The Complete Guide to Binder Jetting in 3D Printing
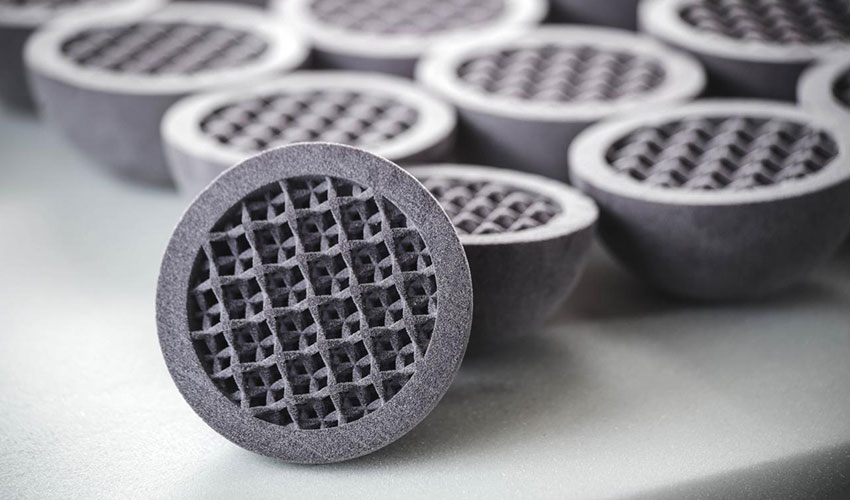
There are numerous additive manufacturing technologies on the market today, each associated with different materials and very specific applications. In this guide, we’ll be talking about binder jetting, which is compatible with a variety of materials, including ceramics and metal. How does binder jet 3D printing work? What materials can you use to manufacture parts? Who are the main machine manufacturers? What are the latest innovations and trends in this field? We took a closer look.
The History and Development of Binder Jetting
This technology was invented in 1993 at MIT, initially to work with ceramics. The rights were quickly taken over two years later by Z Corporation, which was acquired by 3D Systems in 2012. Metal binder jetting was developed by the American company ExOne in 1996. Since then, the technology has undergone numerous advances, attracting the attention of major players such as HP and Desktop Metal, who have launched their own binder jetting solutions, offering enhanced performance and capacity.
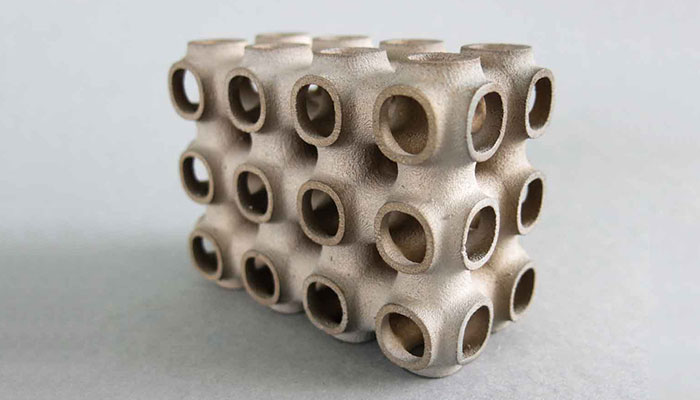
3D printed part sprayed with metal binder (photo credits: Sculpteo)
How Does Binder Jetting Work?
As with all printing techniques, the desired object must first be modeled using CAD software, then exported to a slicer, which sends instructions in the form of G-Code to the machine. Printing begins by lowering the plate, onto which a first layer of powder is spread using a rolling cylinder. A binder is then sprayed in the form of 80 µm droplets using an inkjet print head similar to that used on 2D printers.
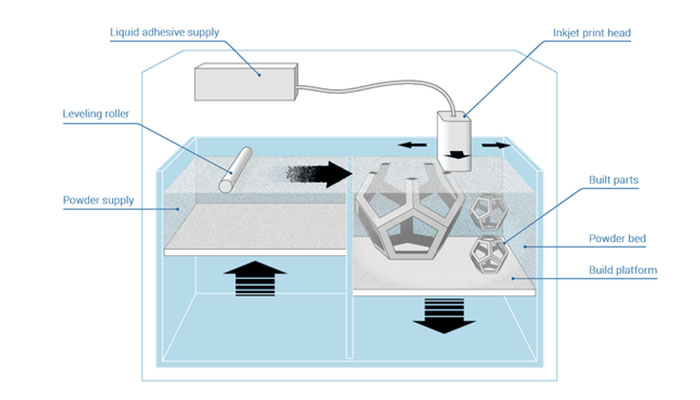
How binder jetting works (photo credits: Additvely)
As the build plate continues to lower, a new layer of powder is spread out and bound in turn. In this way, the object takes shape layer by layer. Thanks to the precision of the binder jetting process, it is possible to create colored models, using binders of different colors, in the manner of an inkjet printer.

After printing, excess powder must be removed (photo credits: 3D Hubs).
Main Advantages of Binder Jetting
Binder jet 3D printing differs from other powder additive manufacturing technologies in its broad material compatibility, since it can print on a wide range of materials (polymers, ceramics, metals, sand, etc.).
This technology is compatible with a wide range of materials, including ceramics, plastic polymers, and even metals such as stainless steel, titanium, inconel and copper, among others. Some materials require the use of a specific binder, such as sand, which uses a chemical binder to create molds or foundry cores.
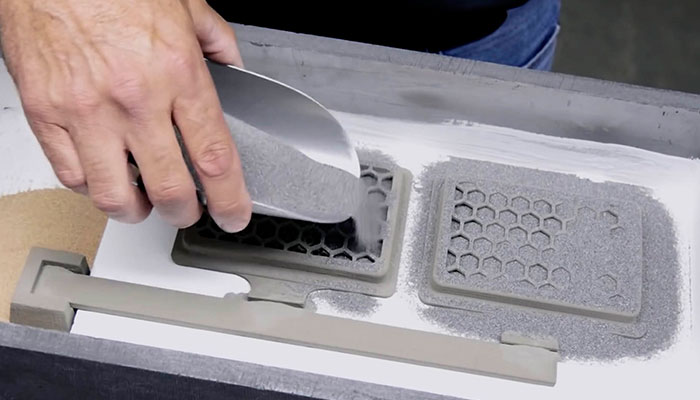
Binder jetting has wide range of compatible materials (photo credits: ExOne)
Post-Processing
After printing, parts made using powder jetting are encapsulated in a mass of powder called a “cake” and require cleaning or depowdering. This process is usually followed by a post-processing step to reinforce the structure of the prints and reduce their porosity. The two main post-processing processes are sintering and infiltration.
Sintering involves heating the part to a high temperature, allowing the powder particles to melt and agglomerate. Sintering is generally used for metal parts, as it produces dense, resistant parts.
Infiltration involves injecting a fluid into the part, filling pores and reinforcing the structure. Infiltration is generally used for ceramic or plastic parts, as it produces stronger, more watertight parts. The choice of post-processing technology depends on the material used and the desired properties of the part.
Manufacturers and Applications
Binder jet 3D printing allows for metal parts or color prototypes to be produced at a lower cost than with other processes such as DMLS or material jetting. However, the porosity of the parts can be higher, influencing the mechanical properties of the component. This technology is popular for the development of mass-produced parts, due to the high print volume of most machines.
Currently, the leading manufacturer of 3D printers using this process with ceramic materials is 3D Systems, which uses the term ColorJet Printing. Other players include Germany’s Voxeljet AG, the Netherlands’ CONCR3DE for thermoplastics, and Taiwan’s ComeTrue for desktop binder jetting 3D printers. For metal-compatible machines, Desktop Metal is the leader (following acquisition of ExOne in 2021), followed by Sweden’s Höganäs (though their brand Digital Metal has now been sold to American company Markforged).
HP and Desktop Metal also entered the binder jetting market in 2018, their technologies offer growing possibilities in metal additive manufacturing and they continue to explore new opportunities in 3D printing, collaborating with industrial partners such as Volkswagen, GKN, Parmatech, Ford, BMW, Google and Adidas.
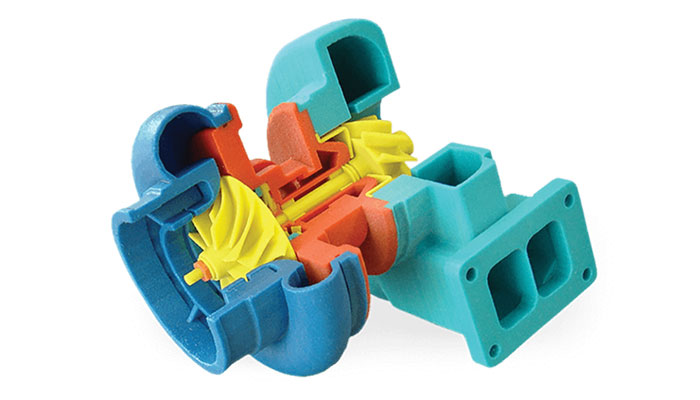
A part printed with ColorJet Printing technology (photo credits: 3D Systems)
Binder jetting has a wide range of applications in the automotive, aerospace, healthcare, luxury goods, foundry, architecture, art and other sectors. It enables the creation of complex, customized, lightweight and resistant parts, with great design freedom. It also offers environmental benefits.
Examples of applications include the manufacture of dental prostheses or bone implants, the creation of jewelry or watches, the production of automotive or aeronautical parts, the production of foundry molds or cores, or the design of sculptures or models.
Find out more about the different 3D printing technologies HERE
Do you use binder jetting? Let us know in a comment below or on our LinkedIn, Facebook, and Twitter pages! Don’t forget to sign up for our free weekly newsletter here, the latest 3D printing news straight to your inbox! You can also find all our videos on our YouTube channel.
*Cover Photo Credits: ExOne
I didn’t see much informations about the binder itself…
I am disappointed and keep looking for informations.
what are the type of binder material?
what are binder materials made of?
Good matter
Its good and understandable