Conseils d’experts : pourquoi choisir l’impression 3D FDM composite ?
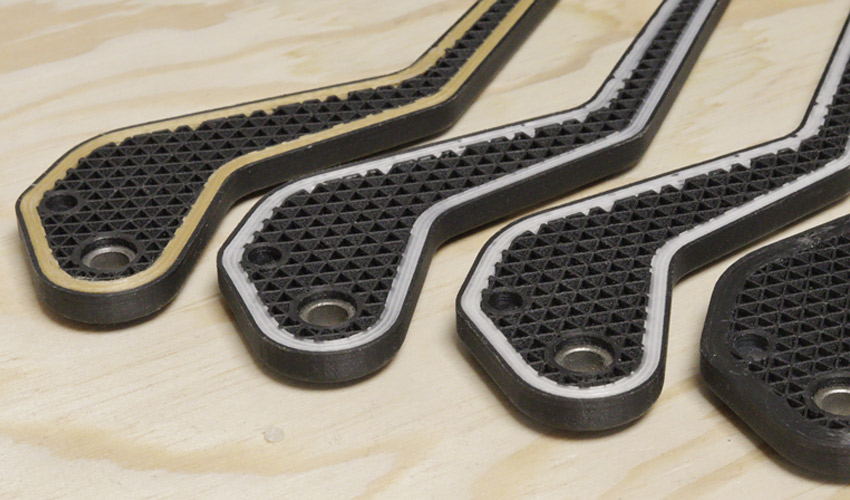
Les matériaux aujourd’hui compatibles avec la fabrication additive sont très nombreux, des thermoplastiques aux métaux en passant par la céramique ou encore les résines photosensibles. Ils offrent des propriétés très diverses permettant de répondre aux exigences de multiples secteurs comme l’aérospatial, l’automobile ou encore le médical. Si on s’intéresse à la famille des polymères, on retrouve notamment les composites : ce sont des matières renforcées à base de fibres. Disponibles sous forme de poudre ou de filament, elles offrent des caractéristiques mécaniques plus intéressantes qu’un polymère classique : meilleure rigidité, résistance à l’impact, légèreté, etc. Des avantages qui poussent de plus en plus d’entreprises à miser sur les matériaux composites en fabrication additive. Mais justement, comment intégrer l’impression 3D composite dans sa chaîne de production ? Quel matériau choisir ? Nous avons rencontré 3 experts du secteur qui nous ont éclairé sur ce sujet !
Notre premier expert est Bastien Debaud, ingénieur applications chez Neofab. Sa principale mission est de conseiller les professionnels dans le choix de la bonne technologie et de les accompagner sur l’ensemble de la chaîne de valeur. Notre deuxième expert est François Edy, responsable technique de la Kimya Factory. Il s’agit du service de fabrication additive proposée par le groupe ARMOR. François assure aujourd’hui la qualité des pièces fabriquées, les délais de production et conseille les clients. Enfin, Dominique Droniou est notre troisième expert. Gérant et fondateur de la société TH INDUSTRIES, il est spécialisé dans l’impression 3D FDM de pièces plastiques techniques et fonctionnelles. Justement, nous nous concentrons ici sur la fabrication additive composite par extrusion et donc plus particulièrement les filaments composites.
- Bastien Debaud
- François Edy
- Dominique Droniou
Les matériaux composites en impression 3D
Un matériau composite est une matière renforcée par une fibre, venant lui apporter des propriétés mécaniques additionnelles. Cette matière de base est appelée matrice et correspond à une large gamme de polymères sur le marché de la fabrication additive. Dominique Droniou explique : « Les fibres sont toutes couplées à plusieurs matières ; on trouve couramment de l’ABS, du PETG, du PLA ainsi que du polypropylène pour les matières basiques. On peut également retrouver du PEEK, du PEKK et de l’ULTEM, celles-ci sont nettement plus difficiles à travailler. » Concernant les fibres, elles sont aussi multiples et généralement on retrouvera du carbone, du verre ou de l’aramide.
Il est surtout important de souligner que ces fibres existent en plusieurs tailles, taille qui impactera fortement le processus d’impression et le résultat final. On parle de fibres courtes et à l’inverse de fibres longues ou continues. Les fibres courtes sont mélangées directement avec le polymère de base : le filament est alors extrudé par la machine. Les fibres longues sont quant à elle déposées en même temps que la matrice, ce qui nécessitera l’utilisation d’une imprimante 3D spécifique.
Certains fabricants se sont justement spécialisés dans le développement de solutions comme par exemple Markforged. Bastien Debaud nous a confié : « Markforged a imaginé un matériau composite baptisé Onyx ; il s’agit d’un nylon propriétaire Markforged chargé en fibres courtes de carbone, compatible avec la gamme de la marque. S’il le souhaite, l’utilisateur peut y ajouter lors du processus d’impression 4 types de fibres différentes : du carbone, du Kevlar, du verre ou du verre haute température. La machine vient ajouter un tissage à la matrice pour lui apporter différentes caractéristiques selon le besoin : résistance à l’impact, renfort ou encore résistance à la température. »
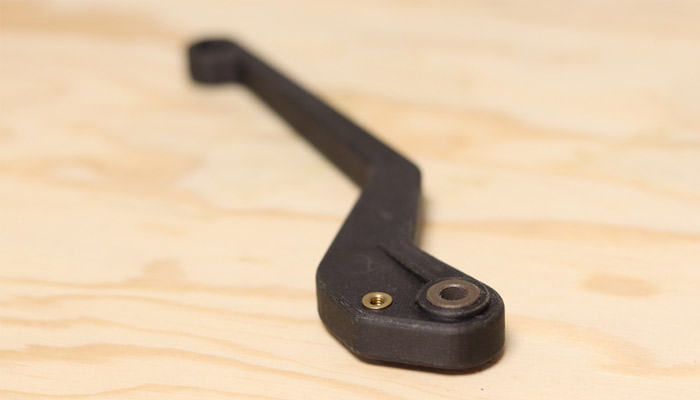
Un exemple de levier de frein imprimé dans un matériau composite (crédits photo : Neofab)
Les critères à prendre en compte pour imprimer des matériaux composites
Aujourd’hui, la plupart des machines FDM peuvent imprimer des composites à fibres courtes. François Edy affirme : « Les fibres courtes sont plus communes en fabrication additive et pourront s’imprimer sur n’importe quelle machine FDM. Veillez toutefois à avoir une buse en acier car les composites sont abrasifs. » Un point de vue partagé par Bastien : « Il vous faudra des buses renforcées car le composite aura tendance à ronger la buse et donc à réduire sa durée de vie. » Côté fibres longues, le processus d’impression est différent et nécessitera l’utilisation d’une machine spécifique capable de déposer la fibre sur le plateau et de la découper selon les besoins de l’utilisateur.
Si on se penche sur les paramètres d’impression, sachez qu’ils sont généralement identiques à ceux de la matrice de base dans le cas des fibres courtes. Pour les machines Markforged, tout est déjà défini pour assurer une meilleure qualité et répétabilité. Bastien affirme : « Il n’y a pas de réglages supplémentaires à faire. L’utilisateur viendra simplement régler sa hauteur de couche et son remplissage et poser une colle sur le plateau pour que la pièce adhère mieux. Le logiciel Eiger calculs les paramètres les plus optimisés pour réduire les étapes de préparation. »
François Edy nous alerte sur un point précis : « L’orientation de votre pièce est importante : les fibres de carbone se déposent dans le sens de l’extrusion. Vous aurez donc une meilleure tenue mécanique dans le sens de la buse. » Quant à Dominique Droniou, il explique : « Les pièces à base de fibres continues sont meilleures que les fibres courtes, mais la dépose de la fibre se fait mal ou ne se fait pas sur de toutes petites pièces. Pour les fibres courtes, plus la matière aura un taux de charge élevé plus il faudra une buse avec un diamètre important (en général minimum 0.6 mm ou 0.8 mm) ce qui limitera les détails. L’aspect sera plus « granuleux » sur les pièces avec forte charge. » Justement sur cet aspect visuel, Bastien nous explique qu’il sera plus mat et poreux.
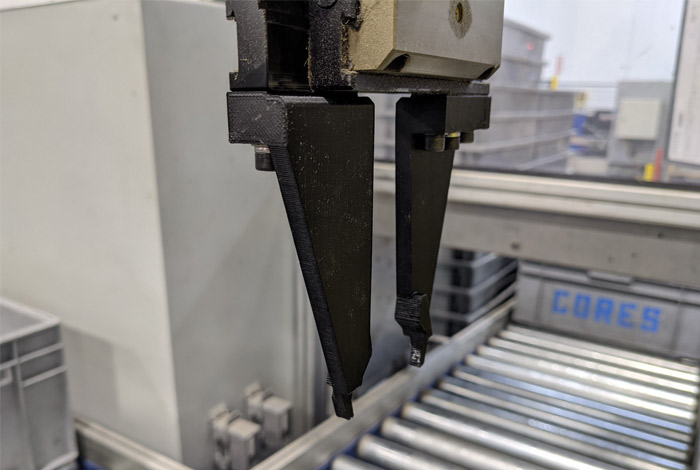
Une pièce imprimée en 3D en ABS Carbon Kimya, installée sur une chaîne de production ARMOR USA (crédits photo : Kimya)
Les avantages et les limites de l’impression 3D composite
L’impression 3D composite offre les mêmes avantages que l’impression 3D « classique » : réduction de délais de production, diminution de la quantité de matière utilisée, possibilité de personnaliser les pièces, etc. Elle se différencie par sa capacité à améliorer les propriétés d’une pièce, que ce soit en termes de résistance mécanique ou à la température. Bastien de Neofab ajoute : « La solution Markforged permet de déposer selon le besoin tout en limitant les coûts. On l’utilise quand on besoin de résistance mécanique. Par exemple, l’Onyx fibres de carbone est 1,5 fois plus rigide que l’aluminium tout en étant plus léger. La fibre de verre haute température permettra quant à elle d’obtenir une pièce résistante jusqu’à 110°C. On peut aussi choisir son type de renfort, isotropique ou concentrique selon son besoin. » Un constat partagé par François Edy qui confirme que le recours à la fibre de carbone améliore grandement la rigidité de la pièce ; d’autres matières comme le bois permettront quant à elle d’apporter des propriétés esthétiques uniques.
Si on se penche désormais vers les limites, ou du moins les freins, à l’impression 3D composite, nos trois experts s’accordent à dire que les fibres continues ajouteront une complexité au processus de fabrication par rapport aux fibres courtes. Dominique affirme : « La fibre continue est plus contraignante que la fibre courte. Les toutes petites zones ne pourront pas être remplies. » François explique quant à lui que les fibres continues répondent à des règles plus restrictives et présentent plus de problématiques techniques au niveau du slicing et de la trajectoire de la buse.
Pour Bastien, une autre limite réside dans le choix des couleurs du matériau ; chez Markforged, le noir est la seule option. De plus, la taille du plateau d’impression peut représenter un frein pour certains utilisateurs qui auraient besoin de produire de grandes pièces.
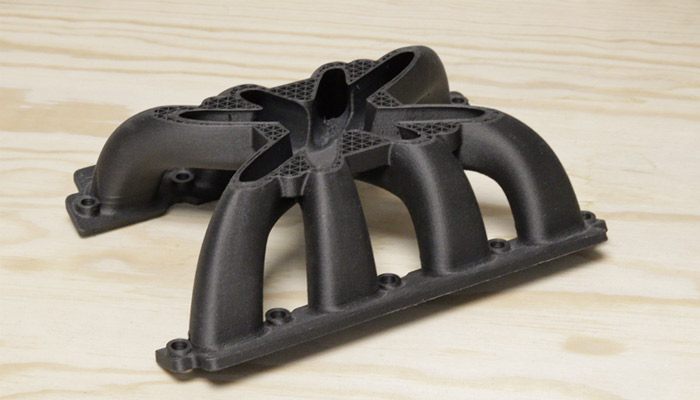
Grâce à la fabrication additive composite, l’utilisateur peut imaginer des formes complexes plus rigides (crédits photo : Neofab)
Les conseils ultimes de nos experts
François Edy conclut : Je vous conseille de tester d’abord des matières plus classiques. Puis, passez au FDM avec des fibres courtes car le processus d’impression est similaire. D’ailleurs, dans certains cas, l’impression 3D composite est même plus facile à mettre en œuvre, tout dépend de votre matrice de base.
Bastien Debaud ajoute : Il est important de s’équiper d’une buse résistante. Si vous voulez une impression composite fiable et répétable, alors je vous conseille la solution de Markforged qui s’appuie sur trois piliers : un logiciel, un matériau et une machine propriétaires. Elle propose une solution de qualité industrielle.
Enfin, Dominique Droniou affirme : Les matières composites permettent d’aller encore plus loin dans l’utilisation de pièces définitives en impression 3D. Ce sont des matériaux plus chers mais qui ont une réelle valeur ajoutée.
Utilisez-vous l’impression 3D composite ? N’hésitez pas en tout cas à partager vos commentaires sur ce projet dans les commentaires de l’article ou avec les membres du forum 3Dnatives. Retrouvez toutes nos vidéos sur notre chaîne YouTube ou suivez-nous sur Facebook ou Twitter !