Satair imprime en 3D une pièce de rechange certifiée pour les avions Airbus
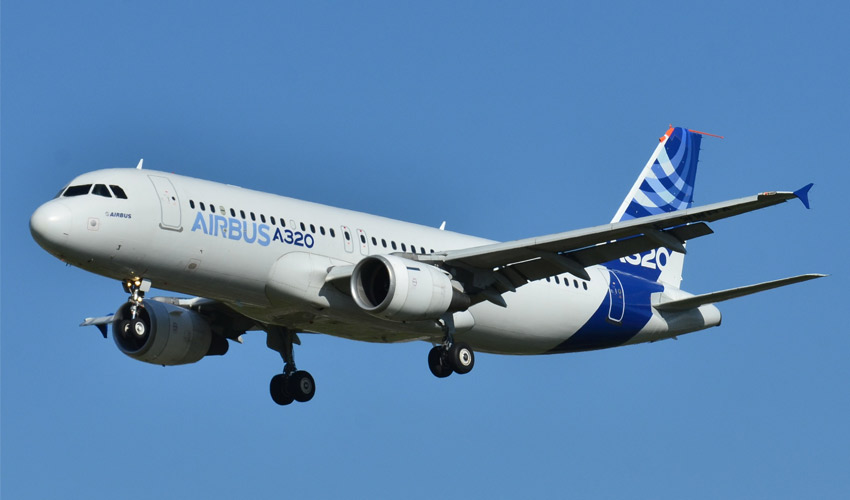
Satair, filiale d’Airbus depuis 2011, vient de fournir à l’un de ses clients une pièce de rechange certifiée et imprimée en 3D métal, qui a déjà effectué son premier vol avec succès ! Cette pièce est la clôture du bout de l’aile d’un avon A320ceo qui n’était plus disponible auprès du fournisseur actuel. En utilisant la fabrication additive métallique pour la remplacer, la compagnie a pu éviter que cet avion soit cloué au sol. A un niveau plus large, cette opération met en évidence la flexibilité accrue de la production de pièces grâce aux technologies d’impression 3D, tout en respectant les mêmes normes de haute qualité garanties par la certification EASA Form1. L’entreprise estime que les coûts ont été réduits de 45 %, ce qui en fait une solution moins coûteuse pour les clients et avec un délai d’exécution plus court.
Satair est une entreprise danoise qui produit des composants aéronautiques et fournit des services depuis 1957. Elle fait entièrement partie d’Airbus depuis 9 ans maintenant, plus particulièrement du département Airbus Services. Satair est présente sur 10 sites dans le monde et emploie plus de 1 300 personnes pour soutenir le cycle de vie des avions Airbus grâce à un portefeuille complet et intégré de produits de gestion du matériel, de services et de modules d’assistance sur mesure, flexibles et à forte valeur ajoutée. Avant de passer à l’impression 3D, la société a étudié diverses alternatives, y compris des méthodes de fabrication conventionnelles.
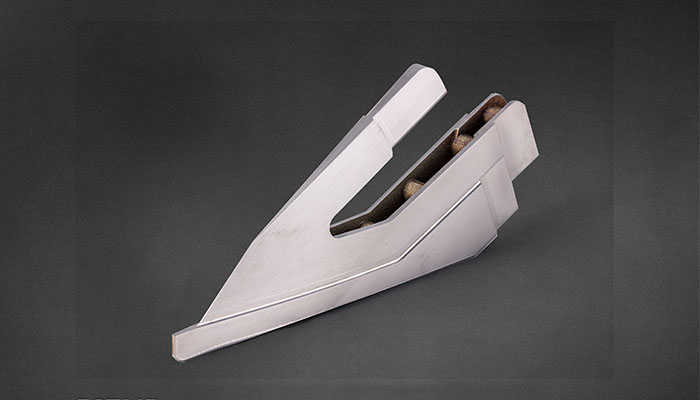
La première pièce en vol imprimée en 3D et certifiée pour le A320ceo (crédits photo : Airbus)
Pourquoi Satair a-t-il choisi la fabrication additive ?
La pièce en question – une clôture de bout d’aile d’A320ceo – existe en quatre versions : tribord, bâbord, supérieure et inférieure. Dans ce cas, le fournisseur de pièces ne pouvait plus fournir la pièce moulée, ce qui a entraîné une perte naturelle des moules utilisés pour créer ces pièces et un coût d’investissement potentiellement élevé pour Satair pour remplacer les moules pour des commandes individuelles. Après avoir étudié d’autres options conventionnelles telles que la reconception de la pièce pour la technologie d’usinage, les implications en termes de coûts et de délais n’étaient pas compétitives. L’un des avantages de la fabrication additive est bien sûr la flexibilité et la liberté accrue lorsqu’il s’agit de fabriquer des pièces uniques, sans avoir à investir dans un moule coûteux.
Felix Hammerschmidt, HO Additive Manufacturing Satair, explique : « Nous nous sommes tournés vers l’équipe de fabrication additive pour trouver une solution. Après une courte pré-évaluation, la pièce a été remise aux bureaux d’études RapidSpares d’Airbus. Grâce à un nouveau processus de certification, ils ont pu recertifier l’ancienne pièce moulée en cinq semaines et l’adapter au titane, qui est un matériau qualifié pour la fabrication additive apte au vol. Le délai de certification devrait encore se réduire à l’avenir, une fois que la technologie sera devenue plus standard. »
Pendant la phase de fabrication, la pièce a été imprimée en 3D dans l’atelier de Reference Manufacturing d’Airbus Filton, qui avait été qualifié en 2019 et est maintenant capable de produire des pièces pour les avions. Le travail d’impression a duré environ 26 heures, les 4 pièces étant imprimées simultanément pour réduire le coût et le temps d’impression par pièce. Après l’impression, des étapes de post-traitement ont été nécessaires pour faire de la pièce une pièce de rechange capable de répondre aux mêmes exigences de sécurité que la pièce classique. La nouvelle pièce imprimée en 3D a été fournie avec un agrément de certification EASA Form 1.
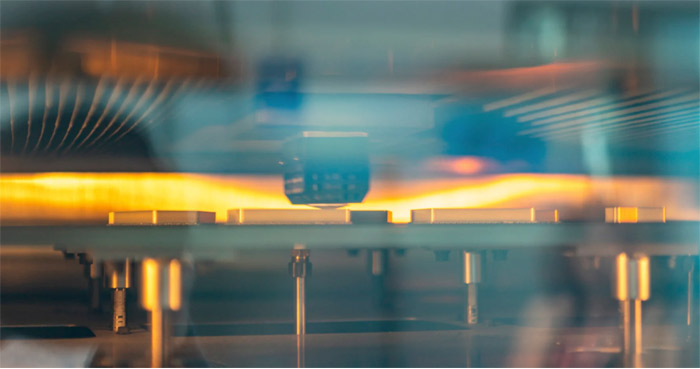
La fabrication additive permet à Satair de réduire coûts et délais de production (crédits photo : Satair)
Bart Reijnen, PDG de Satair, conclut : « Satair est à l’avant-garde de la fourniture de pièces imprimées en 3D pour le marché des pièces de rechange de l’aviation et nous avons actuellement plus de 300 numéros de pièces certifiés pour la technologie couvrant tous les types d’avions de la famille Airbus. […] Avec cette chaîne d’approvisionnement de la fabrication additive maintenant en place, nous serons en mesure de produire ces pièces dans un délai plus court. Quatre autres clients ont déjà demandé cette même pièce suite à cette livraison réussie. Nous avons déjà identifié d’autres pièces en titane pour lesquelles la fabrication additive pourrait devenir un moyen de production plus économique, avec une plus grande flexibilité et des délais plus courts. » Vous pouvez trouver plus d’informations ICI.
Que pensez-vous de cette pièce de rechange imprimée en 3D et certifiée pour l’aérospatiale ? Partagez votre avis dans les commentaires de l’article ou avec les membres du forum 3Dnatives. Retrouvez toutes nos vidéos sur notre chaîne YouTube ou suivez-nous sur Facebook ou Twitter !
L’article ne précise pas le procédé employé : laser, FE, …
C’est fondamental pour le titane.