Les clés pour réussir ses impressions 3D FDM/FFF
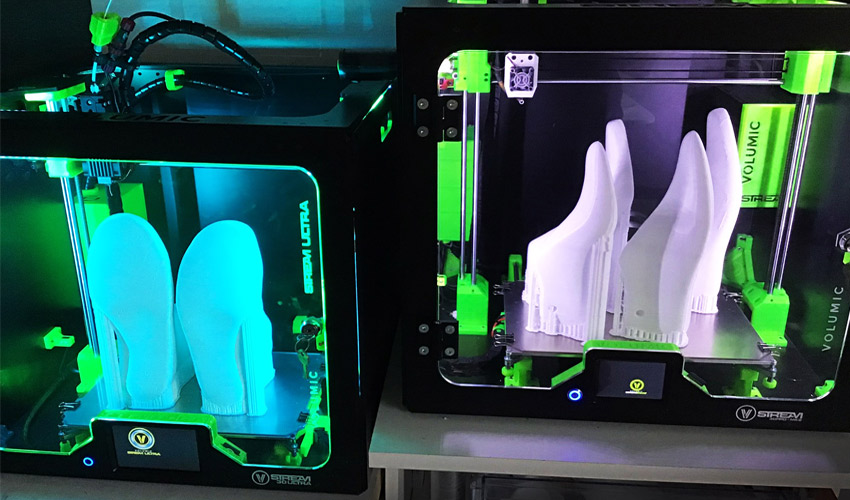
L’impression 3D FDM/FFF est l’un des procédés les plus utilisés sur le marché de la fabrication additive, que ce soit pour produire des prototypes, de l’outillage ou des pièces finies. Aujourd’hui compatible avec une large variété de thermoplastiques, elle permet de concevoir des composants plus ou moins complexes en ajoutant des couches successives de matière sur un plateau d’impression.
Mais comment s’assurer de la réussite de son impression ? Quels sont les éléments qu’il faut prendre en compte pour éviter toute erreur ? Gérard Luppino et Stéphane Malaussena, fondateurs de l’entreprise française Volumic, fabricant d’imprimantes 3D FDM/FFF depuis plusieurs années, nous donnent quelques clés pour optimiser ses travaux d’impression : calibrage du plateau, changement de la buse de l’imprimante, modélisation de la pièce, etc. Voici quelques conseils pratiques qui vous permettront d’obtenir une pièce de qualité.
Mieux concevoir pour mieux imprimer
Quand il s’agit d’imprimer une pièce en 3D, la modélisation est une étape clé rappelle Volumic : concevoir un modèle pour l’impression 3D FDM implique des changements assez importants par rapport à des techniques de fabrication traditionnelle. Elle va permettre d’optimiser non seulement le temps d’impression et le rendu, mais aussi la matière consommée (pour les supports par exemple) et le temps de post-traitement. En effet, une pièce nécessitant des supports aura forcément un temps de post-production et risque d’être bien moins propre qu’une autre sans support. Dans tous les cas, ou il y a support, il y a dégradation de surface, plus ou moins forte selon la technique utilisée, mais toujours présente.
Il faut donc adopter de nouveaux réflexes en essayant d’éliminer toute surface à plus de 45 à 55° d’inclinaison par rapport à la base, et au final il est souvent assez facile de faire un chanfrein à 45° plutôt qu’un épaulement direct qui va nécessiter des supports.
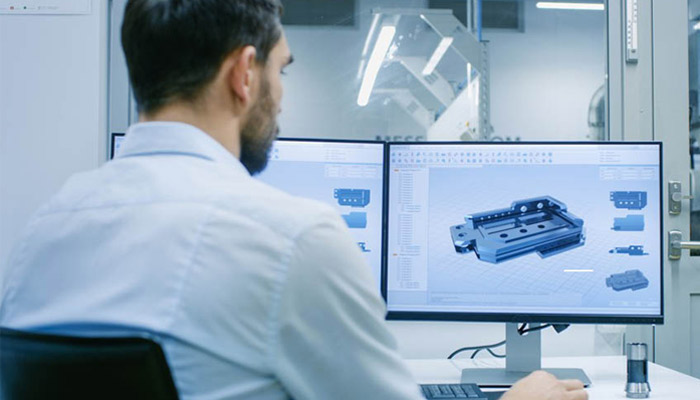
Modéliser pour l’impression 3D est une étape cruciale dans le processus de fabrication
L’évidage des volumes n’est pas forcément une bonne chose non plus en FDM selon le fabricant, car le remplissage de la pièce peut être choisi, contrairement à l’injection par exemple, et des zones évidées nécessiteront souvent des supports en dégradant les surfaces et en consommant de la matière que l’on essayait d’économiser. Les contraintes en injection ne sont pas les mêmes qu’en impression : il faut penser différemment et ce, dès l’étape de modélisation, c’est très important.
Le matériau, un choix à ne pas négliger
De plus en plus de matériaux différents sont disponibles pour subvenir à un maximum d’applications de tous les secteurs d’activités. Toutes les matières ne requièrent pas le même niveau d’expérience et d’attention. Le point principal qui va rendre une matière plus facile ou capricieuse à imprimer reste l’adhérence au plateau. Ce point ne doit en aucun cas être négligé car outre une impression ratée, cela peut aussi engendrer des casses machines assez importantes, dues aux collisions d’un objet qui s’est décollé. On peut avoir des collisions directes avec la tête d’impression qui pourra s’endommager, et causer des casses sur d’autres parties de l’imprimante.
Les matériaux dit « Standard » (PLA, PETG) sont aujourd’hui stabilisés pour fournir une adhérence très correcte afin que les impressions se passent sans encombre, même si l’étalonnage de la machine n’est pas parfait. Des additifs sont en effet ajoutés pour optimiser l’adhérence et faciliter le processus d’impression. Par contre, des matières plus techniques auront bien moins d’adhérence d’une part, mais aussi très souvent un retrait assez important qui risque d’engendrer du warping, et donc réduire encore la surface au plateau, et augmenter encore le risque de décollement.
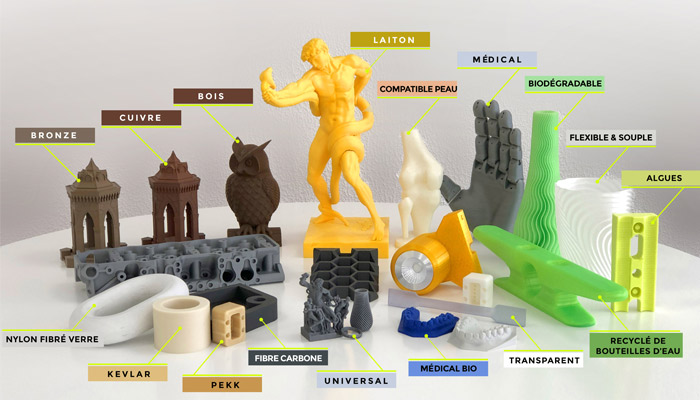
Les matériaux compatibles avec les machines Volumic (crédits photo : Volumic)
Il est donc important de bien préparer sa surface d’impression par rapport à la matière qui va être imprimé, la solution « universelle » n’existant pas. Par exemple, pour des impressions de matières techniques avec plateau à haute température (110/120°C ou plus) la laque type Dimafix sera plus efficace que la 3DLAC, cette dernière étant plus adaptée aux matières standards et plus économique.
Utiliser des revêtements plateaux spéciaux peut aussi s’avérer nécessaire. Un PEKK pourra s’imprimer sur un plateau vitro+Dimafix en règle générale, mais un PEEK ou un PEI sera bien plus capricieux et nécessitera un revêtement en PEI sur le plateau ainsi que de la laque. Pour ce genre de matière, il est aussi conseillé de régler le point zéro machine assez bas (distance entre la buse et le plateau), pour bien écraser la première couche et augmenter l’adhérence.
Les techniques de multiplications de contours sur la première couche pour étendre la surface au plateau sont souvent d’une grande aide, et génèrent assez peu de post-traitement. En collant ainsi la pièce a son contour, au-delà de bien armer la buse, la pièce sera bien mieux maintenue au plateau, même si a l’origine, sa surface de contact avec celui-ci était faible.
Pour les matières qui ont tendance à délaminer sur la hauteur, un bouclier d’un ou deux murs autour de l’objet sur toute sa hauteur peut aussi aider à garder plus de chaleur à l’intérieur et éviter ou réduire ce genre de phénomène.
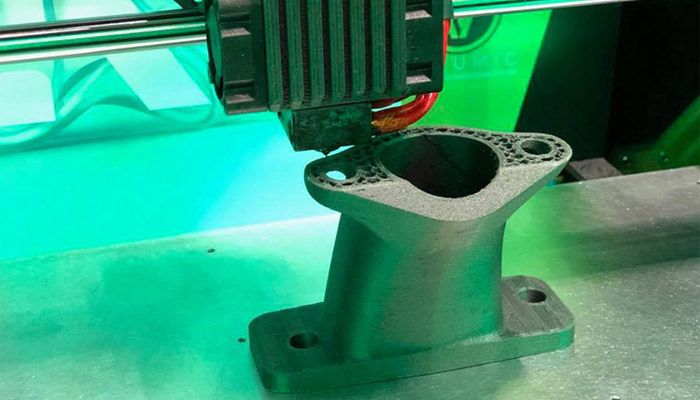
Une pièce imprimée avec du PEKK (crédits photo : Volumic)
Comment bien préparer son fichier 3D
Le modèle STL dont vous disposez est très important pour un résultat de qualité. Très souvent le modèle qui est créé sur un logiciel de CAO comme SolidWorks par exemple, est exporté en STL avec les paramètres par défaut du logiciel. Ce paramètre doit être ajusté selon vos objets afin de générer un modèle avec assez de faces pour avoir des courbes et des formes de très bonne qualité. On sous-estime souvent la résolution du modèle STL à tort, car même si les faces ne se voient pas à proprement dit sur le modèle imprimé, cela va générer un bruit sur les surfaces, surtout sur les machines précises comme les Volumic qui vont retranscrire tous ces milliers de petits mouvements.
Mieux vaut un modèle un peu lourd que pas assez. Ne choisissez pas une résolution trop fine si cela n’est pas réellement essentiel, plus les couches sont fines, plus elles risquent de générer des micro-collisions qui vous donneront un moins bon résultat ou feront échouer votre impression. Plus l’objet est volumineux, plus la résolution du maillage doit être élevée. Une source d’erreur assez fréquente sur les impressions réside aussi dans le fait que le modèle qui va être tranché doit être exempt de toute erreur de maillage (faces ouvertes, qui se recoupe…) car cela risque d’être mal interprété par le slicer et générer des mouvements ou des extrusions qui vont faire échouer l’impression. Vérifiez toujours que le modèle ne contient aucune erreur de face, la plupart des slicers ont d’ailleurs des fonctions intégrées de vérification.
Concernant ces slicers d’ailleurs, il y en a de plus en plus, et des logiciels comme la suite Adobe et Fusion commence à intégrer cela. Les performances de tranchages sont désormais de bonne qualité sur la plupart des logiciels (ce qui n’était pas forcement le cas il y a encore quelques années), les plus grosses différences vont résider sur des fonctionnalités d’aide au positionnement par exemple, de paramètres pour l’optimisation de l’impression et du rendu, ou de la gestion personnalisée des supports, ce qui peut faire toute la différence. Volumic a choisi de travailler avec Simplify3D car sa qualité de tranchage couplée à des paramètres d’optimisations très efficace et sa gestion manuelle des supports en font un outil simple et puissant à un cout très raisonnable.
Enfin, une bonne habitude est de toujours surveiller le début de votre impression et l’état du remplissage de la première couche. Cela vous montrera assez clairement un bon ou un mauvais étalonnage.
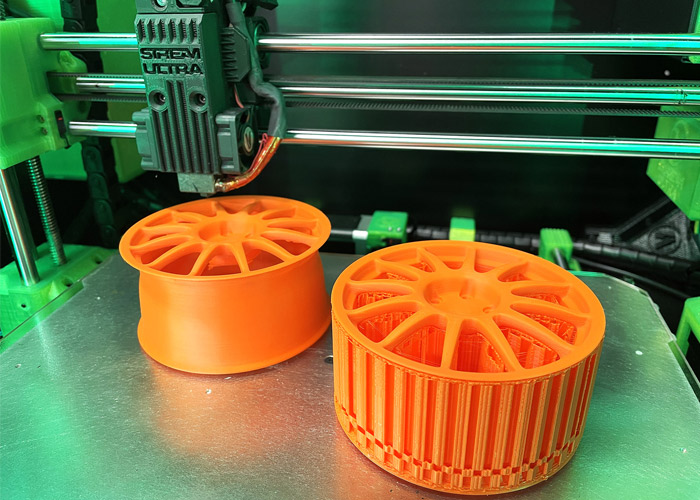
Prototype de design de jantes imprimé en 3D avec l’Universal Ultra Orange Autolissant (crédits photo : Volumic)
Les caractéristiques machines de l’imprimante 3D
Les points essentiels pour l’impression restent bien sûr les températures de buse et de plateau par rapport à la matière. Les profils d’impressions et les indications donnés par les fabricants restent une généralité. Cela ne veut donc pas forcement dire que ce sera adapté en toutes circonstances, et peut être amené à varier selon la température ambiante par exemple, ou le type de buse monté. On sous-estime très souvent ce que 5°C de plus ou de moins à la buse peut changer !
La ventilation de l’objet est elle aussi très importante pour un bon rendu, mais peut aussi diminuer la liaison entre couches de l’objet si elle est trop importante.
Concernant la vitesse, elle va jouer un rôle très important dans la qualité finale de l’objet, et plus spécialement les vitesses relatives selon les zones. Par exemple, augmenter la vitesse d’impression du remplissage fera gagner beaucoup de temps d’impression sans pour autant compromettre la qualité. Par contre, augmenter la vitesse des murs va générer de plus en plus d’artéfacts et de ghosting sur la surface de la pièce. La vitesse de chaque zone a un impact très diffèrent et doit être modifiée indépendamment des autres pour une optimisation parfaite.
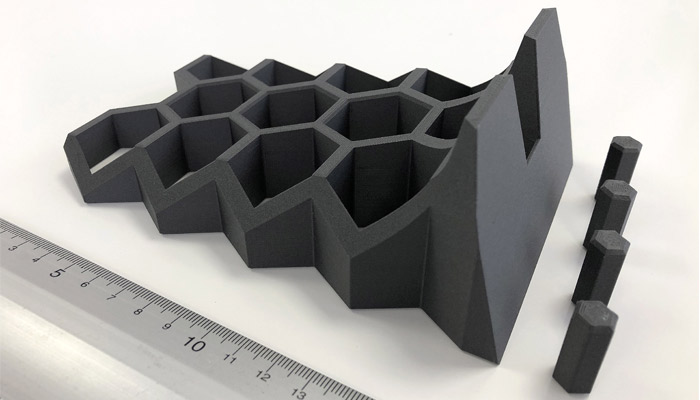
Grille nid d’abeille : Impression en Universal Ultra Carbone Autolissant (crédits photo : Volumic)
La température du plateau va elle, conditionner l’adhérence de l’objet, ce qui est donc plus que primordial. En règle générale, la température du plateau idéale pour une matière donnée est, dans la limite du possible, celle de la Tg de la matière en question.
Un autre point primordial, et qui est surement le plus important de tous, est le refroidissement de la tête d’impression. Une tête mal refroidie génèrera toutes sortes de dysfonctionnements, mais principalement des blocages de filaments. Il suffit, par exemple, d’un changement de 2°C dans le corps de refroidissement de la tête pour faire échouer une impression en PLA. Le filament doit rester le plus froid possible tout au long de la tête pour se liquéfier d’un coup sur la distance la plus courte possible avant la buse (d’où la barrière thermique), et surtout ne pas chauffer progressivement, sinon le filament va systématiquement se bloquer. Une buse et une barrière thermique en bon état, et changées régulièrement, vous donneront des objets de qualité et une répétabilité des impressions. Volumic préconise un changement de la buse au bout de 800 heures d’impression en moyenne. Vous pouvez également utiliser un filament de purge qui va déloger les impuretés. D’ailleurs, notez que plus un matériau est chargé, plus il faudra changer la buse.
Le type de buse utilisé dépend principalement de la matière imprimée. L’impression de matières chargées, même faiblement, doit être impérativement réalisé avec une buse en acier trempé, sans quoi elle va s’user très rapidement et provoquer toutes sortes de problèmes et de baisse de qualité. D’un autre côté, une buse en cuivre plaqué nickel donnera de meilleurs résultats (de par ses performances thermiques) de rendu et de vitesse sur des matières non chargés. Il n’y a donc pas de buse « universelle » qui donnera les meilleurs résultats en toutes circonstances.
Les méthodes de post-traitement pour aller plus loin
Le post-traitement peut parfois s’avérer fastidieux. C’est pour cela que le placement des supports doit être fait avec soin et sans zèle. Une bonne préparation des supports peut être un énorme gain de temps en post-traitement, ne sous-estimez pas cette étape.
Utilisez toujours des gants de sécurité pour travailler les supports, même sans outils, ceux-ci peuvent couper ou griffer. La spatule reste un bon outil pour les décoller, notamment sur les grandes surfaces planes. D’ailleurs, décollez toujours les supports dans le sens du filament de la couche en contact, cela aura moins de résistance que dans d’autres sens. Une option assez efficace pour faciliter le retrait de supports étant de paramétrer au tranchage quelques couches « denses » au contact de l’objet. Cela améliorera d’une part l’état de surface de la pièce à l’endroit des supports, mais créera aussi une surface du support plus solide qui aura tendance à moins se morceler au retrait.
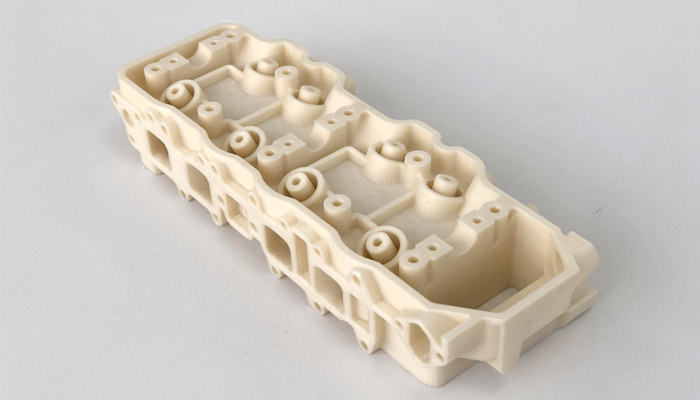
Pièce imprimée avec de l’Universal ULTRA (crédits photo : Volumic)
Certaines matières vont donner de très bons résultats avec des supports, comme l’Universal ULTRA, qui va non seulement offrir des surfaces très propres après retrait, mais s’enlever bien plus facilement que d’autres matériaux. A contrario, le PETG, du fait de son excellente liaison entre couche, va être assez difficile à nettoyer.
Un kit d’outils à ébavurer peut s’avérer d’une grande aide, ainsi que de petits tournevis plat et pinces à becs fins (type électronique) pour nettoyer des parties difficiles d’accès. Les cutters ultrasoniques sont aussi des outils très performants pour ce genre de travaux, un peu onéreux mais très efficaces.
*Crédits photo de couverture : M-Orthopédie
N’hésitez pas à partager vos bonnes pratiques et vos conseils en impression 3D FDM/FFF dans les commentaires de l’article ou avec les membres du forum 3Dnatives. Retrouvez toutes nos vidéos sur notre chaîne YouTube ou suivez-nous sur Facebook ou Twitter !