Mobility and Sustainability Take the Stage at Formnext 2023
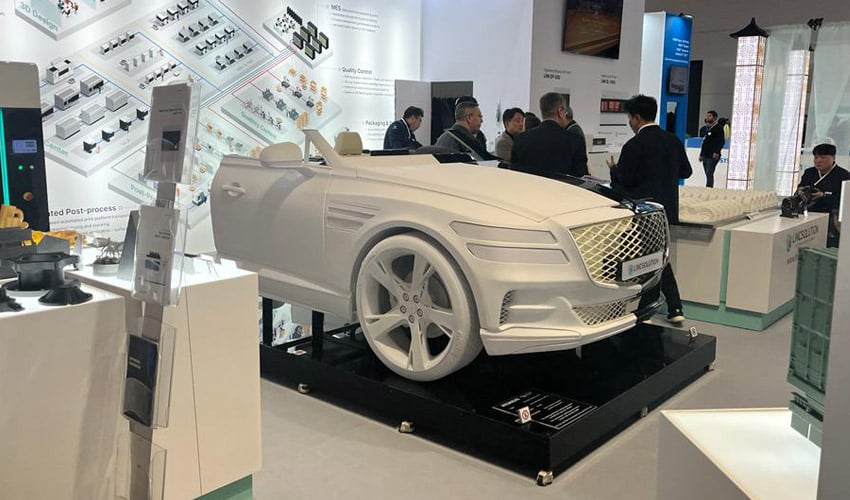
Wherever you went around the Formnext expo in Frankfurt this year, you heard similar buzzwords: automation, mobility and sustainability are some that could be picked up several times – in every industry. We took a closer look and asked around to investigate why these topics were trending and what innovations centered around them.
Going around the event, it was clear that Formnext placed a strong focus on the automotive industry this year. It should be mentioned that innovation and efficiency are the most important drivers in this sector and that additive manufacturing is one of the key technologies driving it forward thanks to its innovative nature. Although AM can be too expensive and ineffective for series production, it still offers numerous advantages in prototyping, single-part manufacturing, and for small series production. The ability to produce complex geometries and customize parts means that additive manufacturing can fully exploit its potential.
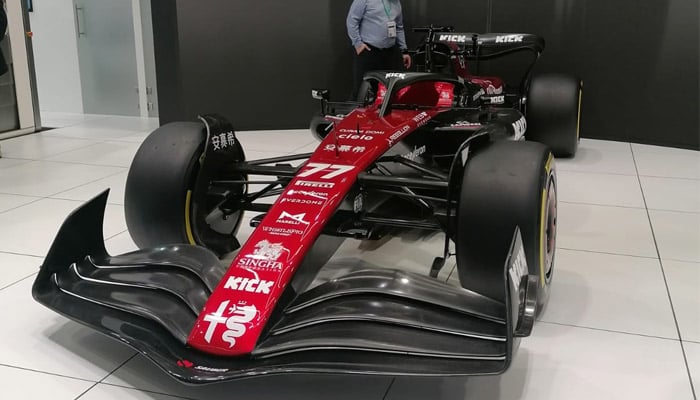
The Alfa Romeo racing car at Formnext 2023
At Formnext, we were able to get a live impression of this and glimpse 3D-printed racing cars from Alfa Romeo, for example, as well as from BWT Alpine in cooperation with 3DSystems. INTAMSYS and the GreenTeam from the University of Stuttgart also impressed us with a 3D-printed, electric, self-driving racing car. These examples are unique applications and prime examples of what is possible with AM. Although 3D printing is the ‘greener’ alternative to conventional manufacturing processes for these individual items, the ‘sustainability’ factor of additive manufacturing needs to be critically examined in the context of the wider automotive industry and series production. The organization Mobility goes Additive has taken on this task.
Mobility, Sustainability & AM: Transparency and Information Exchange
Mobility Goes Additive (MGA), which was also represented at Formnext 2023, is a network of around 120 players from all areas of additive manufacturing with the aim of demonstrating and promoting the potential of AM. MGA therefore brings together users, R&D institutes, machine and material manufacturers who work in eleven interdisciplinary working groups on various relevant topics related to AM in order to advance the field. This is important as the exchange of knowledge between experts is fundamental in order to evaluate these core topics transparently and ensure a reflective transfer of information. In connection with sustainability and mobility, MGA places a special focus on the automotive industry in order to demonstrate new applications there. With regard to sustainability, as mentioned above, the facts and figures need to be processed transparently in order to correctly assess and evaluate the environmental potential of AM.
This plays an important role not only in the automotive industry, but really in any industry involved with AM. To achieve a sustainable ‘green’ transformation of the industry through AM, the carbon footprint, energy consumption, waste reduction, reuse and recycling must be considered, regardless of the sector. One industry that is particularly concerned with sustainable mobility is rail transportation. MGA is focusing on the rail sector in two different working groups. The aim is to determine regulatory framework conditions and approvals for technologies and materials for the additive manufacturing of parts used in trains. However, it is also about the sustainable, long-term creation of reliable train parts with the best possible cost optimization. This should lead to the long-term strengthening of rail transport in order to demonstrate a more sustainable transport alternative.
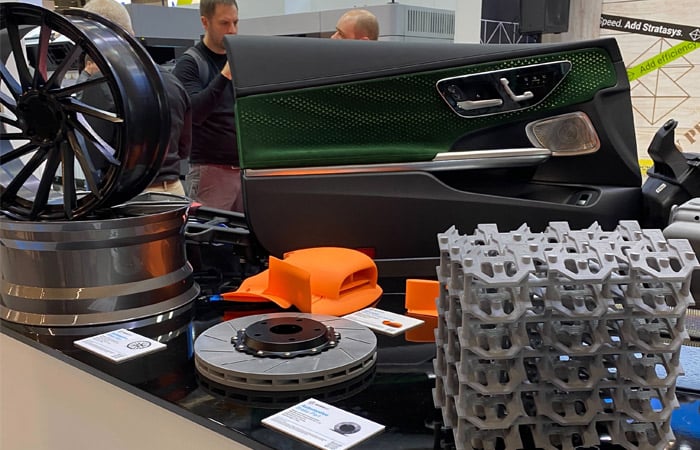
The importance of sustainable materials for the automotive and transportation industry was discussed at Formnext.
The railroads in Europe in particular are important drivers and users of AM and new opportunities are constantly being explored to bring additive manufacturing to rail in even more diverse ways. This was made abundantly clear as well in Formnext’s supporting program. Visitors to the Application Stage on November 9th were able to find out how various European national train companies ÖBB, SNCF and DB are using additive manufacturing and where the challenges and potential lie.
Additive Manufacturing on the Rails
Sebastian Otto from Austrian ÖBB Train Tech spoke about ÖBB’s collaboration with Chromatic 3D Materials for the maintenance of its train fleet. As previously reported, ÖBB relies on the Chromatic RX-AM platform to produce parts and prototypes for its trains. AM enables ÖBB to print parts that are no longer produced conventionally, due to obsolete or discontinued models. In this way, ÖBB can increase the longevity of its train fleet and does not have to manufacture completely new wagons because an essential spare part is no longer available. In this way, AM enables ÖBB to take a sustainable approach to rail transport.
German company Deutsche Bahn is also aiming for trains with a long service life. With a rail network of over 33,000 kilometers, on which several hundred regional trains and around 367 ICE high-speed trains run, the vehicles are exposed to all environmental influences and are subject to wear and tear. Flexible and fast maintenance is therefore a decisive reason for DB to use additive manufacturing. Especially when spontaneous maintenance and interventions are required, AM outperforms conventional maintenance methods.
For example, DB uses Formlabs SLA and SLS printers to print tools and fixings. New materials are also tested in collaboration with Formlabs. Helge Schneevogt and Antonia Knabe from DB Fahrzeuginstandhaltung GmbH (vehicle maintenance) also emphasized the importance of a digital warehouse at DB. By 2030, a digital warehouse will house print templates for around 10,000 parts for vehicle maintenance, which accounts for around 10% of the spare parts in the trains. Of these 10,000 parts, around 70% will be made from polymers and 30% from metal. However, this is currently difficult to enact.
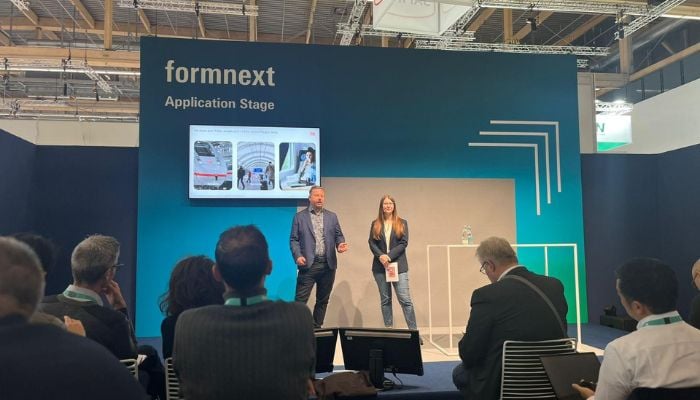
European rail company representatives spoke at the Application Stage about their experiences with AM for rail transport
DB is not only focusing on the maintenance aspect of the trains through additively manufactured parts, but also on improving comfort inside the wagons and at stations with customized applications. The aim is to create a reliable, sustainable means of transportation for the future. To achieve this goal, DB is working with the Berlin-based software provider trinckle. A key feature of trinckle is to generate automated design processes and it provides a platform for advanced product configuration. This allows prints to be customized as required. For example, DB prints handrails with Braille print to help visually impaired people find their way around train stations and can customize the handrails with individual content.
The French SNCF is also experimenting with additive technologies and materials for sustainable integration into its rail system. Pascal de Guio spoke at Formnext about the organization’s experience with polymer printing specifically with multi-jet fusion. SNCF made some promising application trials with PA12, but emphasizes that the AM industry needs to work more on this material to improve its repeatability, predictability and productibility. These quality characteristics are crucial for SNCF, but the focus in manufacturing is always on cost efficiency, a reason as well why they have been experimenting with other technologies such as metal binder jetting and SLM.
Mobility and sustainability go hand in hand and additive manufacturing plays an important role as a driving force in both areas. As the examples of European railroads and Mobility Goes Additive show, there is a lot of research and experimentation into how additive manufacturing can be increasingly integrated into rail transport, but also into the automotive industry, and how a vision of the future can be created in terms of transparency and sustainability.
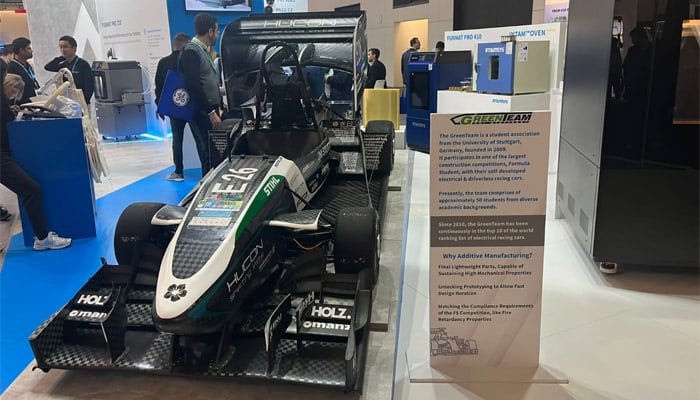
Sustainability and mobility also played an important role in the development of this racing car by Green Team and INTAMSYS.
What do you think of the trending topics of mobility and sustainability in connection with additive manufacturing? Let us know in a comment below or on our LinkedIn, Facebook, and Twitter pages! Don’t forget to sign up for our free weekly Newsletter here, the latest 3D printing news straight to your inbox! You can also find all our videos on our YouTube channel.
*All image credits: 3Dnatives