How to Choose Between a Bowden and Direct Extruder for 3D Printing
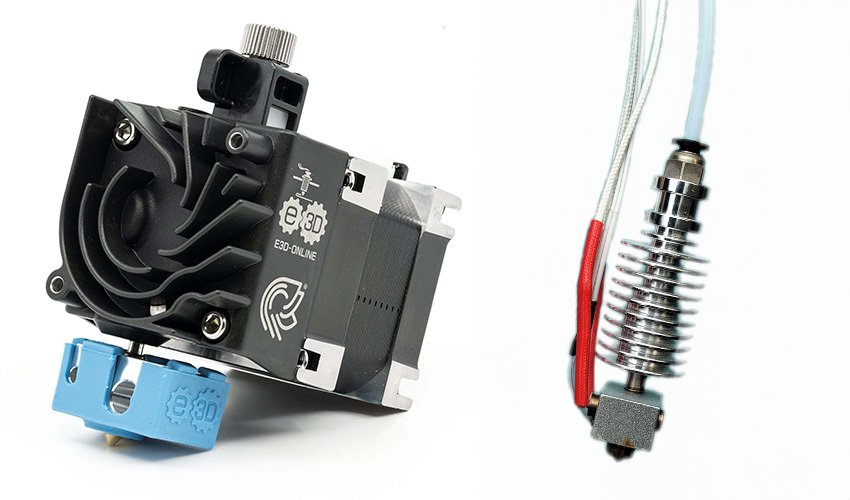
In the 3D printing landscape, the extruder configuration you choose can make all the difference between a successful, flawless print and a frustrating trial-and-error process. FDM 3D printing extruders come in a variety of shapes and forms, but despite the intricate differences of each extruder, they all cater to either one of two types of setup. Bowden and the direct drive extruders are the two distinct powerhouses, each armed with unique advantages and challenges. But how to know which one to choose? To unravel the intricacies of these extruder types, we took a closer look at the performance of both in terms of print quality, speed, versatility, and more.
Before going into the differences, it is important to look at what exactly an extruder is. An extruder is a vital component of the FDM (Fused Deposition Modeling) 3D printing process. Not to be confused with the nozzle, it serves as the mechanism responsible for precisely feeding filament material into the hot-end of a 3D printer where it is then melted and deposited layer by layer to create a three-dimensional object. The extruder is tasked with maintaining consistent filament flow, controlling the rate of extrusion, and ensuring accurate placement of the molten material onto the print bed. Its role in the printing process makes the choice of extruder type a critical decision, as it directly impacts factors such as print quality, speed, material compatibility, and the overall capabilities of the 3D printing system.
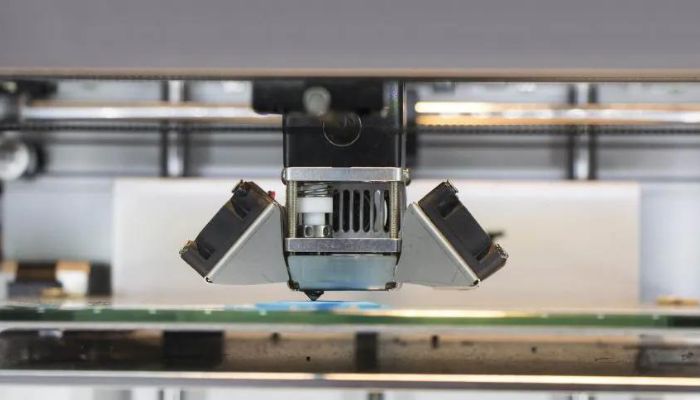
Photo credits: Sculpteo
Bowden vs. Direct Extruder: What to Know
But what exactly is the difference between the two? A Bowden extruder is characterized by its separation of the extruder motor from the hot-end assembly. A PTFE tube (also known as a Bowden tube) connects the components, allowing for reduced moving mass on the carriage and enabling faster movements during printing. This configuration is favored by those aiming for smoother, faster prints. The Bowden setup excels in minimizing vibrations, which is especially advantageous for printing intricate and delicate models. That’s because there is less mass to suddenly move. Since the force of acceleration is equal to mass times speed, it is easier to quickly accelerate and decelerate a lighter object. Also, the lighter the object, the less momentum (kinetic energy) it builds up. However, the increased distance between the extruder motor and the hot-end can result in challenges with flexible filaments, as they tend to buckle inside the tube, affecting extrusion consistency. Part of this problem is also the friction induced by the PTFE tube, or Bowden tube.
In contrast, a direct drive extruder boasts a direct drive coupling of the extruder motor and the hot-end, eliminating the need for a lengthy tube. This setup provides enhanced control over filament movement, making it an ideal choice for printing with a wide array of materials, including flexible filaments. The direct drive extruder’s ability to exert consistent pressure on the filament results in better extrusion control and improved retraction performance, ultimately reducing the chances of stringing and oozing. However, the increased mass on the carriage can introduce vibrations and limit printing speeds, leading to ghosting and ringing which is reduced in a Bowden extruder.
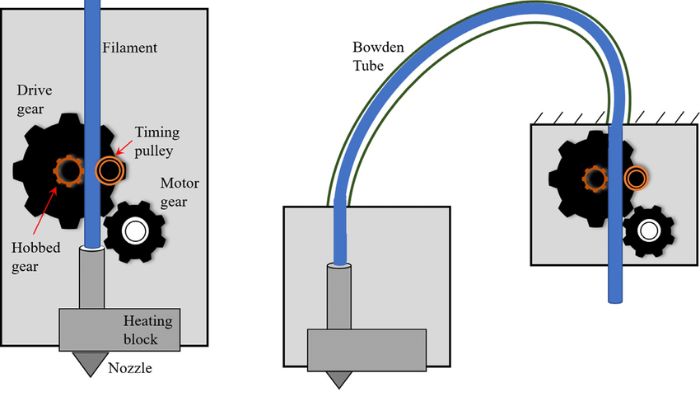
A visual comparison between the system properties of a direct drive extruder (left), versus a bowden extruder (right) (photo credits: ResearchGate)
Choosing a Nozzle
Of course the extruder is not the only thing that needs to be considered. The choice of a nozzle significantly impacts the quality and efficiency of your prints, regardless of whether you’re using a Bowden extruder or a direct extruder. When it comes to Bowden setups, where the filament has to travel through a tube before reaching the nozzle, the selection of the right nozzle becomes especially crucial. Indeed, nozzles made from materials with high thermal conductivity, such as brass, are particularly effective in these setups.
This is because the longer filament path in Bowden systems can lead to increased friction and resistance, potentially affecting the extrusion process. Using a nozzle with good heat conductivity helps in maintaining consistent filament flow and reducing the risk of clogs, this is because in a Bowden system in particular, reducing the pressure exerted on the filament by the nozzle prevents issues down the line. Using a nozzle with good heat conductivity or a high-flow nozzle (Bondtech CHT or E3D volcano for example) helps in maintaining consistent filament flow and reducing the risk of clogs.
In contrast, the dynamics of direct drive extruders bring about a different set of considerations. In these setups, the extruder motor is located closer to the hot-end, resulting in a shorter filament path. This reduced filament path minimizes the friction and resistance encountered by the filament, enabling a wider range of nozzle sizes to be employed effectively. Additionally, when working with a variety of filaments, some of which might contain abrasive additives, the composite filled filaments or wood filled filaments have small particles in their filling which can wear down very fast. But this same abrasive nature will also wear down the PTFE tube of the Bowden setup.
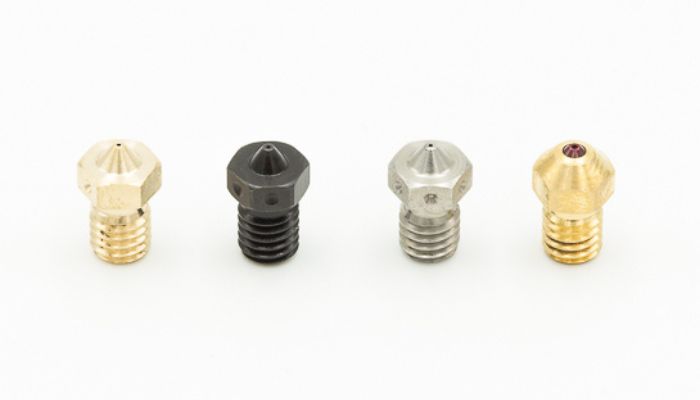
The material and diameter of a nozzle plays a vital role in determining the balance between print quality and speed (Photo credits: filament2print)
Printing Considerations
When aiming for exceptional print quality and intricate detailing in a quick amount of time, a Bowden extruder often takes the lead. Its lightweight nature minimizes the chances of sudden movements that could mar the print’s surface when printing at high speed. This makes it an excellent choice for projects that demand high precision, such as architectural prototypes and intricate art pieces. On the other hand, a direct drive extruder’s immediate control over filament flow is better suited for prints requiring diverse material usage, as well as models that demand accurate retractions to avoid stringing. However, it’s recommended to use a direct drive at a slower print speed if you’re looking for a better quality outcome.
If speed is of the essence, a Bowden extruder usually shines due to its reduced risk of vibrations at higher speeds. This makes it a top contender for large, less intricate prints that need to be churned out quickly. A direct drive extruder, while not as fast as a Bowden, compensates with the ability to handle a wider variety of materials. On the other hand, a direct extruder empowers you with control, versatility, and the ability to handle various materials.
In addition to the aforementioned considerations, correct retraction settings (the process of temporarily pulling back the filament from the nozzle during non-printing movements) are vital for clean prints. The balance of retraction distance and speed is crucial to avoid feeding issues or stringing. Techniques like coasting and Z-hop reduce imperfections, while multi-extruder setups demand specific retraction control. Factors like material, temperature, and print environment influence retraction behavior. Testing and calibration are also essential, as finding the right settings involves experimentation to suit your printer, filament, and model intricacies. A Bowden extruder will require longer retractions as there is more backlash caused by the friction. As such, direct drive extruders require very small or close to no retractions which makes them more suitable for flexible filaments
In any case, whether you are a seasoned professional or 3D printing novice, your choice between a Bowden extruder and a direct drive extruder should be a well-informed decision based on your project’s unique requirements. Both extruder types have their merits and trade-offs, ultimately allowing you to tailor your choice to the specific needs of each print.
Do you prefer a Bowden or a direct drive extruder? Let us know in a comment below or on our LinkedIn, Facebook, and Twitter pages! Don’t forget to sign up for our free weekly Newsletter here, the latest 3D printing news straight to your inbox! You can also find all our videos on our YouTube channel.
*Cover Photo Credits: E3D (left) and 3Dnatives (right)