Titane vs Aluminium : quel métal choisir pour l’impression 3D ?
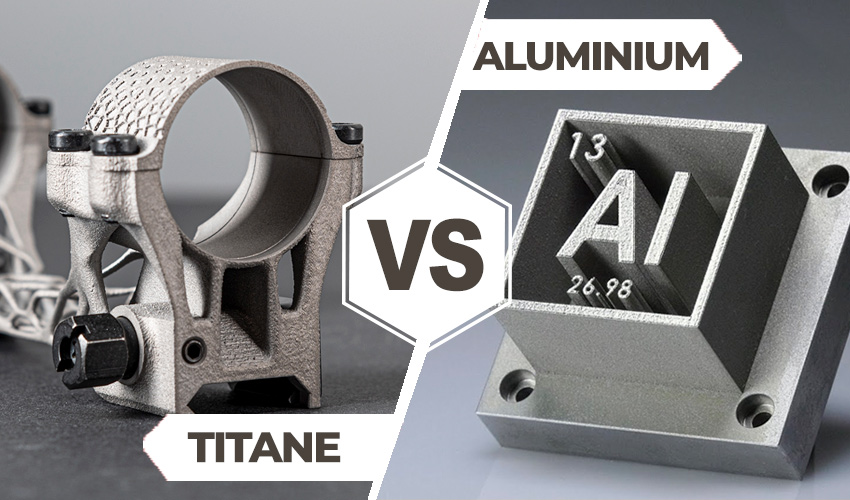
Le métal est actuellement l’un des matériaux les plus recherchés dans les processus de fabrication additive. Sans surprise, ses excellentes propriétés en font le choix idéal pour les applications les plus exigeantes en termes de performance et de résistance. Dans cet article, nous nous concentrerons sur deux des principaux métaux utilisés dans l’impression 3D : le titane et l’aluminium. Ceux-ci sont principalement utilisés pour des procédés tels que la fusion laser sur lit de poudre (L-PBF) ou le dépôt de matière sous énergie concentrée (DED). Ils sont principalement disponibles sous forme de poudre, en particulier dans les environnements industriels. Nous allons comparer leurs similitudes et leurs différences, afin de mieux connaître leurs propriétés et leurs applications, et de comprendre les avantages qu’ils offrent dans ce processus de fabrication.
Production et caractéristiques du titane et de l’aluminium
Le titane
Le titane est un matériau qui ne se trouve pas dans la nature en tant qu’élément et qui doit être extrait de minéraux tels que le rutile (TiO2) ou l’ilménite (FeTiO3). L’extraction du titane pur est un processus complexe qui comporte plusieurs étapes. La méthode la plus utilisée pour la production de titane pur est la méthode Kroll, développée par le chimiste américain William J. Kroll en 1940. Cette méthode implique la réduction du dioxyde de titane (TiO2) avec du chlore gazeux (Cl2) pour produire du tétrachlorure de titane (TiCl4), qui est ensuite réduit avec du magnésium (Mg). Bien que la méthode Kroll soit efficace pour produire du titane pur, il s’agit d’un processus coûteux qui nécessite une grande quantité d’énergie. En outre, la réactivité élevée du titane le rend difficile à obtenir en tant que métal pur, de sorte qu’un échantillon d’une pureté de 99,9 % est considéré comme du titane commercialement pur. C’est pourquoi il est normalement utilisé en combinaison avec d’autres éléments pour former un alliage.
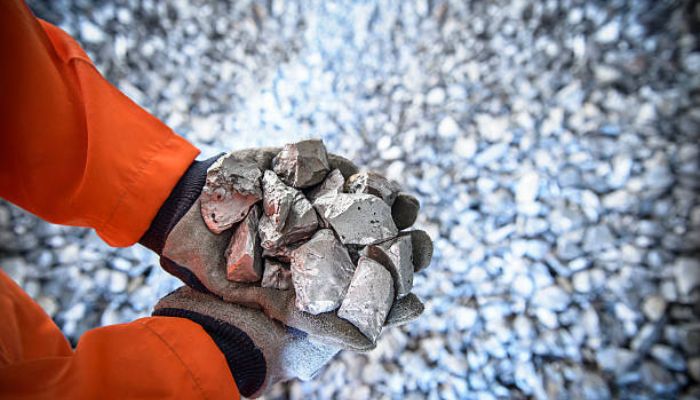
Crédits photo : Getty Images
Le titane possède de nombreuses propriétés qui le rendent très polyvalent et utile dans de nombreux secteurs. Comme expliqué précédemment, il est souvent employé sous forme d’alliage mais le titane extrait pur est utilisé dans certaines applications, comme dans l’industrie médicale, grâce à sa grande biocompatibilité. Ses principales caractéristiques sont une grande résistance mécanique, une faible densité, une excellente résistance à la corrosion et une grande rigidité.
Les principaux alliages de titane utilisés dans l’impression 3D sont les suivants :
- Titane 6Al-4V, grade 5 : c’est le plus important et le plus courant. Il est utilisé en fabrication additive en raison de sa résistance et de sa durabilité élevées. L’alliage est composé de titane, d’aluminium et de vanadium et peut résister à des températures élevées et à des environnements corrosifs.
- Titane 6Al-4V, grade 23 : biocompatible, il est couramment utilisé dans les implants médicaux et les prothèses.
- Titane Beta 21S : plus résistant que les alliages de titane conventionnels, il est également plus résistant à l’oxydation et à la déformation. Il est parfait pour les implants orthopédiques et les applications de moteurs aérospatiaux. Le titane Beta est prisé en orthodontie.
- Cp-Ti (titane pur), grade 1, 2 : utilisé dans l’industrie médicale pour une large gamme d’applications en raison de la biocompatibilité du titane avec le corps humain.
- TA15 : il s’agit d’un alliage presque entièrement composé de titane, auquel ont été ajoutés de l’aluminium et du zirconium. Les composants fabriqués à partir de cet alliage sont très solides et résistants aux températures élevées, ce qui les rend idéaux pour la construction de pièces solides dans les avions et les moteurs. Ils sont également très légers par rapport à leur résistance.
Aluminium
L’aluminium est un métal qui présente un excellent compromis entre légèreté et résistance. En plus d’être résistant à la corrosion, il peut être soudé. Il est assez rare de le trouver à l’état pur, on va donc l’employer sous forme d’alliage, avec des métaux qui vont améliorer ses propriétés physiques et mécaniques, comme le silicium et le magnésium. Comme pour le titane, deux procédés industriels consécutifs permettent d’obtenir le matériau à l’état pur. Dans le premier procédé, appelé procédé Bayer, l’oxyde d’aluminium est obtenu à partir du minerai de bauxite. Le minerai est lavé et broyé, dissous dans de la soude caustique et filtré pour obtenir de l’hydroxyde d’aluminium pur. Il est ensuite chauffé pour obtenir de la poudre d’oxyde d’aluminium. Dans le second procédé, appelé procédé Hall-Héroult, la réduction électrolytique de l’oxyde d’aluminium est effectuée pour obtenir de l’aluminium pur. La plupart des usines de traitement sont construites à proximité des mines afin de réduire les coûts de transport du minerai.
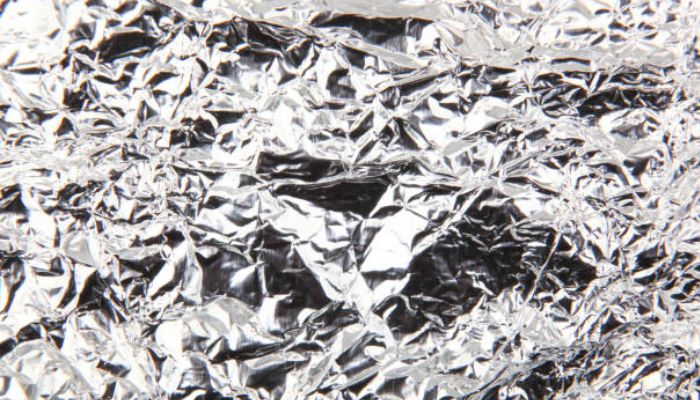
Crédits photo : Getty Images
Comme indiqué ci-dessus, les alliages d’aluminium sont plus courants que la forme pure et sont utilisés dans de nombreuses applications industrielles. En outre, ils présentent un très bon rapport résistance/poids et une très bonne résistance à la fatigue et à la corrosion. Ils sont également recyclables, thermiquement et électriquement conducteurs et peu toxiques.
Les principaux alliages utilisés dans l’impression 3D en aluminium sont les suivants :
- AISi10Mg : il s’agit de l’alliage le plus courant formé par le silicium et le magnésium. Il permet de fabriquer des pièces solides et complexes et est utilisé pour créer divers objets tels que des boîtiers, des pièces de moteur et des outils de production.
- Al2139 : l’alliage d’aluminium le plus résistant, idéal pour des secteurs tels que l’automobile en raison de sa légèreté, de sa solidité et de sa résistance aux produits chimiques. Il a été utilisé par des organisations telles que l’armée de l’air américaine, Mercedes-Benz et Airbus. L’intérêt de ce matériau est qu’il a été spécialement conçu pour la fabrication additive et qu’il surpasse de nombreux autres alliages sur le marché.
- Série Al 7000 : il s’agit d’une série célèbre d’alliages en poudre, avec une résistance élevée à la traction et aux basses températures.
- Al 6061 & Al 7075 : récemment, les fabricants 3D ont obtenu de très bons résultats en utilisant ces deux alliages. Le 6061 a une résistance à la traction et une dureté inférieures à celles du 7075. En revanche, le 7075 résiste mieux aux chocs et se déforme moins que l’aluminium 6061.
- A201.1 : il fait partie de la série 200 des alliages cuivre-aluminium, connus pour être très résistants. Cependant, ils sont difficiles à couler. Ces alliages sont recommandés pour les applications où le rapport résistance/poids est crucial, comme dans les transports et l’aérospatiale.
Et si l’on compare les deux métaux, quelles sont les différences ?
En termes de rapport résistance/poids, le titane est le choix idéal lorsqu’une grande résistance et une grande robustesse sont requises, ce qui explique qu’il soit employé pour les composants médicaux ou même dans les composants de satellites. En revanche, bien que l’aluminium soit moins résistant que le titane, il est beaucoup plus léger et plus abordable. En ce qui concerne les propriétés thermiques, l’aluminium est parfait pour les applications qui nécessitent une conductivité thermique élevée. Le titane, quant à lui, est idéal pour les applications dans des environnements à haute température en raison de son point de fusion élevé, comme les composants des moteurs aérospatiaux. L’aluminium et le titane présentent tous deux une excellente résistance à la corrosion. Le titane est toutefois plus biocompatible que l’aluminium, raison pour laquelle il est largement utilisé dans le secteur médical.
Forme du matériau et technologies 3D utilisées
Forme
Dans la plupart des cas, le titane et l’aluminium se présentent sous forme de poudre, bien qu’ils puissent également être disponibles sous forme de fil, comme le filament de titane ou d’aluminium proposé par Virtual Foundry ou encore Nanoe.
Pour imprimer en 3D des pièces avec ces métaux, il faut d’abord obtenir la poudre d’alliage, ce qui se fait selon deux techniques principales : l’atomisation par plasma ou l’atomisation par gaz. L’atomisation par plasma (gaz ionisé) est un procédé qui utilise des températures élevées, une source d’énergie et de chaleur, un milieu inerte tel que l’argon et des vitesses élevées pour atomiser le métal. Ce procédé produit des poudres résistantes à l’usure de haute qualité. L’atomisation au gaz, quant à elle, utilise de l’air, de l’argon ou de l’hélium comme gaz pour fragmenter un flux de matériau en fusion. Il s’agit d’un procédé très efficace, largement utilisé pour produire des poudres métalliques fines et sphériques. La technique utilisée pour fabriquer la poudre métallique est importante, car elle influence évidemment les propriétés finales de la pièce.
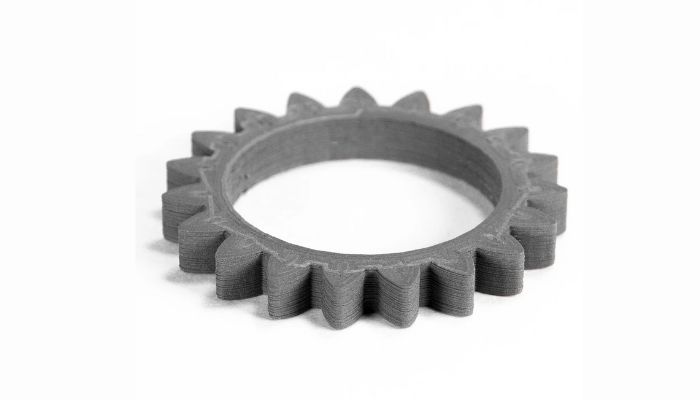
Engrenage en titane 64-5 non fritté (crédits photo : SAPPHIRE3D)
Technologies 3D utilisées
Pour travailler le titane en impression 3D, un grand nombre de procédés peuvent être employés, comme la fusion laser sur lit de poudre (L-PBF), le DED ou le liage de poudre. Pour les procédés relatifs à l’aluminium, il en existe un autre qui s’ajoute à ceux déjà mentionnés, comme la pulvérisation à froid, également connue sous le nom de Cold Spray.
Dans les procédés de fabrication additive L-PBF, le faisceau laser est utilisé pour chauffer le métal en poudre couche par couche jusqu’à son point de fusion et construire l’objet. Le titane fond à des températures très élevées (1 600°C), de sorte que les effets thermiques et mécaniques du matériau devront être analysés avant l’impression 3D. La température de fusion de l’aluminium est beaucoup plus basse (environ 630°C), mais l’aluminium a une réflectivité et une conductivité thermique élevées. Un autre aspect intéressant de la fabrication additive avec l’aluminium est qu’il forme une couche d’oxyde naturelle, ce que d’autres métaux font plus tard sur leurs bords, ce qui signifie que la présence de cette fine couche sur l’aluminium ralentit le processus.
En ce qui concerne le DED, il s’agit d’un processus très similaire au précédent, mais ici le matériau est fondu en même temps qu’il est déposé par la buse et peut se présenter sous forme de poudre ou de fil pour la fabrication. Normalement, cette technologie permet d’obtenir une vitesse de production plus élevée et un coût plus faible par unité de volume.
Dans le cas du Binder Jetting, le matériau se présente sous la forme d’une poudre qui n’est pas fondue, mais pour que les particules adhèrent les unes aux autres, un liant est pulvérisé sur la couche à des endroits spécifiques au moyen d’une tête d’impression. Une étape de frittage est également nécessaire après l’impression. En sortant de l’imprimante 3D, les pièces sont très fragiles et poreuses et devront être traitées thermiquement pour obtenir leurs propriétés mécaniques finales.
Dans les procédés de Cold Spray, on trouve également le matériau métallique sous forme de poudre, mais comme dans ce cas il n’est pas nécessaire de le fondre ou de le fusionner, la pulvérisation à froid permet d’éviter les déformations dues à la chaleur et une atmosphère protectrice n’est pas nécessaire.
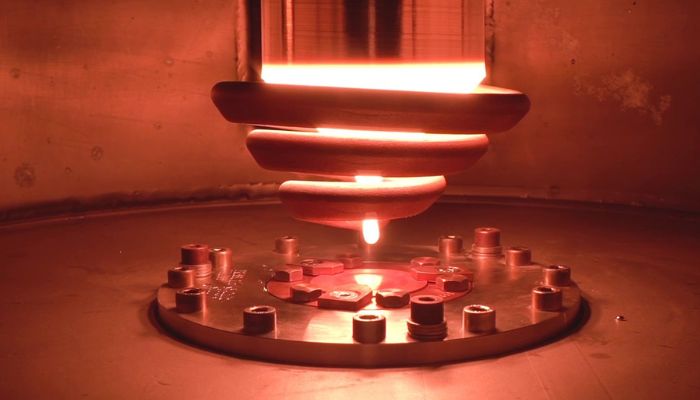
Crédits photo : Sandvik
Post-traitement
Pour obtenir un résultat optimal, il est essentiel de passer par une ou plusieurs étapes de post-traitement. Il n’y a pas de différences spécifiques dans le post-traitement du titane et de l’aluminium, les étapes suivantes s’appliquent donc aux deux matériaux. Le titane et l’aluminium étant souvent utilisés dans des applications soumises à des contraintes mécaniques, le microbillage et le grenaillage de précontrainte sont très utiles. Dans la première méthode, de petites billes métalliques ou céramiques sont projetées contre la surface de la pièce pour créer une déformation contrôlée de la couche superficielle de la pièce. Cela améliore l’adhérence des revêtements ultérieurs et réduit la probabilité de fissures et de fractures, entre autres. Le grenaillage de précontrainte n’enlève que la couche supérieure du matériau, ce qui peut améliorer l’aspect esthétique de la pièce, éliminer la saleté et la corrosion et préparer la surface pour les revêtements ultérieurs.
Une autre option consiste à combiner l’impression métallique avec les méthodes de fabrication traditionnelles. L’usinage CNC est un processus de post-traitement approprié à cette fin, car il garantit des tolérances serrées et la finition de surface souhaitée. Avec la technologie DED en particulier, les pièces imprimées en 3D ont une surface très rugueuse car le métal est fondu directement pendant le processus d’extrusion. C’est pourquoi l’usinage CNC est toujours nécessaire pour obtenir une surface lisse et définie.
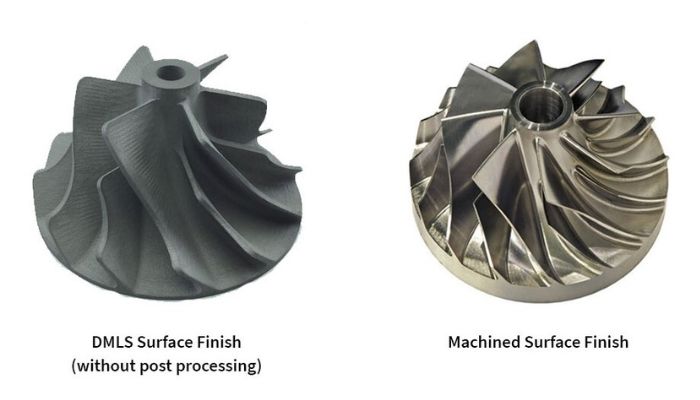
Crédits photo : FacFox
Le recuit de mise en solution est une option de traitement thermique qui consiste à chauffer la pièce imprimée à une température élevée et à la refroidir rapidement pour modifier la microstructure, ce qui améliore la ductilité du matériau, c’est-à-dire sa capacité à se déformer sous l’effet d’une charge avant de se rompre. En général, on obtient de meilleures propriétés mécaniques avec ce procédé, qui est surtout utilisé pour les pièces en aluminium.
Le frittage est également nécessaire pour l’aluminium et le titane quand ils sont employés dans des procédés d’impression 3D dits indirects, comme le FDM ou le liage de poudre. Après la phase d’impression, les pièces doivent subir un processus de déliantage afin de séparer les polymères du liant du métal. Les pièces sont ensuite chauffées à une certaine température dans un four de frittage, juste en dessous de la température de fusion, ce qui permettra de consolider l’objet final. Il en résulte des pièces à très faible porosité, car les cavités où se trouvait le liant sont fermées au cours du processus, ce qui entraîne une compression.
Applications
L’industrie aérospatiale a trouvé un grand avantage à l’utilisation de la fabrication additive de titane. C’est un matériau idéal pour la fabrication de composants aéronautiques, tels que les moteurs à réaction et les turbines à gaz, car il permet de réduire considérablement le poids des structures soumises à de fortes contraintes. Un exemple d’application du titane dans la fabrication additive est le partenariat de Boeing avec Norsk Titanium pour la fabrication de grands composants structurels pour le 787 Dreamliner. La technologie utilisée dans ce processus est le DED, qui serait 50 à 100 fois plus rapide que les systèmes à base de poudre et utiliserait 25 à 50 % de titane en moins que le forgeage, ce qui pourrait permettre d’économiser jusqu’à 3 millions de dollars par avion.
Si le titane est actuellement utilisé dans l’exploration spatiale grâce à l’impression 3D, les applications de l’aluminium dans l’industrie se sont multipliées. Par exemple, Boeing produit des pièces imprimées en 3D à partir d’alliages d’aluminium recouverts de nanoparticules pendant la phase de refroidissement. Cela permet de souder un alliage d’aluminium extrêmement résistant sans qu’il ne se fissure à chaud. Les pièces fabriquées sont beaucoup plus légères, ce qui permet à l’avion d’utiliser le carburant de manière efficace et de parcourir de plus longues distances avec la même quantité de carburant.
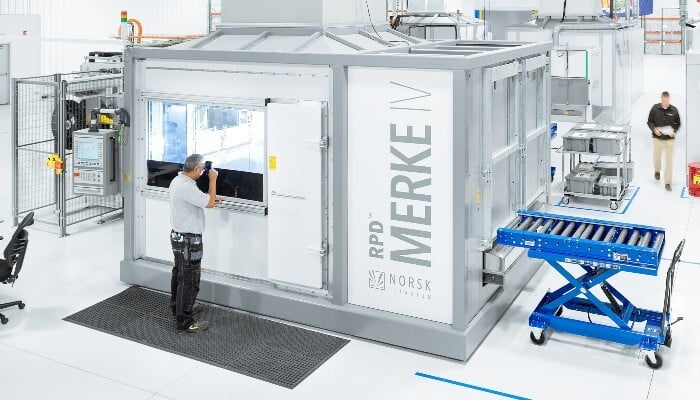
Cette machine fabrique des pièces pour le Boeing 787 (crédits photo : Norsk Titanium)
Bien que le prix élevé du titane dans le secteur automobile puisse être un obstacle à son utilisation généralisée, nous pourrions assister à une augmentation de son emploi dans ce secteur, en particulier dans le segment du luxe. Actuellement, l’impression 3D est utilisée pour créer des pièces dont le rapport poids/performance est crucial. Par exemple, Bugatti a imprimé l’étrier de frein de son système de freinage en titane à l’aide de la technologie SLM en seulement 45 heures, ce qui est censé être 40 % plus léger qu’un étrier de frein en aluminium fraisé de manière conventionnelle. Malgré sa légèreté, la pièce en titane garantit également son élasticité et sa résistance à la température. L’aluminium, quant à lui, est plus courant dans l’industrie automobile. Porsche a eu recours à l’impression 3D pour créer des pistons en aluminium haute performance pour son modèle phare 911, la GT2 RS. Grâce à cette technologie, le moteur biturbo de 700 ch peut gagner jusqu’à 30 ch de puissance et améliorer son efficacité. En outre, en 2020, Porsche a produit un boîtier entièrement en aluminium imprimé en 3D pour une transmission électrique, qui a passé avec succès tous les tests de qualité et de charge de l’entreprise.
Enfin, le titane est un matériau très intéressant dans l’industrie médicale en raison de sa grande solidité et de sa résistance à la corrosion, ainsi que de sa biocompatibilité, qui le rend idéal pour les implants orthopédiques et dentaires. L’impression 3D permet de créer des structures poreuses qui imitent la texture des os, ce qui contribue à la guérison et à la croissance rapides des os et des tissus. TrabTech, en Turquie, fabrique des implants trabéculaires, comme une hanche, en utilisant du titane. L’utilisation de l’aluminium est quant à elle moins courante dans l’industrie médicale que celle du titane, mais il peut être employé pour des applications orthopédiques et dentaires.
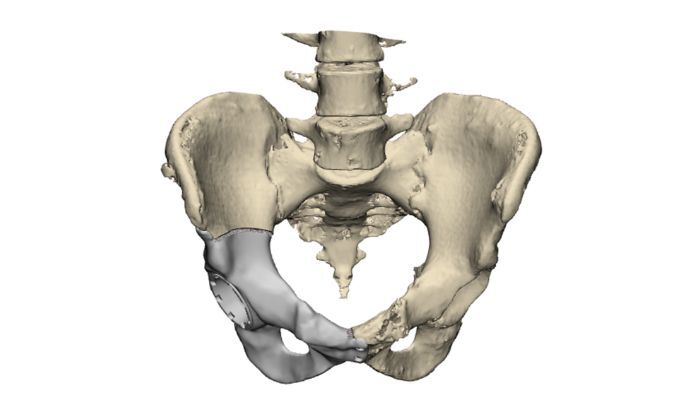
TrabTech fabrique des implants trabéculaires en titane (crédits photo : TrabTech)
Prix et fabricants
Le titane présente un inconvénient majeur en raison de son prix élevé. Selon le rapport Wohlers 2021, la poudre d’alliage de titane Ti-6AI-4V ou le titane pur de grade 2 coûte environ 363 USD par kilogramme, ce qui le place dans l’un des segments de prix les plus élevés. En revanche, l’aluminium est nettement moins cher, l’alliage d’aluminium AISi7 étant disponible pour 94 USD/kg de poudre et l’AISi10Mg pour 98 USD/kg.
Sur le marché des fabricants, nous citons Heraeus Additive Manufacturing, une entreprise allemande spécialisée dans le traitement des métaux précieux qui produit différents types de titane, tels que le 6Al-4V, le grade 5 et le grade 23. GKN, quant à elle, propose du titane pur et du titane Beta 21S. Du côté de l’aluminium, Uniformity Labs et Equispheres produisent l’alliage d’aluminium AISi10Mg, tandis qu’APWorks produit de la poudre d’alliage d’aluminium de la série 7000.
Et vous, utilisez-vous plutôt du titane ou de l’aluminium en fabrication additive ? Partagez votre avis dans les commentaires de l’article. Retrouvez toutes nos vidéos sur notre chaîne YouTube ou suivez-nous sur Facebook ou Twitter !