Die besten 3D-gedruckten Fahrzeuge und Fahrzeugteile
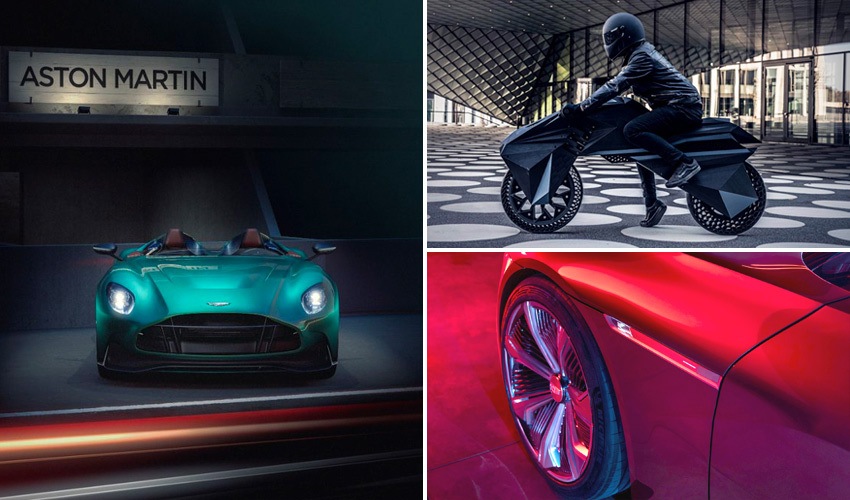
Wie Sie vielleicht schon festgestellt haben, wird die additive Fertigung im Automobilsektor immer beliebter, und viele Fahrzeuge werden heute teilweise oder ganz mit 3D-Technologien konstruiert. Von Autos, Motorrädern bis hin zu öffentlichen Verkehrsmitteln finden sich viele Anwendungsfälle, wofür es auch zahlreiche Gründe gibt. Der 3D-Druck ermöglicht es den Herstellern, die Produktionszeit zu verkürzen, Kosten zu senken und umweltfreundlichere und leichtere Fahrzeuge als traditionell hergestellte zu entwickeln. Um den Einsatz der Technologie in der Automobilindustrie bzw. im weiteren Sinne in der Transportindustrie hervorzuheben, hat 3Dnatives eine Liste von Fahrzeugen erstellt, die ganz oder teilweise im 3D-Druckverfahren hergestellt wurden.
Aston Martin DBR22
Der britische Automobilhersteller Aston Martin, einer der bekanntesten Luxusautofirmen der Welt, hat vor kurzem die additive Fertigung für ein Fahrzeugdesign eingesetzt. Mit dem Modell DBR22, ein Zweisitzer, wird das10-jährige Bestehen der Sonderanfertigungsabteilung des Unternehmens names Q gefeiert. Das Auto verfügt über einen 3D-gedruckten hinteren Hilfsrahmen, dessen Aluminiumteilen zu einem fertigen Hilfsrahmen zusammengefügt werden. Durch den Einsatz dieser Technologie konnte das Unternehmen Gewicht einsparen ohne die Stabilität zu beeinträchtigen. Das fertige Auto wurde auf dem Peeble Beach Concours d’Elegance in Kalifornien vorgestellt, einer der renommiertesten Automobilveranstaltungen der Welt. Mit dem Modell DBR22 und den additiven Fertigungstechnologien schuf das Unternehmen einen ikonischen und innovativen Sportwagen.
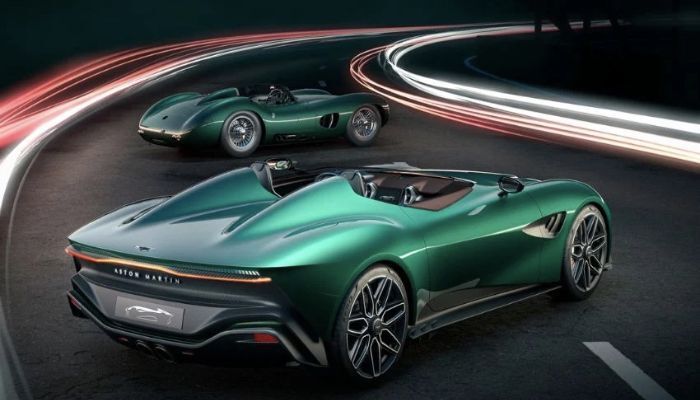
Bild: Aston Martin
Der Porsche GT2RS
Der Automobilhersteller Porsche setzt seit mehreren Jahren additive Fertigungsverfahren für verschiedene Anwendungen ein, die vom Prototyping bis zur Herstellung von Fertigteilen reichen. Wir wollten eines seiner neuesten Projekte im Zusammenhang mit dem Motor hervorheben: Es handelt sich um 3D-gedruckte Kolben für das Vorzeigemodell 911, den GT2 RS. In Zusammenarbeit mit Trumpf und Mahle konnte das deutsche Unternehmen um 10 % leichtere Kolben herstellen und die Kühlkanäle in die Krone integrieren – ein Design, das über subtraktive Fertigungsmethoden nicht möglich gewesen wäre. Diese Gewichtsreduzierung ermöglicht es Porsche, die thermische Belastung der Kolben zu verringern und die Verbrennung zu optimieren, was zu einem höheren Wirkungsgrad führt. Sechs 3D-gedruckte Kolben wurden in einen Motor eingebaut und über 200 Stunden lang erfolgreich getestet.
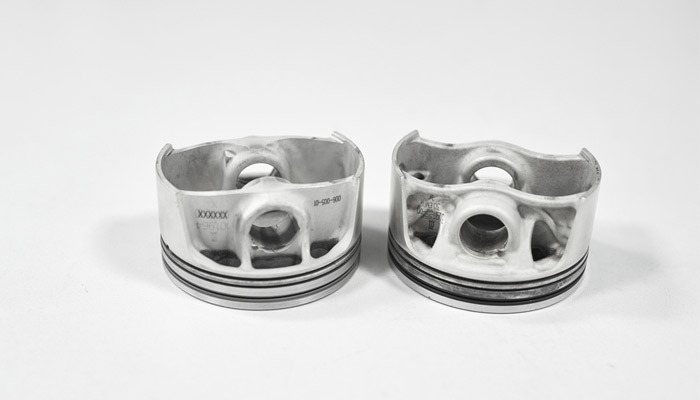
Bild: Porsche
Der Ford Maverick Pickup
Wenn wir an amerikanische Automobilhersteller denken, fällt uns als erstes Ford ein, einer der ersten Hersteller, der Autos in Massenproduktion am Fließband herstellte. Vor allem mit seinem Ford Maverick® Pickup ist das Unternehmen, mehr als 100 Jahre später, immer noch ein Vorreiter. Das Fahrzeug wurde so konzipiert, dass Käufer dank des Ford Integrated Tether Systems (FITS) ihrer Kreativität freien Lauf lassen können. Hierfür gibt es eine Reihe von Steckplätzen an der Rückseite der Mittelkonsole und Ablagefächer unter den Sitzen, die die individuelle Anpassung von Zubehör, insbesondere mit einem eigenen 3D-Drucker, ermöglichen. Im Wesentlichen dienen die Steckplätze als Aufnahme für passende Halterungen für jedes beliebige Zubehör. Dank der frei zugänglichen 3D-Dateien kann der Kunde sich jegliche Wünsche sogar selbst erfüllen.

Ford ermöglicht es Nutzern, das Zubehör ihres Maverick® Pickup-Trucks dank FITS individuell zu gestalten (Bild: Ford)
Der Jeep und Campsite Carbon
Wenn die Rede von bekannten Unternehmen in der Automobilbranche ist, darf Jeep nicht vergessen werden. Die treuen Kunden der Marke dürfen sich glücklich schätzen, dass die additive Fertigung für den unverwechselbaren Jeep Wrangler genutzt wird. Das Unternehmen Campsite Carbon nutzt nämlich den 3D-Druck von Kohlenstofffasern, um innovative Teile für den Außen-, Innenraum und die Motorhaube der JL- und JK-Wrangler sowie des JT Gladiator herzustellen. Obwohl diese Produkte direkt bei Campsite Carbon gekauft werden müssen, scheinen sie bei den Nutzern bereits sehr beliebt zu sein. Insbesondere die einfach zu installierenden konvexen Spiegel, die auch bei geöffneten Türen am Auto angebracht werden können sind populär.
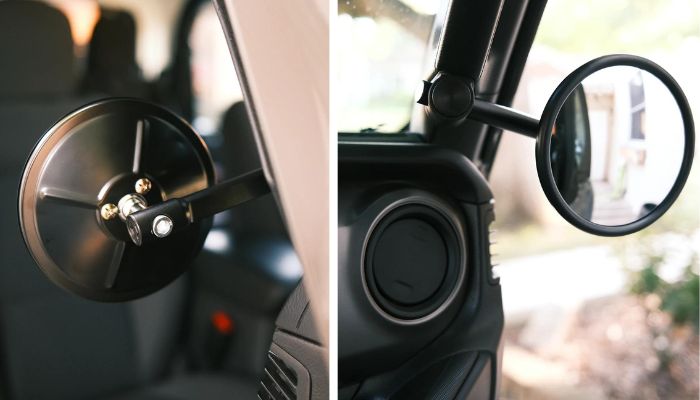
Campsite Carbon bietet eine Reihe von 3D-gedruckten Teilen für Jeeps an, darunter diese Spiegel (Bild: Campsite Carbon)
Der Peugeot 308
Der französische Automobilhersteller Peugeot beschäftigt sich schon seit mehreren Jahren mit der additiven Fertigung im Zusammenhang seiner Fahrzeuge. So findet diese Technologie nun auch Anwendung in dem neuen Peugeot 308, wobei in diesem Fall der 3D-Druck nicht zum Einsatz für Bauteile, sondern für das nötige Autozubehör verwendet wurde. Für die Herstellung von beispielsweise Dosenhaltern, Sonnenbrillenhaltern oder auch Telefon/-Kartenhaltern wurde in gemeinsamer Zusammenarbeit mit HP Inc., Mäder und ERPRO das Ziel verfolgt, den Peugeot 308 mit innovativen Produkten auszustatten. Davon aber noch nicht genug, denn diese sollten sich nämlich angenehm anfühlen, solide und leicht zu bedienen sein, sodass sich der Wohlfühlfaktor im Innenraum erhöht. Verwendet wurde hierbei mittels HP Multi Jet Fusion Technologie, wobei man als Material auf ein flexibles Polymer setzte.
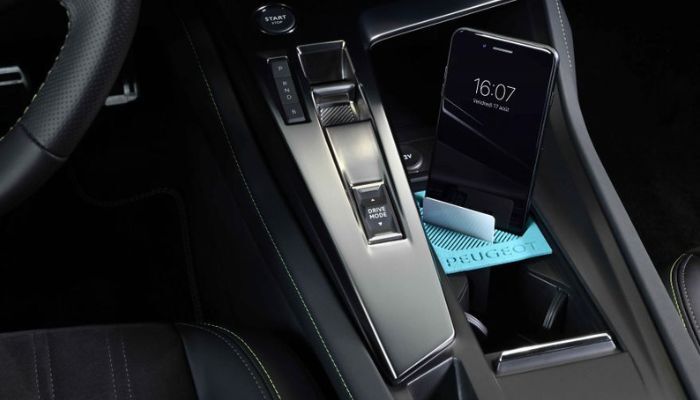
Bild: Peugeot
Der Cadillac Celestiq
Schon in der Vergangenheit glänzte GM mit seinem Aufgebot an additiver Fertigung, denn in gerade einmal fünf Wochen druckten sie 60.000 Teile. Dieses AM-Können spiegelt sich ebenfalls in ihrem Cadillac Celestiq wider, für dessen Bau man von Seiten GM rund 81 Millionen Dollar investierte. Dieses Fahrzeug, welches aufgrund seines Designs, der verwendeten Technologie und seiner Leistung dem Ultra-Luxusbereich zugeordnet werden kann, soll laut Angaben des Herstellers mehr 3D-gedruckte Bauteile enthalten, als jedes andere von GM produzierte Fahrzeug zuvor. Diese mehr als 100 verbauten und 3D-gedruckten Teile werden sowohl aus Polymer, als auch aus Metall gefertigt und finden sich in strukturellen und kosmetischen Teilen wider. Um welche Teile es sich hierbei konkret handelt, darüber gibt der Hersteller keine Angaben.
Der Toyota GR86 und Stratasys
Seit Juni 2022 hat Stratasys, ein führendes Unternehmen im Bereich 3D-Polymerdruck, eine Kooperationsvereinbarung mit Toyota Racing Development (TRD). Für den amerikanischen GR-Cup-Wettbewerb werden Stratasys-Maschinen zur Herstellung von Teilen für den neuen Toyota GR86 hergestellt. TRD hat Stratasys Fortus® 450mc, F370 und F370®CR 3D-Drucker in seinen Werken in Salisbury, N.C., und Costa Mesa, Kalifornien, integriert, um Teile für den Endverbrauch zu drucken. Intern wird ein Motorhauben-Lufteinlass aus FDM® Nylon 12CF für das Auto gedruckt. Eine GR86-Klammer wird hingegen von Stratasys Direct mit dem Stratasys H350™ 3D-Drucker gedruckt, der mit SAF™-Technologie betrieben wird und nachhaltiges Stratasys High Yield PA11-Material verwendet. Zudem wird es möglich sein den Innenraum des Fahrzeugs mit 3D-gedruckten Teilen individuell zu gestalten.
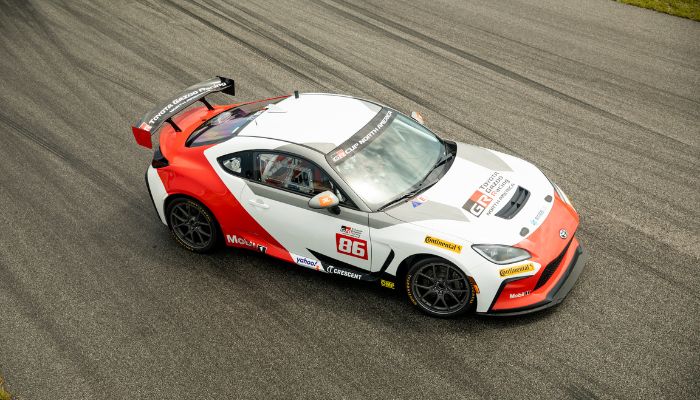
Bild: Toyota
Der BigRep NERA
Das in Deutschland beheimatete Unternehmen BigRep hat NERA entwickelt, ein Elektromotorrad, das mithilfe des 3D-Drucks hergestellt wurde. Der Prototyp mit dem Namen NERA (New-Era) wurde im Innovationslabor NOWlab des Unternehmens konzipiert. Laut Daniel Büning, dem Geschäftsführer von NOWlab, erweitert das Motorrad die Grenzen der Kreativität in der Technik. Tatsächlich verfügt es über erstaunliche Eigenschaften wie luftlose Reifen, einen flexiblen Stoßfänger und ein futuristisches Design. Mit Ausnahme der elektronischen Komponenten wurden alle Teile der Nera mit BigRep’s FDM-Technologie in 3D gedruckt. Für das Design des Motorrads wurden PLA, Pro FLEX, ein flexibles Material auf TPU-Basis, und das ProHT-Filament, das hohe Temperaturen aushalten kann, verwendet.
Divergent 3D und der Blade
2015 stellte Divergent, ein junges kalifornisches Unternehmen, Blade vor, ein Konzeptfahrzeug, bei dem 3D-gedruckte Teile im Fahrgestell integriert sind. Später ging das Unternehmen eine Partnerschaft mit Peugeot ein, um Produktionskapazitäten mithilfe der additiven Fertigung zu verbessern. Im Laufe der Jahre hat das Unternehmen die Anzahl an 3D-gedruckten Teilen erhöht, wovon auch das Blade-Auto profitiert hat. Alle Komponenten des Autos werden mittlerweile mithilfe der 3D-Drucktechnologie entworfen. Zusätzlich hat Divergent eine Software und ein automatisiertes Montagesystem zur Entwicklung von den Teilen konzipiert. Um die Produktion des Automodells fortzusetzen und internationalen Fertigungskapazitäten zu erweitern, wurden bis 2022 vom Unternehmen 160 Millionen US-Dollar aufgebracht. Darüber hinaus gründete Kevin Czinger, der Gründer von Divergent Technologies, das Unternehmen Czinger, das im Jahr 2022 sein erstes Serienfahrzeug, den 21C, ein weiteres 3D-gedrucktes Fahrzeug, nämlich das Hypercar, vorstellte.
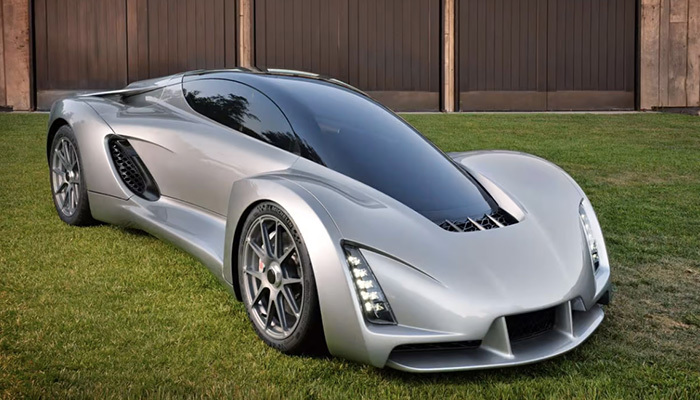
Bild: Divergent
Der BMW iX5 Hydrogen
Zahlreiche Teile des BMW iX5 Hydrogen werden klimafreundlich mithilfe von additiver Fertigung im Additive Manufacturing Campus in Bayern produziert. Um welche Teile es sich dabei genau handelt ist unbekannt. Zudem machen die Hochleistungsbrennstoffzelle und die optimierte Energiebatterie des Antriebssystems das Fahrzeug weltweit einzigartig. Das moderne Sports Activity Vehicle (SAV) der Luxusklasse verbindet bahnbrechende Antriebstechnologie mit den kraftvollen Proportionen und der Vielseitigkeit eines BMW X Modells. Das Auto erreicht durch die Umsetzung von Wasserstoff in Elektrizität eine Leistung von bis zu 125 kW/170 PS. Dadurch ist es möglich, über längere Strecken konstant hohe Geschwindigkeiten zu halten. Bezüglich Emissionen entsteht lediglich Wasserdampf. Zudem wird während Schub- und Bremsvorgängen Energie in einer Strombatterie gespeichert. Infolge der gespeicherten Energie kann eine Systemleistung von 275 kW/374 PS erreicht werden. Attraktiv ist dies für besonders sportliche Fahrmanöver, die charakteristisch für die Marke sind.
Das Motorrad Jane
Das französische Unternehmen Viba ist definitiv Fan der additiven Fertigung: Es nutzt die Technologie für die Herstellung einiger Komponenten seiner innovativen Motorräder. Das Modell Jane ist mit einem 3D-gedruckten Aluminiumtank ausgestattet. Das Teil wurde auf einer Laserfusionsmaschine entworfen, und zwar auf einer der Maschinen von SLM Solutions. Seine Wabenstruktur reduziert das Gesamtgewicht des Bauteils bei ausreichender Steifigkeit. Das Viba-Motorrad ist außerdem mit einem 3D-gedruckten vorderen Kotflügel und einem Pakethalter ausgestattet.
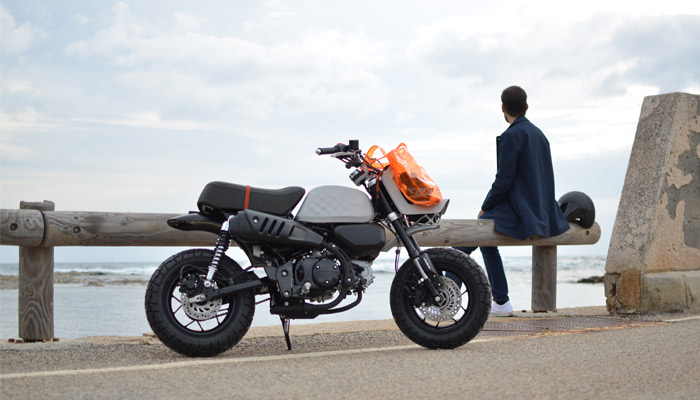
Bild: Viba
Ducati und seine Sportmotorräder
Für die MotoGP-Saison 2022 setzt das Team Ducati Corse bei der Herstellung seiner Sportmotorräder auf die additive Fertigung. Das italienische Unternehmen, das zum Volkswagen-Konzern gehört, arbeitete dazu mit Roboze, ein weiterer italienischer Hersteller, der sich auf die Entwicklung von 3D-Druckern und Hochleistungsmaterialien spezialisiert. Konkret wurde die Technologie zur Herstellung von Teilen für die Motorradserie Desmosedici GP verwendet. Dank der Zusammenarbeit zwischen den beiden war es möglich, Teile aus Polymer statt aus Metall zu drucken. Zu diesen Bestandteilen gehören die Außenhaut und die Hitzeschilde. Die Integration der additiven Fertigung durch eine so renommierte Marke verdeutlicht die Entwicklung in der Welt der MotoGP.
Welches dieser 3D-gedruckten Fahrzeuge würden Sie gerne fahren wollen? Lassen Sie uns zu diesem Thema gerne einen Kommentar da oder teilen Sie es uns auf Facebook, Twitter, LinkedIN oder Xing mit. Möchten Sie außerdem eine Zusammenfassung der wichtigsten Neuigkeiten im 3D-Druck und der additiven Fertigung direkt und bequem in Ihr Postfach erhalten? Dann registrieren Sie sich jetzt für unseren wöchentlichen Newsletter!