3D-gedruckte Absaugpaneele sorgen für saubere Luftfahrt
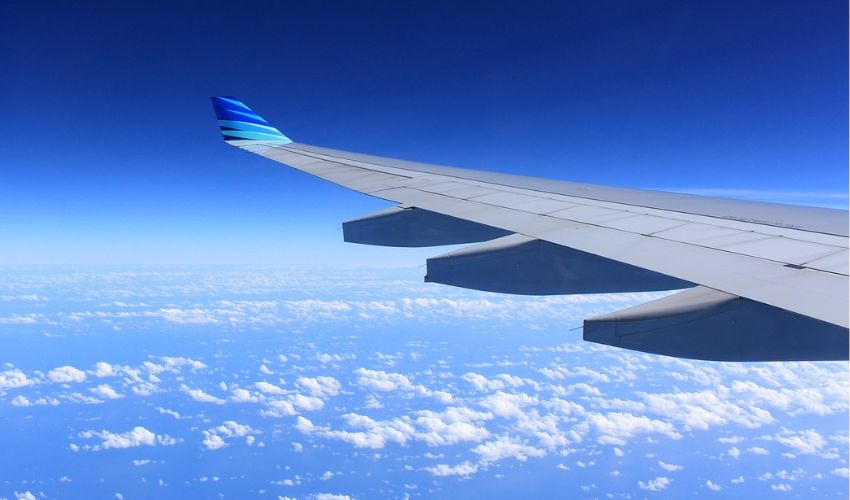
Eines der größten Ziele der Luftfahrt ist es, sichere, leistungsfähige und effiziente Flugzeuge zu entwickeln. Effizient sollen die Flugzeuge vor allem auch im Hinblick auf ihren Energieverbrauch sein. Kann dieser nämlich reduziert werden, verringert sich auch der Ausstoß von Emissionen, was zu einer „saubereren“ Luftfahrt beiträgt. Um all diese Ziele zu erreichen, ist es notwendig, das Prinzip des Grenzschichtverhaltens der Strömung vollends zu verstehen und zu berücksichtigen. Dieses bezieht sich auf die Eigenschaften und das Verhalten der Luftströmung in unmittelbarer Nähe einer festen Oberfläche. Konkret: Wie verhält sich die Strömung zum Beispiel in der Nähe der Tragfläche eines Flugzeugs? Direkt an der Oberfläche ist die Strömung null und geht bis zur freien Strömungsgeschwindigkeit der Umgebung über. Die Grenzschicht ist also eine sehr dünne, aber entscheidende Schicht, welche ausschlaggebend für Sicherheit, Leistung und Effizienz des Flugkraftwerks ist. In einem Test der TU Braunschweig ist es nun durch 3D-gedruckte Absaugpaneele gelungen, die Grenzschicht und deren Verhalten zu optimieren und die Paneele erfolgreich zu testen.
Am Projekt zu den 3D-gedruckten Absaugpaneelen und der anschließenden Testung arbeitete eine Forschungsgruppe des Exzellenzclusters SE²A. Dieser SE²A „Sustainable and Energy Efficient Aviation”-Cluster zielt darauf ab, die zukünftige Luftfahrt effizient zu gestalten und begegnet den derzeitigen Anforderungen mit Innovation. Daran beteiligt sind die TU Braunschweig, das Deutsche Zentrum für Luft- und Raumfahrt und weitere Bildungseinrichtungen eines übergreifenden Forschungsbereichs für Mobilität. Für die Experimente der 3D-gedruckten Absaugpaneele nutzte die Forschungsgruppe einen Niedergeschwindigkeits-Windkanal der Stiftung Deutsch-Niederländische Windkanäle und kooperierte für die Vorab-Tests auch mit dem Institut für Strömungsmechanik. In diesem Windkanal ist der Turbulenzgrad sehr gering und er ermöglichte so ein simuliertes Grenzschichtverhalten der Strömungen, wie sie beim Freiflug vorherrschen. Dadurch waren die idealen Bedingungen für die Tests gegeben.
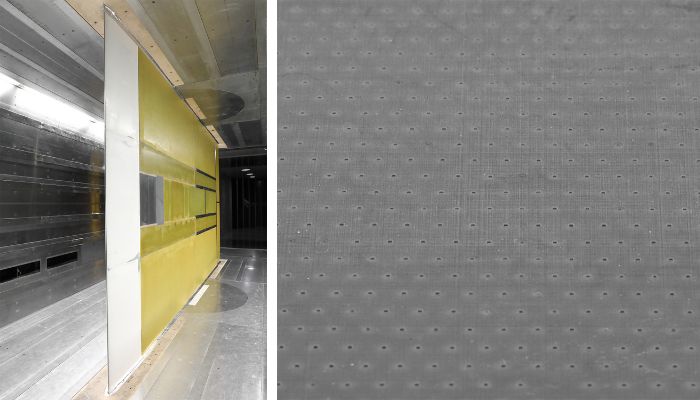
Links: Die ebene Platte in der Messstrecke des Niedergeschwindigkeits-Windkanals Braunschweig (NWB) mit eingebautem Absaugpaneel (mitte, grau). Hier werden 3D-gedruckte, mikroperforierte Paneele auf ihr Grenzschichtverhalten hin untersucht. Rechts: Mirkoperforierte Oberfläche des Absaugpaneels. (Bild: Hendrik Traub/TU Braunschweig)
Um die Effizienz der 3D-gedruckten Absaugpaneele nachzuweisen, musste auch ein hochmodulares Laminarmodell angewendet werden. Dazu wurden die Absaugeflächen aus dem 3D-Drucker mikroperforiert, das heißt mit winzig kleinen Löchern versehen. Infolgedessen konnte eine Laminarisierung der Grenzschicht erreicht werden, denn ein kleiner Teil der Grenzschicht wird durch die Löcher in der Oberfläche der Paneele abgesaugt und die Grenzschicht so stabilisiert. Die Paneele aus dem Drucker mit ihrer perforierten Oberfläche tragen so dazu bei, dass sich die Grenzschicht von aerodynamischen Körpern verändert, indem der laminarturbulente Umschlag stromabwärts verschoben wird und sich der Anteil der laminaren Grenzschicht erhöht. Das hat zur positiven Folge, dass weniger Luftreibung verursacht wird. Bei einer laminaren Grenzschicht ist die Luftreibung bis zu 90 % geringer als bei einer turbulenten Grenzschicht. Die Luftreibung ist insofern ein wichtiger Parameter, als dass sie für 50 % des Gesamtwiderstandes eines Verkehrsflugzeugs verantwortlich ist. „Die laminare Strömungskontrolle ist also eine Möglichkeit, den Treibstoffverbrauch und damit auch die Emissionen von Verkehrsflugzeugen signifikant zu reduzieren“, erläutert Hendrik Traub von der TU Braunschweig, zuständig für die Fertigung der 3D-gedruckten Oberflächen.
3D-gedruckte Absaugpaneele mit Startschwierigkeiten
Entscheidend an diesem Erfolg war auch die Herstellungsmethode, in diesem Fall die additive Fertigung. Bisher wurden Absaugpaneele in F&E aus Edelstahl- oder Titanbelchen gefertigt, die durch Laser mikroperforiert wurden. Dadurch konnten bereits erfolgreiche Entwicklungen umgesetzt und getestet werden. Werden diese Paneele im Anschluss aber gekrümmt, fallen mehrere Arbeitsschritte an. Der 3D-Druck hingegen ist effizienter in der Fertigung und erlaubt die einfachere Umsetzung von unterschiedlichen Geometrien und Komplexitäten. Durch das additive Verfahren konnten im Fall der Absaugpaneele Geometrien, Perforationen und Unterstrukturen in einem Fertigungsschritt kombiniert werden.
Allerdings war die Herstellung der Mikroperforationen mit einem Durchmesser von unter 250 Mikrometer herausfordernd, wie Hendrik Traub erklärt: „Das Finden einer geeigneten Perforationsgeometrie hat entsprechend einen signifikanten Teil unserer Forschungsarbeit ausgemacht. Die Möglichkeit, solche Oberflächen zu drucken, erlaubt jetzt dreidimensional gekrümmte Absaugoberflächen schnell und kostengünstig herzustellen. Das ist sowohl für die Wissenschaft als auch für Segel-, Leicht- und Verkehrsflugzeuge interessant.“ Auch war es anfangs kein Leichtes, ein geeignetes 3D-Druckverfahren zu finden und die Absaugpaneele im Anschluss daran ausgiebig zu testen. Die Vorarbeiten nahmen rund vier Jahre in Anspruch. „Zunächst haben wir verschiedene 3D-Druckprozesse auf deren Eignung für die Fertigung von Absaugpaneelen untersucht. Anschließend haben wir druckbare Perforationsgeometrien und Unterstrukturen analysiert. Dabei müssen die Perforationsgeometrien das Drucken von sehr kleinen Löchern erlauben und die Unterstrukturen eine dichte, aber durchströmbare Unterstützung der mikroperforierten Haut erlauben, ohne die Löcher wieder zu blockieren.“
Beim Testen der Paneele startete die Forschungsgruppe mit kleinen Prototypen und begann dann, diese hochzuskalieren. Wiederum sahen sich die Forscher mit Herausforderung konfrontiert, die in diesem Stadium die Software-Grenzen betraf. Denn obwohl die geometrische Struktur der Paneele mit ihrer minimal perforierten Oberfläche nun druckbar war, ließ die CAD-Software die Dimensionen kaum zu und die Forscher mussten auf eigens programmierte Bibliotheken umsteigen. Traub erklärt: „Die Herausforderung liegt im extremen Kontrast zwischen sehr präzisen geometrischen Details, die bis auf wenige Mikrometer aufgelöst werden müssen, und den verhältnismäßig großen Dimensionen der Absaugpaneele selbst.“
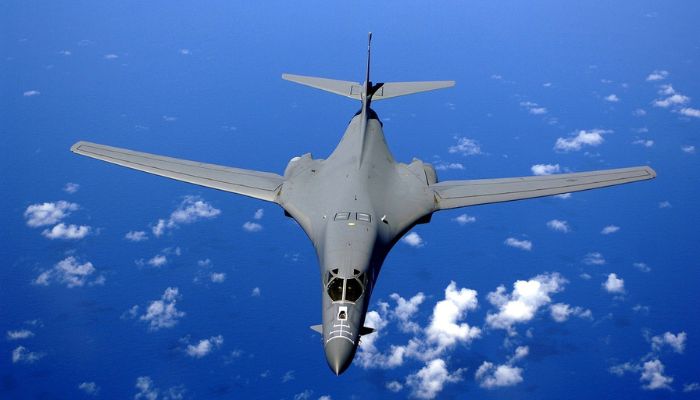
Ziel des Exzellenzclusterst ist es, die Luftfahrt effizienter zu machen und die Emissionen zu verringern. (Bild: Pixabay)
Nachdem auch diese Hürde überwunden war, konnten die 3D-gedruckten Absaugpaneele erfolgreich im Windkanal getestet werden. Der nächste Schritt beinhält nun, die zweite Version der Paneele mit verbesserter Oberfläche für Off-Designfälle ohne Absaugung zu schaffen. Dadurch soll sich die Effektivität des Absaugpaneels erhöhen und es kann auch ohne Absaugung eine ähnliche laminare Lauflänge erzielt werden. Das ist wichtig für Fälle, in denen die Absaugung in einer Flugphase ausgeschaltet oder ausgefallen ist. Auch diese Versuche werden im Niedergeschwindigkeits-Windkanal Braunschweig getestet. Die getesteten Modelle sollen dann die Basis für die ersten dreidimensional gekrümmten Absaugpaneele eines voll-laminaren Flügelmodells liefern. Dieses sollte bis 2025 gefertigt und entwickelt werden. Mehr dazu finden Sie HIER.
Was halten Sie vom Ansatz der 3D-gedruckten Absaugpaneele für eine sauberere Luftfahrt? Lassen Sie uns gerne einen Kommentar da, oder teilen Sie es uns auf Facebook oder LinkedIN mit. Möchten Sie außerdem eine Zusammenfassung der wichtigsten Neuigkeiten im 3D-Druck und der additiven Fertigung direkt und bequem in Ihr Postfach erhalten? Dann registrieren Sie sich jetzt für unseren wöchentlichen Newsletter.
Titelbildnachweis: Pixabay