Webinar: Metal additive manufacturing for industrial applications
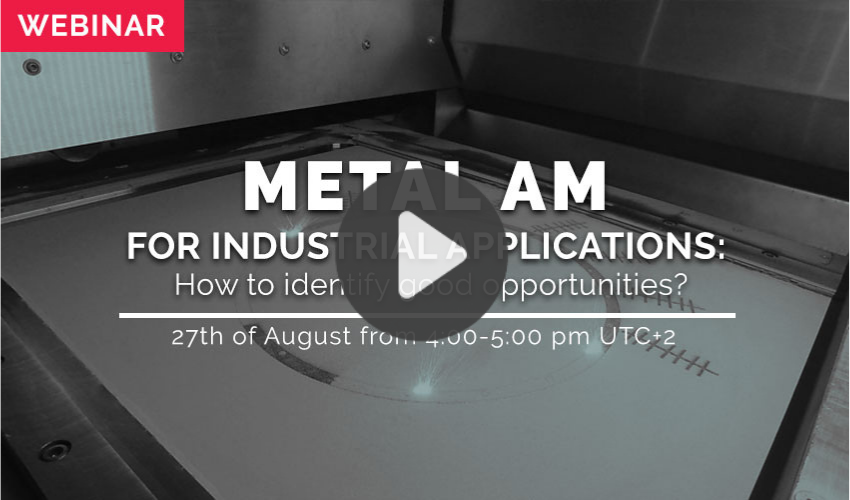
Additive Manufacturing can represent the next stage of evolution for industries around the world. This is already the case in segments like Aerospace, Healthcare or Motorsports. But, for many companies which are aware of the specific challenges of these segments, what value can metal additive manufacturing technology bring to their manufacturing processes? And when should they invest in metal AM?
On the 27th of August, we held a webinar, together with GF Machining Solutions, to list and discuss the key points a company should consider in order to evaluate the benefits of the Laser Powder Bed Fusion (LPBF) process – the most popular metal AM process. Our approach was explained through two real case studies, one related to cutting tools and one related to machinery components. This latest case was presented by the German company ARNOLD UMFORMTECHNIK GmbH & Co. KG, from the Würth Group, a user of metal AM technologies and client of GF Machining Solutions.
For some context, in recent years, metal additive manufacturing has taken an important place in the global 3D printing technology market: there has been a growth in the number of manufacturers of machines, stronger alloys and materials have emerged, software that optimizes the entire design process is available, etc. The final objective of these initiatives is to democratize its use and support companies in the implementation of reliable and sustainable technology, most often in addition to their subtractive manufacturing solutions. This is the mission of GF Machining Solutions. It has turned to metal additive manufacturing a few years ago now and has developed an entire optimized value chain, mastering all stages of manufacturing, from design, printing to post-processing .
Based in Switzerland GF Machining Solutions, belongs to Georg Fischer Group and is present in more than 50 countries around the world. The company turned to metal additive manufacturing a few years ago and has since developed an entire optimized value chain, mastering all stages of manufacturing, from design to printing to post-processing. By combining sophisticated fastening technology with intelligent services, the German company ARNOLD has become one of the world’s leading manufacturers and development partners of high-quality fastening elements and cold-forging press parts.
Watch the replay
Agenda
- 16:00 to 16:05: Introduction and survey by 3Dnatives
- 16:05 to 16:10: Adoption of Metal AM Technology: what is the current status?
- 16:10 to 16:25: Integrating AM inside a manufacturing process chain: what are the key factors to consider?
- 16:25 to 16:40: Case study 1
- 16:40 to 16:50: Case study 2
- 16:50 to 17:00: Q&A
Speakers
Romain Dubreuil has worked with GF Machning Solutions for four years, joining as an AM engineer. He then led a team of additive application engineers including responsibilities for business development. Prior to GF Machining Solutions, he was a Production Engineering Manager for Injection Molding where he also led production teams in product development.
Uwe Wolfarth is the Senior Director Research & Development / Licensing at ARNOLD UMFORMTECHNIK GmbH & Co. KG. By combining sophisticated fastening technology with intelligent services ARNOLD has become one of the world’s leading manufacturers and development partners of high-quality fastening elements and cold-forging press parts.