Todo lo que necesitas saber sobre los soportes en la impresión 3D
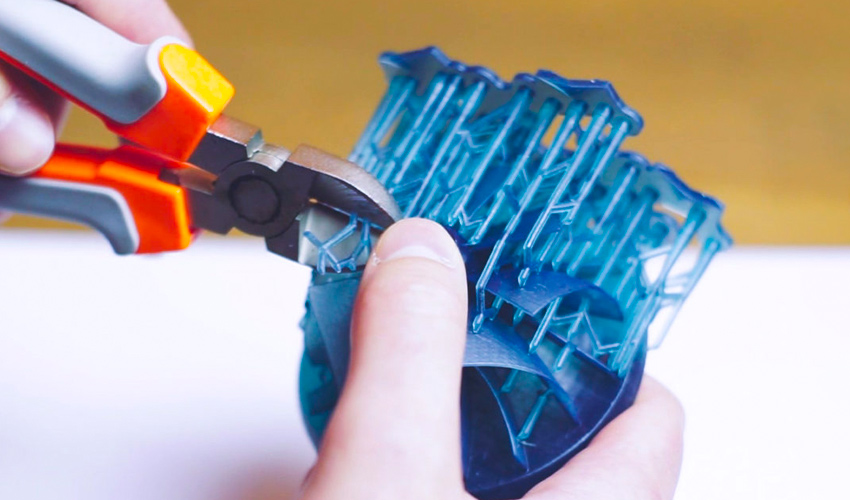
Una de las características de la fabricación aditiva es que permite una gran libertad de diseño para crear piezas complejas y realmente impresionantes. Sin embargo, conseguir que los modelos se fabriquen a la perfección puede requerir pasos intermedios, como la utilización de soportes. En la impresión 3D, se denominan soportes a todas aquellas estructuras que sirven para sostener las áreas en voladizo de una pieza. Aunque de primeras parezca un concepto sencillo, a la hora de configurar los soportes de impresión 3D nos pueden surgir algunas dudas, como por ejemplo, ¿cuándo son realmente necesarios? ¿Cómo se pueden retirar? ¿Qué inconvenientes puede tener su utilización? Para dar respuesta a estas cuestiones, hoy te traemos una guía completa sobre cómo utilizar los soportes de forma eficaz en la fabricación aditiva.
Soportes según la tecnología
Lo primero que debes de tener en cuenta a la hora de plantearte el uso de estas estructuras es que, dependiendo de la tecnología de impresión 3D utilizada y la complejidad de tu diseño, el tipo de soporte y su función variarán. Por ejemplo, en la impresión 3D FDM hay dos reglas generales que debes conocer sobre las estructuras de apoyo: la de los 45 grados y la de los 5 milímetros. La primera hace referencia al desplazamiento horizontal de las impresoras 3D entre capas consecutivas. En este sentido, si un saliente de la pieza se inclina en un ángulo inferior a 45 grados respecto a la vertical, entonces puede imprimir ese saliente sin utilizar soportes. No obstante, si el ángulo es mayor, la máquina no apilará correctamente las capas y el voladizo requerirá estructuras de apoyo. Por otro lado, la regla de los 5 mm explica que cuando un puente (espacio entre dos puntos paralelos de la pieza) tiene menos de 5 mm de longitud, no se requieren soportes, pero de lo contrario, tendremos problemas de impresión. Para conseguir unir los dos puntos paralelos sin soportes, la impresora utiliza una técnica llamada «bridging«. Este método consiste en estirar el material caliente durante distancias cortas para crear la unión con un mínimo de hundimiento.
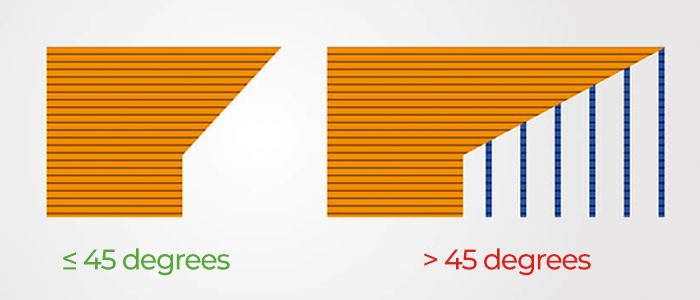
La regla de los 45 grados aplicada a la impresión 3D por extrusión.
Por otro lado, en la impresión 3D de resina, con procesos como SLA o DLP, la pieza final se consigue gracias a la fotopolimerización del material líquido mediante una fuente de luz. Esta tecnología es una de las más precisas, siendo capaz de crear los objetos más pequeños e intrincados con detalles exactos. Se caracteriza por tener un funcionamiento inverso al de extrusión, ubicando la bandeja de impresión en la parte superior. Por esta razón, y para asegurar que las impresiones se adhieren a la plataforma, estas máquinas requieren casi siempre de soportes. Estas estructuras tienen un aspecto de finas columnas con sólo unas pequeñas puntas que están en contacto con el modelo para ahorrar material y tiempo de fabricación. La cantidad de soportes, su ubicación, dónde tocan la pieza y su estructura son calculados por el software y dependen de la complejidad de la pieza en cuestión. Con un posprocesamiento adecuado, la impresión 3D de resina con soporte no debería afectar a la calidad de la pieza final.
En la fabricación aditiva podemos encontrar también una familia de tecnologías que se basan en un lecho de polvo para crear las piezas. En este grupo podemos encontrar el sinterizado selectivo por láser (SLS), sinterización directa de metal por láser (DMLS), fusión por haz de electrones (EBM) o la inyección de aglutinante, también llamada Binder Jetting. Por lo general, estos métodos de fabricación no requieren de soportes ya que el propio polvo actúa como forma de apoyo en cada capa. Aunque esto favorece la libertad de diseño de las piezas, a menudo suele aumentar el coste y tiempo de impresión.
Cabe mencionar que, aunque esta idea de que los métodos de lecho de polvo no requieren de soportes es cierta, lo más correcto sería afirmar que depende del proceso. Por ejemplo, cuando se trabaja con tecnologías de metal es un poco más complejo. En este sentido, el término de “soportes” tiene más una función de anclaje de las piezas a la bandeja de impresión. Robert Chiari, Sales Manager en la empresa DMG MORI, explica: “Debido a las tensiones en los metales, y en particular en los materiales de alta tensión como el titanio, el material puede desprenderse de la construcción por debajo de lo normal. Por tanto, el soporte es realmente una placa que se utiliza para anclar la pieza durante la construcción”. Además, otra función que tiene el polvo que rodea las piezas (además de servir como soporte) es la de eliminar el calor durante el proceso de fabricación para no comprometer la integridad de la pieza o del material.
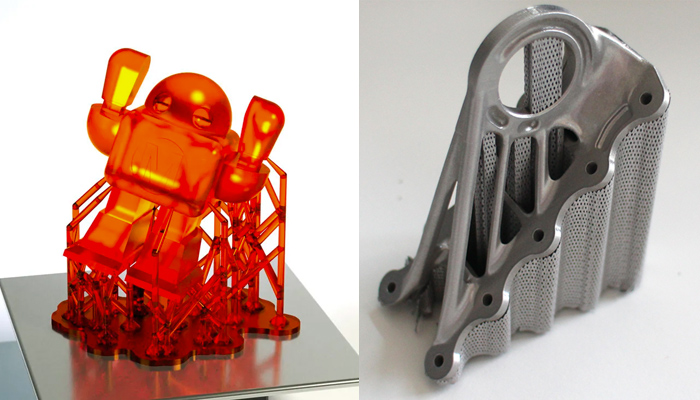
A la izquierda, una pieza impresa en 3D con resina. A la derecha, un «soporte de cabina» del Airbus A350 XWB.
La impresión 3D por inyección de material, también conocida como Material Jetting, consiste en la deposición de fotopolímeros líquidos sobre la bandeja de impresión. Capa a capa, el material se cura al instante mediante una fuente de luz ultravioleta. En este caso, las impresoras 3D requieren de soportes siempre que haya partes de la pieza que sobresalen, sin importar el ángulo o la inclinación de la capa anterior. Estos apoyos pueden ser eliminados mediante pasos de postratamiento, como baños de ultrasonidos y chorreado de arena o agua. Dado que la utilización de soportes en esta tecnología no perjudica el acabado final de las piezas, tras el posprocesamiento es realmente difícil distinguir dónde se han utilizado los materiales de apoyo.
Tipos de soportes de impresión 3D
Aunque las estructuras de apoyo tienen una función similar en cada tecnología, lo cierto es que podemos encontrar diferentes tipos en función de su diseño o de su composición. A nivel de diseño, los más populares son los denominados soportes de celosía. Estas estructuras se suelen utilizar para crear columnas que mantengan firmes las piezas, lo cual es realmente útil con partes en voladizos pronunciados. Suelen ser muy recurrentes gracias a la facilidad y rapidez de fabricación, así como por su compatibilidad con la mayoría de impresiones. El único inconveniente es que, en algunos casos, son difíciles de eliminar e incluso pueden dejar marcas en las piezas.
También están los soportes de árbol, que se caracterizan por comenzar con estructuras de “troncos” y evolucionar en finas ramificaciones a medida que llegan al modelo impreso. Esto es muy útil para apoyar ciertas partes selectivas de la pieza que están en voladizo pero no son demasiado verticales. Los soportes lineales son igualmente muy utilizados y son un tanto similares a los de árbol. Consisten en pilares verticales que están en contacto con la totalidad de la parte en voladizo o el puente. A pesar de que aseguran la correcta impresión de la pieza, son más difíciles de retirar y es probable que causen daños en la superficie del modelo.
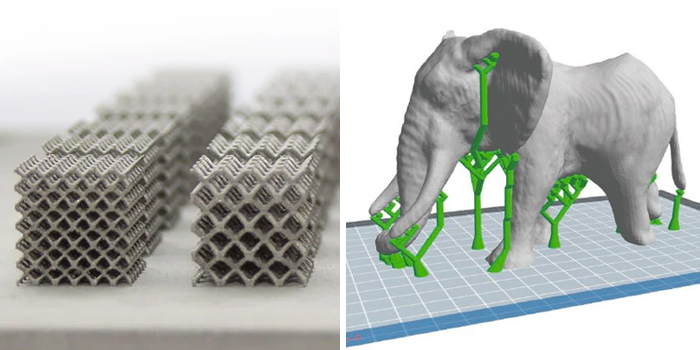
A la izquierda, una estructura de celosía. A la derecha, soportes de arbol.
Por último, en términos de material, encontramos los soportes solubles. Este tipo de estructuras pueden ser creadas mediante impresoras 3D de doble extrusión y pueden ser eliminados al diluirse en agua o en algún disolvente con componentes más complejos. Entre los materiales solubles más conocidos podemos encontrar el PVA o el HIPS, aunque también hay otros más avanzados, como el AquaSys 180 (desarrollado por Infinite Material Solutions) compatible con materiales de alto rendimiento.
¿Cómo optimizar la utilización de soportes?
A la hora de utilizar la impresión 3D en la creación de piezas, es importante conocer la función de los soportes y los beneficios que aporta al proceso de fabricación. Además de lo ya mencionado, como la libertad de diseño y la seguridad de la calidad final de los modelos, el uso de estas estructuras también conlleva una serie de desventajas. La primera está relacionada con la eliminación de dichos soportes, ya que si no se realiza el postratamiento adecuado, el acabado estético de la pieza final se podría ver afectado. Cabe mencionar que la tecnología de inyección de material es la excepción a esta regla.
Por otro lado, cuantos más soportes se configuren en el slicer, más complejo puede ser un diseño para ciertas tecnologías de fabricación aditiva. Esto está estrechamente relacionado con el obvio gasto de material que se requiere para crear los apoyos. La cantidad de material necesario para la pieza se puede optimizar teniendo en cuenta varios aspectos como la orientación y la precisión, además de otros factores de diseño y fabricación. Al configurar correctamente estos parámetros podemos conseguir, no solo una reducción en el tiempo y material de impresión, sino también en los costes finales y en los plazos de entrega.
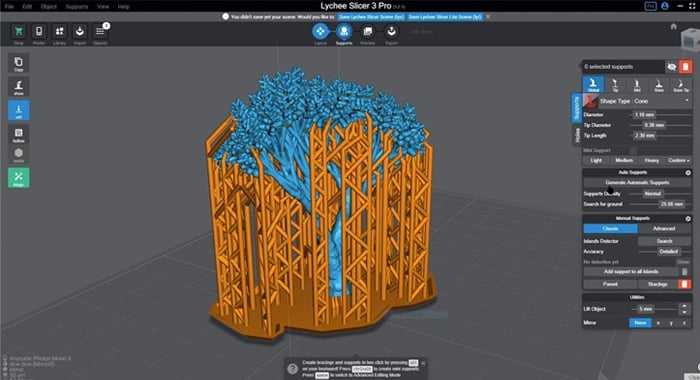
Créditos: Lychee Slicer
En resumen, el uso de soportes en la fabricación aditiva es un mal necesario cuando los modelos cuentan con partes complejas o con muchos voladizos. Aún así, es importante conocer las peculiaridades de cada tecnología para poder sacar el máximo partido a estas estructuras de apoyo, con el objetivo de obtener piezas finales de alta calidad.
¿Qué piensas de esta guía sobre soportes para fabricación aditiva? Deja tus comentarios en nuestras redes sociales: Facebook, Twitter, Youtube y RSS. Sigue toda la información sobre impresión 3D en nuestra Newsletter semanal.
*Créditos foto de portada: Hubs
Información muy interesante, sobre todo a las grandes posibilidades en todos los campos.
Es un gran articulo, muy interesante y me ha aportado algunos tips y puntos de vista a cuidar en las impresiones.