Conseils d’experts : comment concevoir pour la fabrication additive ?
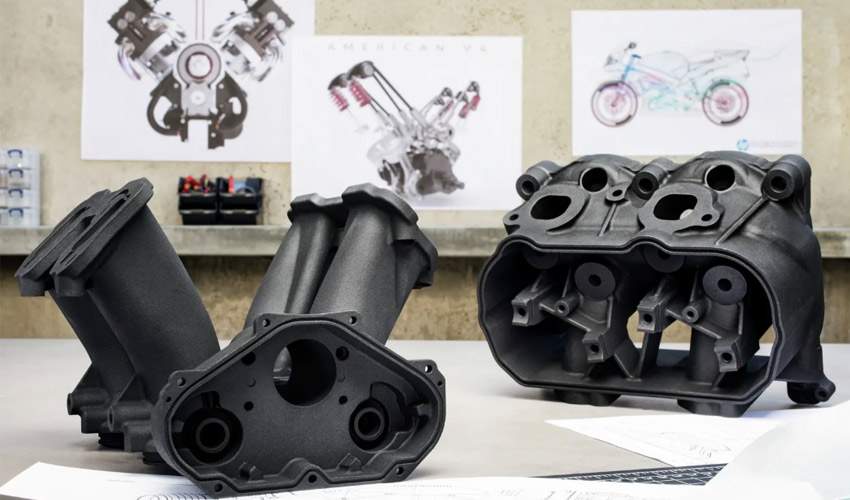
Vous n’êtes pas sans savoir qu’on ne conçoit pas une pièce à usiner de la même façon que celle qu’on imprimera en 3D : à chaque processus de fabrication est associé une technique de conception. En fabrication additive, il existe donc des règles de conception bien spécifiques et des outils qui permettront de créer un design optimisé, prêt à être imprimé en 3D. On regroupe généralement ces méthodes sous le terme de « Design for Additive Manufacturing » (DfAM), méthodes pensées pour optimiser au maximum les performances fonctionnelles de la pièce mais aussi son coût, sa fiabilité, etc. Plusieurs techniques sont aujourd’hui employées, que ce soit la conception générative, l’optimisation topologique ou encore la création de structures lattices. Comment choisir la bonne méthode de conception et optimiser tout le processus de design d’une pièce imprimée en 3D ? Nos experts vous éclairent !
Afin de répondre aux problématiques liées au DfAM, nous avons posé quelques questions à Ravi Kunju, SVP, Strategy and Business Development chez Altair ; Samuel Bernier qui est Lead Designer chez Onepoint ; et Daniel Pyzak, Director WorldWide CATIA Mechanical Systems Modeling & Simulate Centre of Excellence chez Dassault Systèmes.
- Samuel Bernier
- Ravi Kunju
- Daniel Pyzak
La technologie de fabrication à l’origine du design
Pour commencer, il nous paraît important de rappeler que la/les technique(s) de conception choisie va/vont dépendre de la technologie qu’on utilise. Ravi Kunju est assez clair : “C’est le processus qui dicte la manière dont une pièce est préparée et comment elle est terminée.” Si vous possédez une machine FDM, vous n’allez pas imaginer votre pièce de la même façon que si vous possédiez une imprimante 3D métal ou de frittage de poudre. En partant de la technologie même, vous éviterez certaines erreurs et cela vous permettra de mieux optimiser votre état de surface, de maximiser les propriétés mécaniques de votre pièce, de faciliter son nettoyage et donc plus globalement d’économiser du temps, de la matière et de l’argent. Daniel Pyzak de Dassault ajoute : “De nombreuses règles doivent être suivies pendant la phase de design pour obtenir une conception correcte pour l’impression 3D : ces règles dépendent fortement de la machine (taille, type de technologie, matériel).”
Prenons par exemple l’impression 3D métal, et plus particulièrement les procédés de fusion laser sur lit de poudre. Elle fait appel à plusieurs méthodes de DfAM car les objectifs finaux sont assez divers : réduire le poids de la pièce, le nombre de composants, augmenter ses propriétés mécaniques, etc. Ravi Kunju explique : “Par exemple, dans un processus de fusion sélective au laser pour imprimer du métal, une structure de support est requise pour l’impression de surfaces inférieures à 45 degrés. Sinon, la qualité de la surface peut être très mauvaise. Les structures de support sont coûteuses à imprimer et à supprimer, car elles doivent être soustraites de la pièce finale. La meilleure approche consiste à créer des conceptions avec des structures de support minimales. Il faut ajouter une contrainte pour s’assurer que la structure générée a des surfaces bien au-dessus de l’angle de 45 degrés par rapport à l’horizontale.” Minimiser le nombre de supports est donc une étape importante du DfAM – un point qui pourra d’ailleurs s’appliquer à d’autres technologies.
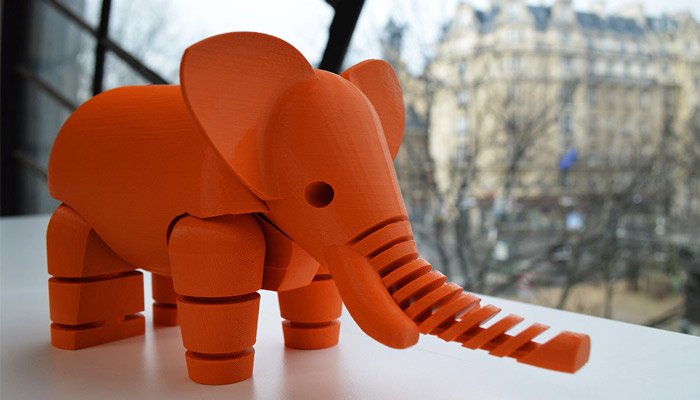
Samuel Bernier a conçu ce petit éléphant pré-assemblé pour l’impression 3D, minimisant les étapes d’assemblage
Orientation et optimisation de la pièce
Nos trois experts s’accordent à dire que l’orientation de la pièce est un point capital à prendre en compte quand on conçoit une pièce, c’est-à-dire le placement de la pièce sur le plateau d’impression. Elle définira en partie la qualité finale de votre pièce, la répartition de la chaleur, les supports nécessaires, etc. Samuel Brenier affirme : “Dans le cas d’une machine FDM, l’orientation de la pièce a un impact particulier sur ses propriétés mécaniques. Par exemple, prenez un prisme creux de la taille d’un stylo Bic. Imprimez-le à la verticale. Tordez la pièce légèrement et elle se brisera. Fabriquez la même pièce à l’horizontal, elle sera une dizaine de fois plus résistante. Analysez toujours les faiblesses de votre design afin de définir la meilleure orientation d’impression. Encore mieux, réfléchissez à l’orientation d’impression pendant que vous modélisez votre objet pour optimiser chaque angle, chaque épaisseur et chaque support.” Cette étape clé réduit donc le nombre d’erreurs, permettant alors de réaliser des économies en termes de temps et d’argent.
L’optimisation topologique est une autre méthode qui va dans ce sens là – elle sera toutefois davantage appliquée dans des procédés sur lit de poudre. Elle existe depuis plus de 20 ans mais s’est réellement industrialisée avec le développement de la fabrication additive. Selon Ravi, c’est “une méthode de conception générative éprouvée, axée sur l’optimisation de la distribution des matériaux à l’aide de méthodes numériques bien définies.” Elle vient donc supprimer la matière qui n’est pas utile à la réalisation et au maintien de la pièce. Il poursuit : “Il est extrêmement important d’évaluer si ce qui est imprimé est optimal, en poids et en répartition, car idéalement, il est préférable de soustraire autant de poids que possible avant de le construire de manière additive.”

Grâce aux solutions logicielles d’Altair, AP Works (filiale d’Airbus) a conçu un cadre imprimé en 3D pour sa moto. Avec l’optimisation topologique, ils ont pu réduire le poids final de la pièce de 30% (crédits photo : Altair)
Enfin, nos experts se sont attardés sur le concept de structures lattices, qui est une forme d’optimisation puisqu’on va chercher à réduire la masse de la pièce tout en conservant son intégrité structurelle. On vient créer un réseau de mailles, de noeuds qu’on rapproche souvent d’une structure en nid d’abeille, un design difficile à obtenir via des méthodes de fabrication classiques. Les avantages d’un tel design sont nombreux mais on retiendra principalement qu’elles offrent un rapport force/poids optimal puisqu’on peut retirer des matériaux dans les zones critiques de la pièce ; une absorption des chocs et une protection contre les impacts, particulièrement intéressant dans le cyclisme par exemple ; et la possibilité de créer de plus grandes surfaces. Daniel ajoute : « Les structures lattices peuvent améliorer le poids ou l’échange thermique et donc les performances finales de la pièce. »
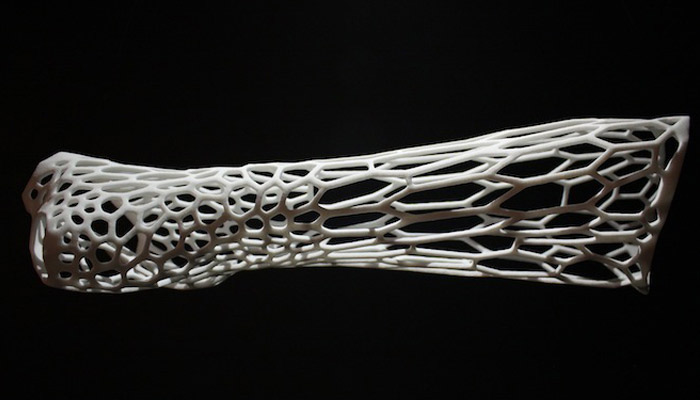
Exemple de structure lattice conçue sous le logiciel CATIA de Dassault Systèmes
L’impact de la conception sur le post-traitement
Pour la majorité des utilisateurs, le post-traitement est encore trop chronophage, considéré comme un processus pénible. C’est pourquoi il est important de minimiser ces étapes au maximum, et ce, dès le début de la conception. Ravi Kunju de l’entreprise Altair nous expliquait qu’il existe aujourd’hui 3 types de post-traitement : thermique, mécanique et thermomécanique. Le premier vient par exemple éliminer les contraintes résiduelles tandis que le post-traitement mécanique sera consacré entre autres à la suppression des structures de supports. Il précise : « Le post-traitement peut avoir un impact significatif sur l’orientation des pièces, la suppression du support, l’imbrication de plusieurs pièces, etc. La conception pour la fabrication additive (DFAM) doit prendre en compte tous ces aspects en liaison avec le volume et les coûts de production. »
Daniel conclut en conseillant de réduire le nombre de supports d’impression (voire de les éliminer), surtout en fabrication additive métal. Il ajoute : « Une autre façon consiste à intégrer ces supports – c’est le travail du concepteur et non celui de l’opérateur machine – à la conception même de la pièce. On n’aura plus besoin de les enlever ! De nos jours, très peu de pièces ont été conçues de cette façon, mais c’est une idée prometteuse. »

L’idéal serait d’intégrer les supports d’impression directement dans le design de la pièce (crédits photo : Altair)
Les conseils de nos experts
Terminons avec quelques conseils pratico-pratiques de nos trois experts qui pourront vous guider dans vos étapes de conception en fabrication additive. Samuel vous conseille de toujours « analyser les faiblesses de votre design afin de définir la meilleure orientation d’impression. Encore mieux, réfléchissez à l’orientation d’impression pendant que vous modélisez votre objet pour optimiser chaque angle, chaque épaisseur et chaque support.«
Ravi vous recommande la chose suivante : « Il est essentiel de comprendre les critères de performance, le volume de production, la taille de la pièce et les coûts en tant que facteurs de sélection du processus d’impression 3D. » Daniel est quant à lui très enthousiaste quand il s’agit de DfAM : « N’ayez pas peur et n’attendez pas : adoptez l’impression 3D le plus rapidement possible! «
Et vous, quelles techniques de conception utilisez-vous pour la fabrication additive (DfAM) ? Partagez votre avis dans les commentaires de l’article ou avec les membres du forum 3Dnatives. N’hésitez pas à nous suivre sur Facebook ou Twitter !
*Crédits photo de couverture : HP/Motus
Excellent article pour mieux comprendre ce qu’est la conception/fabrication additive.