Renault Group ouvre le centre d’impression 3D de sa Refactory à l’externe
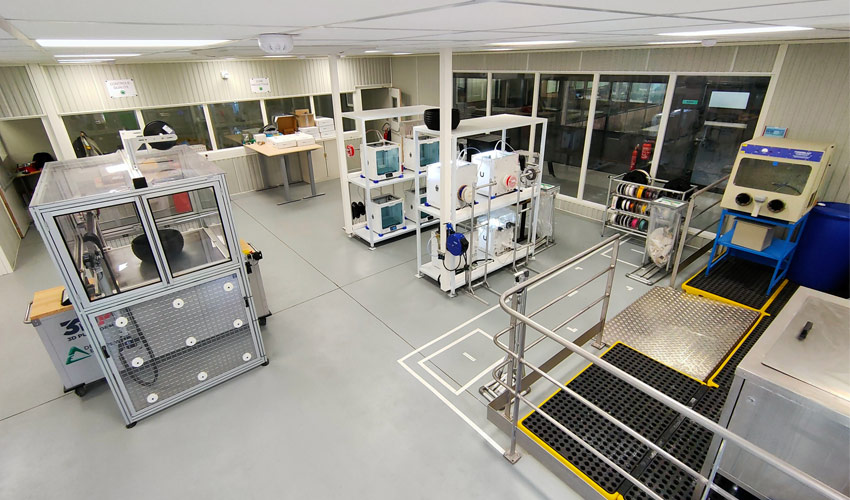
Avec une expérience de plus de 20 ans dans le domaine de la fabrication additive, le constructeur automobile français Renault Group a récemment ouvert son propre centre d’impression 3D au sein de son site de Flins, en région parisienne. Cet espace de 500 mètres carrés s’inscrit dans le projet ReFactory lancé en 2020 par la marque au losange et a pour ambition de s’ouvrir à l’extérieur en produisant des pièces pour diverses industries.
Grâce à ses 18 imprimantes 3D et ses solutions de post-traitement, le centre d’impression 3D est ainsi capable de répondre à des demandes à la fois en interne mais aussi de produire des pièces pour des secteurs comme la mobilité, les transports ou l’agroalimentaire. Mais comment un groupe automobile comme Renault a-t-il intégré la fabrication additive ? Comment compte-t-il déployer son service d’impression 3D à des clients externes ? Mélanie Chevé, Cyril Guillemot, Younesse Khalil et Camel Fettih ont répondu à nos questions !
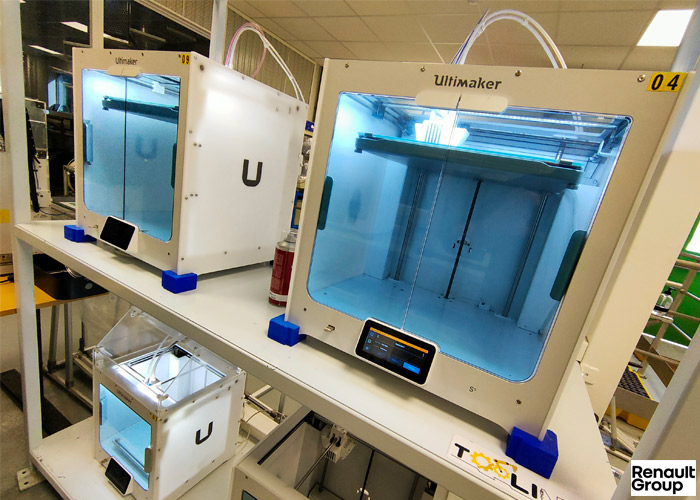
Le centre est notamment équipé d’imprimantes 3D FDM (crédits photo : Renault Group)
3DN : Pouvez-vous vous présenter ainsi que votre rôle chez Renault ?
Je m’appelle Mélanie Chevé, je travaille à l’Ingénierie Process au Technocentre de Guyancourt et j’ai démarré chez Renault il y a 5 ans pour développer l’impression 3D pour les outillages de production. Depuis fin 2021, je travaille avec Cyril et Camel pour les pièces véhicules série en fabrication additive.
Je m’appelle Cyril Guillemot, je suis Chef de Projet Fabrication Additive pour les pièces de véhicule série. Je travaille avec l’ensemble des marques du groupe pour proposer à nos clients de nouveaux accessoires ou pièces d’habillages alliant personnalisation, nouvelles textures et finitions. Ma mission consiste également à associer les moyens digitaux permettant de donner de la valeur à ces pièces et de pouvoir les vendre.

Une partie de l’équipe du centre d’impression 3D de Flins (crédits photo : 3Dnatives)
Je m’appelle Camel Fettih et je suis Chef de Projet Advanced Manufacturing. Dans le cadre du projet Refactory qui vise à transformer l’usine Renault de Flins selon un nouveau modèle industriel tourné vers l’économie circulaire et la mobilité durable, j’ai piloté la mise en place du centre d’impression 3D de référence pour l’ensemble de Renault Group.
Je m’appelle Younesse Khalil et je suis le responsable d’exploitation du centre d’impression 3D. Je suis ravi de participer à cette aventure humaine qui vise à démocratiser l’usage de la fabrication additive.
3DN : Pouvez-vous nous rappeler l’historique de l’intégration de la fabrication additive chez Renault ?
Mélanie Chevé : La fabrication additive chez Renault a commencé il y a une vingtaine d’années au centre de réalisation des prototypes du Technocentre. Les premières technologies étaient utilisées pour prototyper les véhicules efficacement.
Ensuite, la technologie s’est démocratisée et nous avons déployé la fabrication additive dans nos sites de production, avec essentiellement des procédés de dépôt de fil pour concevoir des outillages. Aujourd’hui, cela représente environ 250 imprimantes FDM réparties sur une trentaine de sites de fabrication. Certains ont également des machines de frittage de poudre ou de jet de matière. Sur chaque site, nous avons un référent impression 3D ; au total, c’est une cinquantaine de personnes qui sont impliquées chez Renault Group sur des sujets en lien avec la fabrication additive.
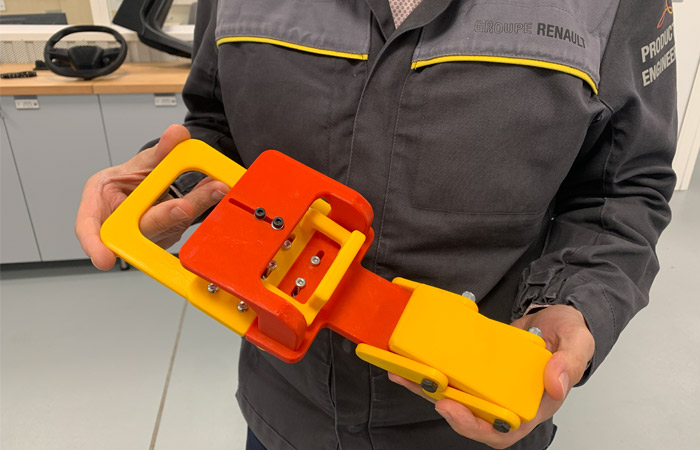
Outillage conçu et imprimé en 3D par le centre de Flins (crédits photo : 3Dnatives)
Il y a un an et demi, le groupe a commencé à se demander si cela avait un sens d’imprimer en 3D des pièces dans ses véhicules. Cette réflexion a été menée sur toute la chaîne de valeur et auprès de toutes nos marques, et de nombreux fournisseurs ont été consultés. Aujourd’hui, nous organisons l’entreprise autour de cette activité d’impression 3D pour les pièces de véhicules série. Cela passe par de nouveaux emplois, des moyens de production interne, la transformation du site de Flins grâce au projet Refactory, mais aussi par un changement de mindset des collaborateurs quant à la conception, le design, les offres de personnalisation jusqu’à la vente client et la logistique associée.
Cyril Guillemot : Nous restons très attentifs et ouverts à l’évolution du marché de la fabrication additive. Sous l’impulsion de notre top management, nous sommes capables de changer nos horizons et de nous adapter très rapidement. Ce n’est pas toujours évident de faire avancer tout le monde au même rythme, car Renault est un grand groupe, mais nous avons cette flexibilité et cette cohérence, c’est dans notre ADN.
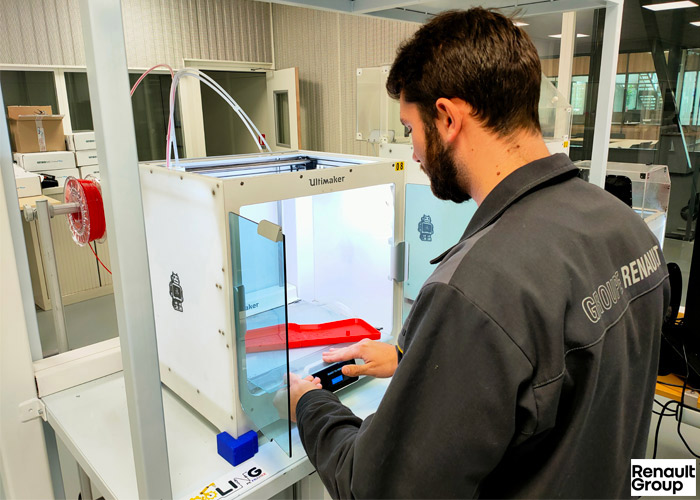
Aujourd’hui, une cinquantaine de personnes sont impliquées chez Renault Group sur des sujets en lien avec la fabrication additive
3DN : Rappelez-nous ce qu’est la ReFactory ? Comment votre centre d’impression 3D s’inscrit-il dans cette démarche ?
Camel Fettih : La Refactory est un projet né en 2020 qui consiste à déployer un nouveau modèle industriel basé sur l’économie circulaire, le tout au service d’une mobilité plus durable. Concrètement, il s’articule autour de quatre pôles d’activités interconnectés : Re-trofit, Re-energy, Re-cycle et Re-start. Ils ont notamment pour objectifs de prolonger la durée de vie de nos véhicules, de produire des énergies vertes, de rénover les pièces automobiles, ou encore de former et d’innover dans l’économie circulaire.
La fabrication additive est une technologie idéale pour l’ensemble de ces pôles, offrant des pièces spécifiques aux nouveaux procédés industriels (outillages, gabarits, etc.) et des composants sur-mesure pour réussir par exemple le rétrofit de nos véhicules. Notre centre d’impression 3D permet de répondre à l’ensemble de ces demandes internes, c’est un outil formidable pour tous les acteurs de la Refactory.
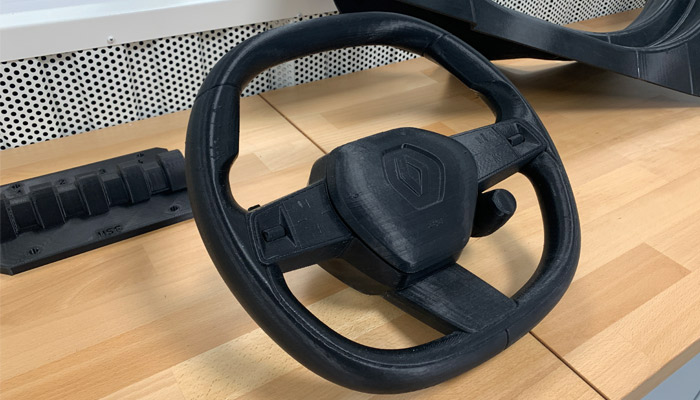
Exemple de prototype imprimé en 3D (crédits photo : 3Dnatives)
3DN : Justement, pouvez-vous nous en dire plus le centre d’impression 3D que vous avez établi sur le site de Flins ?
Camel Fettih : Notre centre comporte aujourd’hui 18 imprimantes 3D polymères, notamment des machines Ultimaker, Stratasys et HP, réparties sur un espace de 500 m2. Nous avons emménagé une zone dédiée au post-traitement où nous allons bientôt intégrer une machine de finition de surface de marque Rösler ainsi qu’une machine de coloration par bain de teinte de marque DyeMansion. Côté matériaux, nous utilisons tous types de polymères que ce soit du PLA, de l’ABS, de l’ASA, du TPU mais aussi du polyamide PA12, des composites et de l’ULTEM. C’est un portefeuille qui augmente au fur et à mesure des demandes de nos clients. Actuellement, 8 personnes travaillent dans ce centre et maîtrisent l’ensemble des étapes de la chaîne de valeur, de la conception au post-traitement. Nous avons donc une équipe pluridisciplinaire, ce qui est une vraie force qui nous permet d’être très agile pour répondre rapidement aux attentes de nos clients.
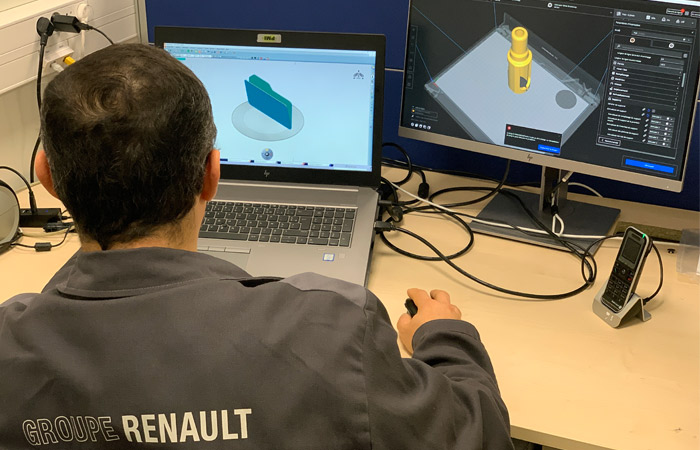
L’équipe maîtrise l’ensemble de la chaine de valeur, de la conception au post-traitement (crédits photo : 3Dnatives)
Ce centre d’impression 3D a pour vocation de devenir une référence chez Renault Group en répondant à la fois aux besoins internes et externes de prototypage et production série. En interne, 60% de notre production sont des prototypes réalisés soit avec le procédé poudre (75%) soit avec le procédé FDM (25%). D’ici 2024, les applications pour les pièces véhicules de série et outillages industriels vont exploser et représenteront 70% de notre production interne grâce au procédé poudre. Nous travaillons pour toutes les marques du groupe (Renault, Dacia, Alpine et Mobilize) mais aussi pour tous les métiers du Manufacturing comme l’emboutissage, la tôlerie, la peinture, l’assemblage, la fonderie et l’usinage.
Au-delà des demandes en interne, notre ambition est désormais de répondre aux besoins de clients externes. Nous travaillons d’ores et déjà avec des acteurs des secteurs de la mobilité, des transports ou de l’agroalimentaire. Nous mettons notre savoir-faire industriel, la qualité automobile et le prix de revient automobile au service de diverses industries. Concrètement, nous proposons des services de conception, d’impression et de post-traitement pour les professionnels. Nous nous appuyons sur les standards de production développés au sein de l’Alliance Renault-Nissan-Mitsubishi pour les appliquer à nos activités d’impression 3D. Renault Group est reconnu pour ses standards de management de la qualité, des coûts, des délais, des ressources humaines et de respect de l’environnement. Ce sont ces mêmes valeurs que nous appliquons dans notre centre pour garantir des niveaux de performance élevés.
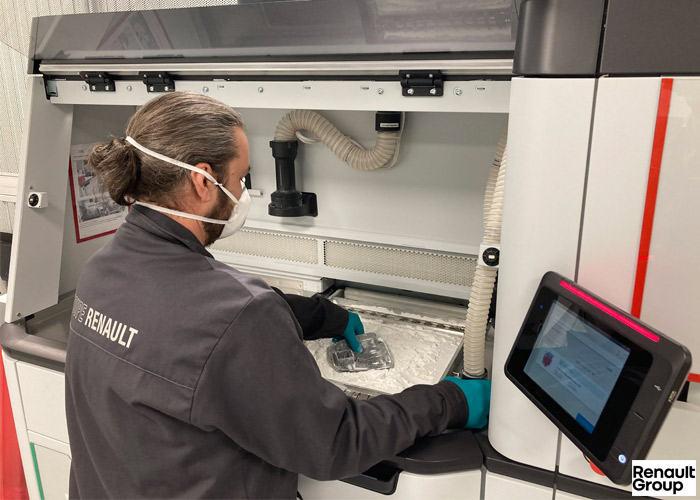
Dépoudrage d’une pièce de l’Alpine A110R
Depuis octobre, nous sommes visibles dans la market place 3Dexpérience de Dassault, et bientôt sur d’autres plateformes de commerce en ligne.
Notre volonté est aussi d’étendre cette expertise sur le marché de la fabrication additive à travers différents partenariats et initiatives. A ce propos, nous avons intégré depuis peu le Digital Manufacturing Network de HP, un réseau international regroupant l’ensemble des services d’impression 3D qui utilisent la technologie HP Multi Jet Fusion dans leur production. Cela nous permettra de répondre à davantage de demandes et d’exigences industrielles.
3DN : Un dernier mot pour nos lecteurs ?
Younesse Khalil : A travers ce centre d’impression 3D, nous souhaitons proposer un service de fabrication à tous les industriels, quel que soit leur secteur d’activité. Grâce au savoir-faire industriel de Renault Group et aux compétences de mon équipe pluridisciplinaire, nous pouvons fabriquer des pièces de qualité, performantes en coût et vertueuses pour la planète en minimisant l’empreinte carbone des industries. Pour contacter directement nos équipes et exprimer vos besoins, merci d’écrire à l’adresse suivante : [email protected]. Si vous souhaitez découvrir notre centre d’impression 3D de l’intérieur, cliquez sur ce lien.
*Crédits photo de couverture : Renault Group
Que pensez-vous de l’utilisation de l’impression 3D chez Renault et de son ouverture à l’externe ? Partagez votre avis dans les commentaires de l’article. Retrouvez toutes nos vidéos sur notre chaîne YouTube ou suivez-nous sur Facebook ou Twitter !