Laser Scanner vs Structured Light Scanner: which should you choose?
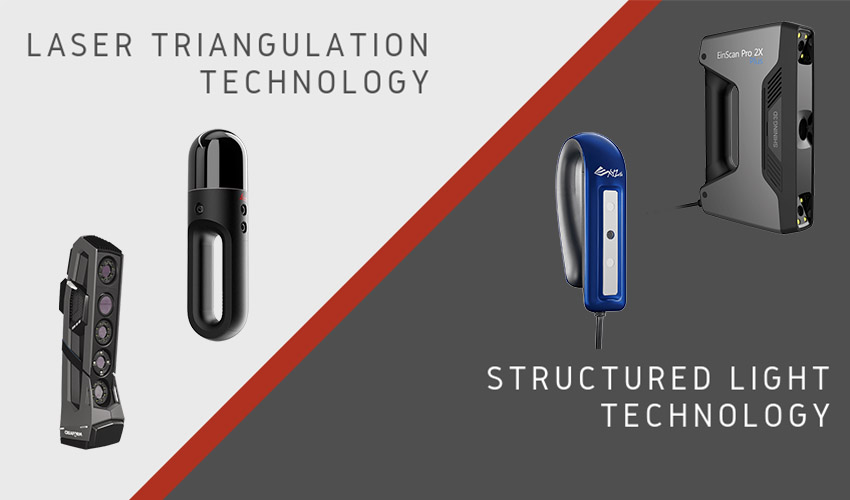
In the 3D printing workflow, 3D scanners are very often an essential step to facilitate the modeling of an object. They make it possible to collect data on the shape and sometimes depending on the 3D scanner, the appearance (such as colours). Therefore, 3D scanning enhances the design process, speeds up and reduces errors in data collection and also saves time and money.
3D scanning can be based on different technologies, each with their own benefits & limitations. In this article we explore the two main technologies used for 3D scanning for 3D printing, in other words, laser triangulation and structured light. So, how do laser scanners compare to structured light scanners? And most importantly, which one should you choose for your project?
Laser Scanners: technology, benefits and limitations
Laser scanners are based on trigonometric triangulation to accurately capture a 3D shape as millions of points. More precisely, they work by projecting a laser point or line onto an object and then capturing its reflection with sensors. Since the sensors are located at a known distance from the laser’s source, accurate point measurements can be made by calculating the reflection angle of the laser light. With the knowledge of the distance of the scanner from the object, the scanning hardware can map the surface of the object and thereby record a 3D scan.
This method is called triangulation because the laser dot (or line), the sensor and the laser emitter form a triangle as seen in the figure below. There are many different types of laser scanners on the market, you can choose between handheld, desktop or professional/industrial devices. The key is that they work within a short-range.
The benefits of the laser triangulation technology are its resolution and accuracy. When talking about accuracy, it is on the order of tens of micrometers. Also, it is possible to buy a laser 3D scanner for a very reasonable price as its design can be quite simple.
However, you should note that the properties of the surface to scan affect the scanning process. Therefore, very shiny or transparent surfaces can be quite problematic for this technology.
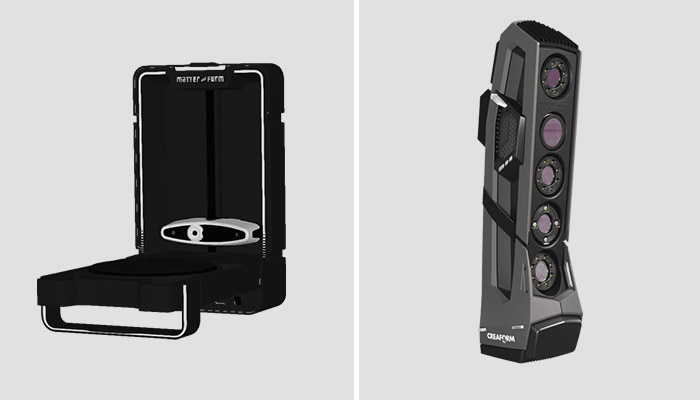
For example, the Matter & Form V2 (on the left) is a desktop laser 3D scanner, retailing for $749. The Go!SCAN SPARK (on the right) from Creaform is a professional handheld laser 3D scanner with a starting price around $30,000.
Structured Light Scanners: technology, benefits and limitations
Today many handheld 3D scanners for 3D printing use structured light technology. This technology also uses trigonometric triangulation but works by projecting a pattern of light onto the object to scan and not a laser line (or dot). The pattern is projected on the object using an LCD projector or some other source of stable light. One or more sensors (or cameras), slightly offset from the projector, look at the shape of the pattern of light and calculate the distance of every point in the field of view. The structured light used in the scanning process can be white or blue and the pattern of light usually consists of a series of stripes, but can also consist of a matrix of dots or other shapes.
This type of device just as the laser scanner works on short ranges and can be handheld or mounted on a tripod.
The benefit of structured light technology is how fast scans are. A scan can be achieved in about 2 seconds and the scanning area is also quite large. Just like laser scanners, structured light scanners are extremely accurate and offer a high resolution.
One of the downsides of this type of scanner is that they are sensitive to the lighting conditions in a given environment. This is less true of laser scanners. For example, working outside would be extremely difficult.
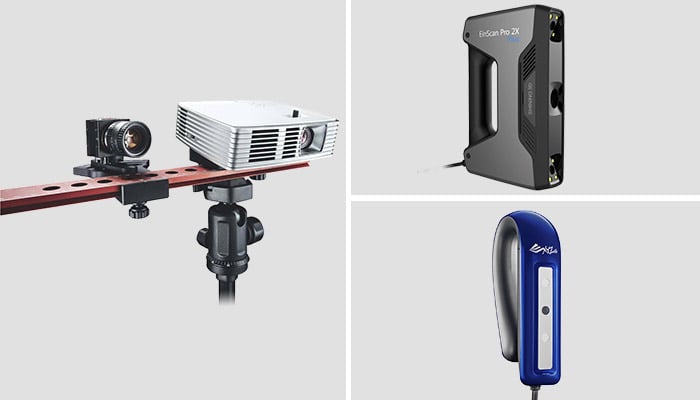
For example, the Structured Light Pro S3 (on the left) from HP is a mounted on tripod device, retailing at around $4,390 (3,930€). The EinScan Pro 2X (top) from Shining3D is a professional handheld structured light device, costing around $6,899 and the Scanner 2.0 (bottom) from XYZprinting is also a handheld device for beginners that costs $256 (226€).
Other Technologies
In the case of the two technologies described above, they are meant for short range 3D scanning. When you need to scan an object from a distance, you will find yourself limited. We will mention two more technologies designed to work for medium to long range 3D scanning.
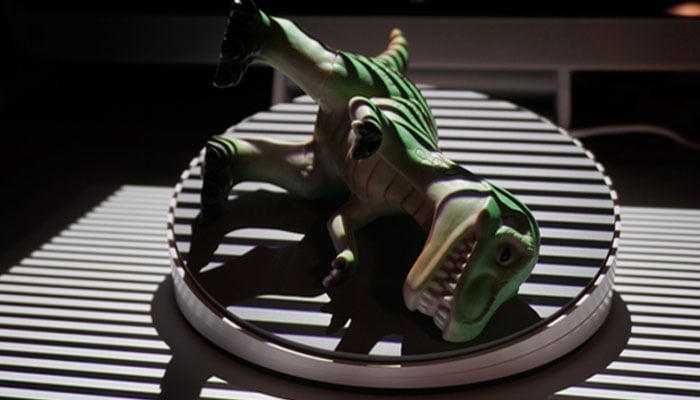
3D scanning using structured light technology
Time-of-flight 3D scanners use laser pulse technology. Just like laser scanners they use lasers to accurately scan a 3D object, however, the technology works completely differently. It works by knowing the speed of the laser light perfectly, then the system measures the length of time the laser takes to reach an object and reflect back to its sensor.
Another type of time-of-flight 3D scanner uses phase-shift systems. This technique works the same as laser pulse technology, but also modulates the power of the laser beam. The scanner compares the phase of the laser sent out and returned to the sensor. This allows it to be more accurate than a laser pulse 3D scanner but not as flexible for long range scanning.
Time-of-flight 3D scanners are definitely not as accurate as laser scanners or structured light scanners, however if you are looking to scan a large object, let’s say a building, you will mostly likely use this sort of technology.
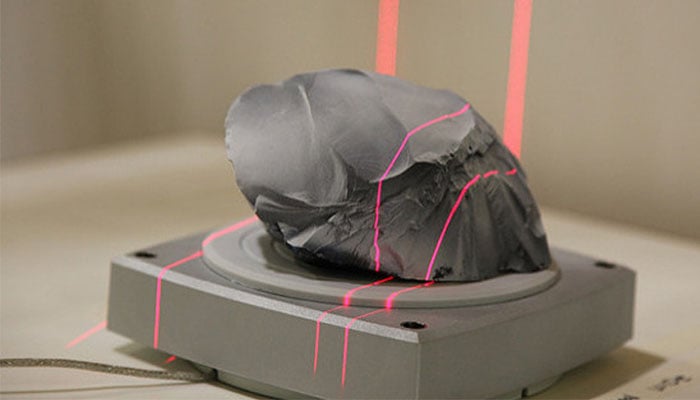
3D scanning using laser triangulation technology
Was this helpful to choose your which technology you should choose? Let us know in a comment below, or on our Facebook and Twitter pages! Sign up for our free weekly Newsletter, all the latest news in 3D printing straight to your inbox!
Good Afternoon,
Has your company ever did anything to take a 2D Adobe file and switch to a 3D file then project the design on say a airplane for paint masking.
Any information you would have would be great!