Rolls-Royce beschleunigt die Integration der additiven Fertigung in seine Produktion
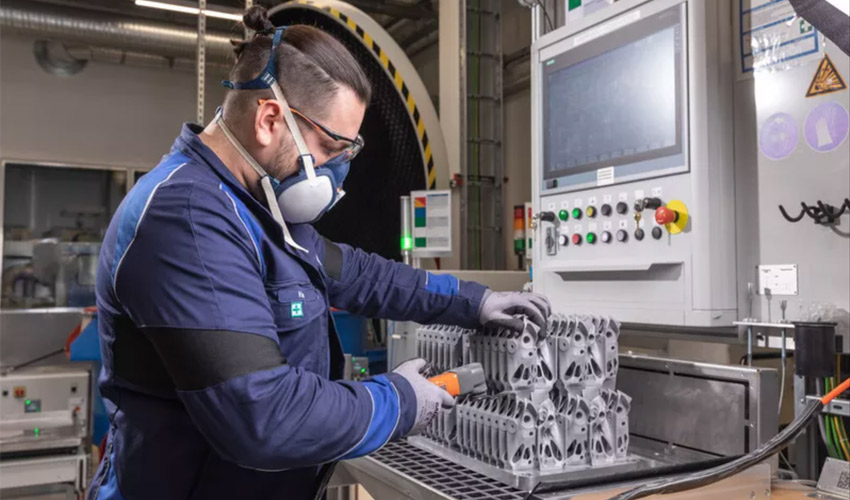
Seit Mitte des Jahres druckt der britische Hersteller Rolls-Royce, ein Tochterunternehmen der BMW Group, für sein Modell Rolls-Royce Ghost Kunststoff- und Metallteile in 3D. Die Teile werden entlang der Produktionslinie an verschiedenen Standorten im weltweiten Produktionsnetzwerk gefertigt und in Goodwood, England, montiert. Der Hersteller wird nach eigenen Angaben mehrere hunderttausend 3D-gedruckte Teile in den Rolls-Royce Ghost einbauen, und zwar über die gesamte Lebensdauer des Fahrzeugmodells. Insbesondere wird Rolls-Royce auf die Erfahrungen von BMW mit seinem neuen Zentrum für additive Fertigung zurückgreifen. Das Ziel ist klar: Der Konzern will 3D-Technologien nutzen, um Fahrzeuge in Serie zu produzieren, wobei Rolls-Royce nur der Anfang dieses großen Abenteuers ist.
Im vergangenen Juni eröffnete die BMW Group in Oberschleißheim, nördlich von München, ihr Kompetenzzentrum für die additive Fertigung, in dem rund fünfzig 3D-Drucklösungen, sowohl Kunststoff als aus Metall, vereint sind. Der Ehrgeiz der Gruppe besteht darin, diese Fertigungsprozesse zu industrialisieren, zu automatisieren und in Bezug auf das Design ständig zu innovieren. Daniel Schäfer, Leiter Produktionsintegration und Pilot Plant Integration bei der BMW Group, ergänzt: „Verfahren wie die additive Fertigung helfen uns, Entwicklungszyklen zu verkürzen und damit unsere Fahrzeuge schneller in die Produktion zu bringen. Der 3D-Druck hilft uns außerdem, die Fertigungszeiten für die Komponenten zu verkürzen und gleichzeitig hohe Qualitätsstandards einzuhalten.“ Diese Vorteile wurden schnell von der englischen Tochtergesellschaft des Konzerns, Rolls-Royce, übernommen, die in der Lage war, die additive Fertigung zu übernehmen und nun Endteile in höheren Stückzahlen konstruiert – wir sind noch weit von der Massenproduktion entfernt, aber das ist ermutigend.
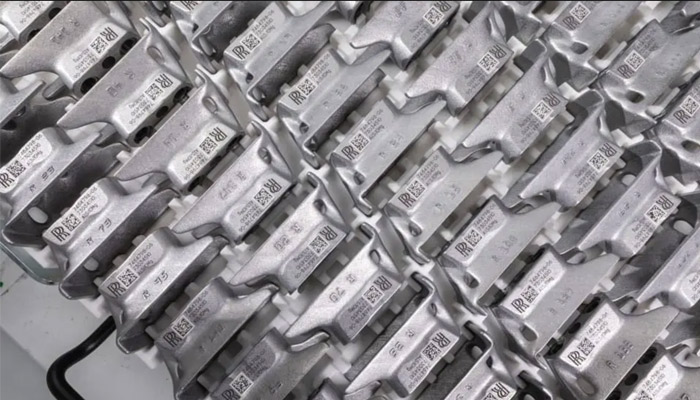
Rolls-Royce hat viele 3D-gedruckte Metallteile hergestellt | Bildnachweis: BMW
Rolls-Royce setzt auf auf die additive Fertigung mit Kunststoff- und Metall
Im vergangenen Oktober stellte Rolls-Royce eine neue Karosserie für das verlängerte Ghost-Modell vor: größer, ohne Abstriche beim Innenraumkomfort. Die vom Hersteller gedruckten Teile befinden sich daher im Fahrgastraum und unter der Karosserie. Für den Innenraum setzte die Gruppe auf Kunststoffbauteile mit den Technologien Selektives Lasersintern und Multi Jet Fusion, während für die Metallteile das Laserschmelzen bevorzugt wurde. Letztere werden im Werk der BMW Group in Landshut gefertigt und anschließend nahezu vollautomatisch in den Produktionsprozess integriert.
Es ist zu beachten, dass jedes 3D-gedruckte Metallteil einen eindeutigen QR-Code und Identifikationsnummer hat, die es ermöglichen, genau zu wissen, wo es platziert werden soll, an welchem Fahrzeug usw. Hätten die Teams traditionellere Fertigungsprozesse durchlaufen, wären sie wahrscheinlich nicht in der Lage gewesen, jedes Teil mit diesen Details zu versehen. Beachten Sie auch, dass das britische Markenlogo auf jeder Komponente vorhanden ist – ein Detail, aber es macht einen Unterschied.
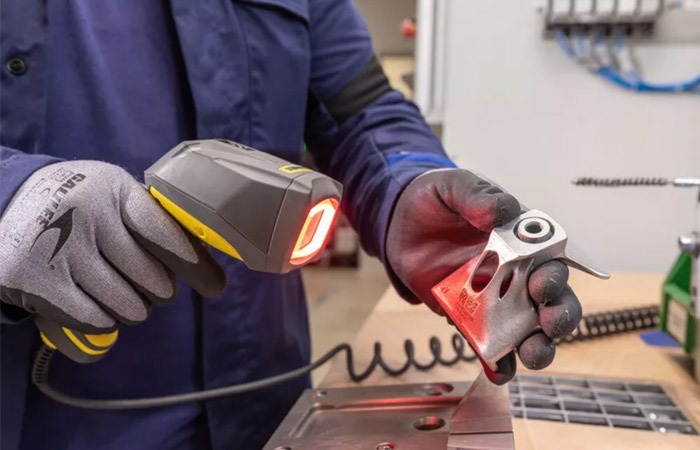
Jedes Metallteil kann durch eine eindeutige Nummer identifiziert werden | Bildnachweis: BMW
Auf der Designseite setzten die Teams bei BMW und Rolls-Royce auf generatives Design, um die Struktur der einzelnen Komponenten zu optimieren und ein leichteres und effizienteres Teil anzubieten. Sie erklären: „In den frühen Phasen der Entwicklung des neuen Rolls-Royce Ghost analysierten die Ingenieure Hunderte von Komponenten und testeten, inwieweit eine Fertigung mit additiven Fertigungsverfahren möglich ist. Im Mittelpunkt standen die Vorteile in Bezug auf Gewicht und Geometrie im Vergleich zu herkömmlichen Verfahren sowie die wirtschaftlichen Vorteile. Bei der Auswahl geeigneter Bauteile für die Serienfertigung mittels 3D-Druck definierten die Experten Kriterien und Anforderungen an die 3D-gedruckten Bauteile und übersetzten diese mit Hilfe von Datenspezialisten in „Maschinensprache“. Dies war der Startschuss für ein neues System der künstlichen Intelligenz, mit dem die BMW Group potenzielle 3D-gedruckte Bauteile in zukünftigen Fahrzeugen schneller und früher identifizieren kann.“
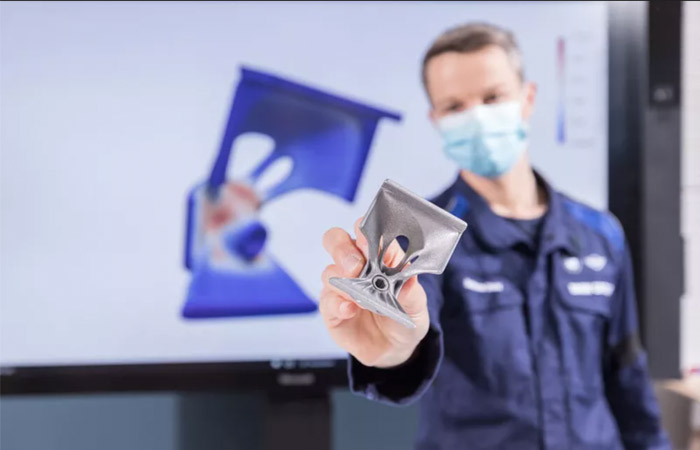
Die Gruppe setzt auf generatives Design und Topologie-Optimierung | Bildnachweis: BMW
Das Ziel wäre also, diesen Produktionsprozess vom Entwurf bis zur Fertigung so weit wie möglich zu industrialisieren und die Anzahl der 3D-gedruckten Teile schrittweise zu erhöhen. Eines ist sicher, die Eröffnung dieses speziellen Zentrums in Deutschland sollte das alles ändern. Weitere Informationen finden Sie HIER.
Was halten Sie von der Einführung der additiven Fertigung bei den Automobilherstellern? Lassen Sie uns dazu einen Kommentar da, oder teilen Sie es uns auf Facebook, Twitter, LinkedIN oder Xing mit. Möchten Sie außerdem eine Zusammenfassung der wichtigsten Neuigkeiten im 3D-Druck und der Additiven Fertigung direkt und bequem in Ihr Postfach erhalten? Dann registrieren Sie sich jetzt für unseren wöchentlichen Newsletter.