New Liquid Metal Printing Process Is 10X Faster
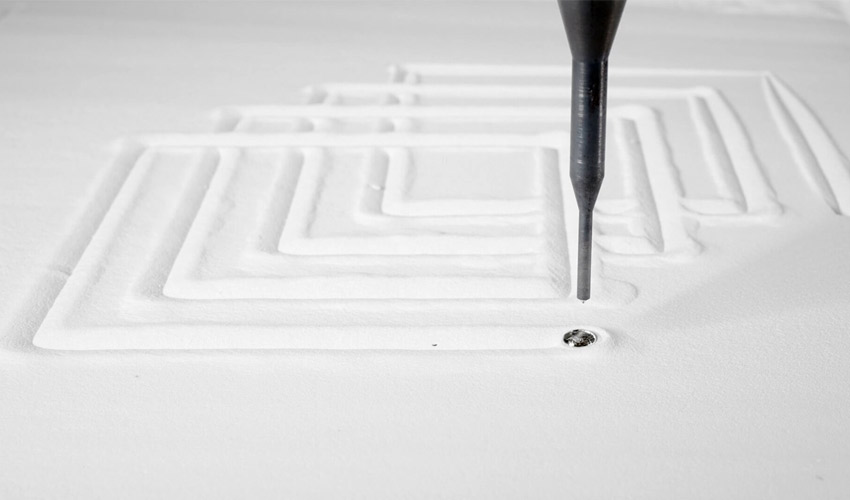
What if you could 3D print large-scale metal parts quickly and cheaply? That’s the question posed by a team from MIT, and more specifically the MIT Self-Assembly Lab, who set out to circumvent the current limitations of metal 3D printing. They have developed a process called Liquid Metal Printing (LMP), which is similar to free-form casting: in concrete terms, molten metal is extruded into a vat of 100-micron glass beads (reminiscent of powder) following a predefined path. From there, the material can harden and form the desired part. No support is required, as the glass beads act as a mold for the molten metal. So far, the team has carried out several experiments with aluminum and achieved very high printing speeds: the process is said to be 10 times faster than other metal technologies on the market, whatever the size of the part.
3D printing in a granular substance is nothing new in itself, but it is generally done with polymers and silicones. Using metals is more complex, not only because of the melting temperature required, but also because of extrusion constraints – molten aluminum can’t be extruded through just any nozzle without corroding and destroying it. Skylar Tibbits, associate professor in the Department of Architecture and co-director of the Self-Assembly Lab, and his colleagues have been working to overcome the volume and time limits imposed by metal additive manufacturing. Today, only the WAAM process can handle large volumes, but it remains too slow compared with so-called traditional manufacturing methods. This is where LMP comes in, seeking to reconcile speed and large format.
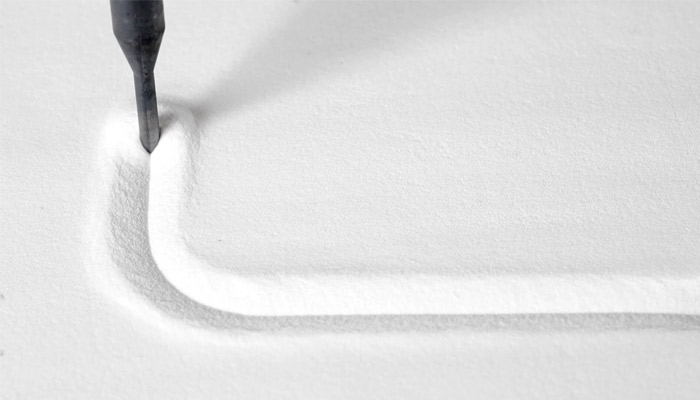
Molten metal is deposited in the powder pan
How Does Liquid Metal Printing Work?
The LMP machine is made up of three essential parts: the nozzle and a custom-built electric furnace, the print bed and a temperature regulator that ensures meticulous control of the aluminum temperature from the furnace to the nozzle. This custom-built 5 kW furnace is the heat source and can contain a graphite crucible to keep the metal molten before extrusion. The nozzle itself posed a number of challenges: in all additive manufacturing processes, one of the issues is to ensure corrosion resistance of the machine’s mechanical components. As you can imagine, molten metal cannot be extruded through just any nozzle. The team therefore carried out several tests before creating a ceramic nozzle.
In tests, the team printed chairs, table legs and decorative objects. They claim that printing speeds are 10 times faster than those of commercially available metal 3D printing processes. Several paths have been tested – spiral, straight, with overlapping trajectories, etc. – and the results are impressive. If we look at the print quality, we see that it’s still crude – the aesthetics aren’t up to scratch, and this is something the team needs to focus on.
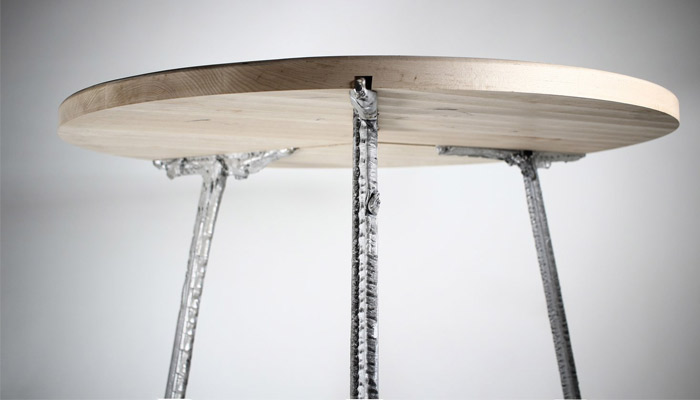
The table legs were 3D printed using liquid metal printing
According to the team, the current coarse resolution of the LMP process is comparable to that of WAAM, as processes requiring strategic post-machining. Nevertheless, the LMP process is at least 10 times faster and, with more efficient heating, could potentially achieve processing rates in excess of tens of kg/hour, approaching the processing rate of injection molding or die casting, at around 100 kg/hour. One of the advantages of LMP technology over other metal additive manufacturing methods is the unique thermal cycle of a print. Unlike the WAAM process, which involves successive melting and cooling of the part to maintain its structure, the granular support used in the LMP process supports the molten material throughout the printing process.
Ultimately, the aim would be to use recycled aluminum, which would be melted down to recreate objects using the LMP process. The team still needs to improve on a number of points, notably resolution and flow control, but the technology looks promising! Tibbits conclude, “If we could make this machine something that people could actually use to melt down recycled aluminum and print parts, that would be a game-changer in metal manufacturing. Right now, it is not reliable enough to do that, but that’s the goal.” You can found out more about Liquid Metal Printing HERE.
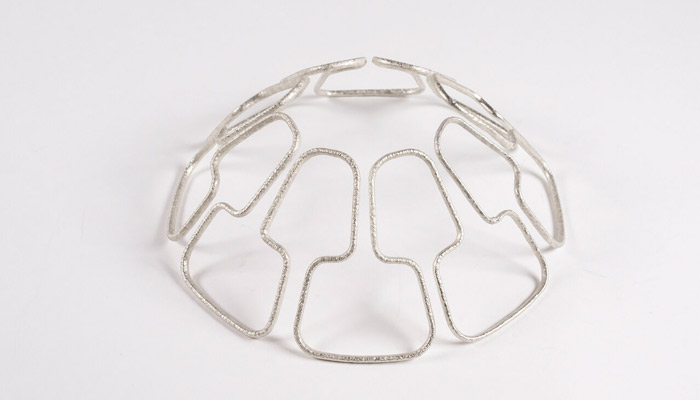
Another example of a shape 3D printed using the liquid metal printing process
What do you think of this liquid metal printing process? Let us know in a comment below or on our LinkedIn, Facebook, and Twitter pages! Don’t forget to sign up for our free weekly newsletter here, the latest 3D printing news straight to your inbox! You can also find all our videos on our YouTube channel.
*All Photo Credits: MIT Self-Assembly Lab