#3DStartup: Phase3D and its Real-Time Inspection Solution for 3D Printing
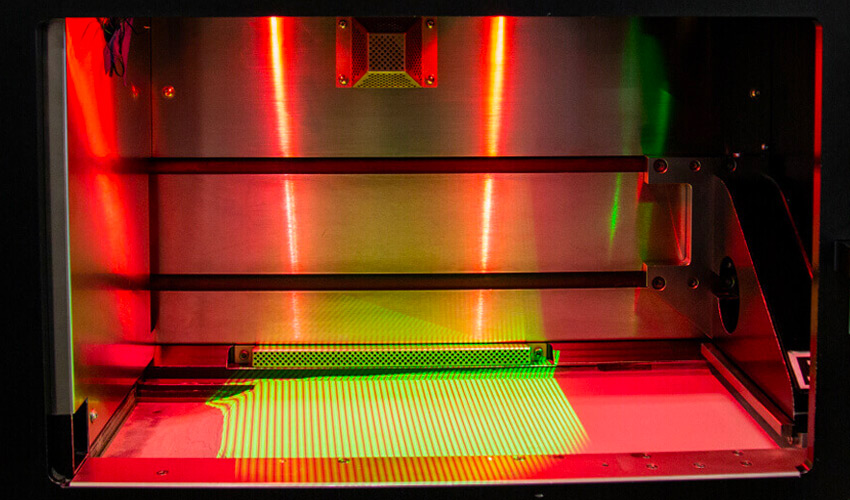
A key issue in the additive manufacturing industry is the quality of the final parts. Depending on the 3D printing technology used and the intended application, this could be more or less affordable. Furthermore, when it comes to powder bed-based systems, it is essential to have a broad understanding of the technology. This goes from the design of the models to the procurement of the final parts, in order to minimize errors. In this context, Chicago-based startup Phase3D has developed a solution for real-time inspection of the manufacturing process. This system is compatible with Powder Bed Fusion technologies, as well as with binder jetting. We spoke with the CEO to learn more about this solution and how it can detect anomalies during additive manufacturing to obtain the best quality.
3DN: Could you introduce yourself and your connection to 3D printing?
My name is Niall O’Dowd and I am the CEO and founder of Phase3D. I have been fascinated by 3D printing since 2010 when I first had access to the technology. My preoccupation with 3D printing since then has been twofold — both as a hobby and as an industrial manufacturing tool. Growing up I was obsessed with CAD and seeing my first sculpture design come to life using a desktop 3D printer (MakerBot Cupcake) for my high school art show was incredible. I designed a multi-piece assembly (pictured below) and it took several design and print iterations to get the fit right. I did not realize it at the time, but this experience of going from imagination to reality so quickly and fluidly proved to be the start of my journey with additive technologies.
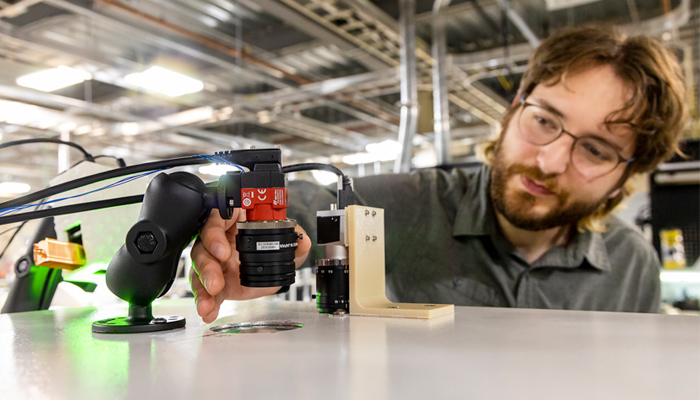
Niall O’Dowd, CEO of Phase3D.
My passion for designing sculptures turned into a love for engineering, leading me into a B.Sc. in mechanical engineering. During my undergraduate degree, additive technologies advanced rapidly in nature and scope across a range of industrial applications. Additive Manufacturing (AM) processes proved to be an invaluable resource for my robotics classes at Rochester Institute of Technology.
I decided to continue my education with a PhD in structural health monitoring (SHM) — the field of non-destructive evaluation to detect and predict failures in manufactured components. Funded by the US Department of Energy, I invented an in-situ monitoring technology which created a repeatable, calibratable, and unit-based SHM system to find micron sized defects formed during AM process. On successful completion of my PhD, I took the next step, which was to commercialize this technology with the founding of Phase3D.
3DN: What is Phase3D? How did it come about?
Phase3D is a startup, founded in 2021, funded by the Department of Energy’s Advanced Manufacturing Office, the National Science Foundation and the Department of Defense. Our mission is to empower users of Powder Bed Fusion (PBF) AM processes by offering a trusted part quality assurance technology. We focus specifically on critical markets, including aerospace, medical, nuclear, energy, and automotive.
The company is committed to providing the advanced manufacturing industry with data-driven methods for part quality assurance. Our flagship product, Fringe, is a computer vision system that inspects every layer of a build for any PBF AM process, to classify defects and certify part quality.
Our team has witnessed first-hand the power of AM and the impact our Fringe technology can make on the world. Part reliability, repeatability and quality issues continue to hinder wider adoption of AM for many potential applications. I founded Phase3D to help accelerate uptake and to enter the next phase of AM: production level parts. We believe that with accurate and reliable in-situ inspection, backed by data, parts can be certified in real time and subsequently integrated more quickly into the supply chain.
In addition, as AM continues to expand further into production for critical use parts, standardization and certification becomes a prerequisite. While traditional manufacturing has tested and trusted quality control measures, the speed of innovation of AM has seen certification and quality standards lag behind somewhat. This is where Phase3D comes in.
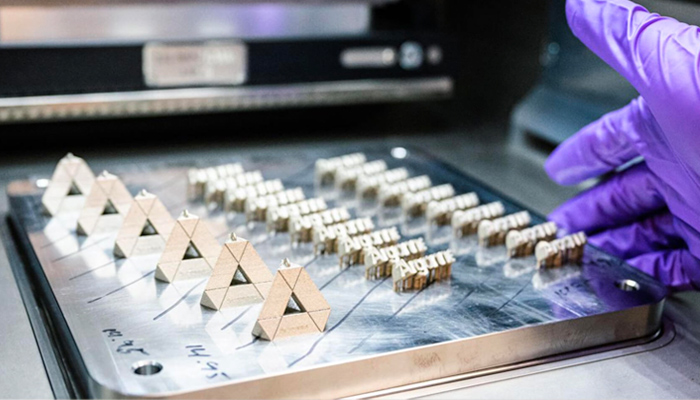
Phase3D helps accelerate industrial-scale additive manufacturing.
3DN: Could you tell us more about your solution “Fringe”? How does it work?
Fringe is a real time in-situ inspection solution for powder-based AM processes that provides companies with objective measurements of the production process. The technology uses structured light to measure the powder and melted, or bound, surface in true measurements, microns. Users of Fringe have the ability to collect and analyze data from every layer of every part on every AM build. Phase3D is working to remove assumptions about AM processes that hinder adoption.
Fringe is used by technicians, engineers, designers, managers, and quality assurance teams for various advanced applications to gather high-quality and reliable data. On the shop floor, technicians use Fringe to reduce lead times and to identify the source of build failures, when they occur. Fringe supplies actionable data to part designers to accelerate design iterations with objective data of what occurred, and where, during the build. Managers use Fringe data to increase machine utilization, and to ensure overall part quality for end-use parts, which can subsequently be passed to the QA team.
3DN: What benefits does it offer to the 3D printing process?
Fringe offers quantifiable, repeatable, and calibratable measurements for PBF AM processes. By adding objective measurements to AM build processes, additive technologies can finally reach their true potential for critical use parts at production scales. A company that installs Fringe can make critical decisions faster. One example is identifying when a part will fail due to any anomaly that Fringe identifies during the build. The technician can stop the build, fix the problem, and restart the process in minutes to hours instead of identifying the failed part during QA and wasting weeks if not months.
Phase3D’s in-situ monitoring system removes assumptions that a layer of powder is flat during the build process by providing accurate measurements for the powder spreading and melting process. This enables users to understand their manufacturing process better and to improve productivity. The goal, someday soon, is to achieve born qualified parts for critical use applications.
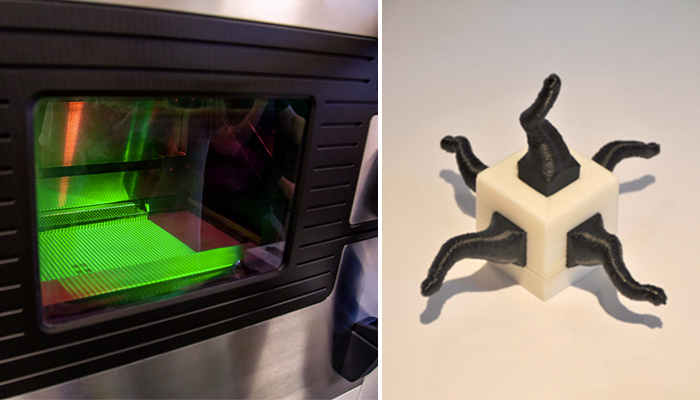
Fringe shows anomalies in the 3D printing process with objective and quantifiable data.
3DN: What markets and applications are Phase3D targeting?
Phase3D is focused on adding value to the cutting edge of AM, for R&D and production facilities. Research institutions such as NASA Marshall Space Flight Center, Air Force Research Lab, and Oak Ridge National Lab are using Fringe to deeply understand powder and part interaction, record process anomalies, and correlate printing conditions to part performance. Production industries where part quality and efficiency is critical — and validated — such as the aerospace, medical device, nuclear, and energy industries, benefit greatly from the documented, data-driven quality systems that are available with Fringe.
3DN: Any last words for our readers?
We are on a mission to empower the AM industry by offering a trusted part quality assurance technology. Our team will be attending industry events throughout 2024. To stay up to date on everything we are doing, check out our website. Finally, we are continually growing our team of engineers, developers, and thought leaders, so check on LinkedIn for job postings if you want to work with a passionate and dynamic team.
What do you think of the solution developed by Phase3D for additive manufacturing? Let us know in a comment below or on our LinkedIn, Facebook, and Twitter pages! Don’t forget to sign up for our free weekly newsletter here, the latest 3D printing news straight to your inbox! You can also find all our videos on our YouTube channel.
*All Photo Credits: Phase3D