Xjet on its Safe, Eco-Friendly Process for Ceramic and Metal 3D Printed Parts
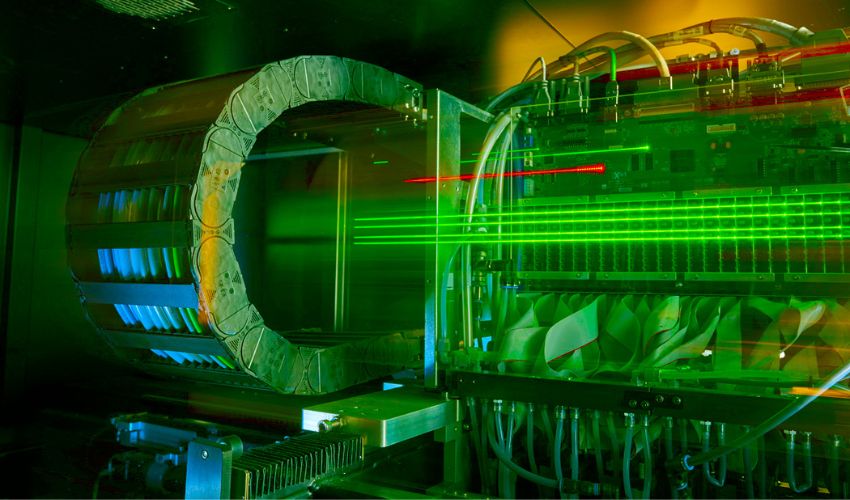
The rapidly-increasing commercialization in the 3D printing arena has already led to massive growth in specific verticals like ceramics and metal. A recent report suggested that the ceramic 3D printing market could reach 384 million USD by 2025. The metal market, which is considered one of the fastest growing in the AM sector, is expected to surpass $18B by 2032 for understandable reasons.
3D printing using the above materials enables the creation of complex parts with superior mechanical properties. NanoParticle Jetting™, the signature process of AM 3D printing leader XJet, is compatible with both ceramics and metals, offering an automated, safe, environmentally friendly path toward scale manufacturing of high-quality, geometrically complex parts. We spoke with the company’s CMO, Guy Zimmerman, to learn more about the technology, its benefits, and XJet’s unique approach.
3DN: Could you introduce yourself and Xjet?
My name is Guy Zimmerman. I joined Xjet recently as the CMO as the company gears up for growth. I have diverse experience, though most relevant is my background in global business including in the 3D printing sector. Meanwhile, Xjet is a 3D printer manufacturer that is addressing the most challenging segment in additive manufacturing, metals and ceramics. High quality, ready to use metal and ceramic parts that go into manufacturing and not into prototyping: that is the ambition using our own patented NanoParticle Jetting™ (NPJ) technology.
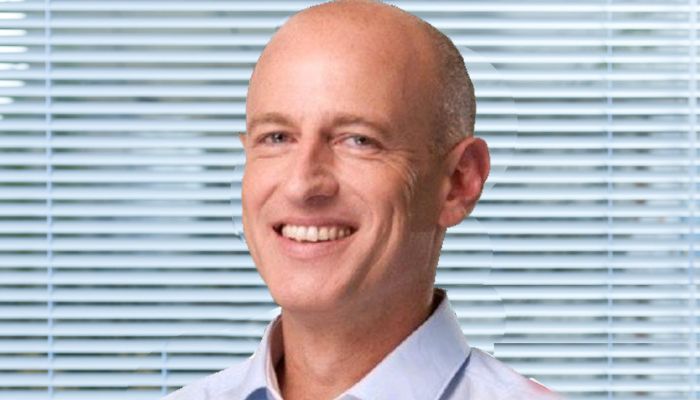
Guy Zimmerman
3DN: How does NPJ work? What are the benefits of using it?
NPJ delivers clean, automated manufacturing of high quality parts in metal and ceramics without involving powders, manual labor, or post processing . What enables this breakthrough is XJet’s unique additive manufacturing process based on nano-particles direct material jetting, which print high-resolution parts using the toughest materials in scale. In this process, the support materials and the main materials are both inks, not powders, a revolutionary approach in AM.
Let’s dive a little deeper into the printing procedure. We call it: Print-Wash-Sinter. The basic principle is using procurable material based on nanoparticles. With this, we are able to simultaneously print the material and the support, which is a very hard but soluble material. Once we complete the build, the support is washed away in water via an automatic process. The final sintering phase is done in a standard industry furnace, but in a significantly lower temperature than powder based solutions. This enables the highest complexity, accuracy and a level surface. It also removes design-related constraints. The technology and the use of thin nanoparticle layers and soluble support enable the creation of complex, accurate geometries, including internal components. This also allows for new design capabilities in a way that was considered impossible up until now.
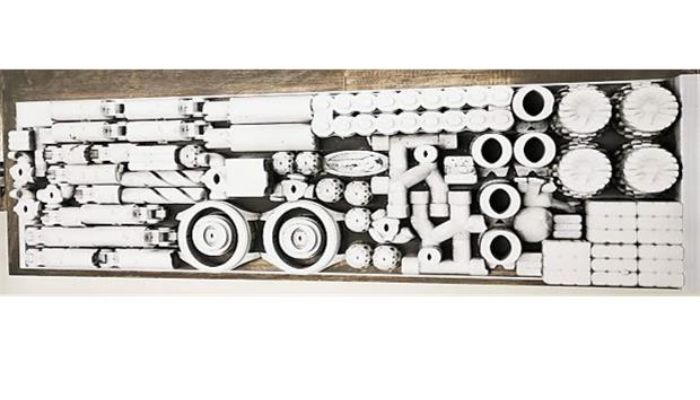
Xjet is capable of making a range of excellent solutions
The result is high-quality, highly accurate parts straight off the process. The printed parts do not require any additional processing or machining. Just like the XJet slogan, all you need to do is print, wash, and sinter.
Another advantage brought by nanoparticles has to do with the ability to print remarkably thin layers. The density level is significantly higher compared to other additive technologies, reaching highest levels of material purity, density and surface smoothness. This significantly improves the parts’ performance and reduces the sintering effect.
As you may know, the sintering process turns the particles into the actual material, which often results in significant shrinkage. With XJet’s technology, the process is done at a temperature lower than 200C, which saves time, boosts density, and reduces isotropic and overall shrinkage. Shrinkage remains the same along the x, y and z axes, resulting in no distortions in the final part. This proprietary and groundbreaking technology is packed in a high throughput manufacturing system. It is a digital, automated process instead of a manual, unsafe, polluting process that results in lower-quality parts.
3DN: What are the applications for Xjet’s solutions?
Together with our market leading customers we are targeting specific verticals and applications in all three industry domains: Industrial, Medical, and Consumer goods.
When it comes to ceramics, mostly Alumina and Zirconia, which offer very high resistance to heat, corrosion and electrical isolation, the freedom of design we bring to this market opens up opportunities in industrial applications (e.g. semiconductors manufacturing equipment parts, heat exchangers and electricity connectors, wave-guard antennas and electrical board parts).
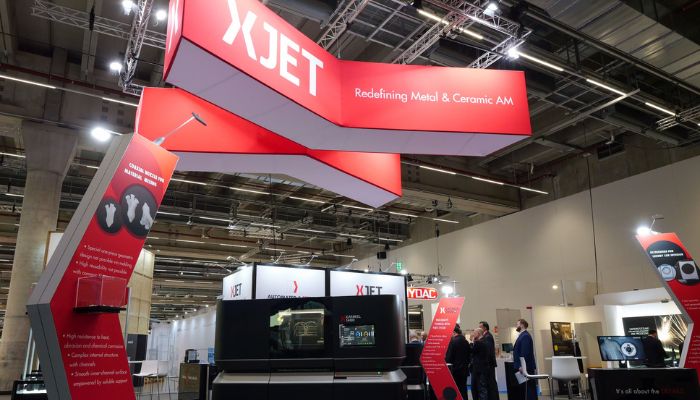
Xjet were present at Formnext 2022
Dental implants and crowns are another obvious vertical that we are getting into which is one of the growing medical markets today. In consumer goods we focus on high value wearables like high-end earbuds (which is an intriguing application, as the printed parts are very small, nonconductive, and customized to offer top acoustic qualities), and luxury watches.
We even make several ceramic parts in our high performance Carmel1400 system, so basically we print our own parts with our own machines. Metal is a more recent technology entering the market replacing traditional MIM (Metal Injection Molding) for short runs and high variety parts like surgical devices, hydraulic systems parts and many more.
We support a spectrum of unique applications that require a high quantity of parts, replacing several traditional technologies. The list includes MIM (metal injection Molding), CNC, and investment casting, a central technology with small parts that struggles whenever part production is under 20,000, making our technology a more economical choice.
3DN: Why did Xjet decide to launch a metal solution?
After we established the ceramics technology among market leaders and ceramic technical leaders, we finalized the development of the metal part of the portfolio with two leading stainless steel materials. Metal is a much larger and diversified market. Developing the metal solution was more challenging, but we’ve reached unprecedented performance levels, even better than ceramics. In early 2022, we introduced it to the market after going through a long evaluation process.
It is now available, and we showcased it at Formnext 2022 with testimonials from the technology’s leading beta users. Visitors learned how this metal solution competes with multiple powder-based technologies, offering clear advantages as an automated, clean metal process for use in a variety of sectors.
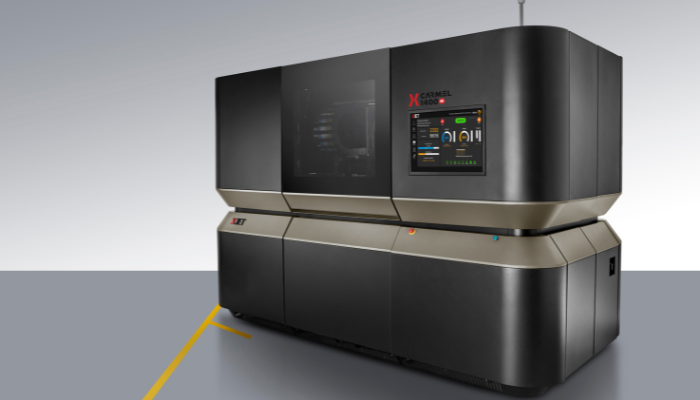
Xjet’s metal solution
The technology offers several benefits. First, we were able to develop soluble support materials that can work with the metal, a huge advantage for many users. Another is the high-quality surface level of the part, which is clear right out of the machine without demanding any additional processes. The third benefit is producing highly complex parts with accuracy, a massive advantage for many applications.
Just to illustrate this, we can print the wristband of a luxury watch from stainless steel as a whole. It might need a little bit of polishing, but that’s it. We are able to print so accurately that we can print the wristband bearings inside the part, no need to assemble it. NJP gives users the ability to print extremely accurate, high-performance parts in metal that are ready-to-use thanks to the unique capability of jet versus powder. We focus on users who want to create high-performance, accurate parts in various consumer-facing verticals.
3DN: Another aspect you are proud of is the sustainability of your process. How exactly is it environmentally friendly?
First of all, it is safe. The materials are safe, they come in closed bottles, and there are no toxic particles or free powder . It’s a safe process for those who operate it, which is not the case for many AM and traditional processes. Additionally, it uses exactly the amount of material needed for the part. It does not waste anything in a truly additive building process.
Our support material is soluble in water and can be safely drained. It contains some minerals, but is so safe it could pass as drinking water in some places. This is safer for humans but also the environment, since it almost eliminates waste disposal issues.
Last but not least, our sintering is also more eco-friendly compared to many other processes. It is typically the most energy-consuming part of the process, but because we conduct it at relatively low temperatures for a lower period, we save quite a lot of energy. These key factors make NJP one of the most environmentally friendly processes in metal and ceramics.
3DN: Any last words for our readers?
To summarize, NPJ technology offers three primary advantages. Nanoparticles in ink make it safer and more accurate, reaching higher density. The second benefit is rooted in the building process, printing the thinnest layers to achieve unbeatable unlimited complexities and true Design for Functionality. And the third is the green element. Our parts can be cleaned in water, leaving no residue.
The process itself consists of only three steps: print, wash, and sinter. Moving forward, we believe the technology will become a major part in the digital transformation of ceramic and metal, industrial, high-quality, complex parts manufacturing. You can learn more about XJet on our website HERE or check out the video below to understand how our technology works.
What do you think of Xjet? Let us know in a comment below or on our LinkedIn, Facebook, and Twitter pages! Don’t forget to sign up for our free weekly Newsletter here, the latest 3D printing news straight to your inbox! You can also find all our videos on our YouTube channel.
*All Photo Credits: Xjet