#3DStartup: Yuyo and their 3D printed surfboards
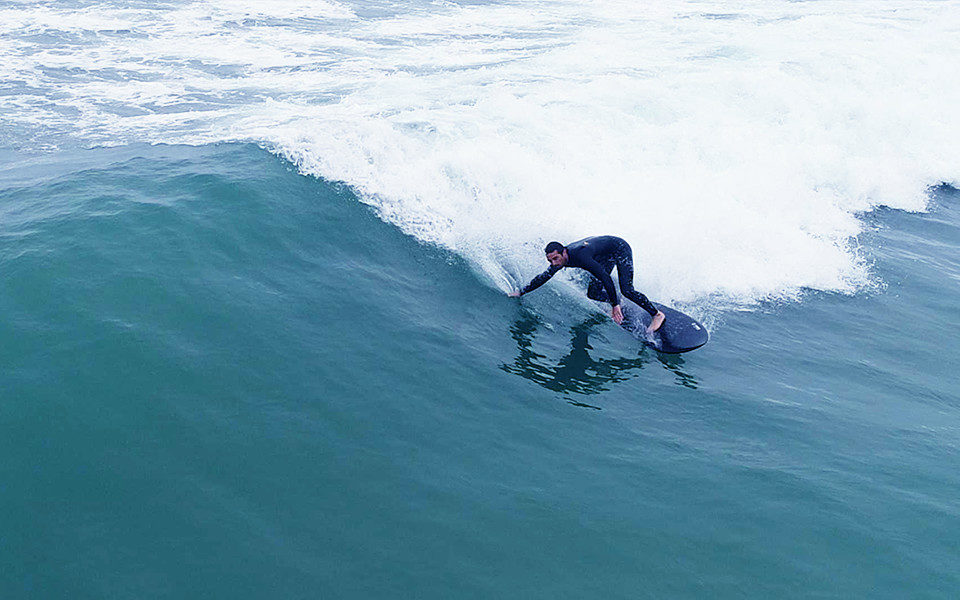
Yuyo is a young French Startup, who makes 3D printed surfboards from biodegradable materials. Since its creation, it has been striving to protect the oceans through greener products. All while maintaining the level of performance expected by many surfers around the globe. By turning to 3D printing, the startup is able to offer custom and locally made boards while reducing the level of waste normally achieved by traditional manufacturing methods. We met Yuyo founder, Romain Paul, who will tell us a little more about the entire production process but also about the link between 3D printing and sustainable alternatives. Technologies could indeed be useful to us in order to respect our planet more.
3DN: Can you introduce yourself and your link to 3D printing?
I have been a surfer since the age of 8 and a shaper for ten years. I decided now to devote myself along with my 3 partners to try to solve the “paradox of the surfer” i.e. to offer practitioners of this sport of ecological and responsible boards, in line with their environmental convictions. We first oriented our research towards wooden constructions, but we had trouble finding the right recipe: glue toxicity, economic viability problems etc. Having worked for an online printer, we regularly attended trade fairs. After a few training sessions and initiation in a Fablab (Labsud in Montpellier) with professionals, we discovered 3D printing’s great potential.
3DN: Explain to us the paradox of the surfer?
The surf industry is characterised by a historical paradox born in the 1950s. At that time, board manufacturers began to use polyurethane and composite alloys, fiberglass and polyester resins in the design of their models. The laminated planks were not only lighter than their larger wooden sisters. But also highly resistant to mechanical stress while retaining the flexibility and fluidity sought by practitioners. Initially reserved for high performance, these manufacturing methods quickly spread to become the undisputed standard in the manufacture of surfboards.
Today, more than half a century later, this method of manufacture has remained the same! The supply of materials has increased slightly with the introduction of expanded polystyrene and epoxy resins, but the planks are made in the same way. A piece of foam (polyurethane or polystyrene) is cut to shape and covered with one or multiple layers of fiberglass and polyester or epoxy resin. In other words: a real cocktail of pollutants, non-recyclable and material particularly toxic for the marine environment. In addition to their impact on the environment, the handling of these products is also dangerous for humans and endangers the health of shapers.
However, by practicing surfing, one naturally develops a particularly acute environmental awareness. The waves on which we surf are the product of natural elements: currents, winds, tides, morphology of the seabed etc. The practice of our sport depends on the goodwill of the seas and oceans, which are our playground. This strong connection to the natural environment makes the culture of surfing a culture by essence eco-responsible. There is therefore a real contradiction between the surfers’ vision and environmental beliefs and the toxicity of the equipment they use. It is this paradox that we wish to solve by proposing bio-sourced surfboards, that is to say composed of 95% natural material, vegetable or mineral. Planks harmless for the marine environment.
3DN: Why did Yuyo turn to 3D printing to make your surfboards?
Additive manufacturing allows us to:
- Use natural materials: we print the internal structure of our boards with PLA, a biopolymer of vegetable origin, entirely biodegradable.
- Produce locally, close to practice sites and thus reduce CO2 emissions from transport
- Limit the margin of error and increase the level of precision by reducing human intervention
- Significantly reduce waste generation compared to traditional subtractive manufacturing
- Produce custom-made boards on demand, with unlimited potential for personalisation.
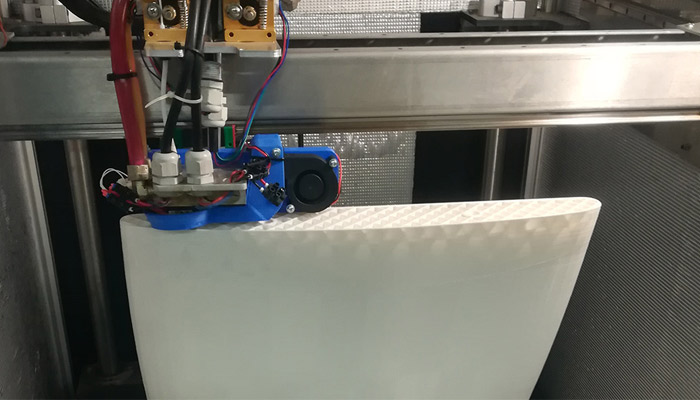
Yuyo printing a board
3DN: Can you tell us more about Yuyo and your 3D printing process?
We made several prototypes with different machine manufacturers in Europe and we finally chose the company Tobeca, based in Vendôme. We ordered a machine form them, that will be installed in our Montpellier workshop in early January. This machine allows us to manufacture boards up to 2,40 m high and 65 cm wide. It takes an average of 30 to 40 hours to print a board. After printing, we laminate our boards with a natural fiber and a biosourced resin.
3DN: How do you think 3D printing can help preserve our environment?
3D printing can relocate industrial production. This contributes to the economic development of the territories concerned but also reduces greenhouse gas emissions linked to transport. It also considerably reduces the production of industrial waste, as we only use the strict amount of material needed to manufacture each piece. Finally, 3D printing allows the democratisation of ecological materials such as PLA.
3DN: Any last words for our readers?
Surf green, surf Yuyo I invite you to see our different board models HERE .
What do you think of Yuyo and their 3D printed surfboards? Let us know what you think in a comment below or on our Facebook and Twitter pages! Don’t forget to sign up for our free weekly Newsletter, with all the latest news in 3D printing delivered straight to your inbox!