Un vaisseau spatial en route vers Jupiter avec des pièces imprimées en 3D
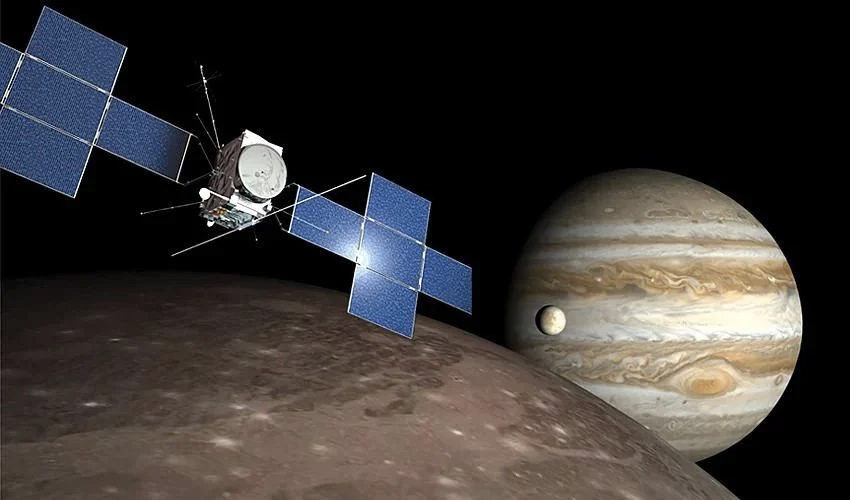
En Espagne, le Centre avancé des technologies aérospatiales (CATEC), la société AIRBUS et la société d’ingénierie CiTD travaillent ensemble pour relever les défis d’une mission spatiale sans précédent. Il s’agit de la première mission européenne vers Jupiter, la plus grande planète du système solaire et la cinquième la plus éloignée du soleil. Pour contribuer au projet, les trois organisations ont utilisé l’impression 3D métal pour réduire le poids du vaisseau spatial JUICE (JUpiter ICy moons Explorer) qui est utilisé lors du voyage vers Jupiter. Avec un total de 11 pièces réalisées à l’aide de la fabrication additive, cette initiative a permis de réduire de 52 % le poids de la structure secondaire de l’engin spatial. Par rapport aux versions développées avec la technologie conventionnelle, c’est un aspect important dans l’optimisation de la structure de l’engin spatial.
Cette première mission européenne vers Jupiter est déjà en orbite. La fusée a été lancée le 14 avril dernier. D’une durée initiale de huit ans et d’une distance de 5 milliards de kilomètres, l’objectif est d’explorer la plus grande planète du système solaire et ses lunes glacées Ganymède, Europe et Callisto à la recherche d’eau liquide. Ceci est un autre exemple clair du rôle de l’impression 3D dans l’exploration spatiale. Fernando Lasagni, directeur technique des matériaux et procédés chez CATEC, déclare : « c’est une étape vraiment importante pour l’industrie spatiale européenne et certainement aussi pour CATEC. Nous avons conçu les supports pour les capteurs de mission et d’autres mécanismes d’actionnement qui font partie de la structure secondaire du vaisseau spatial JUICE mais qui sont essentiels à la mission ». Mais quelle technologie d’impression 3D a été utilisée et quel est l’état actuel du projet ?
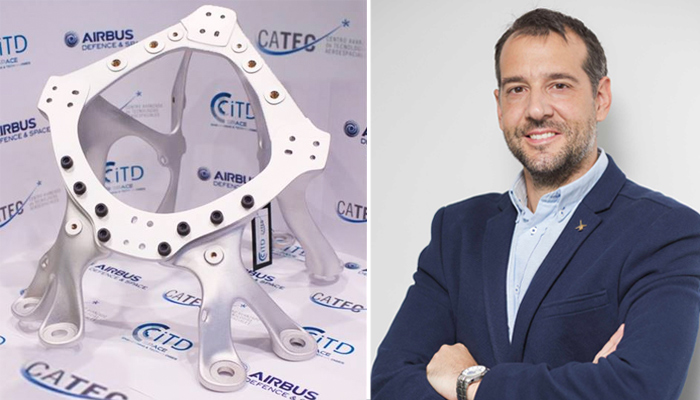
À gauche : l’une des pièces imprimées en 3D pour le vaisseau spatial. À droite : Fernando Lasagni, directeur technique des matériaux et procédés au CATEC
L’impression 3D en route vers Jupiter
Le procédé de fabrication additive choisi pour fabriquer les 11 composants est la fusion laser sur lit de poudre. L’un des aspects qui caractérisent cette technologie d’impression 3D est la grande liberté de conception qu’elle offre aux pièces. De cette manière, il est possible de produire des géométries 30 à 60 % plus légères par rapport aux méthodes d’usinage conventionnelles, en particulier dans les applications aérospatiales. Selon Marta García-Cosio, directrice du CiTD, « La mission spatiale JUICE nécessite une forte réduction de la masse de la structure pour les instruments scientifiques et le carburant, et grâce à la technologie d’impression 3D nous avons pu concevoir et optimiser la masse de la structure secondaire du satellite ». En ce qui concerne les matériaux, les trois organisations ont décidé de fabriquer les pièces en aluminium Al-Mg-Sc (Scalmalloy®).
Le défi était non seulement de réduire le poids des pièces, mais aussi d’y parvenir en un temps record. Pour y parvenir, un plan de test détaillé a été conçu avant la fabrication pour évaluer le comportement de l’aluminium et vérifier la conductivité thermique et électrique du matériau. De plus, une méthode de contrôle de la matière première lors de la fabrication a été développée pour garantir la qualité des alliages et la fiabilité des systèmes de production. Enfin, des méthodes d’inspection avancées (par exemple, la tomodensitométrie) ont été appliquées pour garantir la meilleure qualité de chaque composant fabriqué.
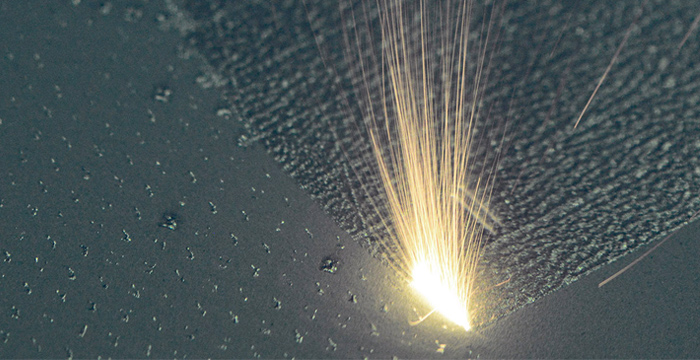
La technologie de fusion laser sur lit de poudre a été utilisée pour la fabrication des pièces de la fusée JUICE. (Crédits : Fraunhofer)
Il s’agit sans aucun doute d’un grand pas en avant pour l’industrie aérospatiale espagnole. « L’expérience acquise a été déterminante pour que l’Agence spatiale européenne (ESA) accorde sa confiance à CATEC pour cette mission spatiale historique vers Jupiter, conclut Fernando Lasagni. C’est aussi un challenge pour nous, qui représente un tournant pour notre technopole. » Pour en savoir plus sur l’avancée de la fusée JUICE vers Jupiter, cliquez ICI.
Que pensez-vous de l’utilisation de la pression métallique pour atteindre Jupiter ? Partagez votre avis dans les commentaires de l’article et retrouvez toutes nos vidéos sur notre chaîne YouTube ou suivez-nous sur Facebook ou Twitter !
*Crédit photo de couverture : NASA/ESA