Airbus und Safran: Anschluss an Konsortium zur Entwicklung des 3D-Metalldrucks
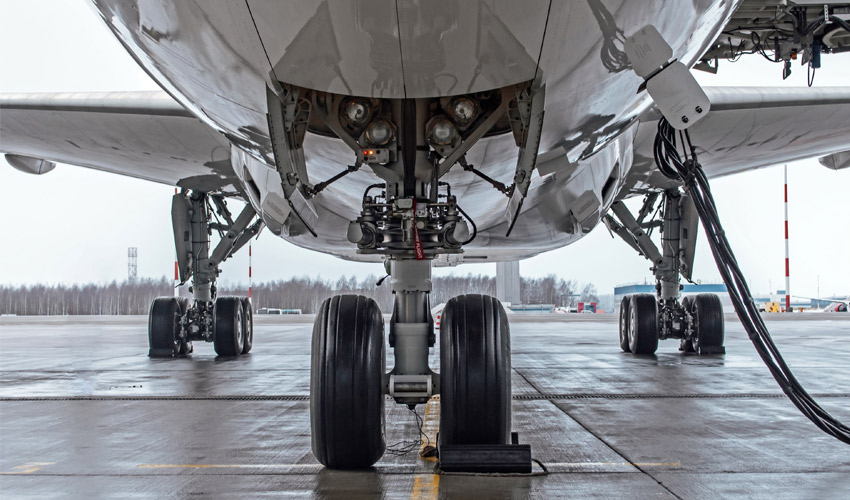
Die Luft- und Raumfahrtkonzerne Airbus und Safran haben angekündigt, dass sie an einem neuen Projekt zur Verbesserung der Fertigungsprozesse in der Luft- und Raumfahrtbranche beteiligt sind. Gemeinsam werden sie an der Entwicklung eines neuen DED-Verfahrens mit der Bezeichnung „Hybrid Direct Energy Deposition (DED) Sprint“ arbeiten, das additive Fertigungs-, Schmiede- und Umformverfahren kombiniert. Das Ziel hierbei ist es zu verstehen, wie Kosten und Produktionszeiten gesenkt und gleichzeitig die Nachhaltigkeit der Komponenten erhöht werden können. Von besonderem Interesse in diesem neuen Konsortium ist die potenzielle Rolle der Directed Energy Deposition (DED), einer metallischen 3D-Drucktechnologie, die bekanntermaßen die Reparatur bestehender Teile erleichtert.
Das Konsortium wird vom National Manufacturing Institute Scotland (NMIS) geleitet und vom Aerospace Technology Institute (ATI) finanziert. Es umfasst mehrere Partner sowie eine industrielle Lenkungsgruppe, die sich aus 13 Unternehmen zusammensetzt, darunter Airbus und Safran Landing Systems. Ihre Beteiligung zeigt das Interesse führender Industrieunternehmen an der additiven Fertigung, die sich um die Entwicklung effizienterer Verfahren für ihre künftigen Aktivitäten bemühen.
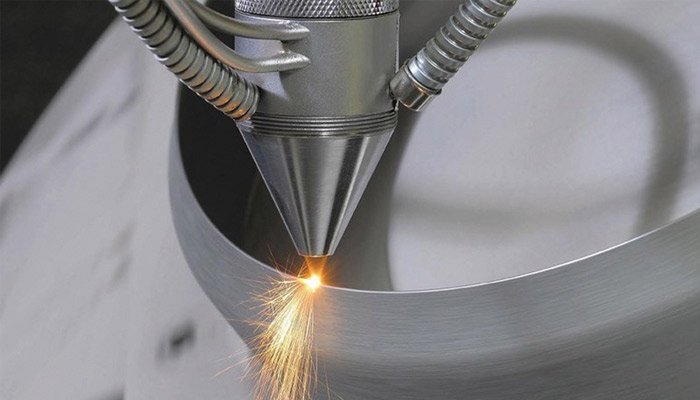
Mit dem DED-Verfahren können Anwender bestehende Metallteile reparieren
Unter der Leitung der Universität Strathclyde und der Universität Cranfield begann das Projekt bereits mit zwei Phasen. Hierbei wird inzwischen einem Demonstrationsteil gearbeitet, das noch in diesem Jahr vorgestellt werden soll. Die dritte Phase wird vom Northern Ireland Technology Center (NITC) an der Queen’s University Belfast geleitet. Das NITC konzentriert sich maßgebend auf die PKM-Bearbeitung. In der abschließenden Phase, der Proof-of-Concept-Phase, werden die herkömmlichen Fertigungsverfahren mit den Alternativen wie der DED-Technologie verglichen. Besonders die DED-Technologie ist im Zuge von Reperaturen von Metallteilen besonders spannend, da hier zusätzliche Funktionen hinzugefügt oder die Konstruktion komplexer und sperriger Komponenten erleichtert werden können. Um den Herausforderungen der Luft- und Raumfahrtindustrie gerecht werden zu können, möchte das Konsortium ein hybrides Herstellungsverfahren entwickeln, das die Abscheidung von Material im DED-Verfahren beinhaltet.
In dieser Branche kommen häufig Schmiede- und Bearbeitungsprozesse zum Einsatz, die beide oft langwierig und kostspielig sein können. Die Produktion von Luftfahrtkomponenten erfordert die Herstellung von komplexen Formen, zeitaufwändige Montageschritte und kostspielige Nachbearbeitungsprozesse. Durch die Integration der additiven Fertigung in die Herstellungskette könnten die Unternehmen ihre Vorlaufzeiten verkürzen und gleichzeitig die Leistung ihrer Teile erhöhen. Sowohl Airbus als auch Safran haben sich bereits mit den Vorteilen der additiven Fertigung befasst, so dass es nicht verwunderlich ist, dass sie sich ebenfalls an dem Projekt beteiligen werden.
Stephen Fitzpatrick, Leiter des Bereichs Additive Fertigung und Bearbeitung am National Manufacturing Institute Scotland, erklärte: „Dieses Projekt hat das Potenzial, effizientere alternative Fertigungsverfahren für Luft- und Raumfahrtunternehmen zu entwickeln, und wird wichtige Impulse für die Branche geben, wie z. B. die Verringerung des Schadstoffausstoßes, die Wiederaufarbeitung und stabilere Lieferketten.“
Es wird davon ausgegangen, dass sich Airbus und Safran Landing Systems an diesen effizienteren Fertigungsmethoden beteiligen und nachhaltige Komponenten für ihre Flugzeuge entwickeln werden. Es bleibt abzuwarten, inwieweit sie nach den Normen und Anforderungen der Luft- und Raumfahrt qualifiziert und zertifiziert werden. Weitere Informationen finden Sie HIER.
Was halten Sie von der Nutzung der DED-Technologie im Bereich der Luft- und Raumfahrt? Teilen Sie uns Ihre Meinung mit und kontaktieren Sie uns. Möchten Sie eine Zusammenfassung der wichtigsten Neuigkeiten im 3D-Druck und der additiven Fertigung direkt und bequem in Ihr Postfach? Registrieren Sie sich jetzt für unseren wöchentlichen Newsletter und folgen Sie uns auf Facebook und Twitter, um stets auf dem Laufenden zu bleiben! Außerdem sind wir auch auf XING und LinkedIN zu finden.