L’impression 3D au service de l’aéronautique
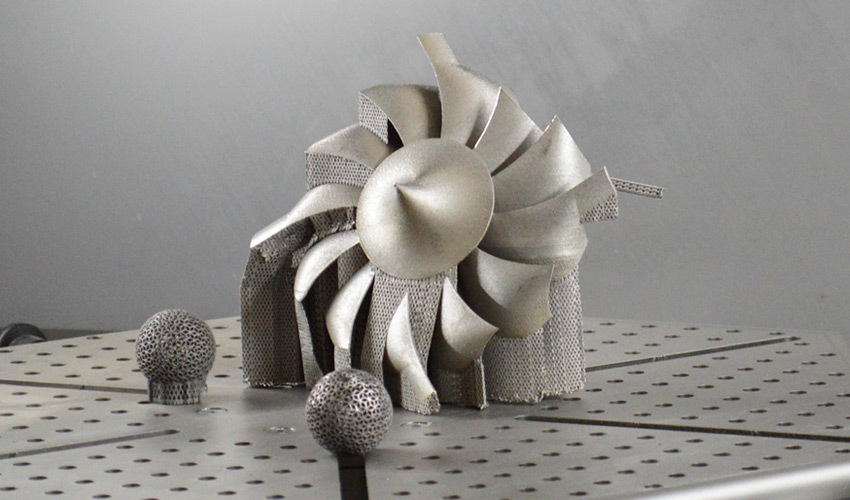
Si cela peut aux premiers abords paraître surprenant, le secteur aéronautique a été l’une des premières industries à adopter l’impression 3D. Initialement utilisée pour le prototypage rapide, la fabrication additive est de plus en plus employée pour produire des pièces d’utilisation finale. Et ce, pour des raisons évidentes. La technologie permet de créer des pièces aux géométries complexes, plus légères et plus solides, une nécessité dans le secteur aéronautique où la résistance et la légèreté sont primordiales. Afin d’illustrer l’importance de l’impression 3D dans le domaine aéronautique, nous avons sélectionné certaines des applications les plus récentes du secteur.
Un caisson d’atterrisseur avant imprimé en 3D
Fin mars dernier, le groupe français Safran nous présentait le premier caisson d’atterrisseur avant en titane, imprimé sur une machine SLM Solutions. Avec son volume imposant de 455 x 295 x 805 mm, la pièce a été conçue en une seule fois – traditionnellement, elle est fabriquée en trois parties avec un bras à 5 axes. Capable de résister aux sollicitations transmises par la roue avant d’un avion d’affaires, le caisson en titane devrait être testé l’année prochaine. Sa masse totale a en tout cas été réduite de 15% grâce à la fabrication additive métal tandis que Safran a considérablement baissé ses temps de production.
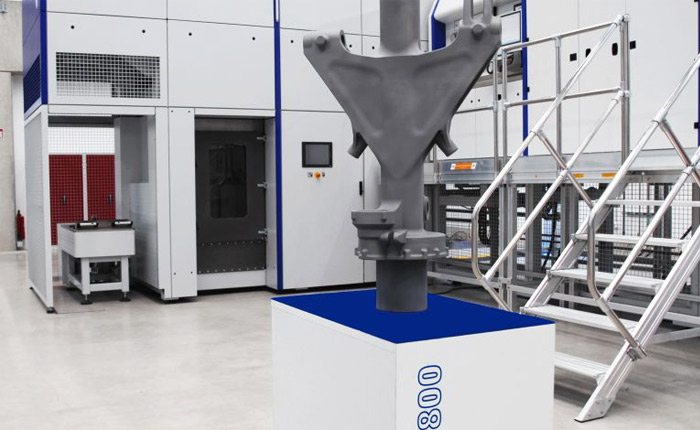
Crédits photo : Safran
L’impression 3D et l’armée de l’air
En Espagne, le Maestranza Aérea de Madrid (MAESMA), un organisme qui gère la maintenance des avions et des hélicoptères de l’armée de l’air espagnole, a intégré la fabrication additive dans ses usines pour développer notamment des outils sur-mesure et tester de nouveaux composants. Il utilise plus spécifiquement des machines FDM pour créer des pièces chargées en fibres de carbone. Ainsi, il a imprimé des pièces d’outillage pour le contrôle des fuites ou encore une clé personnalisée pour le rotor principal de l’hélicoptère. Le MAESMA a également investi dans des solutions de numérisation 3D pour scanner des pièces détachées et constituer un stock de fichiers 3D en cas de maintenance à réaliser.
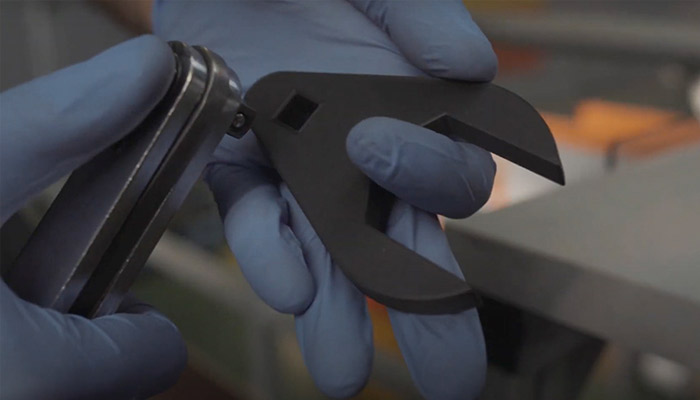
Crédits photo : MAESMA
Norsk Titanium et le Boeing 787
Norsk Titanium US Inc, le leader de la fabrication additive titane destinée à l’industrie aérospatiale, a fourni de nouvelles pièces pour le Boeing 787 Dreamliner. Norsk a utilisé un procédé de dépôt rapide par plasma (RPD) qui consiste à faire fondre un fil de titane dans un nuage de gaz argon. Cette technologie améliore la résistance et la durabilité de la pièce finale et fonctionne de manière similaire au dépôt de matière sous énergie concentrée (DED), bien que le procédé de Norsk utilise un faisceau d’électrons qui lui permet de chauffer la poudre à plusieurs endroits simultanément. Une fois conçues, les pièces ont été certifiées par la FAA (Federal Aviation Administration, une agence gouvernementale américaine qui réglemente l’aviation civile).
Des pièces de luxe imprimées en 3D par Markforged
Récemment, Cabin Management Solutions (CMS) s’est associé à Markforged pour imprimer en 3D des pièces destinées aux avions de luxe. Pour ce faire, les deux entreprise ont eu recours à deux imprimantes 3D Markforged X7, capables de concevoir des pièces renforcées en fibre de carbone et en Kevlar de façon continue. CMS et Markforged ont conçu grâce à ces machines plusieurs pièces personnalisées, notamment des panneaux d’interrupteurs d’éclairage, des chargeurs USB-C et USB-A encastrables, et des supports d’écran tactile réglables. En ce qui concerne les matériaux employées, les deux sociétés ont utilisé du nylon chargé en fibre de carbone baptisé Onyx FR. Au-delà de la finition élégante, les pièces répondent aux exigences strictes de la FAA.
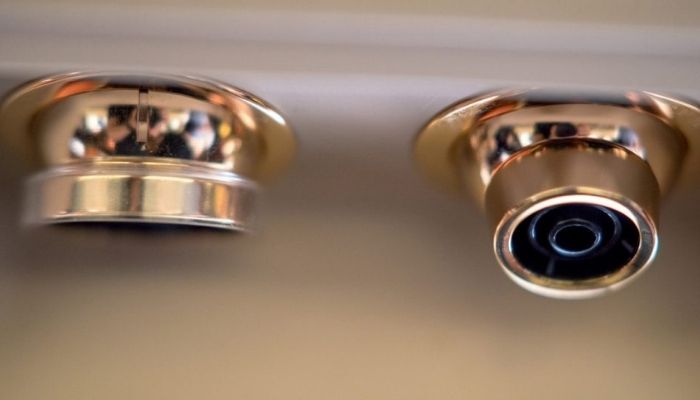
Crédits photo : Markforged
ITP Aero et le Tail Bearing Housing
Fondé en 1989, ITP Aero développe et conçoit des applications destinées au secteur aéronautique. Récemment, à l’aide de la technologie de frittage sélectif par laser (SLS), l’entreprise espagnole a conçu l’une des principales structures du nouveau moteur UltraFan®. Baptisé TBH (Tail Bearing Housing), le composant sera notamment utilisé comme élément de liaison entre l’avion et le moteur. Selon ITP Aero, l’impression 3D a permis de produire des pièces aux géométries complexes, en utilisant seulement de petites quantité de poudre et en réalisant une économie de 25 % de matériaux. La société précise que cette méthode de fabrication est plus respectueuse de l’environnement et réduit l’empreinte carbone lors du processus de production.
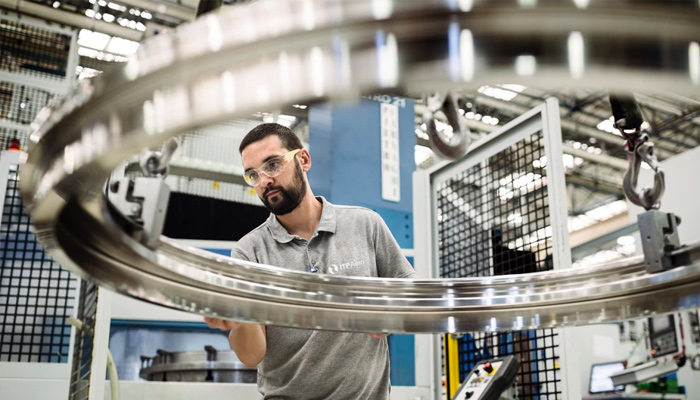
Crédits photo : ITP Aero
Airbus certifie des pièces imprimées en 3D par Materialise et EOS
Outre la technologie d’impression 3D utilisée, le choix du matériau est une étape très importante lors de la conception de pièces. Il est nécessaire que les matériaux possèdent certaines normes et propriétés adaptées à l’aviation. Le PA 2241 FR, un polyamide ignifugé d’EOS, répond à ces exigences et a été certifié par Airbus. Dans le cadre d’une collaboration avec Materialise, une centaine de pièces différentes pour l’avion A350 seront imprimées en 3D à l’aide de la technologie de frittage sélectif par laser (SLS). Les pièces, qui nécessitent un certain niveau de protection contre le feu, la fumée et la toxicité, seront fabriquées à l’aide d’une imprimante 3D EOS P 770. Le volume de production devrait être d’environ 26 000 pièces par an.
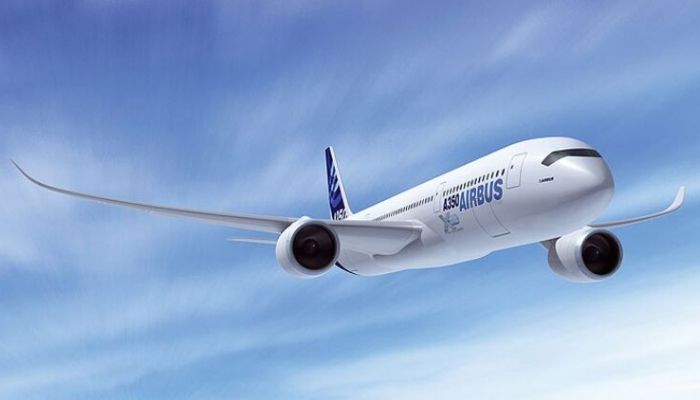
Crédits photo : Airbus
Le centre de fabrication additive de Lufthansa
L’entreprise allemande Lufthansa Technik bénéficie elle aussi des avantages de l’impression 3D. Au sein de la société, la fabrication additive est répartie entre les groupes « Prototypage », « Outillage » et « Vol ». La technologie rend les processus de réparation et de maintenance plus efficaces en interne et est également utilisée pour produire des pièces individuelles et des pièces de rechange pour les composants des avions. En outre, il est possible de produire des outils sur mesure, en utilisant des polymères ou des métaux. Dans la section Vol, chaque pièce imprimée en 3D doit être certifiée et qualifiée avant de pouvoir être utilisée. Le centre vise à accélérer le développement et la production de pièces conçues grâce à la fabrication additive.
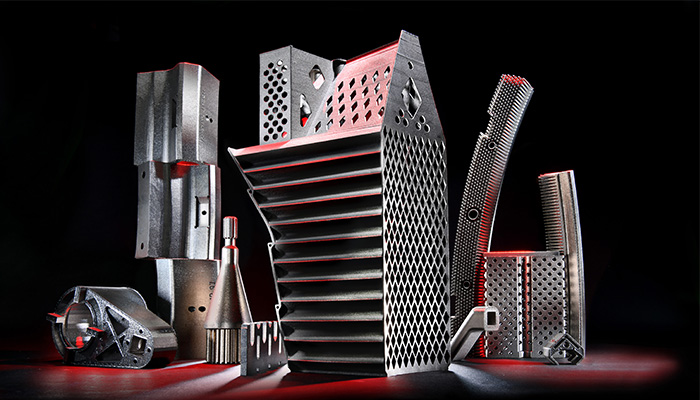
Crédits photo : Lufthansa Technik / Photographe : Jürgen Mai
Saab fabrique et répare des pièces avec l’impression 3D
Saab, une entreprise suédoise spécialisée dans l’aéronautique, l’aérospatial et la défense, a depuis quelques temps intégré la fabrication additive dans son processus de production pour créer des pièces en interne destinées à ses avions de chasse. L’impression 3D permet donc à Saab de créer et réparer des pièces, tout en limitant les délais et coûts de fabrication. En mars dernier, l’entreprise a réalisé l’un de ses premiers vols d’essai avec une pièce imprimée en 3D. Il s’agissait d’une trappe conçue à partir de PA 2200, un polyamide 12, capable de résister aux conditions extérieures. À terme, Saab espère trouver des matériaux encore plus résistants, notamment par rapport au froid glacial présent en haute altitude, et souhaite développer un système d’impression 3D mobile, afin de pouvoir l’amener dans différentes bases.
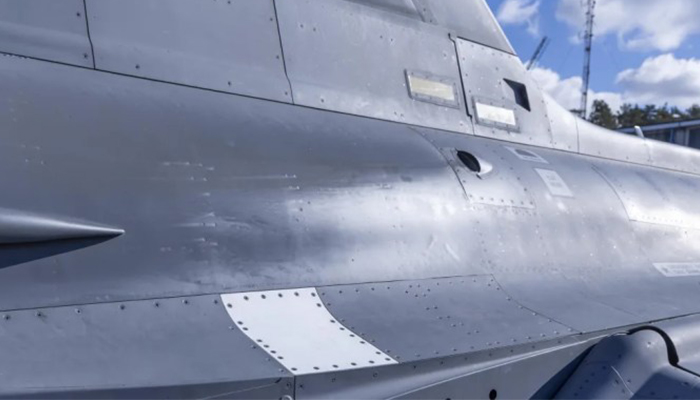
Crédits photo : Saab
Satair et l’impression 3D métal
Filiale d’Airbus depuis 2011, Satair est une entreprise danoise qui produit des composants aéronautiques depuis 1957. Grâce à la fabrication additive, la société a fourni l’année dernière à l’un de ses clients une pièce certifiée et imprimée en 3D métal. L’impression 3D a permis de fabriquer une pièce, la clôture du bout de l’aile d’un avion A320ceo précisément, qui n’était plus disponible chez le fournisseur habituel. Cette méthode de conception a permis selon Satair de réduire les coûts de 45 %, tout en faisant preuve de flexibilité.
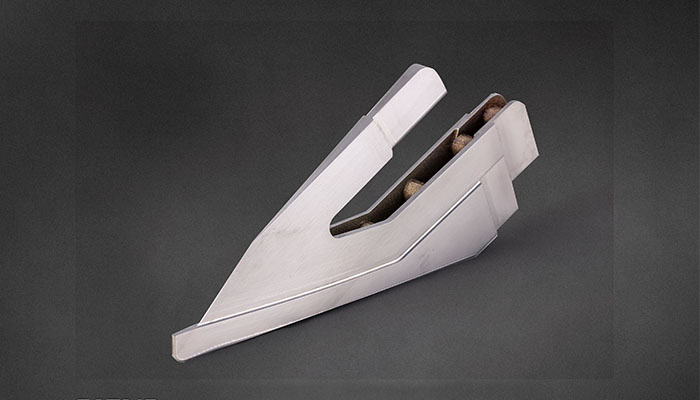
Crédits photo : Satair
Velo3D et le XB-1 Supersonic
Le XB-1 est un avion qui a été mis en service à la fin de l’année 2020 par Boom Supersonic. L’avion à grande vitesse, comparable au Concorde, est considéré comme le premier avion supersonique au monde développé indépendamment. L’avion se distingue par ses 21 composants en titane imprimés en 3D par le fournisseur de solutions d’impression 3D métal Velo3D. Les pièces ont toutes été fabriquées à l’aide de l’imprimante 3D métal Sapphire de Velo3D, qui utilise la fusion laser sur lit de poudre. Les pièces ont été qualifiées puis équipées sur le XB-1, notamment au niveau du moteur et du système de contrôle environnemental.
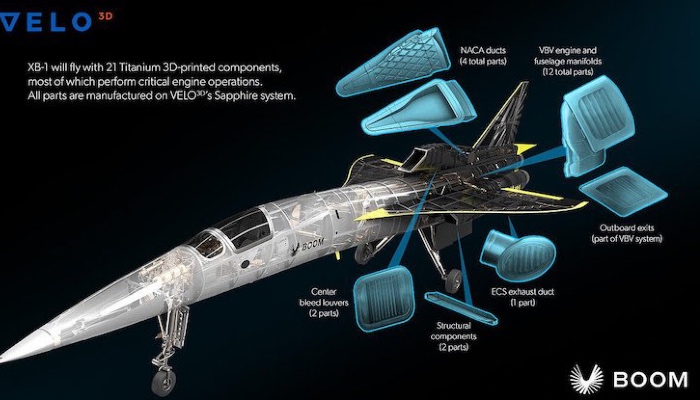
Crédits photo : Velo3D
Le tapis de piste de l’US Air Force
Aux États-Unis, dans le cadre du projet Small Business Innovation Research, Indiana Technology and Manufacturing Companies (ITAMCO) a collaboré avec un professeur de l’université de Purdue, Pablo Zavattieri, pour mettre au point un tapis de piste imprimé en 3D pour les aérodromes expéditionnaires (EAF) utilisés par l’US Air Force. Ces tapis de piste permettent aux avions militaires de décoller et d’atterrir sur n’importe quel terrain plat dans le monde. Traditionnellement, l’armée américaine s’appuyait sur une piste d’atterrissage portable, assemblée avec un tapis en planches d’aluminium. Grâce à la subvention d’un million de dollars américains, Purdue et ITAMCO ont développé des tapis imprimés en 3D qui utilisent des matériaux cellulaires à transformation de phase (PXCM) comme alternative au tapis AM-2, utilisé depuis la guerre du Vietnam.
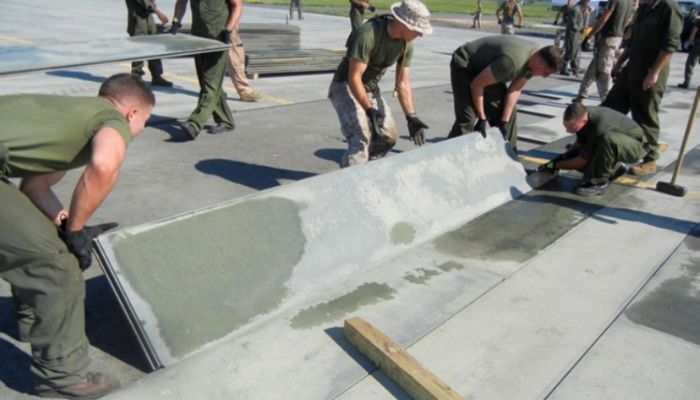
Crédits photo : ITAMCO
Renishaw, HAP et NCAM impriment en 3D des poignées de porte d’hélicoptère
La société d’ingénierie Renishaw a collaboré avec Hyde Aero Products (HAP) et le National Centre for Additive Manufacturing (NCAM) au Royaume-Uni pour fournir des poignées de porte imprimées en 3D pour deux hélicoptères de classe II. Bien que HAP ait déjà investi dans l’impression 3D de polymères avant cette collaboration, ce projet était une première en matière de fabrication additive métal. L’objectif était de voir si l’impression 3D métal pouvait être une solution viable et rentable pour fabriquer des poignées d’hélicoptères et éventuellement d’autres pièces à l’avenir. Les poignées ont été réalisées à l’aide du procédé de fusion laser sur lit de poudre et ont été imprimées horizontalement avec un support en treillis interne.
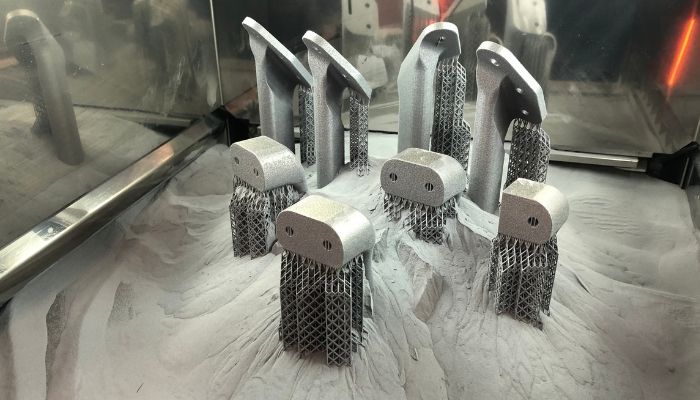
Crédits photo : NCAM
Que pensez-vous de l’usage de l’impression 3D dans l’industrie aéronautique ? N’hésitez pas à partager votre avis dans les commentaires de l’article ou avec les membres du forum 3Dnatives. Retrouvez toutes nos vidéos sur notre chaîne YouTube ou suivez-nous sur Facebook ou Twitter !
Crédits photo de couverture : 3Dnatives