Framatome installe un composant de combustible imprimé en 3D dans une centrale nucléaire
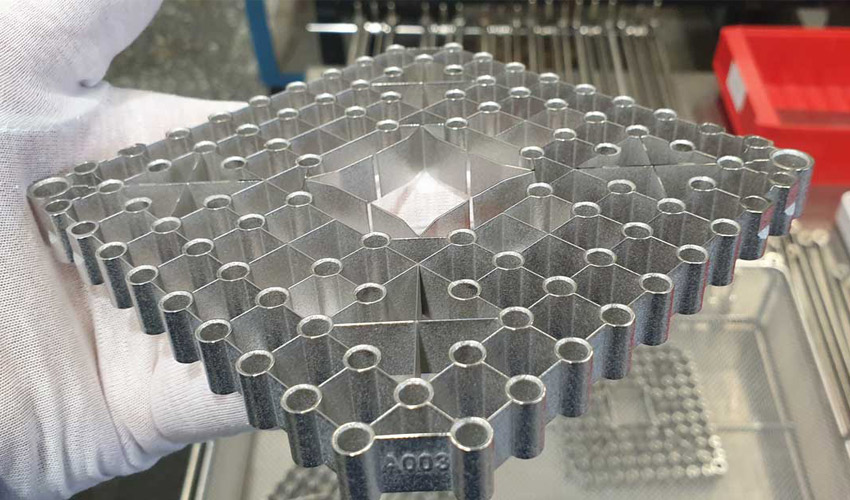
Fondée en 1958, Framatome est une multinationale française spécialisée dans le secteur nucléaire qui a commencé à utiliser les technologies 3D en 2015. Elle a récemment annoncé le développement d’un premier composant d’assemblage de combustible imprimé en 3D en acier inoxydable. Il s’agit de grilles d’extrémités supérieures d’assemblage conçues dans une centrale nucléaire en Suède exploitée par l’entreprise suédoise Vattenfall. Elles ont été installées avec succès dans la centrale, dans le cadre d’un programme d’irradiation pluriannuel.
La semaine dernière, nous vous avions présenté les possibilités qu’offre la fabrication additive dans le domaine de l’oil & gas, capable aujourd’hui de produire des pièces aux géométries complexes afin d’améliorer les performances des solutions du marché. C’est une méthode de production plus rentable, efficace et qui permet de créer des composants en une seule fois, sans passer par des étapes d’assemblage souvent fastidieuses et chères. La fabrication additive permet aussi de garantir la sécurité des procédés et du personnel opérant sur site, un point clé dans l’industrie.
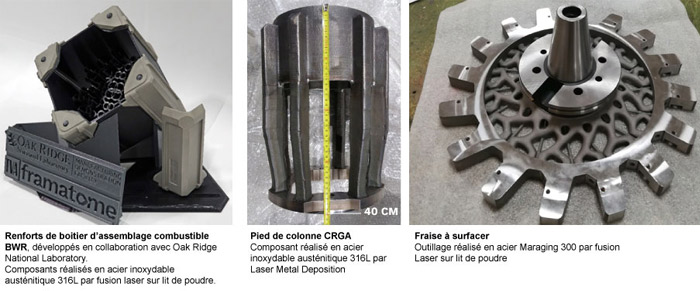
Différentes pièces imprimées en 3D par Framatome (crédits photo : Framatome)
C’est une première pour Framatome qui réussit l’installation d’une première pièce imprimée en 3D métal dans une centrale. Il s’agit donc d’une grille d’extrémité supérieure qui vient maintenir les crayons de combustible, ces tubes métalliques dans lesquels sont empilées des pastilles cylindriques de dioxyde d’uranium fritté. La grille sert également à empêcher les débris volumineux d’aller dans l’assemblage combustible. Lionel Gaiffe, senior executive vice president, Fuel Business Unit, à Framatome, ajoute : “Les avancées en matière d’intégrité des composants fabriqués par impression 3D sont révolutionnaires pour la génération d’une énergie sûre, fiable et bas-carbone, adaptée aux opérations à long terme. Nous apprécions la confiance de Vattenfall, qui nous a ouvert ses portes et offert un tremplin pour les innovations et développements futurs, qui viendront remplacer les procédés de fabrication conventionnels.”
Traditionnellement, le processus de fabrication de ces grilles comprend de multiples étapes et nécessite une surveillance élevée des opérateurs. En effet, elles sont faites à partir de plaquettes découpées et embouties puis soudées entre elle via un laser. En misant sur la fabrication additive, les équipes peuvent s’affranchir de ces étapes et imaginer des conceptions plus complexes pour apporter davantage de performances. Ella Ekeroth de Vattenfall Nuclear Fuel AB déclare :
Le fonctionnement des assemblages de combustible en toute sécurité est essentiel pour Vattenfall. En plus de ce principe de base, nos contributions au développement de procédés de fabrication efficaces et fiables sont dans l’intérêt de toute l’industrie nucléaire. L’objectif global de ces activités est de maintenir et d’améliorer davantage la sûreté et de permettre des opérations économiquement viables à long terme.
En attendant de découvrir les premiers résultats de ce composant imprimé en 3D et installé dans une centrale, vous pouvez retrouver le communiqué de presse officiel ICI.
Que pensez-vous de l’utilisation de la fabrication additive par Framatome ? Partagez votre avis dans les commentaires de l’article. Retrouvez toutes nos vidéos sur notre chaîne YouTube ou suivez-nous sur Facebook ou Twitter !
*Crédits photo de couverture : Framatome