PEEK vs PEKK: Which High Performance Material Should You Choose?
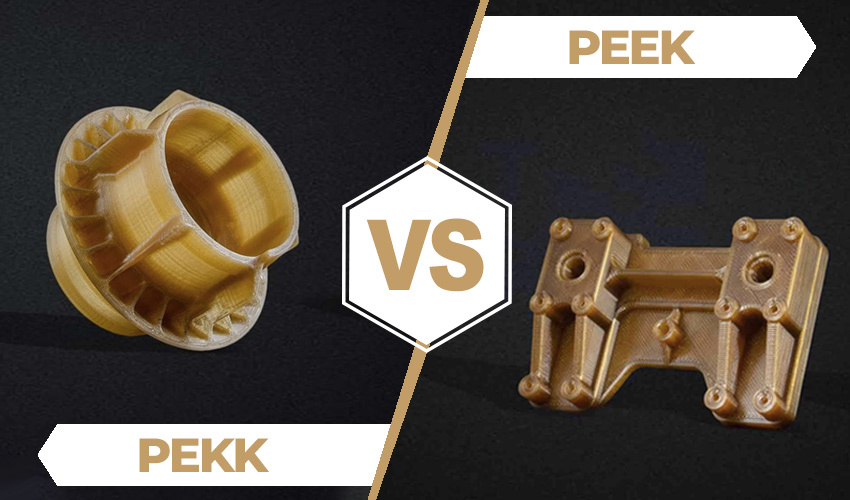
Materials in additive manufacturing are a key component of the process, giving the final part its own chemical properties and mechanical characteristics. Today, the market has a wide choice of materials, from polymers to metals, ceramics and organic inks. If we look at plastics, they are very numerous and can be more or less technical to print with. Whether it is a filament, resin or powder, each one has its specificities. Today we will focus on the category of high performance polymers and more specifically on the family of polyaryletherketones (PAEK). Two materials within the group are increasingly used by industry: PEEK and PEKK.
Generally used in the so-called traditional manufacturing industry (plastic injection, machining, etc.), PEEK and PEKK both have interesting thermal characteristics and are known for their strength. Often compared to metals, they have been compatible with certain additive manufacturing processes for a few years now, including material extrusion (FDM) and selective laser sintering. But what are the differences between these two high-performance thermoplastics? Which one should you choose? We explain everything you need to know!
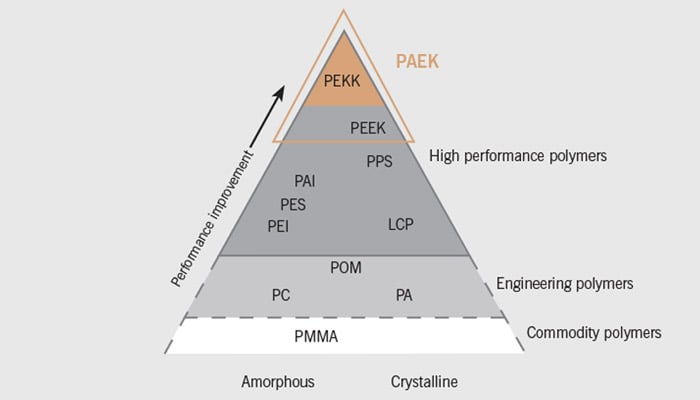
PEEK and PEKK are considered high performance polymers
Composition and characteristics
When comparing two high performance polymers, it is important to start with their composition and properties. This is in order to understand how they will perform during the manufacturing process, which can be a determining factor in your choice. These two materials belong to the PAEK family, a group of high-performance semi-crystalline and amorphous thermoplastics. In this family, the most commonly used polymer is PEEK, which is formed by a molecular structure of 1 ketone and 2 ethers. On the other hand, there is PEKK which has an inverse molecular structure: it has 2 ketones and 1 ether. The ketone bonds are more flexible, which increases the flexibility of the polymer in question. This means that the glass transition temperature (the temperature at which the polymer starts to soften) and the melting temperature are higher with PEKK.
Among the main characteristics of both materials, we find that they have high mechanical strength, high temperature resistance, fatigue resistance and low flammability. In the case of PEKK, this thermoplastic is more resistant to chemical fluids, has good dielectric stability and does not emit toxic fumes. On the other hand, PEEK has excellent mechanical properties and a good strength-to-weight ratio, making it a good substitute for some metals. Both polymers can be sterilized, facilitating their use in healthcare applications.
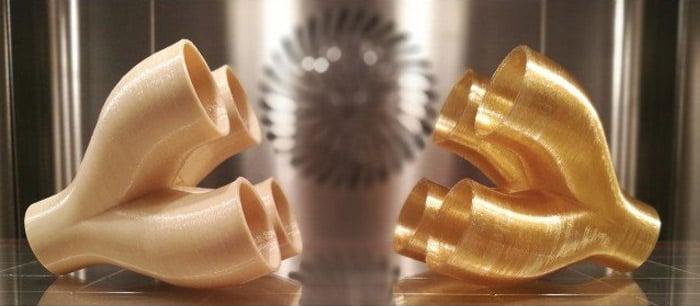
Parts printed using PEKK (photo credits: miniFactory)
PEEK and PEKK therefore have common properties, understandable as they belong to the same family of polymers. However, some of their characteristics differ due to their composition. The main distinction between these two materials is their degree of crystallinity and the speed of crystallisation. This concept refers to the total number of crystalline regions present in a polymer, and is represented as a percentage. In this case, we are comparing two semi-crystalline elements, but their degree of crystallinity depends and varies depending on how they are processed. In general, when we talk about the 3D printing process, PEEK can achieve a high level of crystallization, while PEKK has a much weaker crystal structure. The crystallinity affects the properties of the final piece while the speed of crystalization and the rheological properties have an impact on the ease of printing.
Ease of printing
In this section, we will mainly focus on Fused Deposition Molding (FDM). When dealing with high performance polymers, one needs advanced knowledge to avoid making mistakes during printing, mainly to avoid wasting these expensive materials. You also need a 3D printer that meets certain temperature requirements. When using PEEK for 3D printing, you need a machine with an extruder that can reach 752°F (400°C), as well as a chamber heated to 248°F (120°C) and a building plate that can go up to 446°F (230°C), so that the layers can adhere to it and to remove it without problems (thus preventing issues with warping). In the case of amorphous PEKK, the requirements will be very similar, but not as stringent. The extrusion temperature will typically be between 644 and 680°F (340 and 360°C). Additionally, it also requires both a heated build plate and a heated chamber.
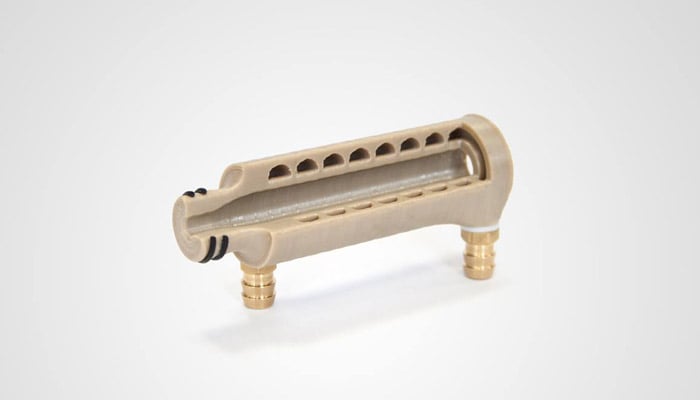
3D printed cooling system with PEEK (photo credits: Apium)
In technical terms, as the extruded filament solidifies, a partial alignment of the polymer molecular chains occurs. Based on the crystallization nuclei, the molecular chains fold up and form ordered regions. Therefore, the lower the percentage of crystallization nuclei in the polymer, the faster the cooling process will be, and therefore the layers will have a better adhesion to each other. This prevents warping. In other words, if the cooling and solidification process is too fast, the molecular chains will not bend properly, which will directly affect the adhesion of the part to the print bed, as well as its final mechanical properties.
As mentioned above, PEKK has a lower degree of crystallization than PEEK. This means that it will be less affected by the cooling process once the part is 3D printed. Therefore, in terms of ease of 3D printing, PEEK will be more complex and technical to use, as it requires specific knowledge that will allow the user to control the extrusion process as well as the cooling steps. On the other hand, when it comes to selective laser sintering (SLS) technology, the polymer behaves differently depending on the size of the parts you want to manufacture. This means that warping deformations will be much smaller or non-existent for smaller models, but the larger the part to be created, the more difficult it will be to control the printing parameters.
Post-processing of PEEK and PEKK
Post-processing of PEEK and PEKK is not the easiest of tasks. In FDM, the use of substrates to design more complex parts has become almost unavoidable. However, there are very few printing substrates that are compatible with these two thermoplastics: most solutions are not as heat resistant and therefore cannot be used.
However, some players have developed 3D printing supports specifically for these high-performance materials: For example, 3DGence and AquaSys. Note, however, that they are still more expensive than conventional materials.
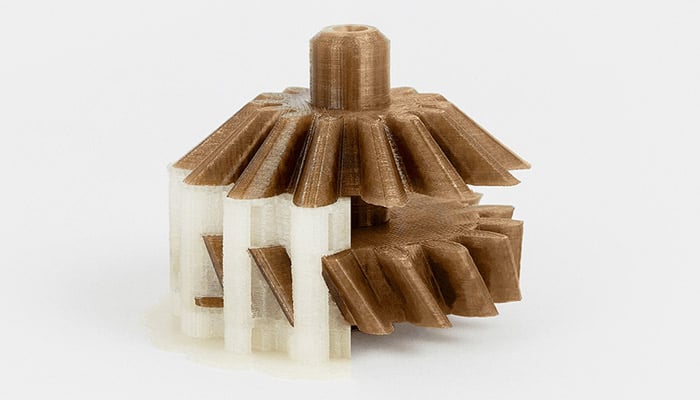
3DGence printing support is compatible with high performance materials (photo credits: 3DGence)
If you use the sintering process, the notion of a printing medium disappears but you will still have to evaluate the price per kilo of powder – we will come back to this a little later.
If we now turn our attention to post-processing methods as such, you should know that it is possible to anneal 3D printed parts with PEEK or PEKK to improve the fusion of the layers and give the final part even higher mechanical characteristics. Some 3D printers integrate this annealing step directly into their machine, as is the case with the miniFactory Ultra.
In addition, your part printed using PEEK can be machined using methods like drilling or milling. You can also metalize your parts if needed.
Applications
Regarding the use of PEEK and PEKK, we can find similar application sectors. The industries that adopt these high-performance materials the most are aerospace, automotive, and aviation, due to the aforementioned advanced characteristics, such as mechanical and high-pressure resistance, lightness, rigidity, among others. Being biocompatible, they are often used in the medical sector. PEEK has properties that facilitate osseointegration, i.e. the direct, structural and functional connection between a bone and the surface of an implant under functional load. On the other hand, PEKK has better resistance to chemical fluids, which is why it will be used more in the oil and gas industry. It can also be fire/smoke certified for the railway industry.
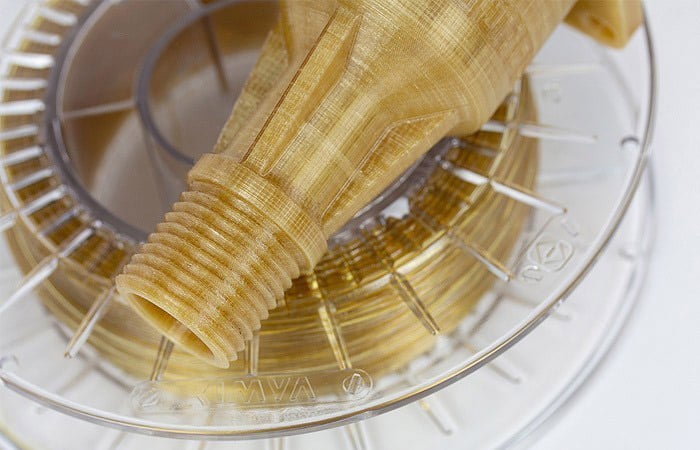
PEKK is used more in the oil and gas sector (photo credit: Kimya)
The cost of PEEK and PEKK
As you can imagine, PEEK and PEKK are more expensive than most polymers on the market due to their properties and characteristics. On average, a 500 gram roll of PEEK will cost you between €300 and 350 (about $350 to 420), while the same amount of PEKK will cost you between €350 and 400 (about $415 to 48). Of course, if you buy a high-performance, carbon-fiber reinforced polymer, the price will be even higher.
For PEKK powder, count on the price being about €500 for one kilogram ($597.06 for about 2.2lbs). A 3D SLS print can therefore quickly become expensive if we consider that an EOS P800 machine requires about 100 kilos of powder, based on its dimensions. Even if about 50% of the unused powder can be recycled, SLS printing jobs with high performance materials are quite expensive compared to nylon. So you’ll need to make sure that the 3D file is perfect with the correct printing parameters – mistakes can be expensive!
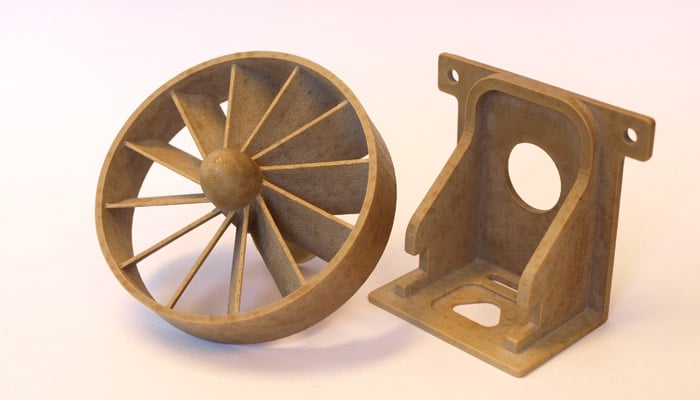
Parts 3D printed with PEKK via a powder sintering process (photo credits: Arkema)
Manufacturers
As explained above, PEEK and PEKK are mainly available as filaments, but there are also powders for sintering, though this is only possible with PEKK. Looking first at PEEK, the main producers of the material are chemists such as Victrex, Evonik, or Solvay. Most of them have developed their own range of filaments; Victrex, for example, offers its Low Melt PAEK (LMPAEK) and works with high-performance machine manufacturers such as Intamsys and 3DGence; Evonik has developed its VESTAKEEP® range for 3D printing of implants.
Beyond the chemists, there are several 3D printing material manufacturers that offer PEEK: 3DXTECH, 3D4Makers, W2 Polymer and OPM. Machine manufacturers are also getting in on the act, such as Zortrax with its Z-PEEK.
For PEKK, the French chemical company Arkema remains the largest manufacturer, whether in powder or granular form. Its PEKK Kepstan® range meets the needs of many manufacturers. The company Lehvoss also offers its LUVOCOM 3F PEKK 50082 NT in granulated form. Finally, Oxford Performance Materials offers a PEKK powder, particularly for the medical sector. As for PEKK filament manufacturers, some of the most prominent are the French brand Kimya, the Dutch company 3D4Makers, the American 3DXTECH or Nanovia.
Do you use PEEK or PEKK in additive manufacturing? Let us know in a comment below or on our Facebook, Twitter, and LinkedIn pages! Sign up for our free weekly Newsletter here, the latest 3D printing news straight to your inbox!
Hi there,
I am based in South africa,
What information do you require from me in order to quote on pekk?