Dental 3D Printing: how are 3D technologies revolutionising this sector?
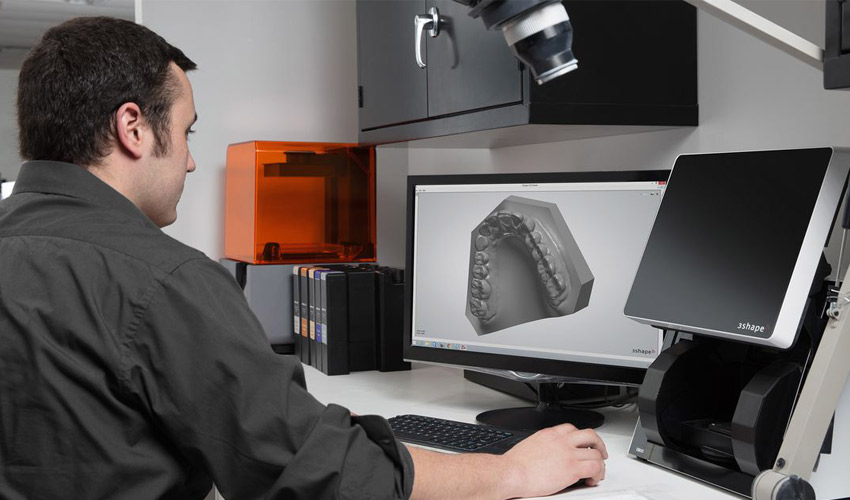
Additive manufacturing has reached a significant number of sectors and industries, subsequently offering important advantages in terms of productivity, costs, customisation and lead times. In the field of dentistry the technology creates solutions adapted to the needs of each patient. It is also a flourishing industry, not too long ago the consulting firm QY Research announced that dental 3D printing was expected to reach $930 million by the end of 2025. In other words, the market is expected to grow at an annual rate of 17%, which can be explained by the constant development of 3D technologies and their materials. Indeed, dental 3D printing includes different processes such as stereolithography or direct metal sintering and therefore a variety of materials: resins, plastics, metals, etc. The application of 3D printing in dental is wide, it is possible to make surgical guides, crowns, trays and dentures and each solution is adapted to each patient with high precision.
It is therefore important to determine which 3D technologies are preferred in this sector and best suited for each application. Also, how are dental professionals reacting to the rise of 3D printing? And how are they preparing and training themselves?
Firstly, the dental sector can be divided into two families of actors: dental practices and dental prosthesis laboratories. Traditionally, they have worked together in the production of custom medical devices (gutters, crowns, bridges, etc.). In fact, the dentist takes an impression of the patient’s teeth and sends to it to the laboratory, which then manufactures the device usually from plaster. This procedure will take a few days, not to mention the round trips between the dentist and the laboratory. As for the patient, he/she will have to make an appointment again without any guarantee that the device will be adapted to his/her needs. The arrival of 3D technologies is disrupting this procedure and completely dematerialising work processes.
Dental 3D Printing Technologies and their Materials
When we talk about dental additive manufacturing, it is important to understand that several technologies are involved, whether it is fused deposition modeling, photopolymerisation or laser sintering, the choice will depend on the type of application at stake. Olivier Bellaton, Director and Founder of Biosummer3D points out that each process comes with its own advantages and disadvantages. For example, the FDM process will manufacture pieces “at a cost of a couple of pennies and no post-processing after printing. However, speed, accuracy and biocompatibility are not present.” Generally, the latter technology will be used to create orthodontic dental models for thermoform gutters, whether for alignment, bleaching or restraint. On the other hand, 3D printed dental solutions using PEEK are emerging. The 3D printer manufacturer, IEMAI3D said, “There are many advantages to making partial prostheses with PEEK. It is a strong and lightweight material that will improve patient comfort. The frame of the prosthesis is produced without metal and is completely neutral in terms of taste.”
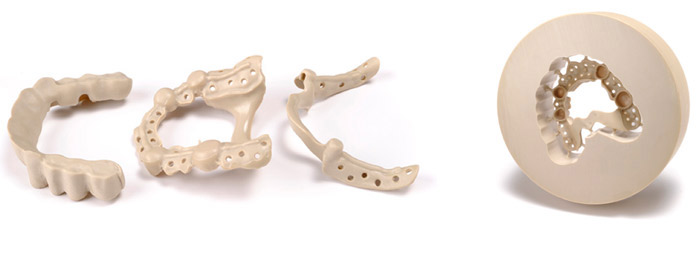
Photo Credits: Juvora
Another additive manufacturing process used in the dental sector and probably the main one is photopolymerisation. Whether we are talking about stereolithography (SLA) or DLP, this process offers a much higher resolution, and most importantly biocompatible materials. In this case, liquid resins. Anton Lopez, Channel Sales Manager France at EnvisionTEC told us, “Combined with CE/FDA approved materials, photopolymerisation and especially DLP, gives more accurate printing which allows more accurate devices to be created. The finishing is much less complex, which reduces manufacturing time. Also, it is very easy to change materials and print for different applications. This is very beneficial for the dental industry because professionals can treat their patients more quickly”. In terms of applications, this technology offers more possibilities due to its precision; we are talking about surgical guides, temporary crowns and bridges, calcinable elements such as dental stellites, etc.
Finally, we also find metal additive manufacturing as a process in dentistry. Mainly used to produce implants, stellites, or nickel-chromium screeds. Oliver Bellaton comments, “This technology requires sustained production to absorb investments of up to several hundred thousand euros with skills coming from the industrial world rather than the dental sector.” Metal printers are much more expensive than other technologies and will sometimes require more post-processing work reducing productivity for some. After talking with a dental technician, he explained that a crown made by machining requires 15 minutes of work, however a 3D printed metal one requires 5 hours of printing. On the other hand, in terms of cost per unit, additive manufacturing is much more interesting, 75 cents for the latter against more than 7 euros.
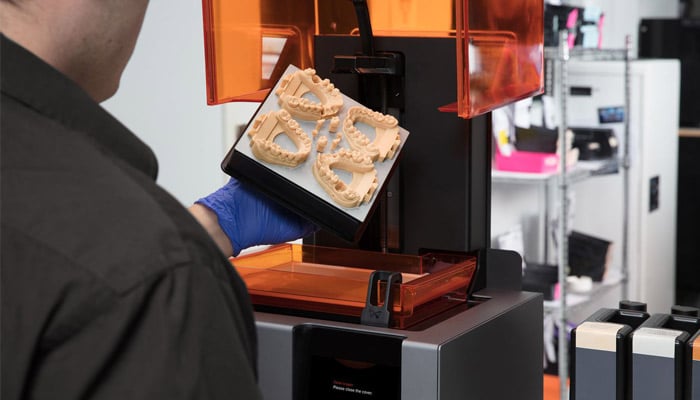
Photo Credits: Formlabs
A dematerialised manufacturing process
As mentioned above, 3D technologies should be able to provide greater precision and reduce manufacturing times. But what are the new steps to follow when creating 3D printed dental devices? Oliver Bellaton explains, “The physical impression will be replaced by a 3D digital impression taken by the dentist with an intra-oral scanner (meaning a camera will reconstruct in 3D and in real time the surface of the teeth and gums). This 3D file can then be sent over to the dental laboratory through a secure web platform. The laboratory will review the digital impression and model the morphology of the crown in its design software (CAD), taking into account the limits of the gum, interference with other digitised teeth and even the shape of the patient’s smile with a face scanner. In case of doubt, a quick exchange by split screen with the dentist allows to validate the shape of the crown. The 3D file of the crown can then be sent to a 3D printer for manufacturing. In the near future, the dentist could have the 3D printer directly in the office for simple manufacturing. All digital flow configurations are possible. The process may take only a few hours, which in some cases means that the patient could only be brought in to the practice once.” The result is reduced logistics flows and production times, a personalised system that is much more adapted to the patient’s morphology.
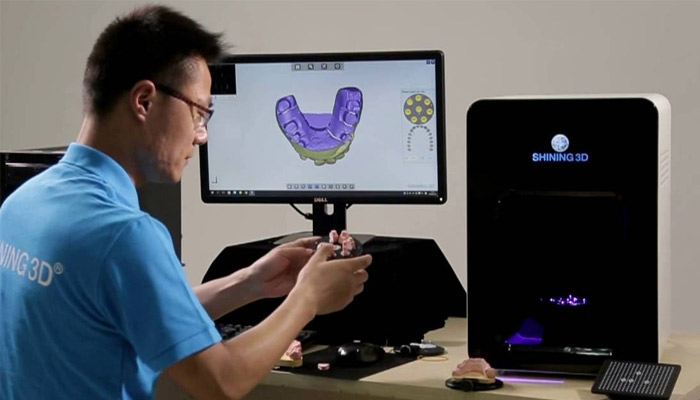
Photo Credits: Shining 3D
Dentists and dental technicians will therefore have to equip themselves with 3D scanners or printers but also with CAD software, an obstacle for many professionals today. Nicolas Klaus, Dental Product & Business Development at Formlabs explains, “The essential pillars of these new working methods are 3D scanners, CAD software and 3D printing. Generally, there is a point of resistance in the software on which training is not obvious”.
What is the future of dental 3D printing?
While 3D technologies have significant advantages for the sector, their adoption may frighten some practitioners because it requires a new work logic, training in software, scanners and printers and a certain amount of confidence in these innovative processes. Today, for example, more than 50% of French laboratories have equipped themselves with 3D scanners and machine tools and 20% with 3D printers. These players recorded a 70% increase in turnover, proof that they represent real gains for dental professionals. Anton from EnvisionTEC added, “Most practitioners are very receptive and open to new digital technologies. It is simply a matter of asking clinicians and dental industry professionals to understand and trust the new digital technology and its benefits for themselves, their company and their patients. And of course, education and training play an important role. This is why many manufacturing companies are investing in this field to better understand the technology and its clinical applications“.
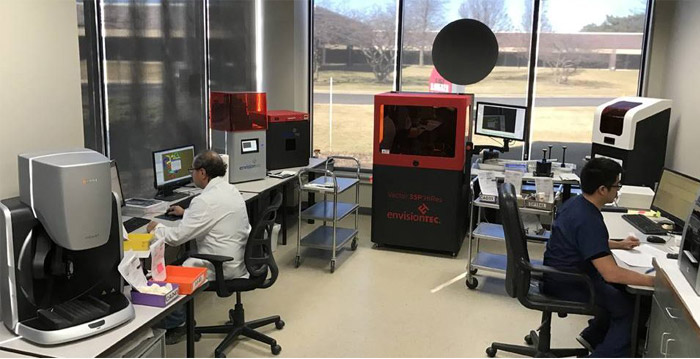
Photo Credits: EnvisionTEC
The future is therefore encouraging for the dental 3D printing industry with many enthusiasts who see the technology as a good way to improve their efficiency and the safety of their interventions. In fact, SmarTech Publishing’s 2018 report showed a 35% annual growth in 3D dental printing, reaching $9.5 billion in 2027 – the report takes into account hardware, materials and parts printed in 3D.
Are you excited for the future of 3D printing in the dental field? Let us know in a comment below or on our Facebook and Twitter pages! Sign up for our free weekly Newsletter, all the latest news in 3D printing straight to your inbox!
I am writing from Argentina. Nerd to know if already Is possible to create complete dental prótesis of some material non-derivated from petroleum…such as acrylic. Some material from the vegetable kingdom. Can you informe? Thanks.
Tati
Dear Friend,
Is that dencher made out of resin in dlp is directly fixed in mouth?
Thanks in advance