SKOP, le premier stéthoscope connecté imprimé en 3D
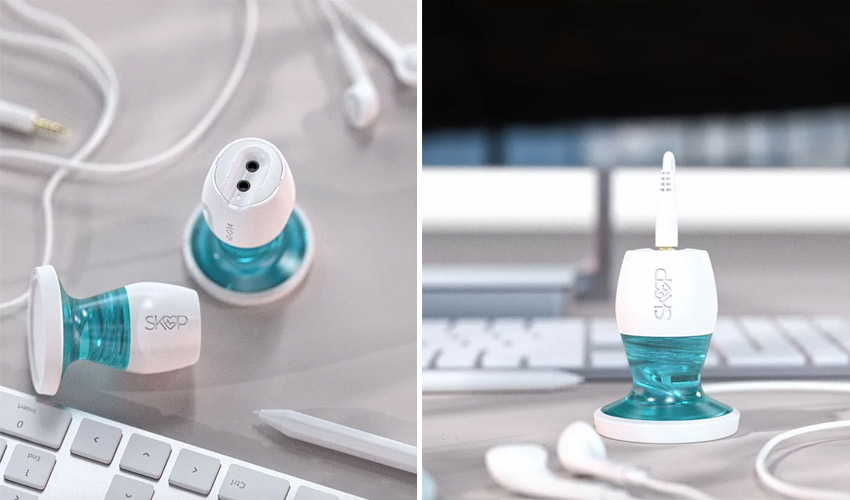
Les technologies 3D ont ces derniers temps prouvé leur efficacité et rapidité dans le secteur médical, permettant à de nombreux projets de voir le jour pendant la crise de la COVID-19. Face à la pénurie de certains équipements et dispositifs médicaux, makers, fabricants, services et acteurs du secteur de l’impression 3D se sont mobilisés pour imprimer en 3D des respirateurs, des visières de protection, des écouvillons et dispositifs connectés pour faciliter les téléconsultations médicales. C’est en tout cas sur ce créneau que s’est développée WeMed, une jeune pousse française fondée il y a quelques mois dans ce contexte de crise. Portée notamment par Cyrille Lecroq, elle est derrière le Skop, un stéthoscope connecté imprimé en 3D, réalisé en collaboration avec plusieurs acteurs du secteur dont l’entreprise française F3DF et Formlabs.
La téléconsultation est pratiquée depuis quelques années en France déjà, visant à mieux organiser notre système de santé mais également à favoriser l’accès aux soins – par exemple dans des zones où les médecins sont moins nombreux. La crise sanitaire a fait exploser le nombre de téléconsultations – 500 000 réalisées en une semaine seulement lors du premier confinement en mars dernier. Ce modèle a rapidement montré des faiblesses, notamment en termes d’outils et d’équipements médicaux disponibles chez soi, que ce soit en termes de praticité ou de coûts. C’est face à ce constat que Cyrille Lecroq décide de développer un stéthoscope connecté abordable qui permettrait au patient de s’examiner chez lui et au médecin de recevoir le signal sonore directement à son cabinet en temps réel afin qu’il puisse faire son diagnostic. Afin d’obtenir rapidement un produit satisfaisant, il se tourne vers les technologies 3D, ayant déjà quelques connaissances en impression 3D.
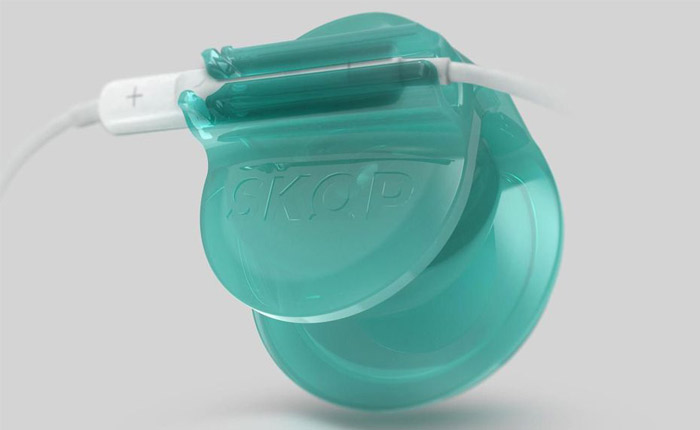
L’une des premières versions du SKOP (crédits photo : WeMed)
Il explique : « En 2017, j’ai suivi une formation avec F3DF, deux pour être plus précis : une sur la fabrication additive et une autre sur les outils Autodesk et plus particulièrement Fusion 360. A l’époque, l’impression 3D représentait pour moi un intérêt particulier pour le prototypage mécanique. Quelques années après, pendant le premier confinement, j’ai mis à profit les connaissances acquises pour développer cette idée de stéthoscope connecté. L’impression 3D était ce que j’avais sous la main et je savais qu’elle me permettrait de prototyper rapidement le projet que j’avais en tête. »
De l’idée à l’objet, le défi de la modélisation
Après plusieurs échanges avec les équipes F3DF qui ont su conseiller Cyrille dans le choix de la technologie, des matériaux mais aussi des prestataires et acteurs du secteur, le projet Skop commence à émerger. L’objectif était de concevoir un stéthoscope en plastique pour faire baisser son prix. Aujourd’hui, la plupart des solutions sont en métal car la densité des alliages métalliques permet de mieux conduire le son du stéthoscope. Or le plastique étant moins dense, il fallait trouver une solution adaptée. Cyrille a donc imaginé une sorte de cône pour conduire ce son, une alternative qui marchait mais qui était peu pratique car ce cône mesurait 20 cm. C’est en s’inspirant de la forme de la cochlée, cet organe en forme d’escargot qui se situe dans l’oreille humaine, qu’il a pu réduire la taille de l’outil et optimiser sa forme. Et c’est là que l’impression 3D prend tout son sens : elle permet de réaliser des formes complexes grâce à des outils de modélisation et des techniques d’optimisation. Ce design n’aurait pas pu être conçu via des méthodes de fabrication traditionnelle et rapidement, Cyrille opte pour l’impression 3D.
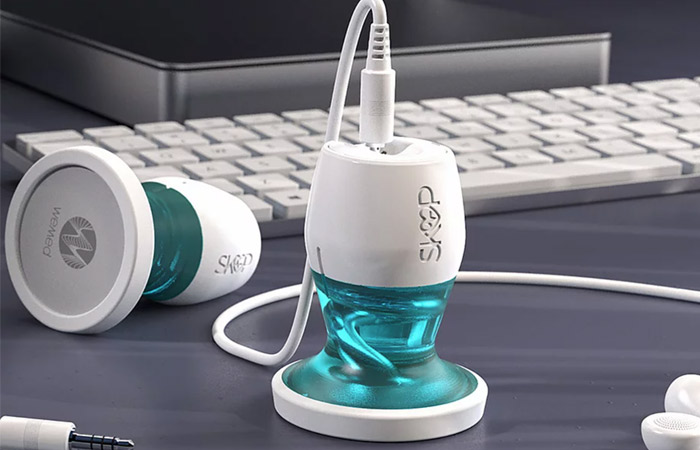
Le SKOP est connectable à un smartphone, une tablette ou un ordinateur pour une écoute à distance (crédits photo : WeMed)
SKOP, un produit complexe développé par fabrication additive
Le stéthoscope Skop est composé de trois parties : le main qui vient conduire le son, le middle à savoir la tête qui comprend un circuit intégré et enfin la membrane. Ce sont les deux premières qui sont imprimées en 3D. Rapidement, Cyrille a fait le choix de la photopolymérisation car il fallait produire une pièce très claire, sans stries et avec des couches très fines. Il s’est tourné vers les solutions de Formlabs pour toute la partie prototypage. Il explique : « Les machines Formlabs sont abordables et proposent des qualités de surface très satisfaisantes. De plus, dès le début, les équipes ont été très investies dans le projet et nous ont accompagnés sur toute la partie prototypage et préparation à l’industrialisation. » Formlabs a par exemple fourni 7 litres de LT Clear Resin afin que Cyrille puisse mettre au point son projet. Au total, c’est plus de 100 itérations qui ont été imprimées en 3D avant de trouver le bon produit.
La fabrication additive n’aura pas uniquement servi à cette étape de prototypage : WeMed va continuer avec cette méthode de production – la photopolymérisation en l’occurrence – tout simplement parce que le stéthoscope est composé d’éléments qui sont impossibles à fabriquer autrement de par leurs formes géométriques. La startup s’est d’ailleurs fixée comme objectif la production de 60 000 pièces par mois. Cyrille Lecroq conclut : « Skop est un projet qui montre tout le potentiel de la fabrication additive mais aussi l’importance de s’entourer des bonnes personnes. Les équipes F3DF ont largement contribué à la réussite du projet, mais aussi celles de Third. Ce sont des éléments rassurants de savoir qu’on peut s’appuyer sur leur expertise, l’apport de leurs connaissances et ce, de manière continue. »
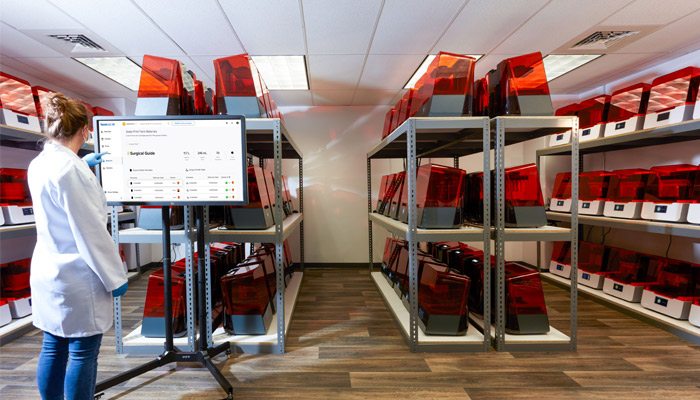
Formlabs a fourni 7 litres de résine afin d’aider Cyrille Lecroq dans le développement du SKOP (crédits photo : Formlabs)
WeMed pense déjà à la suite et veut développer un spiromètre connecté. Reste à savoir si elle s’appuiera sur l’impression 3D pour le concevoir. En tout cas, si vous souhaitez obtenir une formation à l’impression 3D dans le secteur médical, n’hésitez pas à contacter les équipes de F3DF qui sauront vous accompagner dans votre projet ! Et pour en apprendre plus sur WeMed, le Skop, et la conception produit, F3DF organise un Live Classroom gratuit en compagnie de Cyrille Lecroq.
Que pensez-vous du stéthoscope SKOP ? N’hésitez pas à partager votre avis dans les commentaires de l’article ou avec les membres du forum 3Dnatives. Retrouvez toutes nos vidéos sur notre chaîne YouTube ou suivez-nous sur Facebook ou Twitter !