Titanio vs Aluminio: ¿qué metal escoger para la impresión 3D?
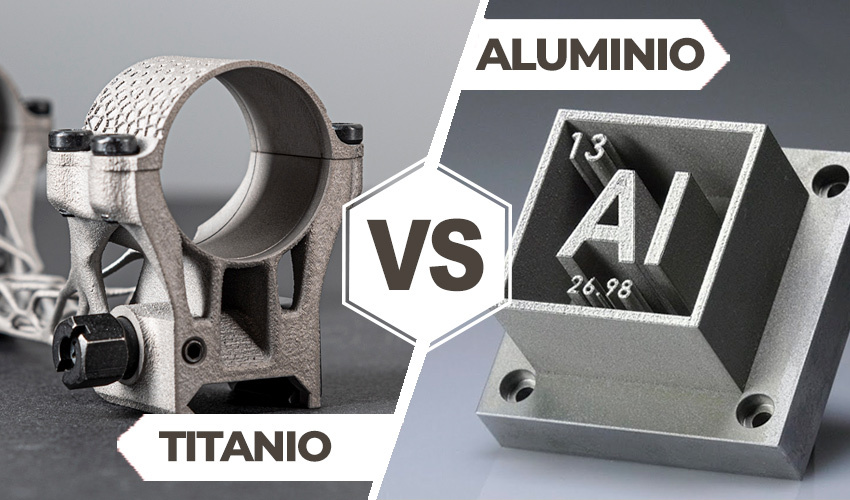
En la actualidad, el metal es uno de los tipos de materiales más demandados en los procesos de fabricación aditiva, junto con el plástico. Y no es para menos, ya que sus excelentes propiedades lo convierten en la opción ideal para las aplicaciones más exigentes en cuanto a rendimiento y resistencia. En este artículo, nos centraremos en dos de los principales metales utilizados en la impresión 3D: el titanio y el aluminio. Estos son utilizados, en la mayoría de los casos, para procesos como la fusión láser por lecho de polvo (L-PBF) o la deposición de energía directa (DED). Se encuentran disponibles principalmente en forma de polvo, enfocados para entornos industriales. Compararemos sus similitudes y diferencias, para profundizar en sus propiedades y aplicaciones, y comprender las ventajas que ofrecen en este proceso de fabricación.
Producción y características
Titanio
El titanio es un material metálico que en sí no se encuentra en la naturaleza como elemento, y debe extraerse de unos minerales que pueden ser rutilo (TiO2) o ilmenita (FeTiO3). La extracción del titanio puro es un proceso complejo que implica varias etapas. El método más utilizado para la producción de titanio puro es el Método Kroll, desarrollado por el químico estadounidense William J. Kroll en 1940. Este método implica la reducción del dióxido de titanio (TiO2) con gas de cloro (Cl2) para producir tetracloruro de titanio (TiCl4), que luego se reduce con magnesio (Mg) para producir titanio metálico. Aunque el Método Kroll es efectivo en la producción de titanio puro, es un proceso costoso que necesita una gran cantidad de energía. Por otra parte, la alta reactividad del titanio hace difícil su obtención como metal puro, por lo que una muestra de pureza 99,9% es catalogada como titanio comercialmente puro. Debido a esto, normalmente se utiliza combinado con otros elementos formando una aleación.
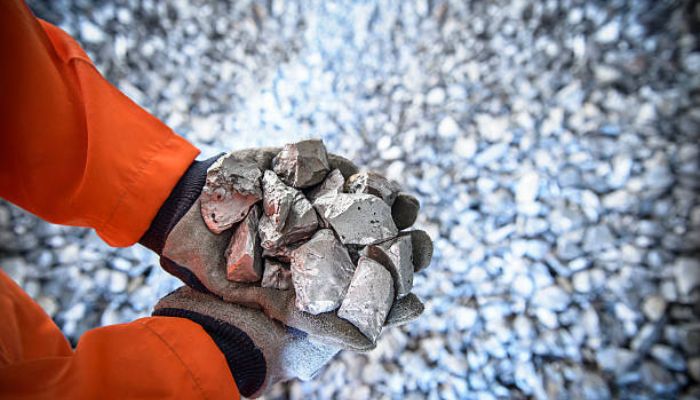
Créditos: Getty Images
El titanio tiene muchas propiedades que lo hacen súper versátil y útil en muchos sectores. Se suele utilizar en combinación con otros elementos para formar una aleación porque su alta reactividad dificulta su obtención como metal puro, pero el titanio puro extraído se utiliza en algunas aplicaciones, como en la industria médica gracias a su alta biocompatibilidad. Entre sus principales características destacan su alta resistencia mecánica, baja densidad, una excelente resistencia a la corrosión y rigidez.
La aleaciones de titanio más importantes y utilizadas en la impresión 3D son las siguientes:
- Titanio 6Al-4V, grado 5: es la más importante y común. Se utiliza en la impresión 3D por su gran resistencia y durabilidad. La aleación está hecha de titanio, aluminio y vanadio, y puede soportar temperaturas altas y ambientes corrosivos.
- Titanio 6Al-4V, grado 23: es biocompatible y por eso es normalmente utilizada en implantes y prótesis médicas.
- Titanio Beta 21S: tiene una resistencia mayor que las aleaciones de titanio convencionales y además es más resistente a la oxidación y a la deformación. Es perfecta para implantes ortopédicos y aplicaciones en motores aeroespaciales. El titanio beta se utiliza bastante en ortodoncia.
- Cp-Ti (titanio puro), grado 1, 2: se utiliza en la industria médica para una gran cantidad de aplicaciones debido a la biocompatibilidad del titanio con el cuerpo humano.
- TA15: es casi completamente de titanio, pero tiene un poco de aluminio y circonio añadido. Los componentes hechos con esta aleación son muy fuertes y resistentes a altas temperaturas, lo que los hace ideales para construir partes fuertes en aviones y motores. Además, son bastante ligeros en comparación con su resistencia.
Aluminio
El aluminio es un metal con un gran compromiso entre ligereza y solidez. Y es que además de ser resistente a la corrosión, también se puede soldar. Lo encontramos de manera bastante excepcional en estado puro y es más frecuente encontrarlo como aleación con otros metales que mejoran sus propiedades físicas y mecánicas, como el silicio y el magnesio. Al igual que el titanio, para obtener el material de forma pura podemos realizar dos procesos industriales consecutivos. En el primer proceso, llamado proceso Bayer, se obtiene óxido de aluminio a partir del mineral de bauxita. Se lava y tritura el mineral, se disuelve en soda cáustica y se filtra para obtener hidróxido de aluminio puro. Luego se calienta para obtener óxido de aluminio en polvo. En el segundo proceso, llamado proceso Hall-Héroult, se lleva a cabo la reducción electrolítica del óxido de aluminio para obtener aluminio puro. La mayoría de las plantas de procesamiento se construyen cerca de las minas para reducir los costes de transporte del mineral.
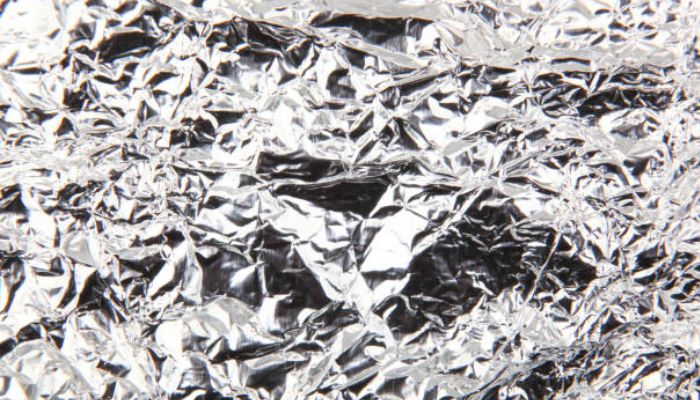
Créditos: Getty Images
Como ya hemos dicho, las aleaciones de aluminio son más frecuentes que la forma pura y se utilizan en muchas aplicaciones industriales. Además, tienen una muy buena relación resistencia-peso y una muy buena resistencia a la fatiga del metal y a la corrosión. Entre sus propiedades también encontramos que es altamente reciclable, conductor térmico y de electricidad y bajo en toxicidad.
Las aleaciones más importantes y utilizadas en la impresión 3D del aluminio son:
- AISi10Mg: es la aleación más común formada por silicio y magnesio. Permite fabricar piezas sólidas y complejas y se utiliza para crear objetos diversos como carcasas, piezas de motores y herramientas de producción.
- Al2139: la aleación de aluminio más fuerte creada por la empresa alemana EOS. Es ideal para sectores como la automoción debido a su ligereza, fuerza y resistencia química, y ha sido empleada por organizaciones como la Fuerza Aérea de los Estados Unidos, Mercedes-Benz y Airbus. Lo interesante de este material es que fue diseñado específicamente para la fabricación aditiva y supera a muchas otras aleaciones en el mercado.
- Al serie 7000: es una famosa serie de aleaciones en polvo, con alta resistencia a la tracción y a las bajas temperaturas.
- Al 6061 & Al 7075: recientemente los fabricantes 3D están teniendo muy buenos resultados utilizando estas dos aleaciones, el 6061 tiene menor resistencia a la tracción y dureza que el 7075. Y por otra parte, el 7075 resiste mejor al impacto y se deforma menos que el aluminio 6061.
- A201.1: es parte de la serie 200 de aleaciones de cobre-aluminio, conocidas por ser muy resistentes. Sin embargo, es difícil moldearlas por fundición. Estas aleaciones son recomendadas para aplicaciones donde la relación entre fuerza y peso es crucial, como en el transporte y la aeroespacial.
¿Y si comparamos los dos metales que diferencias obtenemos?
El aluminio y el titanio son dos metales muy diferentes que se utilizan en una amplia gama de aplicaciones y para decidir entre cuál de los dos utilizar hay que tener en cuenta las diferencias entre sus propiedades.
En cuanto a la relación resistencia-peso, el titanio es la opción ideal cuando se necesita una alta resistencia y robustez, es por eso que se utiliza en componentes médicos o incluso en componentes para satélites. En cambio, aunque el aluminio es menos resistente que el titanio, es mucho más ligero y asequible. Si hablamos de las propiedades térmicas, el aluminio es perfecto para aplicaciones que requieren una alta conductividad térmica. Por otro lado, el titanio es ideal para aplicaciones en entornos de alta temperatura, gracias a su elevado punto de fusión, como por ejemplo en los componentes de motores para el sector aeroespacial. Tanto el aluminio como el titanio tienen una excelente resistencia a la corrosión. Sin embargo, el titanio es más biocompatible que el aluminio y es por eso que se utiliza en gran mayoría en el sector médico.
Forma del material y tecnologías 3D utilizadas
Forma
En la mayoría de los casos, el titanio y el aluminio se encuentran en forma de polvo, aunque también puede estar disponible en forma de alambre/hilo, como el filamento de titanio o aluminio de Virtual Foundry o Nanoe con su oferta Zetamix.
Para imprimir piezas en 3D con estos metales, primero se debe obtener el polvo de la aleación, lo cual se realiza mediante dos técnicas principalmente: la atomización por plasma o la atomización por gas. La atomización por plasma (gas ionizado) es un proceso que utiliza altas temperaturas, una fuente de energía y calor, un medio inerte como el argón y altas velocidades para pulverizar el metal. Este proceso produce polvos de alta calidad resistentes al desgaste. Por otro lado, la atomización por gas utiliza aire, argón o helio como gas para fragmentar una corriente fundida de material. Es un proceso muy eficaz y bastante empleado para producir polvos metálicos finos y esféricos. La técnica utilizada para fabricar el polvo metálico es importante, ya que, como es obvio, influye en las propiedades finales de la pieza.
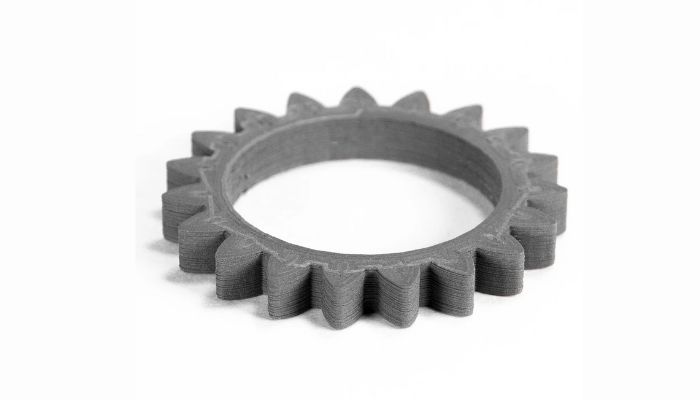
Engranaje fabricado con Titanio 64-5 sin sinterizar. Créditos: SAPPHIRE3D
Tecnologías 3D utilizadas
Para trabajar con titanio en la impresión 3D se pueden utilizar una gran cantidad de tecnologías para metal como la fusión láser por lecho de polvo (L-PBF), la deposición de energía directa (DED) o la llamada Binder Jetting. Para los procesos con aluminio contaremos con otro más además de los ya mencionados como la pulverización en frío, también conocida como Cold Spray.
En los procesos de fabricación aditiva de L-PBF, el haz de láser se utiliza para calentar el metal en polvo capa por capa hasta su punto de fusión y construir el objeto. El titanio se funde a temperaturas muy altas (1600°C) por lo que se necesitará analizar previamente los efectos térmicos y mecánicos del material antes de imprimir en 3D. En cuanto a la temperatura para fundir el aluminio es bastante más baja ya que rondan los 630°C, pero a su vez hay que tener en cuenta que el aluminio tiene una alta reflectividad y una alta conductividad térmica para el proceso. Algo también muy interesante en la fabricación aditiva con aluminio es que este material forma una capa de óxido natural, cosa que hacen los otros metales más tarde en sus bordes y que implica que al tener esa fina capa por encima, el proceso será más lento.
En cuanto a la deposición de energía directa encontramos un proceso muy parecido al anterior pero aquí el material se funde al mismo tiempo que se deposita en la boquilla y podemos encontrarlo en forma de polvo o alambre para realizar la fabricación. Normalmente esta tecnología nos da una mayor velocidad de producción y un menor coste por unidad de volumen.
Si hablamos de inyección aglutinante o Binder Jetting, el material estará en forma de polvo, el cuál no se funde sino que para que las partículas se adhieran entre sí, en este caso, se pulverizará un aglutinante sobre la capa en los puntos concretos mediante un cabezal de impresión. También es necesario un paso de sinterización después de la impresión. Al salir de la impresora 3D, las piezas son muy frágiles y porosas y tendrán que ser tratadas térmicamente para obtener sus propiedades mecánicas finales.
En los procesos de pulverización en frío también encontraremos el material metálico en forma de polvo pero ya que en este caso no es necesario fundirlo ni fusionarlo al pulverizarlo en frío podemos evitar la distorsión del calor así como que no será necesaria una atmósfera protectora.
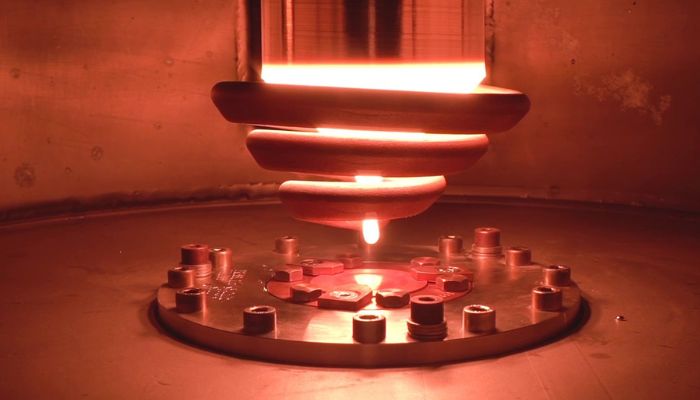
Créditos: Sandvik
Postprocesado
Para lograr un resultado óptimo, es crucial aplicar un proceso de postprocesado a las piezas. No hay diferencias específicas en el postprocesado del titanio y el aluminio, por lo que los siguientes pasos se aplican a ambos materiales. Debido a que el titanio y el aluminio se utilizan a menudo en aplicaciones sometidas a esfuerzos mecánicos, la técnica de bead blasting y shot peening son muy beneficiosas. En el primer método, se lanzan pequeñas bolas de metal o cerámica contra la superficie de la pieza para crear una deformación controlada en la capa superficial de la misma. Esto mejora la adherencia de los revestimientos posteriores y reduce la probabilidad de grietas y fracturas, entre otras cosas. El shot peening solo elimina la capa superior del material, lo que puede mejorar el aspecto estético de la pieza, eliminar la suciedad y la corrosión, y preparar la superficie para los revestimientos posteriores.
Otra opción es combinar la impresión en metal con métodos de fabricación tradicionales. El mecanizado CNC es un proceso de postprocesado adecuado para este propósito, ya que garantiza tolerancias ajustadas y el acabado superficial deseado. Especialmente con la tecnología DED, las piezas en bruto tienen una superficie muy rugosa debido a que el metal se funde directamente durante el proceso de extrusión. Por lo tanto, siempre es necesario el mecanizado CNC para obtener una superficie lisa y definida.
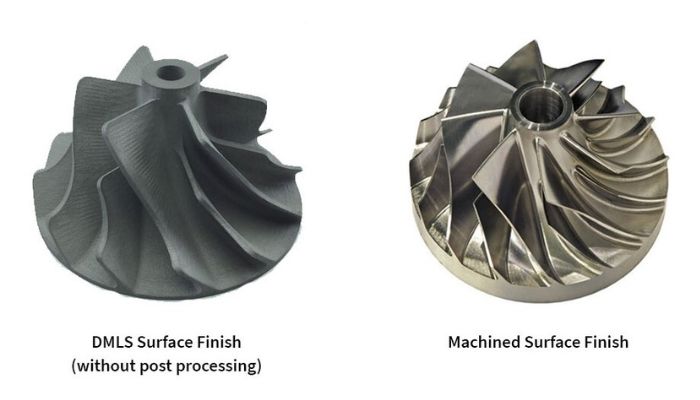
Créditos: FacFox
El recocido por disolución es una opción de tratamiento térmico que implica calentar la pieza impresa a alta temperatura y enfriarla rápidamente para cambiar la microestructura, lo que mejora la ductilidad del material, es decir, su capacidad para deformarse bajo carga antes de romperse. En general, se obtienen mejores propiedades mecánicas con este proceso, que se utiliza especialmente para piezas de aluminio.
La sinterización también es necesaria para el aluminio y el titanio cuando se utilizan en los llamados procesos indirectos de impresión 3D, como la FDM o la unión de polvos. Tras la fase de impresión, las piezas deben someterse a un proceso de desaglomerado para separar los polímeros del aglutinante metálico. A continuación, las piezas se calientan a cierta temperatura en un horno de sinterización, justo por debajo de la temperatura de fusión, que consolidará el objeto final. Esto da lugar a piezas con una porosidad muy baja, ya que las cavidades donde se encontraba el aglutinante se cierran durante el proceso, lo que da lugar a la compresión.
Aplicaciones
La industria aeroespacial ha encontrado un gran beneficio en el uso de la fabricación aditiva de titanio. El titanio es un material ideal para la fabricación de componentes aeronáuticos, como motores a reacción y turbinas de gas, ya que puede reducir significativamente el peso de las estructuras sometidas a grandes esfuerzos. Un ejemplo de la aplicación del titanio en la fabricación aditiva es la asociación de Boeing con Norsk Titanium para fabricar componentes estructurales de gran tamaño del 787 Dreamliner. La tecnología utilizada en este proceso es el DED, que funde el alambre de titanio con sopletes de plasma para producir la pieza final. Este proceso es entre 50 y 100 veces más rápido que los sistemas basados en polvo y utiliza entre un 25 y un 50% menos de titanio que la forja, lo que podría suponer un ahorro de hasta 3 millones de dólares por avión.
Aunque el titanio se utiliza actualmente en la exploración espacial con la impresión 3D, se ha incrementado la aplicación del aluminio en la industria. Por ejemplo, Boeing produce piezas impresas en 3D a partir de aleaciones de aluminio que se recubren con nanopartículas durante la fase de enfriamiento. Esto permite soldar una aleación de aluminio extremadamente resistente sin que se agriete en caliente. Los bastidores fabricados son mucho más ligeros, lo que permite a los aviones utilizar el combustible de manera eficiente y volar distancias más largas con la misma cantidad.
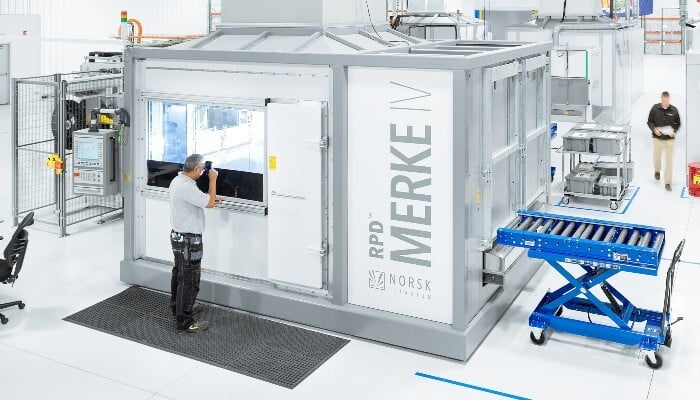
Esta máquina fabrica piezas para el Boeing 787. Créditos: Norsk Titanium
Aunque el precio elevado del titanio en el sector del automóvil puede ser un obstáculo para su uso generalizado debido a la importancia del precio para los consumidores finales, podemos ver un aumento en su uso en este sector, especialmente en el segmento de lujo. Actualmente, la impresión 3D se utiliza para crear piezas en las que la relación entre peso y rendimiento es crucial. Por ejemplo, Bugatti imprimió la pinza de freno de su sistema de frenado en titanio con tecnología SLM en solo 45 horas, lo que se dice que es un 40% más ligera que una pinza de freno de aluminio fresada convencionalmente. A pesar de su ligereza, la pieza de titanio también garantiza su elasticidad y resistencia a la temperatura. Por otro lado, el aluminio es más común en la industria automotriz. Porsche utilizó la impresión 3D para crear pistones de aluminio de alto rendimiento para su modelo insignia 911, el GT2 RS. Gracias a esta tecnología, el motor biturbo de 700 CV puede obtener hasta 30 CV más de potencia y mejorar la eficiencia. Además, en 2020 Porsche fabricó una carcasa completamente de aluminio impreso en 3D para un propulsor eléctrico que superó todas las pruebas de calidad y carga de la empresa.
El titanio es un material muy atractivo en la industria médica debido a su gran resistencia y resistencia a la corrosión, además de ser biocompatible, lo que lo hace ideal para implantes ortopédicos y dentales. La impresión 3D permite la creación de estructuras porosas que imitan la textura ósea, lo que contribuye a la rápida cicatrización y al crecimiento del hueso y tejido. La empresa TrabTech de Turquía fabrica implantes trabeculares, como una cadera, utilizando titanio. Por otro lado, el uso del aluminio es menos común en la industria médica en comparación con el titanio, pero puede utilizarse para aplicaciones ortopédicas y dentales. Sin embargo, el titanio sigue siendo el material preferido debido a su biocompatibilidad y propiedades únicas.
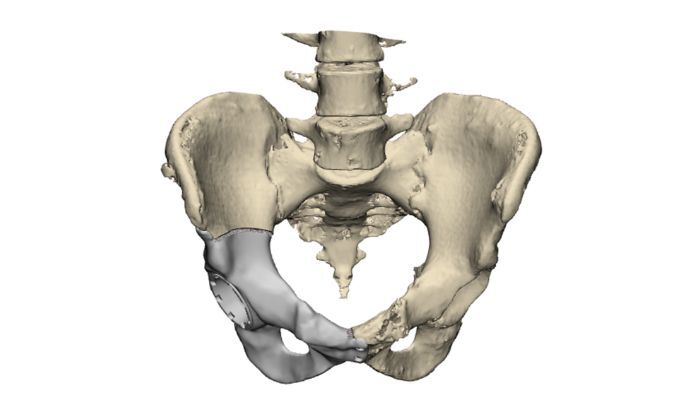
TrabTech fabrica implantes trabeculares de titanio. Créditos: TrabTech
Precio y fabricantes
El titanio presenta una desventaja importante debido a su elevado precio. Según el Informe Wohlers 2021, el polvo de aleación de titanio Ti-6AI-4V o titanio puro de grado 2 cuesta alrededor de 363 dólares estadounidenses por kilogramo, situándose en uno de los segmentos de precios más elevados. En contraste, el aluminio es considerablemente más económico, con la aleación de aluminio AISi7 disponible por 94 dólares/kg de polvo y AISi10Mg por 98 dólares/kg.
En el mercado de fabricantes, destacamos a Heraeus Additive Manufacturing, empresa alemana especializada en el procesamiento de metales preciosos que produce diversos tipos de titanio, como 6Al-4V, grado 5 y grado 23. Estos tipos de titanio también son producidos por PyroGenesis Additive y AP&C. GKN, por otro lado, ofrece titanio puro y titanio Beta 21S. Por el lado del aluminio, Uniformity Labs y Equispheres son empresas de comercialización que producen la aleación de aluminio AISi10Mg, mientras que APWorks produce el polvo de aleación de aluminio de la serie 7000.
¿Qué te parece este artículo sobre el titanio y el aluminio en la impresión 3D? Deja tus comentarios en nuestras redes sociales: Facebook, Twitter, Youtube y RSS. Sigue toda la información sobre impresión 3D en nuestra Newsletter semanal.