Un nuevo metamaterial para la impresión 3D de piezas de aviones y cohetes
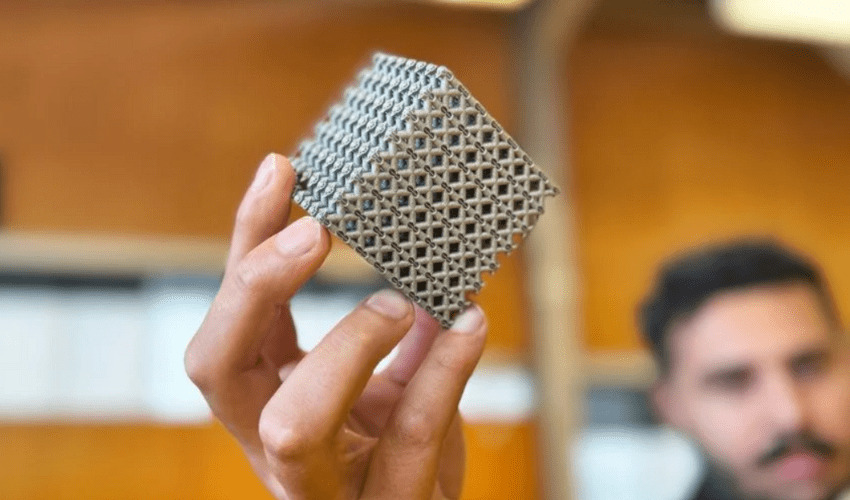
La naturaleza es fuente de inspiración para muchos investigadores, se inspiran en el comportamiento de las plantas o los animales para imaginar nuevos conceptos y materiales. Tal es el caso de un equipo de investigadores de la Universidad RMIT (Real Instituto de Tecnología de Melbourne). Han desarrollado un metamaterial impreso en 3D cuya estructura de celosía es parecida a la del coral Tubipora musica, también llamado «coral de tubo de órgano». Esto sería especialmente útil en la industria aeroespacial, especialmente para producir piezas de aviones o cohetes más resistentes y ligeros.
El metamaterial impreso en 3D ha sido fabricado en el RMIT Advanced Manufacturing Precinct a partir de una aleación de titanio utilizando el proceso de impresión 3D de fusión láser por lecho de polvo (LPBF), lo que en sí, no es una novedad. Lo que sí tiene un carácter innovador es el material artificial que han creado: este tiene propiedades únicas que no existen en la naturaleza. El metamaterial, que consiste en un entramado de cubos de titanio, se caracteriza por su relación resistencia/peso que no existe en la naturaleza y por lo tanto, combina ligereza y resistencia. La peculiaridad de la estructura es que es un 50% más resistente que la aleación de magnesio fundido WE54 de última generación, el cual tiene una densidad similar y que se utiliza en la industria aeroespacial. Gracias a la nueva estructura, los puntos débiles del cubo están sometidos a la mitad de tensión y las grietas que pudieran aparecer se desvían a lo largo de la estructura. El resultado es una estructura más robusta con potencial para la fabricación de piezas de aviones y cohetes, al igual que dispositivos médicos como implantes óseos, sobre todo por sus propiedades de biocompatibilidad y resistencia a la corrosión y el calor.
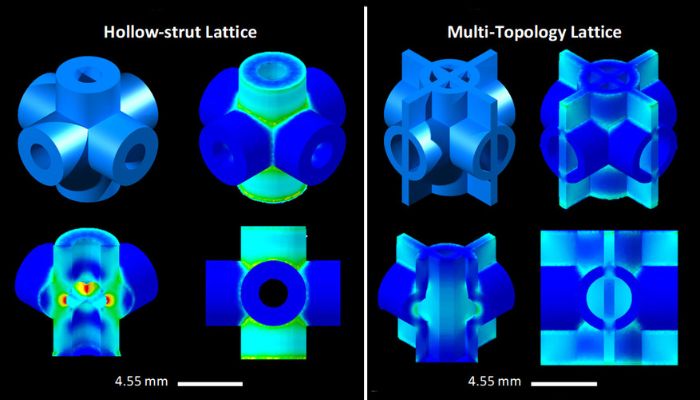
Concentración de tensiones en rojo y amarillo en la rejilla (izquierda), mientras que (a la derecha) la nueva estructura de la rejilla distribuye las tensiones de manera más uniforme.
¿Hacia un metamaterial más estable?
Sin embargo, según Ma Qian, catedrático del RMIT, los intentos por reproducir «estructuras celulares» huecas en metales, que se vienen realizando desde hace décadas, han fracasado debido a problemas de fabricación y concentración de tensiones en las partes internas de los espaciadores huecos, lo que ha dado lugar a fallas prematuras. Según Qian, lo ideal sería que la tensión se distribuyera uniformemente por los materiales celulares complejos. Sin embargo, en la mayoría de las topologías, es común que menos de la mitad del material soporte la carga de compresión, mientras que la mayor parte del material es estructuralmente insignificante, añade. El uso de la fabricación aditiva ha permitido superar estas limitaciones y distribuir mejor la carga al tiempo que aumenta la resistencia. «Hemos diseñado una estructura de rejilla tubular hueca por cuyo interior discurre una fina tira. Estos dos elementos combinados muestran una fuerza y ligereza que nunca se han visto en la naturaleza”, explica Qian. “Al combinar eficazmente dos estructuras de rejilla complementarias para distribuir uniformemente la tensión, evitamos los puntos débiles donde normalmente se concentra la tensión».
El autor principal del estudio y estudiante de doctorado del RMIT, Jordan Noronha, añade: «En comparación con la aleación de magnesio fundido más resistente del que se dispone actualmente en aplicaciones comerciales y que requiere de una alta resistencia con un menor peso, se ha demostrado que nuestro metamaterial de titanio de densidad comparable es mucho más resistente o menos propenso a sufrir deformaciones permanentes bajo el efecto de la presión, por no mencionar que es más fácil de fabricar».
La nueva estructura tiene el potencial de ser producida en tamaños de varios milímetros o metros, utilizando distintos tipos de impresoras. Además, el equipo de investigación espera utilizar el material en el futuro en entornos con temperaturas más elevadas. Sin embargo, la adopción por parte de la industria podría llevar algún tiempo, ya que la tecnología utilizada para producir el nuevo material aún no está disponible para el público en general. Si quieres conocer más sobre el tema, haz clic aquí.
¿Qué te ha parecido este metamaterial impreso en 3D?Deja tus comentarios en nuestras redes sociales: Facebook, Twitter, Youtube y RSS. Sigue toda la información sobre impresión 3D en nuestra Newsletter semanal.
*Créditos de todas las fotos: RMIT University