Les thermoplastiques hautes performances : PEEK, ULTEM et autres polymères
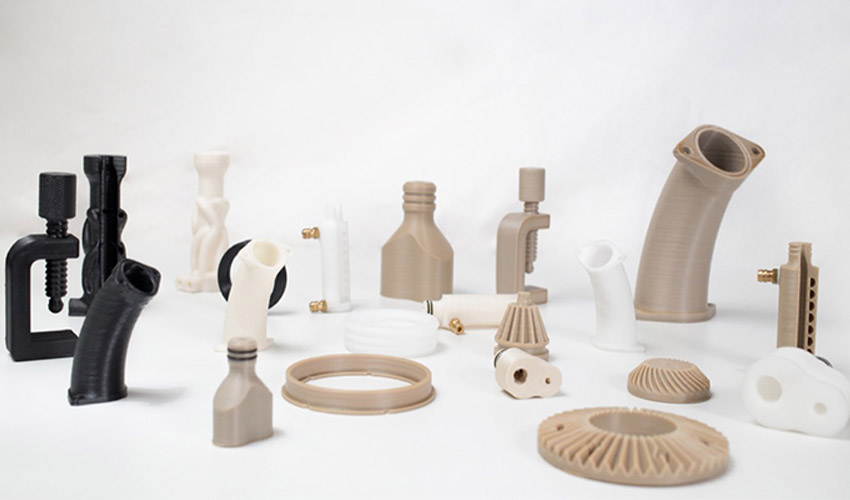
Ces dernières années, les thermoplastiques hautes performances sont devenus un sujet brûlant dans l’impression 3D et leur marché connaît une croissance rapide. Ces matériaux sont attrayants dans l’industrie en raison de leur résistance et de leur légèreté, et il en existe un certain nombre qui peuvent être utilisés pour la fabrication additive. Un exemple est le polyaryléthercétone (PAEK), une famille de plastiques semi-cristallins capables de résister à des températures élevées tout en conservant une résistance considérable. Le PAEK est principalement utilisé sous forme de polyétheréthercétone (PEEK) et de polyéthercétonecétone (PEKK), deux matériaux à haute rigidité. Une alternative beaucoup moins chère, le polyétherimide (PEI), également connu sous le nom d’ULTEM, est également devenu de plus en plus courant. Mais que sont exactement les plastiques hautes performances ? Comment les imprimer ? Qui sont les fabricants ? Le guide suivant des familles PAEK et PEI vous dira tout ce que vous devez savoir sur ces matériaux.
Production et propriétés des polymères hautes performances
La première chose à savoir sur les polymères hautes performances est que même s’ils partagent des propriétés communes, ils ne sont pas tous exactement les mêmes. Cependant, en général, les thermoplastiques hautes performances, en particulier le PEEK, sont aussi résistants que l’acier et 80 % plus légers que le métal, ce qui les rend très recherchés dans l’industrie manufacturière. En plus de leur résistance mécanique et thermique exceptionnelle jusqu’à 250 °C en fonctionnement continu, les matériaux PAEK sont, contrairement à la plupart des autres plastiques, également résistants à la dissolution dans les huiles et autres substances. En cas d’incendie, presque aucun gaz ni vapeur nocive n’est libéré.
Et bien qu’ils soient de plus en plus répandus dans la fabrication additive, il est indéniable que leur croissance a été plus lente que celle des autres polymères. En effet, ces matériaux existent depuis plus de trois décennies, notamment via le moulage par injection ou l’usinage. Initialement, Stratasys était la seule entreprise capable de produire des imprimantes capables de supporter les températures élevées requises pour faire fondre les polymères PAEK et PEI. Cependant, à mesure que le marché commençait à s’ouvrir, d’autres entreprises ont également eu l’occasion d’expérimenter ces imprimantes, ce qui a conduit à une commercialisation massive de leurs inventions. Avec le temps et la réduction des barrières à l’entrée, nous constatons que de plus en plus d’entreprises se lancent dans ce domaine et commencent à fabriquer des imprimantes 3D capables de traiter les thermoplastiques PAEK.
Un autre matériau, le PEI, a été développé pour la première fois par la division plastiques de General Electric à la fin des années 1980. Cependant, en 2007, SABIC, l’une des plus grandes sociétés publiques d’Arabie Saoudite, a acquis la division et avec elle les droits sur la marque ULTEM. Comme ce matériau représente une alternative moins coûteuse au PEEK, il a immédiatement suscité un grand intérêt d’un point de vue financier. Combiné avec ses diverses propriétés physiques importantes, telles que la résistance élevée à la chaleur, aux solvants et aux flammes, la rigidité diélectrique et la conductivité thermique, il représentait une excellente solution pour les projets d’ingénierie. L’ULTEM est devenu un matériau privilégié pour les applications d’ingénierie avec des exigences très élevées, telles que dans l’industrie aérospatiale.
L’impression 3D avec des plastiques hautes performances
En général, les polymères PAEK et PEI sont imprimés en utilisant la technologie FDM (Fused Deposition Modeling) ou le procédé SLS (Selective Laser Sintering). Cependant, compte tenu de la capacité de ces polymères à haute température, il est compréhensible qu’aucune imprimante 3D ordinaire ne puisse traiter ces filaments. Une imprimante 3D PAEK/PEI doit disposer d’une buse capable de supporter des températures supérieures à 300°C, car c’est le point de fusion de ces polymères. De plus, le plateau chauffant doit atteindre au moins 150 °C pour que l’objet puisse être retiré. Enfin, des mécanismes de refroidissement plus puissants sont nécessaires pour garantir le bon équilibre de température dans la chambre fermée.
Le post-traitement des thermoplastiques hautes performances est nécessaire et, comme pour toute pièce imprimée FDM complexe, des structures de support sont requises. Cependant, avec le PAEK et le PEI, il peut être difficile de retirer le support en raison de la rigidité du produit final. Par conséquent, une gamme d’outils est souvent utilisée pour terminer la pièce.
Avec le procédé SLS, en revanche, la pièce est imprimée presque parfaitement sans avoir besoin d’outils supplémentaires. Cependant, les fabricants doivent prendre en compte la déformation. Une fois qu’un objet cesse de s’imprimer et que la température dans la chambre baisse, les polymères ont tendance à rétrécir. Pour cette raison, le PAEK et le PEI sont très populaires lors de l’impression de petits objets, mais plus la pièce est grande, plus l’effet de déformation est fort. Bien que cela puisse être contrôlé dans une certaine mesure en optimisant les paramètres d’impression clés tels que la vitesse et la température, cela reste un défi.
Par ailleurs, l’utilisation de thermoplastiques hautes performances est encore loin d’être pleinement développée. Certains aspects du processus de fabrication sont encore travaillés et continuellement améliorés. Cependant, de nouvelles innovations améliorent constamment cette expérience. Un certain nombre d’entreprises travaillent actuellement sur une solution FDM qui consiste à imprimer la structure de support de l’objet à partir d’un matériau différent afin de pouvoir la retirer plus rapidement et plus facilement après l’impression. De plus, d’autres sociétés comme Kimya ont commencé à proposer des combinaisons de matériaux pour tirer le meilleur parti de plusieurs matériaux. De cette manière, le produit final peut être constitué, par exemple, de 70 % de PEEK et de 30 % de fibre de carbone.
Les applications possibles
Comme on peut s’y attendre, une famille de matériaux possédant autant de propriétés importantes est utile dans diverses industries. L’industrie automobile a rapidement commencé à utiliser les capacités uniques du PAEK et du PEI pour une variété d’applications. L’un des domaines dans lesquels ces matériaux ont le plus grand impact est celui de la production d’outillages à faible coût et à grande vitesse pour le moulage par injection, le thermoformage et les montages. Cela permet aux entreprises de produire de petits à moyens volumes à faible coût sans avoir à investir dans une fabrication en gros volume. La production de pièces personnalisées est également de plus en plus demandée car elles peuvent être adaptées selon des exigences spécifiques et peuvent recevoir des modifications complexes qui améliorent leur conception structurelle.
Comme beaucoup d’autres matériaux d’impression 3D, les familles PAEK et PEI sont largement utilisées dans le domaine médical. Le PEEK est connu pour protéger les scanners d’imagerie par résonance magnétique (IRM). Il est également considéré comme un biomatériau avancé utilisé pour les implants médicaux, les tiges de renforcement et les dispositifs de fusion vertébrale. Parce qu’il peut résister à l’eau bouillante et à la vapeur surchauffée, il est idéal pour les produits qui doivent être stérilisés à des températures extrêmement élevées.
Les thermoplastiques hautes performances sont également couramment utilisés dans l’industrie aérospatiale. La résistance chimique, le rapport résistance/poids élevé et les faibles niveaux d’incendie, de fumée et de toxicité font de ces polymères des substituts idéaux au métal, couramment utilisé pour les pièces et les outils des engins spatiaux. L’isolation thermo-acoustique, les supports structurels, les supports et entretoises, les fixations, les connecteurs et les systèmes de tuyauterie ne sont que quelques exemples dans lesquels l’ingénierie aérospatiale utilise le PAEK et le PEI, réduisant souvent le poids des pièces de 70 %. Parmi les autres industries qui utilisent des thermoplastiques avancés figurent le transport maritime, le nucléaire, le pétrole et le gaz, et bien d’autres encore.
Principaux fabricants et prix des matériaux
Comme on pouvait s’y attendre, de nombreuses grandes entreprises ont déjà reconnu le changement qui se dessine dans le domaine des thermoplastiques hautes performances dans le domaine de la fabrication additive. Il n’est donc pas surprenant de voir des noms comme Arkema, Lehmann & Voss et Solvay (pour n’en citer que quelques-uns) mentionnés lorsqu’il s’agit de fabriquer des matériaux PAEK. Cependant, en ce qui concerne l’Île-du-Prince-Édouard, la marque ULTEM de SABIC est la seule disponible sur le marché pour le moment.
En ce qui concerne les imprimantes capables de traiter le PAEK et le PEI, le fabricant chinois INTAMSYS a beaucoup retenu l’attention car il propose une gamme d’imprimantes 3D professionnelles et de bureau adaptées aux polymères hautes performances. Mais le néerlandais Tractus3D est également de plus en plus populaire, tout comme le géant allemand EOS, qui a récemment lancé une nouvelle imprimante HTLS (frittage laser à haute température) capable de traiter ces matériaux.
Cependant, comme on peut s’y attendre, ces polymères hautes performances ne sont pas vraiment bon marché. Le PEEK, l’UTLEM et le PEKK font partie des matériaux d’impression 3D les plus chers du marché. Bien que l’ULTEM soit une alternative légèrement moins chère, une bobine de filament de 1 kg commence à plus de 180 € et coûte souvent beaucoup plus cher en fonction de la marque et des propriétés du matériau. Le PEEK coûte désormais souvent entre 270 € et jusqu’à plus de 650 € pour 1 kg de matériau, tandis que le PEKK coûte en moyenne entre 370 € et 460 € pour le même montant.
Si vous êtes intéressé par des filaments fabriqués à partir de ces matériaux, vous devez également garder à l’esprit que vous ne pouvez pas imprimer avec n’importe quelle imprimante. Vous devez investir dans une imprimante spécialement conçue pour les polymères hautes performances, comme mentionné ci-dessus. Ces imprimantes sont également naturellement plus chères qu’un modèle FDM bon marché. Beaucoup commencent à plus de 4 500 € et la plupart sont bien au-dessus. Cependant, au fil des années, nous avons constaté qu’à mesure que le marché se développe, les choix des consommateurs évoluent également. Peut-être verrons-nous dans un avenir proche les prix des imprimantes et des matériaux baisser à mesure que les applications de fabrication additive utilisant des polymères hautes performances se généralisent encore plus.
Que pensez-vous de l’utilisation de polymères thermoplastiques haute performance dans l’impression 3D ? Pouvez-vous imaginer que d’autres secteurs soient également transformés dans un avenir proche ? Partagez votre avis dans les commentaires de l’article. Retrouvez toutes nos vidéos sur notre chaîne YouTube ou suivez-nous sur Facebook ou Twitter !
*Crédits de toutes les photos : ApiumTec