a registered trademark, dated Dec. 28. 2000, initially owned by Dr. Dieter Schwarze and Dr. Matthias Fockele (fromer F&S, Fockele and Schwarze), DPMA register number 30094322.
SLM was founded by F&S and it can be used in German and English, in German we called it “Selektives Laserschmelzen von Metallpulvern”.
BR
Dr. Dieter Schwarze
SLM Solutions Group AG