Phase3D Detects Metal 3D Printing Errors
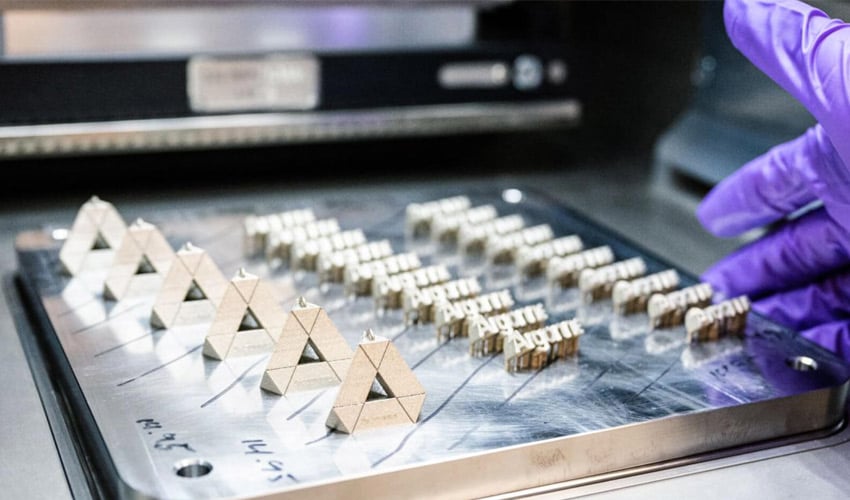
Phase3D, a startup previously known as Additive Monitoring Systems, has developed optical monitoring software specifically for metal additive manufacturing. In practical terms, this innovative solution can rapidly identify printing defects as they happen, helping to prevent any decrease in productivity or performance. At present, Phase3D is working alongside the Argonne National Laboratory, which is backed and overseen by the US Department of Energy. Together, they are exploring how metal 3D printing can contribute to the fight against global warming and the decarbonization of manufacturing processes. Additionally, they are conducting research into certification challenges that metal 3D printed parts may face, particularly in demanding fields like aeronautics and defense.
Regardless of which additive manufacturing process is employed, users may encounter printing errors that can significantly impact the final product’s quality, surface, properties, and performance. Fortunately, the ongoing development of technology has led to several solutions that can help overcome these challenges. In many cases, software tools are deployed either during the design phase or during the manufacturing process itself to monitor and correct any issues in real-time. One of these cutting-edge solutions is Phase3D. Leveraging structured light technology, this system can perform non-destructive evaluation on any 3D print, specifically targeting the metal additive manufacturing process.
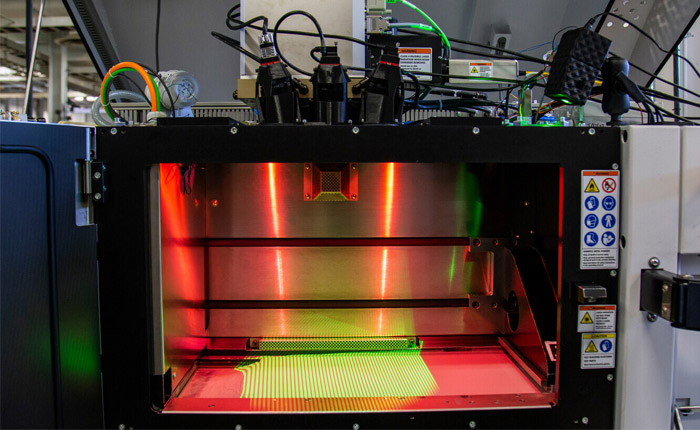
Phase3D’s solution installed on a 3D printer (Photo credits: Phase3D)
To put it simply, the structured light used by Phase3D measures the height of each deposited layer, allowing it to quickly detect any defects and halt production if necessary. The solution is currently compatible with powder bed fusion and powder binding processes, including ExOne machines and the EOS M290 printer. According to Dr. Niall O’Dowd, Founder and CEO of Phase3D, “In 3D printing, there can be up to tens of thousands of layers that can be as small as a fifth of the width of a human hair. Instead of using images or relative heat from the process to find defects, we created a reliable inspection system that inspects the height of the layers. As standards and regulations mature, it’s really important to have this kind of inspection data.”
Working closely with Xuan Zhang, Principal Materials Researcher at the Argonne National Laboratory, Phase3D is testing the effectiveness of its solution. Together, they deliberately introduce defects during the metal printing process while adhering to strict safety criteria. Through collaboration and rigorous testing, Phase3D aims to refine its technology and provide reliable, high-quality monitoring solutions for metal 3D printing.
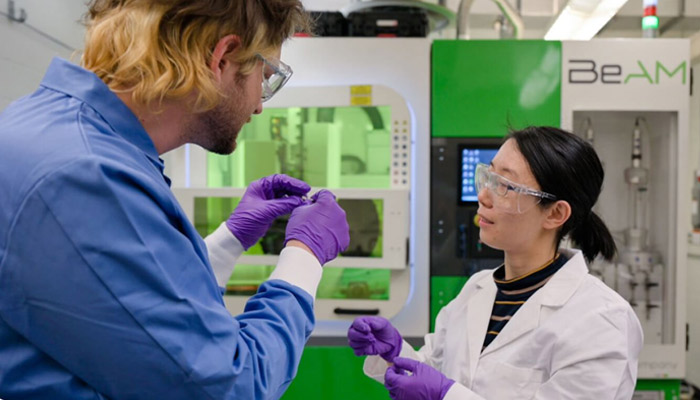
Dr. Niall O’Dowd and Xuan Zhang (Photo credits: Phase3D)
Dr. Niall O’Dowd concludes that “In a random build, sometimes we’re looking at a pore that is just tens of micrometers in size. Without post-build inspection, we don’t know if we are seeing fluctuations or anomalies. Instead, we deliberately introduce a defect that is anywhere from 20 to 200 microns, and then we test our technique.” The two partners are also working on the certification of the produced parts, but have not disclosed the method used. In any case, you can find more information HERE.
What do you think of Phase3D’s optical monitoring software? Let us know in a comment below or on our LinkedIn, Facebook, and Twitter pages! Don’t forget to sign up for our free weekly Newsletter here, the latest 3D printing news straight to your inbox! You can also find all our videos on our YouTube channel.
*Cover photo credits: Argonne National Laboratory