WEBINAR: Del molde tradicional a la fabricación aditiva, ¿qué pasos hay que seguir?

En comparación con la tecnología de impresión 3D, la fabricación tradicional de moldes requiere más pasos y procesos, y el ciclo de producción de moldes es más largo. A la hora de plantearse fabricar un molde o incluso modificar el ya existente con técnicas tradicionales se debe pasar por estrictas normas y certificaciones, lo cual aumenta el tiempo de adopción del molde y en muchas ocasiones retrasa procesos de producción. Es por ello que el plantearse la adopción de moldes creados con fabricación aditiva parece una solución eficiente, que si bien es cierto, aún no sustituirá las técnicas tradicionales es una tecnología imprescindible a la hora de pensar en manufactura de moldes. Para abordar este tema y conocer el proceso productivo, 3Dnatives presenta su siguiente webinar bajo demanda: «Del molde tradicional a la fabricación aditiva, ¿qué pasos hay que seguir?».
¡Inscríbete gratis aquí para ver el webinar!
La adopción de moldes no está únicamente relacionada con las empresas de manufactura de maquinaria y bienes de equipo, más empresas dentro del sector de la automoción o aeroespacial lo utilizan para la fabricación de piezas o utillajes. Tal es el caso de AIRBUS, que comenzó la adopción de las tecnologías 3D en 2018 y ha ido incrementando su utilización desde ese entonces. De acuerdo al estudio de Business Research se espera que el mercado mundial de moldes industriales crezca de $ 26,21 mil millones en 2020 a $ 27,91 mil millones en 2021 a una tasa de crecimiento anual compuesta del 6,5%, llegando a las $ 38,62 mil millones en 2025. Actualmente después de América del Norte, Europa occidental representa el 23% del mercado global de los moldes industriales. La fabricación de moldes industriales tiene más de un siglo de historia, para su fabricación se han utilizado históricamente técnicas sustractivas, y posteriormente ha llegado el moldeo por inyección hasta que hace unos años comenzó la adopción de moldes con impresión 3D para el termoformado, pero igualmente fabricados con material compuestos como molde final. De acuerdo al business research el paso de moldes tradicionales a moldes impresos en 3D reduce el consumo de energía y el tiempo del ciclo de enfriamiento del 15 al 60%.
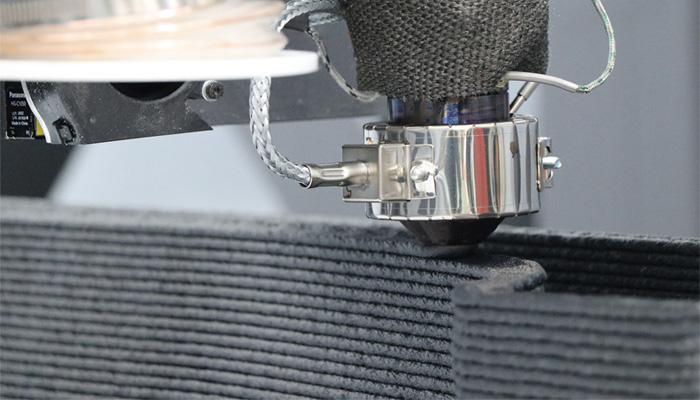
Créditos: Discovery 3D Printers
Nuestros expertos
Con esta perspectiva del sector actual, hemos llevado a cabo un webinar bajo demanda en el cual varios expertos del sector nos han dado su visión y conocimiento de la importancia de pasar del molde tradicional a la fabricación aditiva e incorporar la tecnología como proceso productivo hoy en día. Estos son los perfiles de los ponentes que han participado:
Francisco Bárcenas, nacido en Valdepeñas hace 31 años y Diseñador de productos por la EASDAL. Ha trabajado en la empresa familiar desde su creación, al principio inmersos en el diseño, fabricación y puesta en marcha de las fresadoras cnc y desde el 2015 en continuo conocimiento en el mundo de la impresión 3D por termoplásticos. Trabaja en el continuo desarrollo de cada equipo de fabricación aditiva fabricado en la empresa y en constante conocimiento de los nuevos materiales termoplásticos que se encuentran en el mercado. Ha liderado numerosos proyectos de I+D con grandes empresas del sector automoción, naval o eléctrico siendo ellos siempre con resultado positivo y dando lugar a una tecnología de fabricación aditiva adaptada a la necesidad concreta del cliente.
Ricardo Pinillos, nacido en Valencia con 41 años e Ingeniero de Materiales por la Universidad Complutense de Madrid y residente en Madrid, posee un Master Internacional de Materiales Compuestos por la Universidad de Göttingen. Lleva trabajando los últimos 12 años en Airbus en el departamento de utillaje dentro de la ingeniería de fabricación y fue responsable de la aceptación de los primeros utiles que fabrican el revestimiento del ala inferior y superior del A350. A participado y liderado numerosos proyectos de R&D en el ámbito del utillaje para la fabricación de componentes aeronáuticos en materiales compuestos y durante los últimos 5 colaboró junto con otros compañeros del departamento en la introducción de la tecnología de fabricación aditiva dentro de sus procesos productivos así como la investigación y desarrollo de la misma en el ámbito del utillaje. Posee una amplia experiencia y conocimiento en distintas disciplinas de fabricación en el mercado, tanto convencionales como emergentes.
Raúl Burgos, ingeniero industrial, ha trabajado desde el año 2002 en AIRBUS (19 años). Ha pasado por múltiples departamentos dándole la posibilidad de conocer el proceso completo de un avión. En su paso por Alemania trabajó como arquitecto aeronáutico en la planta de Hamburgo y comenzó a tener contacto con la tecnología de impresión en 3D para piezas avionables. De vuelta en España, se incorporó al departamento de Ingeniería de Utillaje en la planta de Illescas como ingeniero de R&D para la búsqueda de nuevas tecnologías y soluciones que permitan mejorar los medios productivos usados. Entre esas tecnologías está el uso de la impresión 3D tanto con polímeros como con metal como procesos auxiliares para llevar a cabo esta tarea. Entre las areas de conocimiento, de las cuales se ha especializado, cuenta con una gran experiencia en diseño, digitalización y automatización y fabricación aditiva.
- Francisco Bárcenas
- Ricardo Pinillos
- Raúl Burgos
¿Quieres ver el webinar sobre cómo pasar del molde tradicional a la fabricación aditiva? ¡Regístrate aquí y te enviaremos la grabación por correo electrónico! Deja tus comentarios al respecto en nuestras redes sociales: Facebook, Twitter, Youtube y RSS. Sigue toda la información sobre impresión 3D en nuestra Newsletter semanal.