All You Need to Know About HIPS for 3D Printing
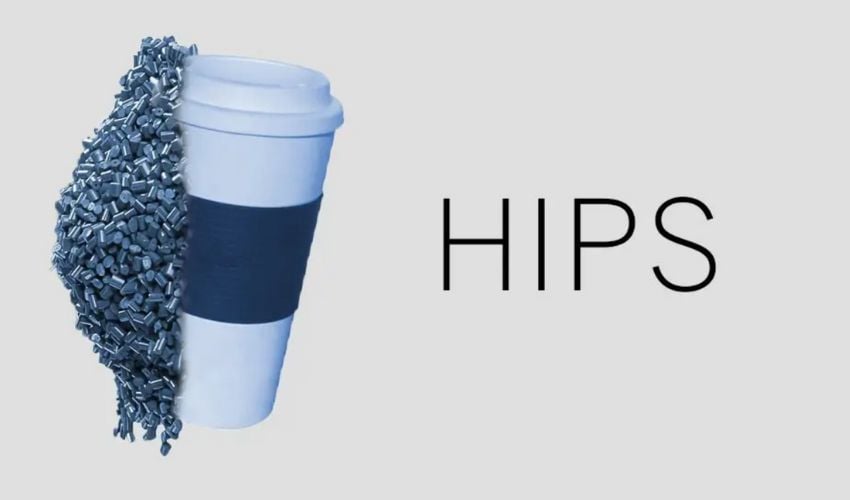
HIPS (High Impact Polystyrene) is a thermoplastic polymer based on a mixture of polystyrene and polybutadiene rubber. Many popular materials in 3D printing are particularly characterized by their resistance to chemical solvents. However, in the case of HIPS, the solubility is a great advantage because the material is mainly used in filament form as a support material in FDM 3D printing. Backing materials, or support structures, are used to print parts that have an angle of more than 45 degrees to prevent them from slipping or breaking during the printing process. After the printing process is completed, these structures are removed, which is easier with materials such as HIPS, which have high solubility. This article reviews the properties of HIPS as a filament and the advantages it offers as a support structure.
Production and Characteristics
HIPS (High Impact Polystyrene) is a widely used material in 3D printing due to its versatility and unique characteristics. The material is derived from polystyrene, a synthetic polymer commonly found in various consumer products. HIPS is produced through extrusion, where the filament is melted and then extruded through a nozzle to create the desired shape layer by layer. It has similar properties to ABS, but is harder and more impact resistant. As already mentioned, the material is particularly characterized by its comparatively high solubility in relation to certain chemicals, which allows for relatively smooth separation when used as a support structure. HIPS can be dissolved in a specific solvent, such as limonene, without damaging the main printed object. This property makes it perfect for complex designs and intricate structures. It is typically used in the area of ABS printing as support structure, and the temporary stability of the HIPS form plays a central role here. It also has a smooth and scratch-resistant surface, it is heat resistant, and its white translucent color simplifies coloring.
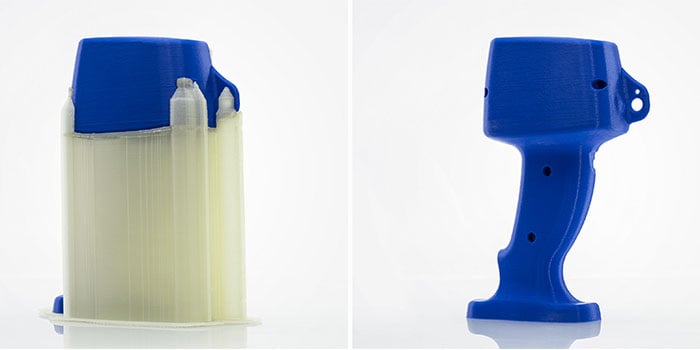
HIPS is mainly used as a support structure (Image credits: Zortrax)
However, HIPS plastic, despite its advantages, also has some disadvantages that must be considered. One drawback is its vulnerability to degradation when exposed to various chemicals such as solvents, acids, and alkalis. This can result in brittleness, discoloration, or breakdown of the material over time. Additionally, HIPS has a low temperature resistance and can become brittle in cold environments, making it unsuitable for applications exposed to extreme temperatures. Another limitation is its limited resistance to UV light, causing yellowing and brittleness with prolonged exposure, which reduces its overall lifespan.
Furthermore, HIPS exhibits poor flame resistance and can easily ignite and burn, making it inappropriate for applications where fire safety is a concern. Compared to other plastic materials, HIPS has relatively poor tensile strength and may not be as strong. It is not biocompatible and should not be used in medical applications involving direct contact with human tissue. Lastly, HIPS is not ideal for outdoor use due to its susceptibility to UV light, moisture, and extreme temperatures, all of which can accelerate its degradation and reduce its overall lifespan.
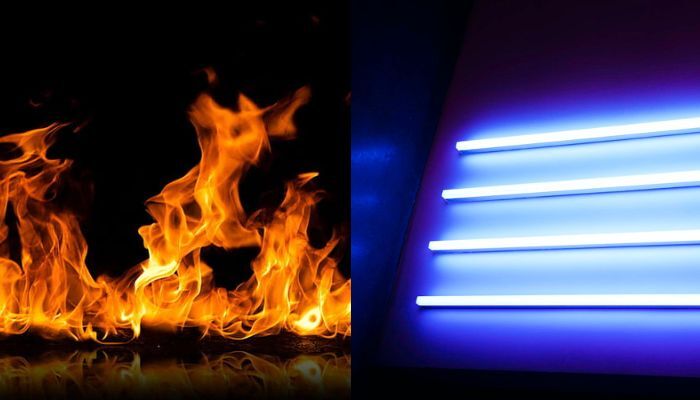
HIPS can be flammable and sensitive to UV light (Photo credits: Thompson Coburn LLP, Unsplash)
3D Printing with HIPS
If you use HIPS as a support structure, you should have a 3D printer with two extruders, which can reach a temperature between 230 and 245 degrees. In addition, you should have a heating bed that can reach temperatures between 90 and 110 degrees because HIPS tends to deform. It is also recommended to use a 3D printer with a lockable installation space to counteract deformation. You should protect your respiratory tract and ensure good ventilation, as printing with HIPS can create toxic fumes such as styrene.
After the printing process, you should wait until the printed part has cooled down completely before starting to remove the supporting structures. Unlike PVA or BVOH support structures, HIPS needs to be removed with chemicals. Therefore, you should only use it as a support structure for materials such as ABS, because certain other materials can be sensitive to the chemical limonic acid, and as a result, the component might be damaged. Before removing support structures with chemicals, it is recommended to first remove large parts by hand for cost reasons, as one liter of chemical costs approximately 30 euros. When dealing with liquids of this type, you should protect your eyes, respiratory tract and hands to avoid irritation.
Applications
HIPS plastic, known for its remarkable properties, finds widespread use in a variety of applications. One common application is product packaging, where its low weight, moisture resistance, and ease of molding into different forms make it a popular choice. It is frequently used in packaging consumer items like toys, electronics, and cosmetics. HIPS also serves well in the creation of signs and displays due to its good dimensional stability, allowing it to maintain its shape even under changing temperature and humidity conditions.
In the automotive industry, HIPS is used for manufacturing interior parts such as instrument panel components, benefiting from its strong impact resistance and ease of fabrication. Its lightweight nature, impact resistance, and moldability into various shapes and colors make it an ideal material for the production of toys and children’s products. Additionally, HIPS is widely used as a casing for electrical and electronic equipment, thanks to its exceptional dimensional stability and resistance to moisture. The medical field also benefits from HIPS, as it is employed in the manufacture of various medical devices, including orthopedic splints, owing to its high impact resistance, low weight, and ease of processing. Finally, HIPS is employed in food packaging applications, particularly in the production of clamshell containers, due to its moldability and strong moisture resistance.
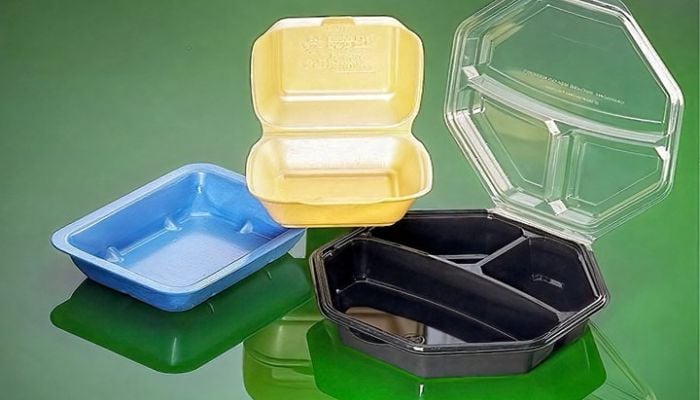
Photo Credits: Plastics technology
Manufacturers and Price
When it comes to pricing, HIPS plastic offers a cost-effective solution compared to other materials. A filament spool of HIPS is relatively inexpensive and can be purchased for prices ranging between $17 and $35. There are reputable manufacturers such as iGo3D, Zortrax, 3Dmensionals, and MatterHackers that offer HIPS filaments for purchase. However, it is important to consider certain factors before making a purchase. It is recommended to closely examine the ingredients of the HIPS filaments, as some may contain additives that facilitate the printing process but can also make it challenging to remove them after printing.
In addition to filament pricing, when selecting a manufacturer or supplier for HIPS, it is crucial to evaluate aspects beyond cost alone. Factors such as quality, reliability, product consistency, customer support, and delivery timelines should be taken into consideration. Thorough research, comparison of offerings, and reading customer reviews or testimonials can help make an informed decision. It is also worth exploring local suppliers or distributors, as they may offer competitive pricing and convenient logistics for procuring HIPS filaments. Engaging in discussions with industry professionals or seeking recommendations from relevant trade associations can provide valuable insights into reputable manufacturers, suppliers, and pricing trends in the HIPS market.
What do you think of HIPS as a support structure in 3D printing? Let us know in a comment below or on our LinkedIn, Facebook, and Twitter pages! Don’t forget to sign up for our free weekly Newsletter here, the latest 3D printing news straight to your inbox! You can also find all our videos on our YouTube channel.
*Cover image credits: Felfil
The first picture is the exact same as simplify3d’s and All3D’s articles on PVA. Are you sure that is HIPS? (the purple spring picture)