How Has 3D Printing Revolutionized the Music Industry?
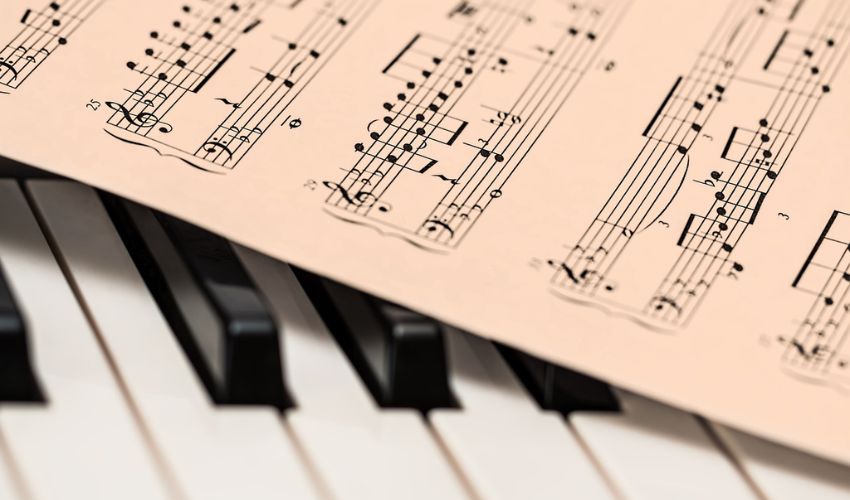
It is becoming clear that additive manufacturing has the potential to completely revolutionze the music industry. Though it is hardly the first time that we have seen a significant impact being made by 3D printing on a sector, in this particular one, the technology has not only transformed and optimized the manufacturing processes of instruments or pieces of art, but it has also managed to add value to them, above all when it comes to improving accessibility to music. Moreover, it has helped with other applications like reviving instruments from the past, helping those in need and made the industry more sustainable.
But are 3D printed instruments more accessible? Is it true that there is an improvement in the design and customization of musical products? Do musicians have a new and valuable tool to project their future? To understand the true impact of AM technology in music and answer these questions, we took a closer look at how exaclty 3D printing has influenced different aspects of the sector.
A Path to Sustainability With 3D Printing in the Music Industry
It is known that 3D printing has an incredible capacity to improve the efficiency of production processes as it allows users to digitally design a product and then build it in a precise way. Thanks to this process, it is significantly easier to design a prototype and understand how it will look in the final stages of development, testing exactly what need to be built in a much less costly and efficient way. All this while also eliminating possible waste that could be caused by traditional methods.
In the field of music in particular, 3D printing has enormous potential to promote a more sustainable world. We can see this potential reflected both in the manufacturing itself and in the fact that the technologies are being used to solve some of the problems in the industry. If we talk about products such as vinyl, for example, they arenot exactly sustainable, as they are made of polyvinyl chloride (PVC), a non-biodegradable plastic material that contributes to air pollution when burned. In addition, much of the production of vinyl records is done in other countries, which due to the pandemic has caused supply problems.
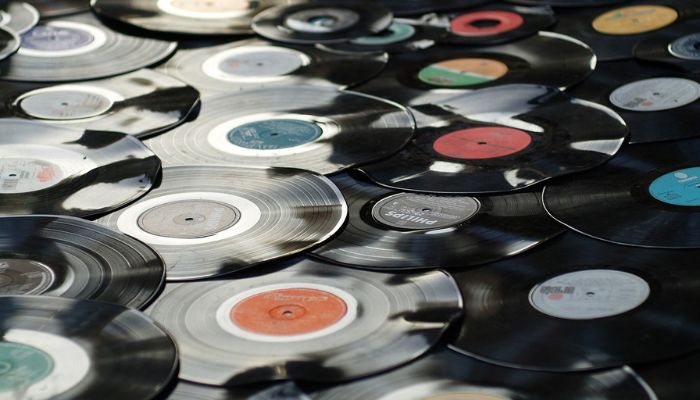
Photo Credits: Unsplash
3D printing in the meantime enables the manufacture of musical instruments, audio components and vinyl records, among others, using more environmentally friendly materials. By using additive manufacturing, it is possible to reduce dependence on non-biodegradable plastic materials and explore more environmentally friendly options. An example of this can be seen in the work of Green Vinyl Records, a Dutch company seeking to produce more sustainable vinyl records. Instead of using traditional plastics, Green Vinyl Records uses eco-friendly materials to create records that retain the same quality and sound as always. In addition, they claim that their manufacturing process saves 60% in energy consumption and speeds up production time.
Additionally, in the world of music, we are also seeing how artists, musicians and engineers are joining forces to create amazing and sustainable products. The “Greenaxe” electric guitar made by Olaf Diegel is a reflection of this movement. Using recycled sawdust, wood binder and a 3D printer, Diegel managed to minimize overall manufacturing costs. The result is a beautiful, handcrafted guitar created from recycled materials, making music more affordable and accessible without relying on unsustainable processes.
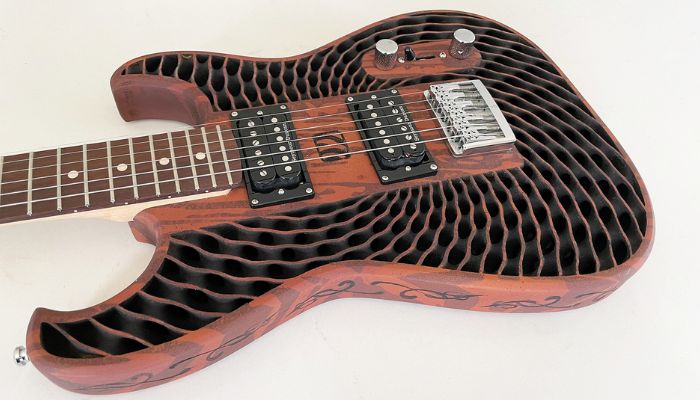
The “Greenaxe” electric guitar made by Olaf Diegel (photo credits: Olaf Diegel)
“The main impact is the simplicity and the reduction of the manufacturing cost. If we compare traditional lutherie with respect to our Digital Lutherie, all the modifications we make to the instruments must first be designed by means of a 3D modeling program. Here it is possible to explore artistic and/or functional options, plan the instrument, combine materials, etc.,” explained Martin Juarez Brizzi, CEO of the 3D printed instruments company called Fona.
Production of Musical Instruments Using 3D Printing
In terms of how musicians can market their products, 3D printing also plays an important role. 3D technologies enable the manufacture of customized and exclusive products, giving artists and musicians new opportunities to create unique and eye-catching products for their fans. Whether it’s reproducing hard-to-find vintage instruments to play at their concerts or creating new designs for their merchandising, 3D printing has become an avenue for more accessible and cost-effective production of music products. However, when the worlds of technology and art come together, there is usually some discord. More traditional musicians and instrument designers feel that 3D printed instruments do not produce as good a sound, while others argue that this technology allows for more precise, less cumbersome designs and, therefore, higher quality instruments.
Still, it is undeniable that 3D printing has revolutionized the way musical instruments are created and accessed, becoming a valuable tool in this regard. With the use of specific materials and technologies, instruments can be manufactured with specific sonic and physical characteristics that were previously not possible using conventional production techniques. 3D printing technology has also freed up access to musical instruments, making them more accessible and affordable for musicians around the world. This is especially good for communities where access to instruments is limited. Musicians can now obtain customized instruments that suit their specific needs and preferences, without having to rely on a limited supply on the market or even being able to make them themselves from online platforms such as Thingiverse or MyMiniFactory.
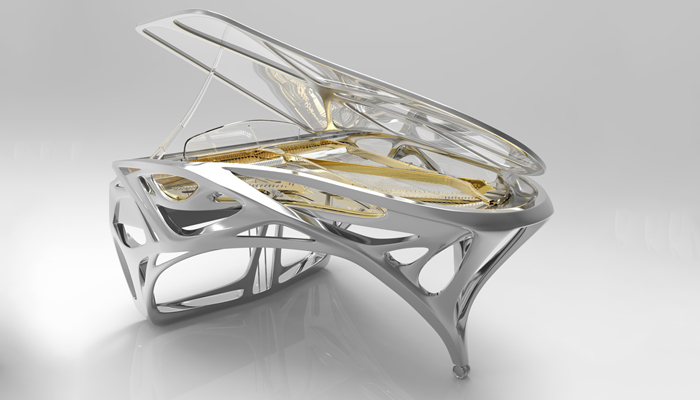
The Grand Piano by Monad Studio (photo credits: Monad Studio)
3D printing also enables the creation of new musical instruments that combine elements of different existing instruments. This results in the creation of hybrid instruments that have unique sonic and physical characteristics. This is because it allows greater freedom when it comes to exploring new instrument concepts and creating customized instruments tailored to the individual needs of musicians. In addition, combining different elements of existing instruments can also lead to new ways of creating music. “The most interesting thing about digital fabrication is not the fact of replacing all components by 3D printing, but combining 3D printing with existing methods and, in that way perhaps, impacting productivity, expanding the customization of an instrument, giving it more artistic or functional argument,” expanded Brizzi.
Technologies and Materials Used for 3D Printed Instruments
As for 3D printed musical instruments, it is important as well to understand what they are being made out of, with a number of different ones being used. Polylactic acid (PLA), acrylonitrile butadiene styrene (ABS), polycarbonate (PC), polyetherimide (ULTEM), acrylonitrile styrene acrylate (ASA) and polyethylene terephthalate glycol (PETG) for example are all common in the production of instruments that have plastic structures. Moreover, they are able to be manufactured from resins or even nylon in both powder and filament form. Apart from the previously mentioned polymer materials, it is also possible to use powdered metals for 3D printed instruments.
In general the use of any of these materials, both polymer and metal, will depend on the goals of the manufacturer when creating the instrument. One example is that to improve the overall strength of 3D printed musical instruments, they are usually reinforced with short or continuous fibers and made with these composite materials. Afterwards, a post-processing can obviously be applied to achieve the desired surface finish. “From the beginning, we have used FDM (fused deposition modeling) to manufacture Syos mouthpieces. Our catalog of conditions is very demanding, especially since musicians are going to put the product in their mouths. We had a French company develop a material specifically adapted to our needs,” noted Maxime Carron, co-founder of Syos, a creator of 3D printed mouthpieces.
If we talk about the technologies for manufacturing them, we can find the appropriate ones for each type of material and instrument. If for example we are talking about a ukulele made from ABS it is mostly likely going to be made using FFF 3D printing. Butif on the other hand we are talking about a 3D printed trumpet, it is more likely that powdered metal and technologies liks DMLS, SLS or EBM will be used.
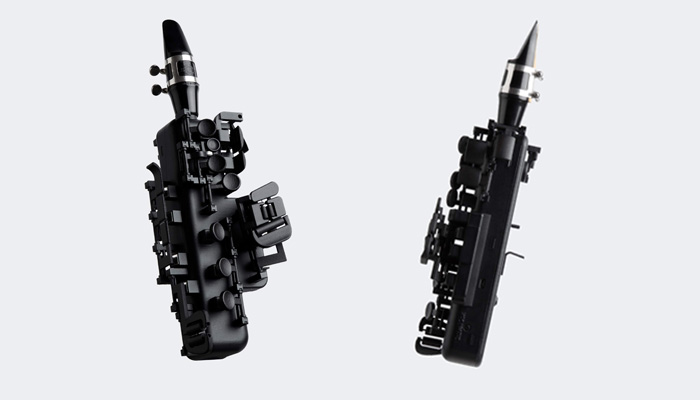
The saxophone has a small size and is very light (photo credits: Odisei Music)
The Catalan company Odisei Music is dedicated to the design and manufacture of 3D printed electronic wind instruments, the most famous being its electronic saxophone. Named Travel Saz, it uses Multi Jet Fusion technology in the production process. Its goal is to spread music around the world by helping musicians develop their musical skills in a faster and easier way, thus demonstrating the potential of technology in this industry.
“We use one of HP’s Multi Jet Fusion printers to manufacture our 3D printed saxophones. This machine allows us to manufacture final parts with very good aesthetic and mechanical finishes. We also use this technology because of its high production. We believe that for the type of products we design and manufacture it is the one that best suits our needs,” explained Ramón Mañas from OdiseiMusic
Accessibility to Music Through New Technologies
It seems certain that 3D printing can certainly be used to help musicians. Indeed Frank DeFalco, manager of Canada Makes, an organization dedicated to 3D printing, commented that “3D printed instruments are no worse or better, just different in their approach” in an interview with Design Engineering. The approach in most cases is to enhance the musician’s experience and help them with whatever they need.
One such example that illustrates the creation of instruments to make them more accessible and comfortable comes from Robert Hunter, a PhD student in engineering at the University of Ottawa. He designed a clarinet and a wrist strap that work together to help the musician support the weight of the instrument for long periods of time. The inspiration came from his own experience playing the clarinet in high school, where he suffered intense pain in his thumb tendon after hours of practice.
Blind people have also found an accessible way to read musics thanks to the 3D printed staves for the blind project led by Kim Yeaji and a team of researchers at the University of Wisconsin. Kim experienced gradual vision loss and discovered in music a way to connect with the world. “It wasn’t just building a prototype for her or the music school. It’s a true collaboration where we worked with Kim to understand her needs and find solutions together,” noted one of the engineers involved in the project.
The project, known as “Tactile Stave Notation”, seeks to recreate paper scores using distinct reliefs that can be not only read, but also recognized through the sense of touch. To achieve this, very detailed 3D printing was needed, so they used selective laser sintering (SLS), which allowed for a better resolution and allowed the recreation of the notes as small elevations on the score.
Carron continues, “There is still a long way to go to make music more accessible, and the fact that new technologies such as 3D printing are being used for manufacturing can help whet the appetite of technology fans. Music still has a very traditional image, at least in France. The use of color and unusual materials, as well as the breaking of codes, can also generate a form of attraction by the novelty it brings to an aging and very old-fashioned market. In any case, that’s what we hope for at Syos!” But, it is clear that although there is still work ahead, 3D printing is the perfect tool for the drive towards accessibility in the music industry.
Acoustics and Production Processes
As we have seen, in addition to instrument manufacturing, 3D printing has improved the accessibility of music for different types of users. Especially for those who unfortunately have difficulties to enjoy it in many aspects. Moreover, 3D printing has enabled faster and more efficient production of acoustic components, which has reduced costs and improved efficiency in the production of sound equipment. This in turn improves the ability of engineers and designers to test and validate their projects prior to mass production, which increases accuracy and quality in production.
To add onto those incredible applications, music is said to be a great ally in the fight against memory-related disorders of old age. 3D printing has also contributed in this aspect, for example we can see it in this Gramophone called “Memory Loss Music Box”. It has been created through 3D printing with bamboo and can be manufactured from home. Its main objective is to bring the joy of music to people with memory loss, such as dementia or Alzheimer’s disease.
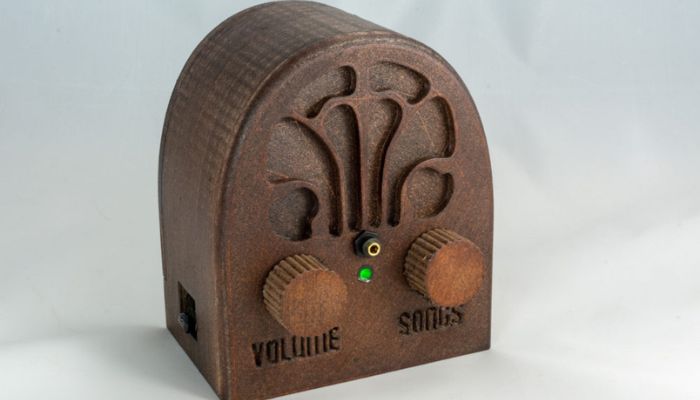
Memory Loss Music Box from Makers Making Change (photo credits: Makers Making Change)
In conclusion, it is hardly a secret that 3D printing has had a hugely positive impoact on a lot of industries. Among those we can certainly include music, as using 3D printers to create instruments and more that are both beneficial for the environment and accessible to all of us will definitely continue into the future. The process can start with a change in the materials used and the reduction of waste as well as an active listening to those in need. Perhaps at some point we will obtain sustainably sourced vinyl, which could be printed in the record stores themselves. Or maybe we could go to a musical instrument store, having the possibility to customize our instrument according to our specific needs.
How do you think 3D printing has most influenced the music sector? Let us know in a comment below or on our LinkedIn, Facebook, and Twitter pages! Don’t forget to sign up for our free weekly Newsletter here, the latest 3D printing news straight to your inbox! You can also find all our videos on our YouTube channel.