Comment l’impression 3D révolutionne la chaîne de production automobile : l’expertise de Makershop/HAVA3D
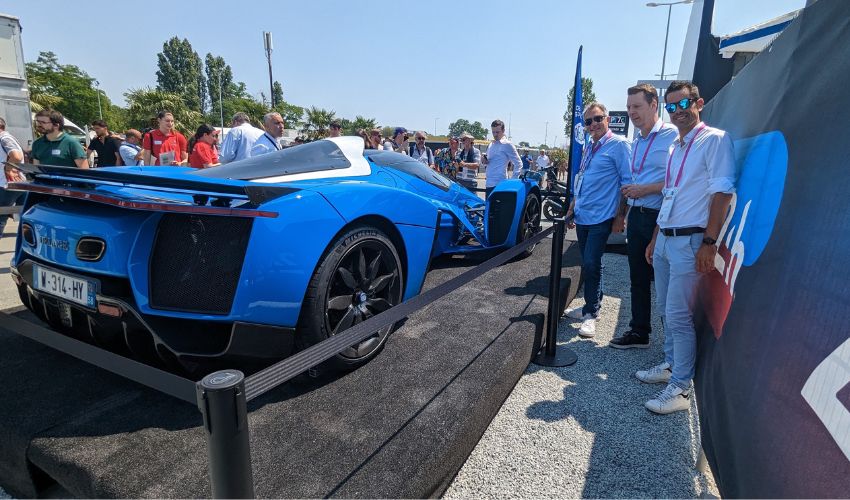
À mesure que les éditions se succèdent, l’innovation tient une place toujours plus importante dans les 24 Heures du Mans, dont le centenaire s’est déroulé le week-end des 10 et 11 juin. L’impression 3D était ainsi présente lors des International Business Days, la convention d’affaires des 24 Heures du Mans, à laquelle ont participé plusieurs acteurs du marché. Une présence qui ne doit rien au hasard pour Makershop/HAVA3D, qui accompagne depuis plusieurs années les acteurs de l’industrie automobile.
Avec des exemples toujours plus nombreux, la fabrication additive intervient à toutes les étapes du cycle de fabrication des véhicules, via différentes technologies, du FFF à l’impression 3D métal en passant par la stéréolithographie (SLA) et le frittage sélectif par laser (SLS). La technologie est ainsi utilisée pour des cas d’usage variés, du prototypage aux pièces finies en passant par des outils d’aide à l’assemblage.
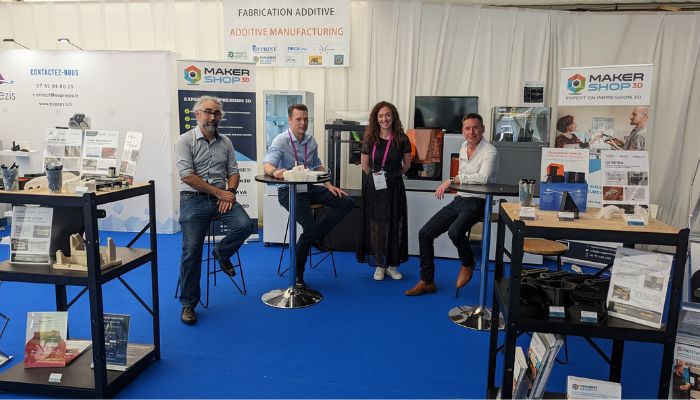
Makershop/HAVA3D Group aux International Business Days, la convention d’affaires des 24 Heures du Mans, les 7 et 8 juin derniers
Makershop/HAVA3D, l’un des leaders français pour les solutions 3D professionnelles, s’est ainsi forgé une solide expérience auprès des acteurs de l’industrie automobile en les aidant à intégrer la fabrication additive au sein de leurs processus de production. Retour aujourd’hui sur plusieurs cas d’application de l’entreprise dans le secteur automobile.
L’impression 3D de pièces détachées automobiles
Parmi les clients de Makershop, on retrouve ainsi LM Retro, une société qui propose l’impression 3D résine de pièces détachées en rupture d’approvisionnement, principalement pour le secteur automobile. Lee Mésange, le fondateur, explique : “la fabrication additive libère des contraintes de la plasturgie et de ses moules très coûteux, un procédé peu rentable pour fabriquer un nombre limité de pièces”.
LM Retro imprime depuis janvier 2022 des pièces à l’unité ou en petites séries, et ce “à un coût désormais abordable”, explique le fondateur. L’entreprise s’est ainsi appuyée sur Makershop pour acquérir l’imprimante 3D SLA Form 3L du fabricant américain Formlabs et les accessoires de post-traitement : Form Wash L pour le nettoyage des pièces ainsi que la chambre UV Form Cure L pour achever la polymérisation.
L’impression 3D résine permet notamment à LM Retro de produire des pièces à la fois esthétiques, flexibles, étanches et résistantes aux températures élevées. Grâce aux solutions adoptées, LM Retro a la capacité de produire des pièces en grand nombre et, parfois même, des pièces grand format, fabriquées avec une large diversité de résines.
La fabrication de moules pour des pièces volumineuses en fibre de carbone aux formes complexes
Dans la lignée des 24 Heures du Mans, l’équipe technique de Makershop/HAVA3D a accompagné les étudiants de l’association ESTACA Formula Team dans la conception d’une monoplace de type Formule 1 dans le cadre de la compétition Formula Student. Le véhicule a pu être construit en moins de 18 mois grâce à l’impression 3D.
Dans ce cas de figure, le recours à la fabrication additive a notamment permis de réduire la masse aérodynamique du véhicule, ce qui a eu pour effet de le faire gagner en performance. Concrètement, l’impression 3D a été employée pour fabriquer 24 moules en PLA utilisés pour concevoir des pièces volumineuses avec des géométries parfois complexes en fibres de carbone, comme les sidepods et les ailerons. La fabrication de ces moules a été réalisée sur les UltiMaker S5 Pro Bundle et l’imprimante F421 haute température de 3DGence. Grâce à l’utilisation de ces imprimantes 3D, l’équipe technique Makershop a réussi à livrer les 24 moules en seulement quinze jours. Un temps record permettant aux membres de l’ESTACA Formula Team d’assurer les délais de la finalisation de sa monoplace. À noter que la production de moules via l’impression 3D est bien moins coûteuse que la fabrication des moules traditionnels en acier ou en aluminium.
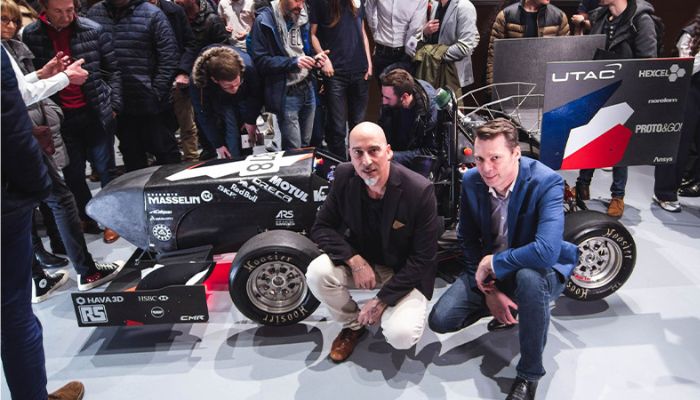
Crédits photo : Makershop/HAVA3D Group
La production de pièces détachées et de petites séries en temps de CoVid
Via Makershop, HAVA3D Group a également accompagné les Écoles Militaires de Bourges dans l’intégration de 60 imprimantes 3D UltiMaker S5 utilisant la technologie FFF. Elles ont été installées en avril 2020, au début de la crise du CoVid-19. Il s’agit de la plus grande ferme d’imprimantes 3D militaires en Europe. À ce jour, les machines ont permis de fabriquer plus de 70 000 pièces. Il peut s’agir de pièces de réparation pour des véhicules tels que des capuchons, bagues, commodos, ou encore de protections individuelles.
La fabrication additive a permis aux Écoles Militaires de Bourges de centraliser leur production sans dépendre de la chaîne d’approvisionnement, alors fragilisée par la crise sanitaire. Le recours à cette technique a ainsi réduit le temps de réparation et les risques de panne, et ce tout en diminuant les coûts et en renforçant l’autonomie de l’armée de Terre.
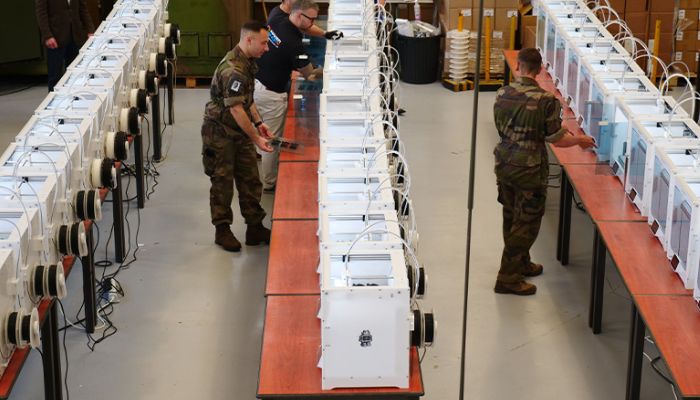
Crédits photo : Makershop/HAVA3D Group
L’impression 3D d’outils destinés aux voitures électriques
La société britannique Dunlop Systems fabrique des solutions anti-vibrations pour le secteur automobile, notamment des composants de suspension pour pneumatiques et des systèmes électroniques de contrôle. La société a adopté l’impression 3D composite du fabricant Markforged dans le cadre de la conception et de la mise sur le marché d’une voiture électrique, notamment pour les pièces prototypes en Onyx.
L’Onyx et la fibre de carbone ont ainsi intéressé Dunlop Systems pour leur capacité à constituer des pièces à la fois légères et robustes, qui résistent aux environnements corrosifs. Le fabricant automobile a d’ailleurs décidé de remplacer l’ensemble de son outillage par cette nouvelle méthode de production. Dunlop Systems justifie également le recours à la fabrication additive par les économies qu’elle lui a permis de réaliser. L’usage de l’impression 3D a, en effet, fait passer le coût des pièces de 8 000 à 2 000 livres sterling, indique le fabricant. Concernant l’outillage, Dunlop Systems ne dépense à présent plus que 11 000 livres, contre environ 20 000 auparavant. Mark Statham, Production Engineering Manager chez Dunlop Systems, espère même économiser 40 000 livres sur l’année grâce à la fabrication additive.
Dunlop Systems prévoit de se servir d’une autre imprimante 3D de Markforged, issue de la gamme X7, afin de pouvoir répondre au nombre grandissant d’applications de la part de ses clients.
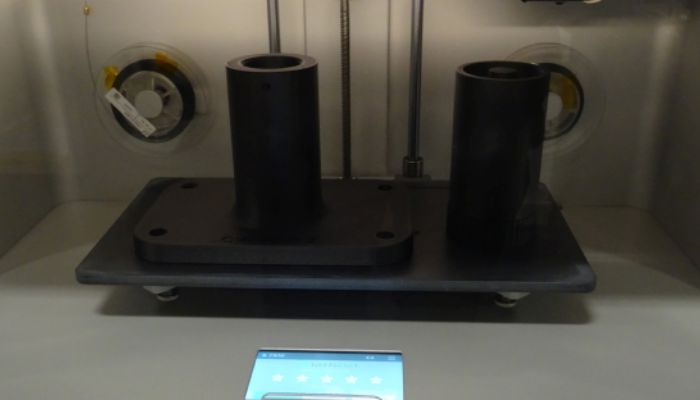
Crédits photo : Dunlop Systems
La fabrication d’outils de posage résistants aux fluides chimiques et répondant aux normes FST
Dans son cas d’application interne, Makershop/HAVA3D propose à ses clients de fabriquer un gabarit de posage pour des équipements industriels contenant des fluides chimiques.
Pour répondre aux exigences de l’industrie automobile (résistance au feu et à la fumée), l’entreprise mancelle s’est orientée vers les solutions de 3DGence. Parmi elles, l’imprimante 3D F421, qui dispose d’un grand volume de fabrication thermorégulé de 380 x 380 x 420mm et de trois modules d’impression. En outre, elle est compatible avec de nombreux matériaux, du PLA au PEEK en passant par l’ULTEM™, sans oublier les matériaux chargés en fibres de carbone.
L’équipe de Makershop/HAVA3D a, par exemple, choisi l’ULTEM™ 9085 pour imprimer l’outillage de posage. Ce matériau présente de nombreux avantages, à savoir la rapidité d’impression, qui permet de réduire les délais de fabrication, ainsi que la résistance aux fluides chimiques et à tout type de solvants, huiles ou hydrocarbures. L’ULTEM™ 9085 répond également aux normes FST (Flame, Smoke and Toxicity), notamment à la norme UL94-V-0.
Concernant le post-traitement du gabarit, Makershop/HAVA3D a enfin opté pour le Material Management System (MMS). Cet équipement permet à la fois de stocker les bobines de filament 3D, avec un contrôle de l’humidité, de les faire sécher et de faire cuire les pièces imprimées. La combinaison des deux équipements de 3DGence simplifie la traçabilité des productions et facilite la certification, tout en présentant de faibles coûts d’utilisation.
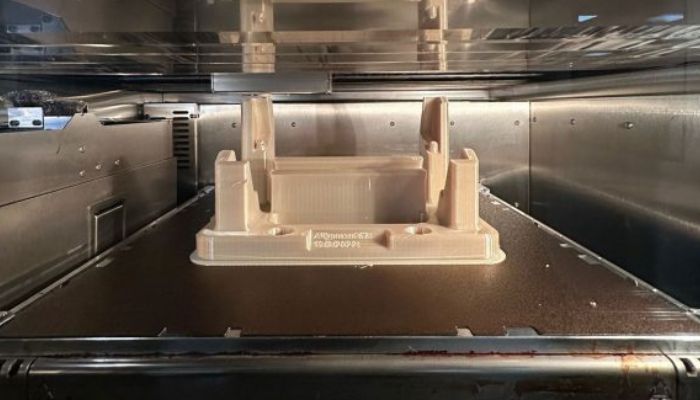
Crédits photo : Makershop/HAVA3D Group
Que pensez-vous de ces différents cas d’application de l’impression 3D dans l’industrie automobile ? N’hésitez pas à partager votre avis dans les commentaires de l’article ou avec les membres du forum 3Dnatives. Retrouvez toutes nos vidéos sur notre chaîne YouTube ou suivez-nous sur Facebook ou Twitter !
Superbe voiture la Delage D12…
Superbe projet devenu réel.
Une Supercar qu’Imalize connaît bien 😉
Mix Innovation/conventionnel pour l’excellence, l’efficience.