Schneider Electric exploite les avantages de l’impression 3D DLP pour créer des pièces de rechange

Schneider Electric est une entreprise européenne fondée en 1836, présente dans le monde entier. Elle est engagée dans le développement et la fabrication de disjoncteurs à air, entre autres. Ils ont récemment intégré la fabrication additive dans leur activité afin de palier le manque de stock dans la chaîne d’approvisionnement, notamment pour produire des pièces de rechange et de l’outillage. Au sein du département de gestion des installations, ils ont décidé d’adopter l’imprimante 3D Shape 1 développée par la société RAYSHAPE ; celle-ci leur permet de fabriquer ces pièces plus rapidement et à moindre coût. Depuis plus de 5 mois, Schneider profite de tous les avantages offerts par ce procédé d’impression 3D résine.
Dans l’industrie manufacturière, les pièces de rechange ne sont pas des articles produits en grande série, de sorte que toute rupture dans la chaîne d’approvisionnement peut affecter l’ensemble de l’industrie à grande échelle. C’est là qu’intervient l’impression 3D, qui est un système beaucoup plus rapide et moins coûteux pour produire des pièces uniques ou de petites séries par rapport aux autres méthodes de fabrication traditionnelles. De plus, le développement de nouveaux matériaux avancés permet de relever certains défis et favorisent l’adoption de la technologie. Ce dernier point était particulièrement important pour Schneider, car la plupart de ses applications nécessitent des matériaux très résistants, mais avec une précision dimensionnelle adéquate. Pour y répondre, ils se sont tournés vers le fabricant chinois RAYSHAPE, qui se consacre au développement de solutions professionnelles d’impression 3D DLP, notamment des machines, des matériaux et des solutions de post-traitement.
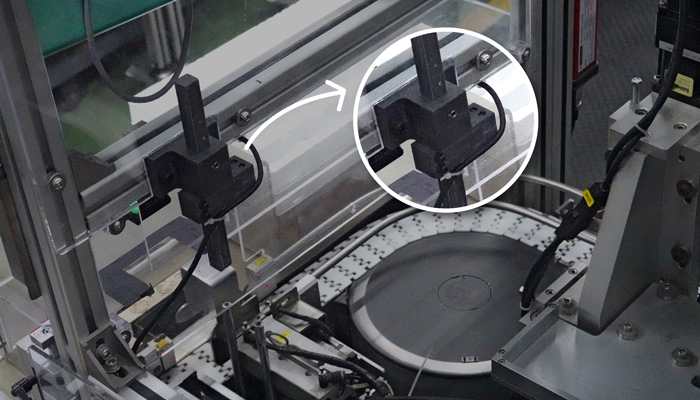
Schneider Electric a intégré l’imprimante 3D Shape 1 de RAYSHAPE dans ses activités (crédits photo : RAYSHAPE)
Les avantages de l’adoption d’imprimante Shape 1 de RAYSHAPE
En intégrant la fabrication additive résine à son activité, Schneider a réduit le temps de la chaîne de collaboration, qui exige que les ingénieurs, les fournisseurs et les responsables des achats créent la pièce finale. Grâce à l’imprimante 3D Shape 1 de RAYSHAPE, les ingénieurs ont pu résoudre certains de leurs défis en concevant et en imprimant en 3D les pièces de rechange. Contrairement à l’usinage CNC, qui est une méthode qui demande plus d’efforts et de temps, l’impression 3D est une technologie qui leur permet d’apporter des solutions le jour même. De plus, l’un des grands avantages de cette technologie est qu’elle peut fabriquer des pièces en une seule fois, sans passer par des étapes d’assemblage, le tout en dehors des heures de travail.
La Shape 1 est une imprimante 3D de bureau capable d’imprimer à des vitesses allant jusqu’à 50 mm/heure avec une grande précision, ce qui signifie que plusieurs outils d’une hauteur de 10 cm pourraient être créés dans le même laps de temps. Avec un volume d’impression de 192 × 108 × 300 mm, la machine a permis de produire plusieurs pièces imprimées en 3D en trois heures environ. Pour répondre aux exigences en termes de matériaux, RAYSHAPE a recommandé à Schneider d’utiliser la résine Pro 10. Ce photopolymère présente une dureté Shore de 86D et des performances mécaniques équilibrées en termes de résistance élevée à la traction, à la flexion, un faible taux de déformation et un faible fluage.
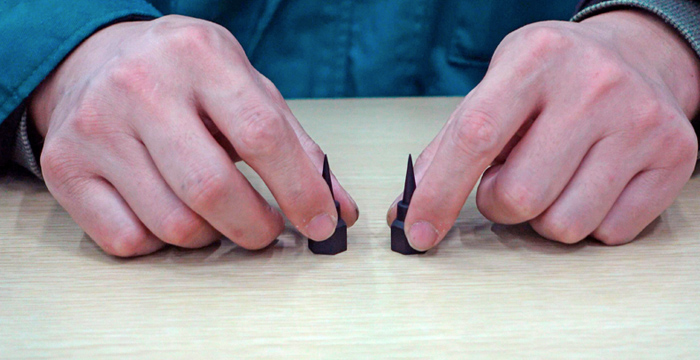
L’impression 3D DLP permet de concevoir des pièces détachées plus rapidement et à moindre coût (crédits photo : RAYSHAPE)
L’avantage concurrentiel de la fabrication additive a permis aux ingénieurs de mieux maîtriser les processus. L’entreprise devient plus efficace, capable de traiter des défis en profondeur et en nuance. Le rythme des lignes de production devient plus gérable, les problèmes ne sont plus urgents et peuvent être résolus plus efficacement. En termes d’investissement, l’équipe de Schneider Wuhan affirme avoir imprimé en 3D plus de 110 pièces en cinq mois, ce qui lui a permis de réduire les coûts de 80 % et de produire deux fois plus qu’avec d’autres méthodes. Ce résultat est très positif par rapport à l’usinage CNC. Avec l’impression 3D, ils ont pu rentabiliser leur machine dès la création de la 100e pièce. Si vous voulez en savoir plus sur la façon dont la technologie de RAYSHAPE a permis d’accélérer les processus de production de Schneider, rendez-vous sur leur site ICI.
Que pensez-vous de l’utilisation de la technologie de RAYSHAPE par Schneider Electric ? N’hésitez pas à nous dire ce que vous pensez dans les commentaires de l’article. Retrouvez toutes nos vidéos sur notre chaîne YouTube ou suivez-nous sur Facebook ou Twitter !
*Crédits photo de couverture : RAYSHAPE