Boeing testet 3D-Druck für Teile ihres Kampfhubschraubers
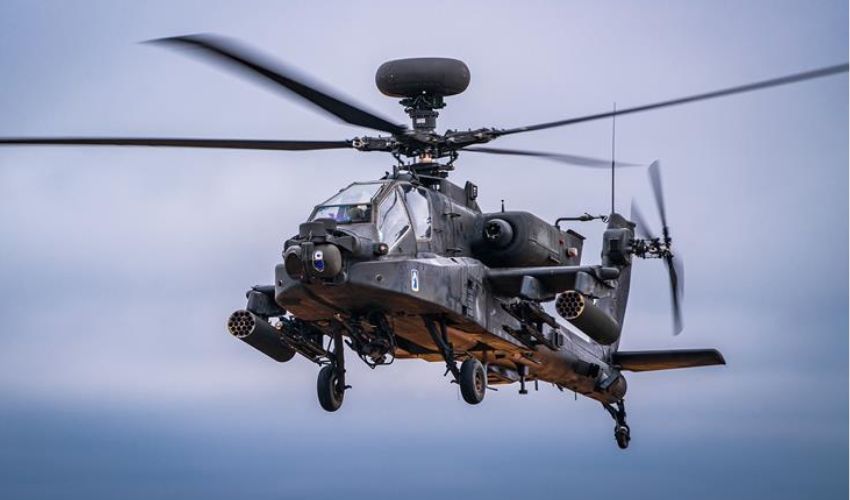
In der amerikanischen Rüstungsbranche gewinnt der 3D-Druck immer mehr an Bedeutung! Das US-Unternehmen für Luft- und Raumfahrt Boeing will im April 2024 anfangen, den vollständig 3D-gedruckten Prototyp des Hauptrotorsystems ihres AH-64 Apache Kampfhubschraubers zu testen. Zudem will Boeing die 3D-gedruckten Komponenten mit den auf herkömmliche Weise hergestellten Komponenten vergleichen. Des Weiteren sollen Ermüdungstests mit den traditionell geschmiedeten Teilen durchlaufen werden, so Andy Pfeiffer, der leitende Konstrukteur und Experte für additive Fertigung bei Boeing Global Services.
Auf der letzten jährlichen Konferenz der Association der US-Army (AUSA-Konferenz) präsentierten Boeing und die Non-Profit-Organisation Applied Science and Technology Research Organization of America (ASTRO) gemeinsam ihre erste durch den 3D-Druck produzierte Komponente im Rahmen des Jointless Hull Project. Diese war die Hauptrotor-Verbindungseinheit, ein Gelenk für das Rotorsystem, welche vollständig und am Stück durch den größten 3D-Metalldrucker weltweit im Rock Island Arsenal, Illinois, gedruckt wurde. Bei diesem sogenannten Jointless Hull Project ist der Drucker sogar groß genug, um eine Panzerhülle am Stück zu drucken. Das Ground Vehicle Systems Center der Armee unterstützt ASTRO finanziell mit 95 Millionen Dollar aus dem US-Haushalt. Mit Hilfe dieser Gelder soll ASTRO Fortschritte in der additiven Fertigung Teile größerer Formate voran treiben. Dazu zählen beispielsweise Panzerhüllen und andere Prototypen von Kampffahrzeugen in der Rüstungsindustrie. Zudem untersucht ASTRO die Wirtschaftlichkeit der Produktion unterschiedlicher 3D-gedruckter Komponenten, so ASTRO-Ingenieurin Emma Gallegos.
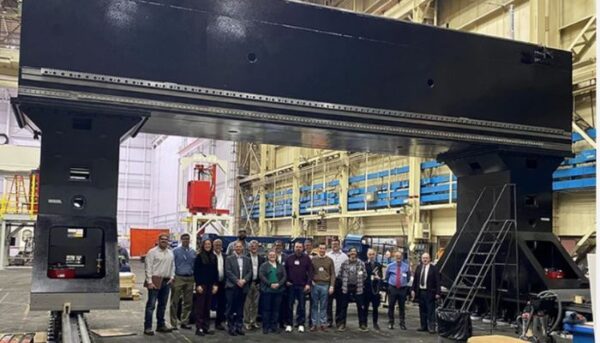
Größter Metalldrucker weltweit (Bild: ASTRO America)
Abwägung zwischen herkömmlicher und additiver Fertigung bei Boeing
Beim von Boeing verwendeten 3D-Druck für den AH-64 Apache sticht besonders die hohe Geschwindigkeit des Druckvorgangs im Vergleich zu herkömmlich verwendeten Produktionsmethoden hervor. Der 3D-Druckprozess der Hauptrotorenverbindung aus Aluminium der Serie 6000 selbst beanspruchte etwa acht Stunden. Zusätzlich nahm das Auftragen des Aluminiums 45 Minuten in Anspruch. Die Durchführung der Herstellung der Bauteile mit Hilfe der traditionellen Technologie des Schmiedens dauert deutlich länger, nämlich ein Jahr, so Pfeiffer. Durch die additive Fertigung werden demnach Fertigungsvorlaufzeiten eindeutig verringert. In Folge dessen hat Boeing der ASTRO eine Liste von Komponenten überreicht, die erneuert werden sollen und potentiell aus dem 3D-Drucker geschaffen werden sollen.
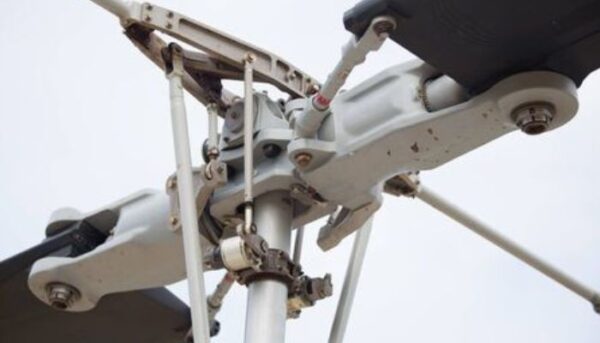
Hauptrotor eines Helikopters (Bild: 123RF)
Jedoch kann bezüglich des Kostenaspekts die konventionelle Fertigung des Schmiedens in Bereichen mit Massenproduktionen profitabler sein. Bei der Herstellung geringerer Mengen hingegen ist der 3D-Druck günstiger und wirtschaflich von Vorteil. Des Weiteren weist die Mikrostruktur 3D-gedruckter Bauteile eine höhere Stabilität, Robustheit und Materialstärke auf als die durch das klassische Fertigungsverfahren fabrizierte Struktur. Boeing erhofft sich daneben durch das neu verwendete Verfahren die Lieferkette von Teilen, die üblicherweise geschmiedet werden, zu optimieren. Außerdem ist bei der Entscheidung zwischen einem der beiden Verfahren ausschlaggebend, ob das Unternehmen bereits einen Zulieferer und die benötigten Werkzeuge besitzt, die zur Herstellung nach herkömmlichen Methoden benötigt werden. Boeing betont hingegen die Wichtigkeit der additiven Fertigung bei dringenden Reparaturarbeiten an Flugzeugen, die eine flexible Ersatzlieferung von Teilen bedürfen.
Was halten Sie von Boeing und der Herstellung von Kampfflugzeugteilen mittels des 3D-Drucks? Lassen Sie es uns in einem Kommentar unten oder auf unseren LinkedIn-, und Facebook-Seiten wissen! Vergessen Sie nicht, sich für unseren kostenlosen wöchentlichen Newsletter anzumelden, um die neuesten 3D-Druck-Nachrichten direkt in Ihren Posteingang zu bekommen! Sie können auch alle unsere Videos auf unserem YouTube-Kanal finden.
*Titelbildnachweis: US Army