A Closer Look at 3D Printing Materials: Ceramics and Organic Material

Over the years, additive manufacturing has grown exponentially. And currently there are many different 3D printing technologies that allow objects to be built depositing of layers one by one. At first, printing materials were scarce, but gradually and through research and development, it has been possible to expand the number and types of materials. The best known are certainly the polymers – PLA, ABS, resins, nylon and so on – and metals. However, today we want to draw your attention to about two lesser known but increasingly important material groups: ceramics and organic materials.
Ceramics
Ceramics
When we talk about ceramics, we often think of the more traditional ones like clay or porcelain. However, there are also more technical ceramics for advanced applications. Currently, there are two main groups of technical ceramics on the market today: oxides and non-oxides. The first group includes the metal oxides alumina, zirconia and silica, and the second group consists of materials such as silicon carbide, silicon boride or silicon nitride. The use of these materials is ideal for parts that require high temperature and wear resistance. A ceramic 3D printer can use different manufacturing processes, from powder bonding to stereolithography to extrusion. You can learn more about the different ceramic 3D printers on the market in our listing.
Sand
Sand could also be considered to fall under the ceramic umbrella. It is used to create complex parts that take advantage of the benefits of additive manufacturing, primarily for the manufacture of foundry molds. The use of this material reduces waste, saves energy and the manufacturing time is much shorter than other techniques. It can be used for mass production of finished products or for prototyping, with machines like ExOne’s S-Max Flex. In the video below, you can see an example where Sandhelden uses sand to create bathroom collections.
Concrete
Concrete is another one of the ceramic materials we want to highlight. To make it, stone aggregates and water are mixed, creating a uniform mixture that is also compatible with 3D printing. Thus, additive manufacturing in the construction industry has become increasingly important. Using concrete as a building material is very economical, while printers range in price from $180,000 to over $1 million. Some of the printers you can find on the market include the Apis Cor House printer or the Crane from WASP. Speed is one of the advantages that characterize these machines: in 48 hours, you can erect the walls of a house!
Stone
Stone is another ceramic options compatible with additive manufacturing. This material is mainly used in the form of filament for FDM/FFF 3D printers. The stone strands are made up of a mixture of plaster and plastic. Manufacturers offering both filaments include ColorFabb and Formfutura. The surprising thing about these filaments is that they really look and feel like stone, ideal for decorative applications that seek a more natural finish.
Organic Materials
Biological Tissue
Having looked at ceramic materials, let’s now turn our attention to organic materials, starting with bioprinting. Bioprinting is the 3D printing of an ink composed of cells that can be used to obtain skin, tissue, tendons or even organs. The printing is usually done by depositing successive layers through a custom-made syringe. There is still a lot of progress to be made, but the advances are real.
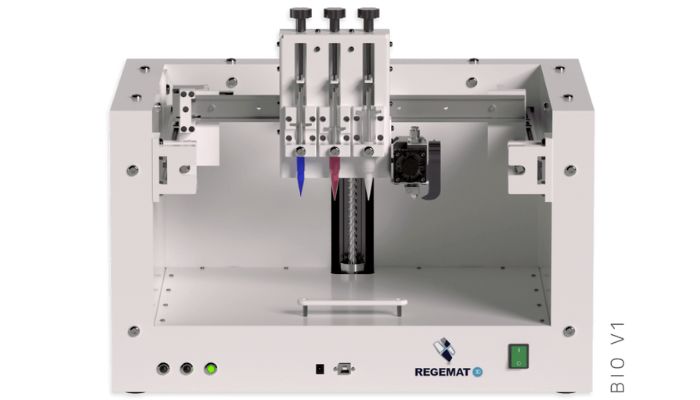
The BIO V1 3D bioprinter (photo credits: Regemat)
Wood
Wood is an organic material that is mainly used in the form of filament, similar to stone, for FDM/FFF 3D printers. However, there are also solutions like the Desktop Metal Shop System™ – Forust Edition, wherein binder jetting is used for wood 3D printing. For the 3D printing filaments, they contain 30-40% wood fiber and 60-70% polymer. Among the manufacturers that offer these filaments are also ColorFabb and Formfutura. The interesting thing about this material is that they really resemble wood, both visually and to the touch. They can also be used for the production of more sustainable finished parts.
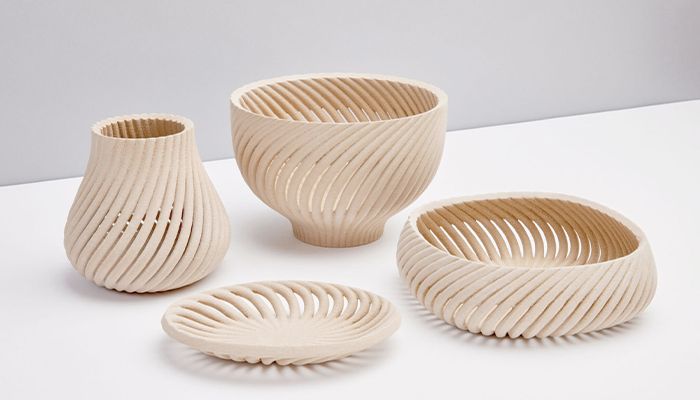
Photo Credits: Forust
Wax
This organic material is primarily used for molding, whether for mechanical parts, artwork, dentistry or jewelry making. In terms of material, for example, M3 Hi-Cast is used with 3D Systems’ ProJet MJP 3600W and 3600W Max 3D printers. Note that Stratasys’ Solidscape specializes in wax 3D printing machines, with models such as the 3Z Studio, 3Z Pro and MAX2. They work similarly to plastic FDM printers, but include a milling tool in each layer to make them uniform and level. Finally, 3D Systems offers the ProJet MJP 3600W, or Project MJP 2500W, ideal for jewelry making.
Food
Who would have ever thought that we could print food with 3D printers? Pasta, ice cream, chocolate, bacon, meat… 3D printing is revolutionizing the kitchen! And you may be wondering if there are food printers, the answer is yes. Among them are Foodini by Natural Machines, Brill 3D Culinary Studio, Mycuisini 2.0 or Choc Creator V2 Plus for chocolate printing.
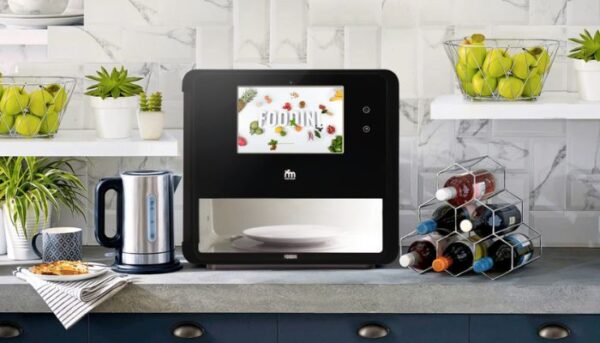
The Foodini 3D printer (photo credits: Natural Machines)
What do you think about ceramic and organic materials? Do you use them for your 3D printing projects? Let us know in a comment below or on our LinkedIn, Facebook, and Twitter pages! Don’t forget to sign up for our free weekly Newsletter here, the latest 3D printing news straight to your inbox! You can also find all our videos on our YouTube channel.
It’s so cool that sand can be used to make foundry molds so that you can make all kinds of parts. What kinds of sands are best to use with 3d printers? I think it’s cool that sand can be used to make things.