Los implantes impresos en 3D más sorprendentes de la medicina
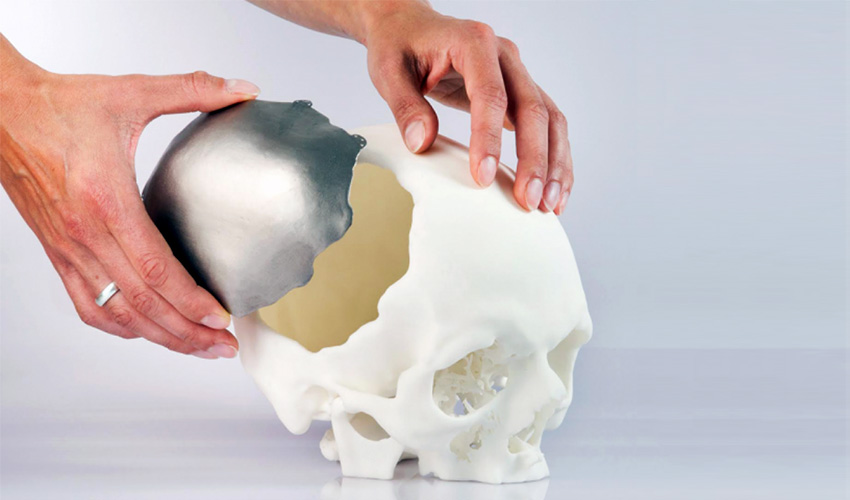
Uno de los grandes beneficiados con la llegada de las tecnologías de fabricación aditiva ha sido el sector médico. Gracias a la facilidad para desarrollar modelos únicos para cada paciente, por fin nos estamos acercando a la llamada: medicina personalizada. Hace algunas semanas te presentamos la selección con órtesis impresas en 3D, y te hemos hablado igualmente de prótesis desarrolladas con impresión 3D, esta semana ha tocado hacer una selección a los implantes impresos en 3D.
Cuando hablamos de implantes sabemos que es un tema muy delicado, ya que es la introducción de un elemento externo al cuerpo del paciente, reemplazando algo que no está funcionando o para el tratamiento de alguna enfermedad. Al ser algo externo debe estar hecho a medida para cumplir con los requerimiento de cada persona, por ello la fabricación aditiva ha caído como anillo al dedo en estos desarrollos. El equipo de 3Dnatives te ha hecho una selección con algunos de los implantes impresos en 3D más innovadores que existen actualmente.
Un implante de clavícula impreso en PEEK
Hace un par de años conocimos uno de los grandes avances en el ámbito médico. El fabricante de impresoras 3D IEMAI y el Hospital Universitario de Kunming habían integrado con éxito un implante de clavícula impreso en 3D a partir de PEEK, un termoplástico de alto rendimiento altamente resistente y biocompatible. El paciente que recibió este implante impreso en 3D sufría cáncer y, al tener que someterse a sesiones de quimioterapia, no pudo recibir un implante metálico. El dispositivo en cuestión se diseñó a medida y la fabricación aditiva hizo posible satisfacer las necesidades del paciente de forma mucho más rápida y sencilla. El modelo se imprimió en la máquina IEMAI 3D MAGIC-HT-M y parece que el PEEK fue muy bien aceptado por el cuerpo.
Impresión 3D de huesospara el oído
El martillo, el yunque y el estribo son tres huesos ubicados en nuestro oído, siendo los más pequeños del cuerpo humano porque no crecen después del nacimiento. Por tanto, su forma, tamaño y posición son muy importantes para el correcto funcionamiento del oído. Sin embargo, a veces estos huesos se rompen y necesitan ser reemplazados. Esto es lo que sucedió en Sudáfrica, donde a un paciente se le implantaron huesos de titanio impresos en 3D después de un accidente de coche. Tras el escaneo 3D de su oído medio, el equipo de cirujanos detrás de la operación pudo modelar un implante a medida, que luego se imprimió en una máquina de fusión láser de lecho de polvo. El titanio fue el material utilizado en este caso por su biocompatibilidad y resistencia.
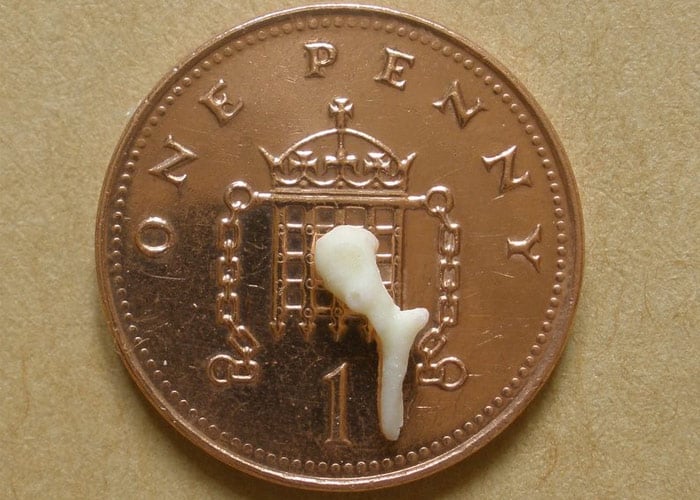
Esta imagen muestra un huesecilllo real de nuestro oído que fue fabricado nuevamente gracias a la impresión 3D.
Una nueva forma de hacer prótesis de rodilla
La empresa estadounidense Monogram Orthopaedics tiene la misión de cambiar la manera en que se desarrollan las operaciones de rodilla. Actualmente están desarrollando una solución que combina la impresión 3D y la robótica para permitir la personalización masiva de implantes ortopédicos. Estos implantes están diseñados, según la empresa, para un máximo contacto cortical y estabilidad. Para ello diseñan una parte lo más cercana a la anatomía original del paciente, gracias a una tomografía computarizada que permitirá una representación 3D de la estructura ósea original y la impresión 3D utilizando una aleación de titanio. Esto permitirá que los implantes sean menos dolorosos y menos propensos a romperse. Aunque aún no han comercializado el producto, ya han alcanzado una serie logros es su iniciativa.
Implante de mandíbula tras retirar un tumor
Anelia Myburgh, es una mujer australiana de Melbourne que mejoró su calidad de vida gracias a las tecnologías de fabricación aditiva. Debido a un tumor maligno ubicado en su mandíbula y dientes, los doctores se vieron forzados a extirparlo, lo cual provocó una desfiguración en el rostro de la mujer al perder más del 80% de la mandíbula. El caso de de Myburgh llevó al cirujano maxilofacial George Dimitroulis a explorar las posibilidades de la fabricación aditiva para la creación de modelos personalizados. Así, creó un implante de mandíbula con un marco de titanio capaz de incorporar injertos de hueso. Tras más de 5 horas de cirugía y varios meses de recuperación, podemos afirmar que la operación fue todo un éxito y los avances en esta tecnología devolvieron a Anelia la seguridad y confianza en su vida.
Particle3D imprime implantes óseos
Con el lema de marca registrada «We Print Bone», Particle3D fue fundada en 2014 por un profesor y dos estudiantes de ingeniería médica con el objetivo de desarrollar una nueva solución para reemplazar huesos destruidos o extirpados quirúrgicamente. En la actualidad, Particle3D sigue desarrollando implantes óseos personalizados para cada paciente basados en la propia tomografía computarizada o resonancia magnética del paciente. Esto da como resultado implantes impresos en 3D que proporcionan una arquitectura interna única similar al hueso que contiene micro y macro porosidades, al igual que el hueso real.
La caja torácica creada por Renishaw
Debido a un cáncer en el pecho, el galés de 71 años Peter Maggs se sometió a una operación de 8 horas para la extirpación del tumor. En el proceso quirúrgico se extrajeron tres costillas y parte de su esternón, por lo que los médicos buscaron una forma de reemplazar las partes que faltaban. Para ello, recurrieron a la fabricación aditiva de metal, concretamente a las soluciones de la empresa Renishaw, con el fin de crear un modelo de caja torácica de alta calidad y biocompatibilidad. El cirujano cardiotorácico Ira Goldsmith explicó que uno de los principales beneficios de utilizar una prótesis impresa en 3D es que puede personalizarse y adaptarse por completo al paciente. Y así lo demostró, ofreciéndole a Maggs una solución rápida y eficiente.
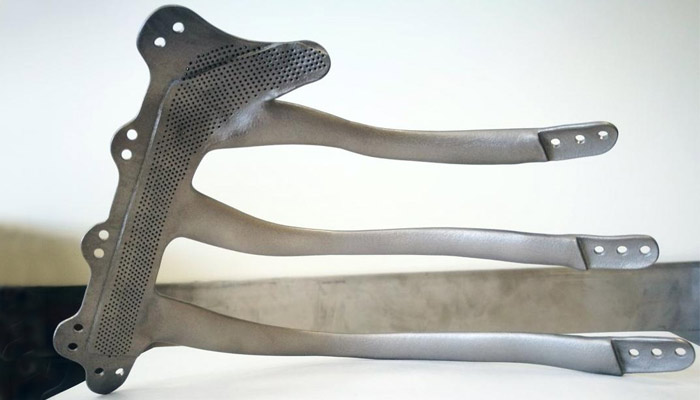
Créditos: Renishaw
La tecnología patentada de NanoHive Medical
NanoHive Medical es una empresa pionera en implantes de fusión intersomática espinal impresos en 3D. Usando su tecnología patentada de celosía de titanio blando biomimético, la compañía ofrece a cirujanos y pacientes propiedades de módulo elástico biomecánico, imágenes de diagnóstico precisas y atracción e integración de las células osteoblásticas. Esto resulta en una menor rigidez o incomodidad experimentada para el paciente y una estabilidad del implante más rápida en comparación a los métodos de implante PEEK existentes.
Una retina artificial de carbono impresa en 3D
Además de utilizar la impresión 3D en la traumatología, también se puede implementar en las retinas. En este caso, un ingeniero australiano desarrolló una retina artificial impresa en 3D hecha de carbono para ayudar a las personas a ver de nuevo. El Dr. Matthew Griffith de la Universidad de Sydney hizo un gran avance cuando se dio cuenta de que un cuerpo es solo un semiconductor basado en carbono, como un ordenador. Con esta idea, determinó que podía replicar un ojo creando un dispositivo de carbono (y por lo tanto totalmente biocompatible) que absorbía la luz y luego creaba una carga electrónica, exactamente como un ojo. Además, gracias a la impresión 3D, le fue totalmente posible diseñar él mismo esta retina artificial. Aunque el dispositivo aún no está terminado y ni siquiera se someterá a estudios clínicos hasta los próximos años, Griffith tiene la esperanza de que sea útil para los pacientes que han perdido la vista. Espera incluso que permita la restauración de la visión a color que a día de hoy no es posible.
Una costilla impresa en 3D con poliamida flexible
En 2018, el búlgaro Ivaylo Josifov llegó al hospital con amigdalitis y se fue con una nueva costilla impresa en 3D. Una primicia para el país. En el estudio de su caso los médicos descubrieron una deformidad en sus costillas que presionaba contra los pulmones, lo cual requería una cirugía inmediata. Para curarlo, en asociación con el fabricante polaco de impresoras 3D 3DGence, los médicos utilizaron la fabricación aditiva. Primero realizaron un escáner 3D del hueso del paciente y luego lo imprimieron en 3D a partir de poliamida flexible. Gracias a la operación y la cooperación entre la empresa de impresión 3D y los médicos, Ivaylo Josifov goza ahora de una buena salud.
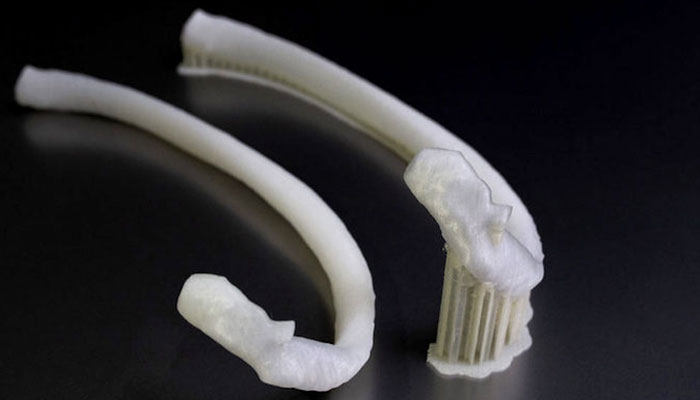
Créditos: 3DGence
Los implantes restauradores de AB Dental
AB Dental utiliza la sinterización selectiva por láser (SLS) para crear sistemas de implantes personalizados. Así pretende revolucionar la tecnología y las aplicaciones en el campo oral-maxilofacial. El sistema de la empresa permite a los médicos planificar tratamientos de restauración dentales y faciales con más precisión en comparación con los métodos tradicionales. La compañía ofrece varios implantes restauradores impresos en 3D para pacientes, incluyendo el aumento del techo del seno, la reparación del hueso orbitario y un implante subperióstico para maxilares reabsorbidos.
Nexxt Matrixx y la creación de modelos porosos
La empresa estadounidense Nexxt Spine se especializa desde hace varios años en la fabricación de implantes para enfermedades de la columna. Con Nexxt Matrixx, la compañía ha logrado otro innovador proyecto: implantes de titanio impresos en 3D para respaldar la osteogénesis, mejorar la topografía de la superficie y promover la producción de factores angiogénicos. El nombre está inspirado en la rejilla porosa del 75% del implante, que favorece la osteointegración y la visualización radiológica. La empresa utiliza equipos de GE Additive en la fabricación de sus implantes y, por lo tanto, se basa en el proceso DMLM para crear sus piezas de titanio. Andy Elsbury, fundador de Nexxt Spine, afirma que los pacientes y las clínicas se benefician de la resistencia y biocompatibilidad de los modelos de titanio.
Válvulas cardíacas de silicona
Recientemente hemos visto ejemplos de implantes para modelos originalmente hechos con tejido orgánico. Este es el caso de una prótesis de válvula cardíaca bioinspirada, que se hizo con silicona impresa en 3D. Creadas tras una colaboración entre un equipo de investigadores del ETH Zurich y la empresa sudafricana Strait Access Technologies, estas válvulas cardíacas se crearon como una forma de reemplazar las válvulas en una población cada vez más anciana. Los investigadores decidieron crear la válvula con silicona, ya que es compatible con el cuerpo humano. Además, mediante el uso de la impresión 3D, podrían hacer una válvula que se adapte más al paciente. Cabe señalar que, aunque los resultados iniciales fueron prometedores, estiman que pasarán otros 10 años antes de que estas válvulas puedan estar realmente en el mercado.
Un implante craneal para una joven
Tiffany Cullern es una joven británica que fue diagnosticada con un tumor cerebral a los 20 años. Se trataba de un fibroma osificante juvenil psamomatoso, un tumor benigno que había que extirpar rápidamente para que el cerebro de la joven no sufriera daños. Los médicos decidieron que Tiffany se sometiera a una operación de 6 horas para extirpar el tumor. Aunque la operación salió bien, la niña no respondió durante los dos días siguientes, ya que tenía el cerebro hinchado. Para reducir la presión, los médicos tuvieron que extirpar parte del cráneo, 12,7 cm para ser exactos. Tiffany tuvo que vivir con esto durante las primeras tres semanas después de la operación. Más tarde se le implantó un modelo impreso en 3D hecho de titanio, plástico y calcio que desde entonces ha reemplazado la parte que faltaba del cráneo.
Un implante para combatir la osteoartritis y el dolor articular
En humanos y perros, encontramos una pequeña capa de cartílago que preserva las superficies de las articulaciones y permite que los huesos se muevan correctamente. Con el tiempo, este cartílago se descompone, lo que produce osteoartritis y, por lo tanto, dolor en las articulaciones. Para combatir esto, investigadores de la Universidad Estatal de Carolina del Norte desarrollaron un implante textil que contiene cartílago derivado de las células madre del paciente. Este tipo de implantes, parcialmente impresos en 3D, han sido probados con éxito en un grupo de perros con problemas de cadera. Este grupo se dividió en dos, y una parte recibió el implante y la otra no. Aquellos perros que recibieron el implante recuperaron toda su potencial movilidad en los 4 meses tras la operación.
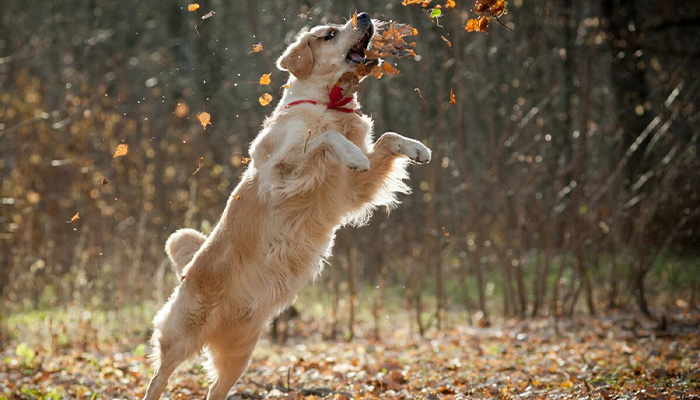
Créditos de las fotos: Deposiphoto
Facilitar la integración de un implante ocular
La órbita es la cavidad ósea en la que se asienta el ojo, cada uno de forma diferente en cada persona. Los procedimientos quirúrgicos alrededor de la órbita son, por tanto, complejos y, a menudo, largos, especialmente cuando hablamos de implantes. Generalmente los médicos deben garantizar la posición de la órbita y su correcta inserción. En Hong Kong, un equipo de investigadores imprimió en 3D modelos para facilitar estas operaciones. El equipo comienza con el escáner y la radiografía del paciente para crear un modelo CAD. Luego imprimen las partes de un molde en una máquina Stratasys con un termoplástico biocompatible y luego presiona una hoja de titanio en el molde para obtener la forma del implante. Este no es un caso igual al de los implantes impresos en 3D que hemos visto, pero queríamos hacer mención a esta iniciativa donde se redujo significativamente el tiempo de operación.

A la izquierda, el molde utilizado para crear la forma del implante. A la derecha, un modelo de órbita para ayudar a los cirujanos con sus operaciones. | Créditos: Stratasys
¿Qué piensas de los implantes impresos en 3D para la medicina personalizada? Deja tus comentarios en nuestras redes sociales: Facebook, Twitter, Youtube y RSS. Sigue toda la información sobre impresión 3D en nuestra Newsletter semanal.
[…] Fuentes: 3Dnatives […]