Un métamatériau pour l’impression 3D de pièces d’avions et de fusées
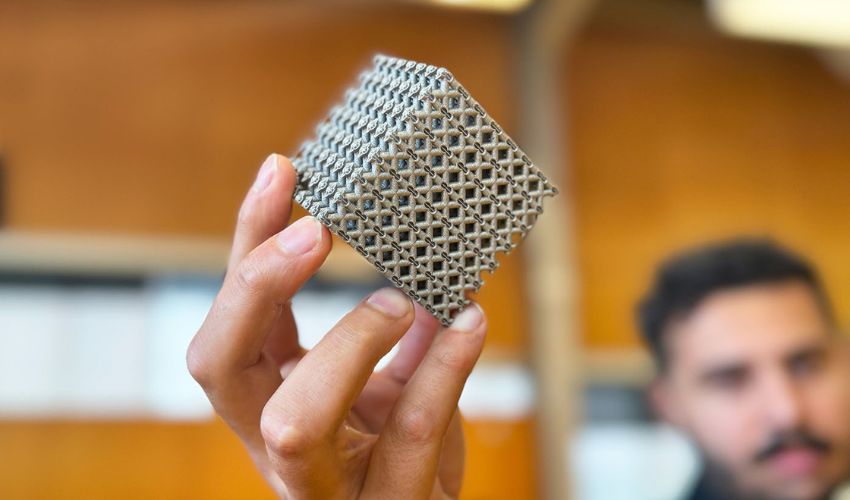
La nature est une source d’inspiration pour de nombreux chercheurs ; ils s’appuient sur le comportement des plantes ou des animaux pour imaginer de nouveaux concepts et matériaux. C’est le cas de cette équipe à l’université RMIT : elle a mis au point un métamatériau imprimé en 3D dont la structure en treillis rappelle la résistance du corail Tubipora musica, aussi appelé corail « orgue de mer ». Celui-ci serait particulièrement utile dans l’industrie aérospatiale, notamment pour produire des pièces d’avions ou de fusées plus résistantes et légères.
Le métamatériau imprimé en 3D a été fabriqué au RMIT Advanced Manufacturing Precinct à partir d’un alliage de titane en utilisant le procédé d’impression 3D de fusion laser sur lit de poudre (LPBF), ce qui n’est pas une nouveauté en soi. Le matériau doit plutôt son côté innovant du fait qu’il s’agit d’un matériau artificiel doté de propriétés uniques qui n’existent pas dans la nature. Le métamatériau, qui correspond à un cube de titane en treillis, se caractérise en effet par un rapport résistance/poids qui n’existe pas dans la nature et allie ainsi légèreté et solidité. La particularité de la structure est qu’elle est 50 % plus résistante que l’alliage de magnésium coulé WE54 suivant, qui présente une densité similaire et est utilisé dans le domaine de l’aérospatiale. Grâce à la nouvelle structure, les points faibles du cube subissent deux fois moins de contraintes et les fissures qui pourraient apparaître sont déviées le long de la structure. Il en résulte une structure plus robuste qui recèle un potentiel pour la fabrication de pièces d’avions ou de fusées ainsi que d’appareils médicaux comme les implants osseux, notamment grâce à ses propriétés de biocompatibilité ou de résistance à la corrosion et à la chaleur.
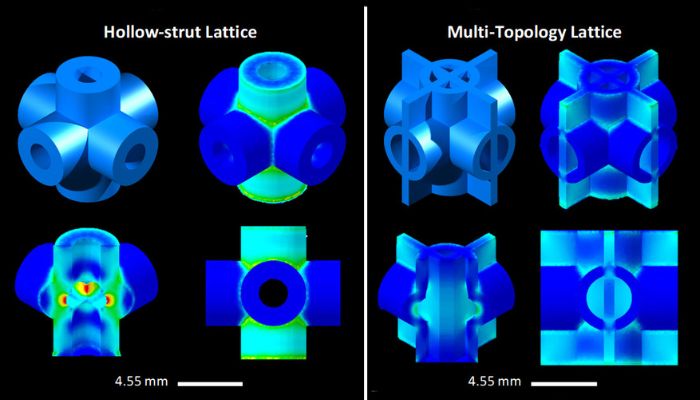
Concentration des contraintes en rouge et en jaune sur la grille (à gauche), tandis que (à droite) la nouvelle structure de la grille répartit les contraintes de manière plus uniforme.
Vers un métamatériau plus stable ?
Cependant, selon Ma Qian, professeur au RMIT, les tentatives de reproduire les « structures cellulaires » creuses dans les métaux, qui durent depuis des décennies, ont échoué en raison de problèmes de fabricabilité et de concentration des contraintes sur les parties internes des entretoises creuses, ce qui a entraîné des défaillances prématurées. Selon Qian, dans l’idéal, la contrainte devrait être uniformément répartie dans tous les matériaux cellulaires complexes. Cependant, dans la plupart des topologies, il est courant que moins de la moitié du matériau supporte principalement la charge de compression, tandis que la plus grande partie du matériau est structurellement insignifiante, poursuit-il. L’utilisation de la fabrication additive a permis de dépasser ces limites et de mieux répartir la charge tout en augmentant la résistance. « Nous avons conçu une structure de grille tubulaire creuse à l’intérieur de laquelle passe une fine bande. Ces deux éléments combinés montrent une force et une légèreté qui n’ont jamais été vues ensemble dans la nature », explique Qian. « En associant efficacement deux structures de grille complémentaires pour répartir uniformément la tension, nous évitons les points faibles où la tension se concentre normalement ».
L’auteur principal de l’étude et doctorant du RMIT, Jordan Noronha, ajoute : « Comparé à l’alliage de magnésium coulé le plus résistant actuellement disponible dans les applications commerciales et nécessitant une résistance élevée avec un poids faible, il a été démontré que notre métamatériau en titane, d’une densité comparable, est beaucoup plus résistant ou moins susceptible de subir des déformations permanentes sous l’effet de la pression, sans parler du fait qu’il est plus facile à fabriquer. »
La nouvelle structure a le potentiel d’être produite dans une taille de plusieurs millimètres ou mètres, en utilisant différents types d’imprimantes. De plus, l’équipe de recherche souhaite à l’avenir utiliser le matériau dans des environnements où règnent des températures plus élevées. L’adoption par l’industrie pourrait toutefois prendre encore un certain temps, car la technologie utilisée pour produire le nouveau matériau n’est pas encore disponible pour le grand public. Pour plus d’informations, cliquez ICI.
Que pensez-vous de ce métamatériau imprimé en 3D ? Partagez votre avis dans les commentaires de l’article. Retrouvez toutes nos vidéos sur notre chaîne YouTube ou suivez-nous sur Facebook ou Twitter !
*Crédits de toutes les photos : RMIT University
A chaques articles de 3Dnatives je Rêve de fabriquer Tout de ma maquette de Drone figther en Vrai !!!! entierement reconfigurable rapidement aux missions dédiées !!!
Cela me serais une Révolution!!! Mais l « Actualité » n est pas aux créateurs free en France!!!
Merci Thank you merci a vous et à Tous !